Regional Quality Manager Resume Samples
4.5
(118 votes) for
Regional Quality Manager Resume Samples
The Guide To Resume Tailoring
Guide the recruiter to the conclusion that you are the best candidate for the regional quality manager job. It’s actually very simple. Tailor your resume by picking relevant responsibilities from the examples below and then add your accomplishments. This way, you can position yourself in the best way to get hired.
Craft your perfect resume by picking job responsibilities written by professional recruiters
Pick from the thousands of curated job responsibilities used by the leading companies
Tailor your resume & cover letter with wording that best fits for each job you apply
Resume Builder
Create a Resume in Minutes with Professional Resume Templates
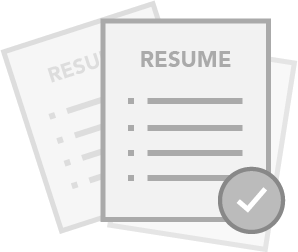
CHOOSE THE BEST TEMPLATE
- Choose from 15 Leading Templates. No need to think about design details.
USE PRE-WRITTEN BULLET POINTS
- Select from thousands of pre-written bullet points.
SAVE YOUR DOCUMENTS IN PDF FILES
- Instantly download in PDF format or share a custom link.
SB
S Bernhard
Serena
Bernhard
313 Liza Port
Chicago
IL
+1 (555) 112 7743
313 Liza Port
Chicago
IL
Phone
p
+1 (555) 112 7743
Experience
Experience
Chicago, IL
Regional Quality Manager
Chicago, IL
Lubowitz, Hettinger and Shields
Chicago, IL
Regional Quality Manager
- Providing and ensuring training and support for LabCorp quality policies and procedures
- Establishes and maintains documentation relevant to food safety and quality for assigned EM’s
- Working knowledge of ASW D1.1, API-1104, ASME Sec, II, VIII, IX, B31,1, B31.3, B31.4 codes and/or specification(s)
- Interact with market leaders, other departments, and the community to promote Humana programs and strategic initiatives. Implement these in Quality area to align with Humana’s programs and strategy
- Responsible for tracking and reporting key quality performance metrics including PPM performance, Scrap Monitoring and Waste Reduction, 8D and Cost of Quality
- Develop overall training programs in support of above and work with Human Resources to provide training curriculum and resources to support same
- Review and continuously improve product quality documentation system by writing and updating quality assurance procedures
Phoenix, AZ
Regional Quality Manager North
Phoenix, AZ
Considine-Farrell
Phoenix, AZ
Regional Quality Manager North
- Manage areas that impact cost of quality such as sort, rework, ICIM project selection
- Work closely with quality personnel to review product consistency while monitoring scrap rates to determine trends and areas of improvement
- Monitor plants quality on an ongoing basis and provide regular updates to senior leadership
- Establish and direct Plants Quality Policies & Procedures
- Maintain quality service by establishing and enforcing organization standards
- Support AQP processes - Lead the effort to move from corrective to preventive working closely with Engineering
- Direct DEEDS customer satisfaction organization in the continuous improvement of the CS Operating System and the connectivity to other flows and swimlanes (common processes and procedures, systems, performance metrics, cost model and people management)
present
Dallas, TX
Regional Quality Manager, NA & Asia Pacific
Dallas, TX
Spencer Group
present
Dallas, TX
Regional Quality Manager, NA & Asia Pacific
present
- Facilitates implementing process specific quality/workflow systems with process owners to meet the BU QMS framework
- Provide relevant training and support to site QA/QC
- Providing leadership and support to the region in matters of quality
- Support plants and businesses in order to provide a full technical answer to a customer complaint and answering in a timely manner
- Provides on-site support during regulatory inspections, to assure clear communications
- Strong in managing leading indicators to drive personnel and business performance Product expertise
- Drive leadership and practices to ensure the development of preventive actions to avoid quality defects
Education
Education
Bachelor’s Degree in Engineering
Bachelor’s Degree in Engineering
Towson University
Bachelor’s Degree in Engineering
Skills
Skills
- Strong interpersonal skills -- the ability to build strong customer relationships to ensure partnerships and alliances
- A strong leader with excellent communication and organizational agility skills that have resulted in a track record of successful objective completions
- Good critical thinking skills and proven quality improvement experience
- Strong planning capabilities with the ability to think ahead and plan over a 1-2 year period
- Strong leadership skills with the ability to lead people and achieve results through others
- Strong proficiency using common PC applications: MS Word, MS Excel, MS Visio, MS Office, MS SharePoint, MS PowerPoint
- Past experience with External Manufacturing is highly desirable
- Excellent organizational skills with ability to work in fast paced environment
- 5+ years of experience in quality assurance roles, including experience as a Plant Quality Manager in a manufacturing environment
- Excellent knowledge of Six Sigma and Lean Methodology
15 Regional Quality Manager resume templates
Read our complete resume writing guides
1
Regional Quality Manager Resume Examples & Samples
- Compliance to accreditation, state, and federal regulations. Facilitate surveys and site visits. Complete annual QI documents, and reporting requirements. Conduct oversight of any corrective action plans
- Collection of annual HEDIS data. Oversight of vendor. Review of final reports and participation in barrier analysis
- Oversight of investigation of quality and attitude issues. Assures appropriate actions are taken. Implement Peer review process/committee
- Oversight of medical record documentation review and continuity of care and coordination of care studies
- Interact with market leaders, other departments, and the community to promote Humana programs and strategic initiatives. Implement these in Quality area to align with Humana’s programs and strategy
- Builds Human Capital. Promotes staff development and training opportunities. Acquires and retains talent
- Previous Medicaid or Medicare experience
- BSN/MSN degree preferred but experience may be substituted
- HEDIS experience
2
Regional Quality Manager Resume Examples & Samples
- Maintain quality
- Maintain national standards and regulatory requirements
- Ensure a positive learner experience
- Assessment and delivery of vocational qualifications
- Internal and external quality assurance processes
- Awarding organisation and regulatory requirements
- Centre and qualification approval and recognition
- Maintaining national standards for assessment
- Assessment malpractice
- Compliance, irregularities and sanction issues
- Other complex delivery and quality assurance issues
- Subject specific information by functioning as an advocate for one or more sectors
- Programme delivery
- Assessment
- Verification
- Centre quality processes
- Assessment associate development
- Assessment associate monitoring
3
Regional Quality Manager Resume Examples & Samples
- Lead the development and deployment of the Quality strategy for Hydraulics Americas Region - FC ensuring alignment with Global Hydraulics Group
- Ensure the Hydraulics Americas - FC Plants comply with applicable Eaton, customer and industry-specific Quality requirements by conducting the necessary audits and assessments and determine system effectiveness
- Develop and implement a Quality organizational structure capable of supporting the strategic initiatives and lead the efforts to integrate quality into the development of short and long range business plans
- Manage the development, implementation, and use of the Balanced Scorecard tool to all levels of the organization (Region and Plant)
- Analyze key quality-related operational metrics related to both the Eaton Balanced Scorecard and customer systems and perform periodical reviews to evaluate results and establish action plans to close the gaps at an operational level
- Manage the implementation of 6-sigma in accordance to Corporate and Group guidelines
- Lead the sharing of best / transferable practices across the Region for the Quality function
- Continually improve the capability of the Quality organization through ongoing development activities and identification of talent to promote functional bench strength. Ensures deployment of Eaton’s quality functional excellence tool set and provides input to development plans for functional reports
- Champions the Eaton Quality System (EQS) within the Region. Identifies and leads initiatives across the organization to address common barriers for the plants and enable improvement in effectiveness and efficiency of EQS. Responsible for overseeing utilization of EQS to control and improve key regional quality processes and plants
- Support the Operations Assessment (OpA) process as a Lead Assessor for Quality and represent the Quality Function in the OpA Leadership Review (OpA-LR) process for the Americas Region and identifying common themes and actions
- Lead quarterly Quality functional reviews with specific focus on EQS self-assessment effectiveness and maturity, corrective and preventive actions, timely closure of actions, and other items as required
- Overall ownership of the Quality Alert and Escape Management process for the Americas Region – FC Plants. Ensures timely escalation / communication of customer spill incidents, and coordinates with Group, Plant Quality/OpEx, and Supplier Development colleges to ensure appropriate containment, root cause, and corrective actions are undertaken with the utmost urgency
- Bachelor’s degree in Engineering or Business from an accredited institute
- Ability to work in the United States without company sponsorship
- Minimum 10 years of experience in manufacturing, engineering or quality assurance with demonstrated ability to drive results in the area of Quality, continuous improvement, etc
- Demonstrated knowledge of Quality Management Systems such as ISO-9001, TS-16949, AS-9100 etc
- Three years of experience in a role with multiple site responsibilities
- EQS Assessor, ISO 9001 Lead Auditor certified
- Certified Manager of Quality / Organizational Excellence (CQM / OE), ISO-9001 Auditor and Six Sigma Blackbelt
4
Regional Quality Manager Resume Examples & Samples
- Define Regional Quality objectives, and monitor progress
- Manage the Region’s Quality System in accordance with the Faurecia Excellence System (continuous improvement processes)
- Lead all quality improvement activities within the Operations Region to include execution of developed processes (FES, CIQ, etc.)
- Coordinate CIQ evaluations and coach/mentor plant teams to develop and execute improvement plans
- Ensure that appropriate Quality resources (people and methods) are allocated to each plant
- Manage the Quality Network within the region and professional development of Quality Team members while working closely with Regional Operations Director and Plant Managers
- Have the authority to stop delivery of any parts in case of serious non conformity (particularly Safety & Regulation concerns)
- Develop and drive improvement initiatives within the Region in coordination with Quality Network
- Develop and execute plans to drive flawless launch of new programs
- Minimum 10 years experience including an experience in Quality
- Experience in a management role in a matrix organization
- Lean manufacturing experience is a plus
- Project Management Methodology
- Quality tools, processes and Systems
- APQP & PPAP validation process
- Entrepreneurship mindset
- Ability to lead others at all levels of organization
- Oral and written communication & presentation skills
- R&D Experience
- Production Experience
- Logistic basis
- Knowledge of product & technology
- Cost model
- Panel & Strategy management
- Supplier audit process
- Integrity
5
Regional Quality Manager Resume Examples & Samples
- Develop, coach and lead QFS colleagues, including on-site visits to support GMP, QMS, and Food Safety programs
- Establish performance goals for the QFS team making sure key objectives of the business are met
- Work with and support Technical Services group in Overland Park on projects, programs, new technologies
- Ensure standard laboratory methods are implemented and training records are current for all laboratory colleagues, implement new technologies to align with corporate initiatives
- Establish reports to show laboratory accuracy and timeliness with continuous improvement opportunities identified
- Drive root-cause identification and corrective actions for quality incidents and customer complaints, identify opportunities for improvement based on trends
- Coordinate sanitary transportation program and audits for carriers, wash stations, maintenance facilities
- Lead by example keeping safety and environmental objectives at the forefront of what you do
6
Senior Regional Quality Manager Resume Examples & Samples
- Drive creation of quality initiatives, process change initiatives, and other Change/Six Sigma initiatives to enable the region to meet and exceed business plans
- Must be willing to travel as necessary, up to 50%
- Experience with Six Sigma tools and Lean techniques required
- An independent problem solver who can make high quality judgments and decisions quickly with excellent organization skills to work across functions and upwards
- Sound business judgment, proven ability to influence others, and strong analytical thinking skills and attention to details are critical to success in this position
- Creative in finding new solutions / designing innovative methods, systems and processes
- Strong project management and organizational skills, experience working on complex initiatives with cross-functional teams in a dynamic environment
- Excellent communication skills, ability to simplify complex topics for broad audiences
- Ability to handle changing priorities and use good judgment in stressful situations
7
Regional Quality Manager Resume Examples & Samples
- Drive continuous improvement program across processes
- Analysis of utilization, efficiency and available date for the process
- Undertake detailed process improvement studies and up skills the team members
- Mentor Green Belt/ Yellow Belt projects
- Drive culture of continuous improvement
- Provide training and quality support, development of metrics and dashboards in line with customer requirements
- Ability to lead a team, coordinate with other location and drive standardize practices
- Should meet and exceed client metrics: External and Internal quality metric should be consistently green
- Strengthen quality management processes/framework to improve quality delivery
- Accurately capture SLA/SLO metrics, the reporting needs of each of the client and set up/customize processes to seamlessly meet clients expectations
- Ability to get out of the box ideas and process improvement initiatives in the process
- Should drive process control and compliance in addition to managing audit requirements
- Should ensure knowledge consistency through means like calibrations, quizzes, D-Sat Scrubbing etc
- Should have persuasive, collaborative and influencing skills
- Strong interpersonal skills to manage client expectations /engagements effectively
- Excellent Transactional Quality Domain Knowledge
- Strong Process Knowledge and Compliance to multiple audit postures
- Design overall framework of learning development for associates across all locations
- Post- Graduate Degree is Preferred
- Certified & Trained on Black Belt (Green Belt certification is a Must, Black Belt is desirable)
- Demonstrated success in Transactional Quality
- Exposure to different improvement frameworks like Six Sigma, Loan
- Thorough knowledge of MS office tools like Power Point and awareness of BI tools such as SAS,SPSS project, excel are critical for the job
- Strong communication & facilitation skills
- Strong analytical skill- ability to work with huge volume off data using statistical tools
- Flexible approach to tackling projects
- Excellent knowledge of Six Sigma and Lean Methodology
8
Regional Quality Manager, NA & Asia Pacific Resume Examples & Samples
- Support plants and businesses in order to provide a full technical answer to a customer complaint and answering in a timely manner
- Support the establishment and maintenance of BU Quality Management System (QMS) serving as the framework for how AkzoNobel PPC plans, sustains, and improves its operational processes
- Facilitates implementing process specific quality/workflow systems with process owners to meet the BU QMS framework
- Define process capability measurements and Performance Management systems
- Support Sites and functions in gap analysis and action execution
- ISC responsible person for third party registrations and customer-quality related activities
- Rationalize and simplify 3rd party registration and recertification processes and documentation control policies and site/business quality manuals, while ensuring compliance is maintained
- Provide relevant training and support to site QA/QC
- Accountable for performance management of key service and processes for continuous improvement
- Drive leadership and practices to ensure the development of preventive actions to avoid quality defects
- Responsible to promote the culture of Quality Excellence at all levels within the region
- Operating with full view of the customer portfolio, and specific requirements and interacting with Sales and Marketing and with their customers to understand and communicate
- Providing leadership and support to the region in matters of quality
- To ensure that our Manufacturing processes and related SOPs reflect our capability to deliver consistent product quality
- To manage & reduce quality defects & customer complaints effectively
- To ensure continuous quality improvements
- If required, provides subject matter expert support related to the GMP (Good Manufacturing Practices) regulatory compliance of site operations, process and products to raise the quality level of all sites to assure a sustainable level of quality and regulatory compliance, and to increase productivity of GMP quality operations
- Provides on-site support during regulatory inspections, to assure clear communications
- When necessary provides hands-on support to complete investigations into potentially serious matters
- BS or MS (preferred) in Chemistry, Chemical Engineers or related science, with 10+ years of relevant experience executing large-scale process improvement, quality management, systems implementation in pharma or chemical manufacturing environment
- Leadership in Quality Assurance/Control in Multi-site/regional business required Professional practice in project management in an industrial manufacturing environment
- Ability to work in a complex organization with the demonstrated ability to liaise with top management of the regional organization - communication skills, negotiation, and relationship management skills required
- Demonstrated depth of knowledge and SME in all areas of QA process, certifications (included but not limited to ISO, GMP) and management systems
- Certified Six Sigma Black Belt preferred. Lower level certifications considered
- Experience developing and deploying modern QMS (Quality Management Systems) practices and processes in a matrix organization, ensuring harmonization cross-functionally and in multiple regions
- Knowledge of Manufacturing Excellence methods
- Excellent command / highly proficient in spoken and written English
- Strong communication skills, both orally and in writing, and the ability to influence at all levels
- Credible communicator at all levels of organization from Operators to Corporate Officers
- Strong in managing leading indicators to drive personnel and business performance Product expertise
- A proven ability to teach, mentor, and coach across multiple levels of an organization and to
- Lead, motivate, develop and coach teams
9
Regional Quality Manager Resume Examples & Samples
- This role has no direct reports
- The position will work with operational site management (Plant Managers, Quality Managers, etc.), corporate quality, and cross-functional and business leadership personnel to achieve quality improvement objectives while developing as a successor to higher level quality leadership positions
- Bachelor of Science (BS) undergraduate college degree or equivalent in a technical discipline (E.g. Engineering, Chemistry, Biology, Physics, etc.)
- 5+ years of experience in quality assurance roles, including experience as a Plant Quality Manager in a manufacturing environment
- Must have experience in management or development of an ISO9001 or ISO/TS16949 based quality management system
- Must have experience in leading and facilitating project teams
- Working knowledge of automotive industry quality management standards (AIAG – APQP, PPAP, SPC, MSA, etc.) and quality assurance problem solving tools (E.g. 5-Why, Cause & Effect Diagrams, DOE, 8D, etc.)
- A strong leader with excellent communication and organizational agility skills that have resulted in a track record of successful objective completions
- Change management leadership capability
- Experience utilizing quality assurance PC Applications: Minitab, SPC Applications, etc
- Certification as a Quality Engineer (CQE), Quality Manager (CQM), Quality Auditor (CQA) or Six Sigma Black Belt through ASQ or an equivalent certification is preferred, but not required
10
Regional Quality Manager Resume Examples & Samples
- Maintaining advanced global engineering and manufacturing facilities
- Identifying customer needs to provide continued added value solutions
- Continually improving processes, material and designs to ensure every solution exceeds customer expectations while providing unparalleled value
- Oversee quality assurance activities for the organization
- Establish quality metrics for functional areas within the organization
- Strategically plan, review, and execute activities associated with continued compliance to the following management systems and accreditations: ISO 9001 Quality Management System (QMS)
- Develop, implement, maintain, and communicate quality strategies and programs throughout the organization
- Direct, oversee, and provide input into the relevant quality systems, including: change control; documentation systems; quality procedures, standards and policies; customer complaints, quality system reporting; and other related areas
- Prepare and conduct quality review meetings with the management team
- Direct the utilization of APQP and PPAP methodologies to improve the quality output of processes by identifying and removing the causes of defects and minimizing variability in manufacturing and business processes
- Review and continuously improve quality and reliability standards by studying product and consumer requirements with other members of management and with manufacturing operators, technicians, and engineers
- Direct and continuously improve rework standards by devising inspection and physical testing methods and procedures
- Review and continuously improve product quality documentation system by writing and updating quality assurance procedures
- Maintain product quality by enforcing quality assurance policies and procedures and government requirements; collaborating with other members of management to develop new product and engineering designs and manufacturing and training methods
- Prepare product and process quality reports by collecting, analyzing, and summarizing information and trends
- Complete quality assurance operational requirements by scheduling and assigning employees; following up on work results
- Direct and continuously improve in-process product inspection standards by studying manufacturing methods; devising testing methods and procedures
- This list of duties and responsibilities is not all inclusive and may be expanded to include other duties and responsibilities as management may deem necessary
- Will have day to day quality responsibilities at the New Berlin, Wisconsin manufacturing facility and will report directly to the Director of Operations. Direct reports to this role include the Juarez, Mexico and Des Plaines, Illinois Plant Quality Managers
11
Eacr Regional Quality Manager Resume Examples & Samples
- Work with Segment Quality leadership to ensure communication of segment and group requirements as well as alignment of facility practices with these requirements
- Plan and oversee the analysis, inspection, test, and/or service of product to assure the customer requirements are met
- Evaluation of vendors executing products and services provided to Cameron
- Maintenance of existing and development of new Quality requirements to control execution of work at the facilities
- Perform regular visits of facilities throughout EACR region to ensure compliance with facility manual
- Keep management team abreast of significant issues or developments identified during quality activities and actions being taken to improve the situation
- Direct workers engaged in inspection and testing activities to ensure continuous control over materials, facilities, and products
- Implement quality training programs to key personnel in conjunction with other managers
- Investigate and address customer complaints regarding quality
- 3 plus years’ management experience
- Ability to read, analyze, and interpret general business periodicals, professional journals, technical procedures, or governmental regulations
- Should have a working knowledge of API Q1, API 6A and 16A
- Experience in conducting internal/external quality audits
- Experience with root cause failure analysis
- Experience working with SAP
- Basic Computer skills (Microsoft Office, Outlook)
12
Regional Quality Manager Resume Examples & Samples
- Coordinates ISO, AS, or TS standards, where applicable
- Quality Improvement Board participation (CQIB)
- Report on the suitability and effectiveness of the region Quality Assurance System
- May fill the role of direct supervisor of Lean Focal in Lean and Quality functions
- Assist the Managing Executive in creating a quality attitude at all branches
- Frequent communication with site Quality Assurance Representatives
- Visit to each site once a quarter for training and coaching
- Work with the department manager to establish goals, assess competency and direct quality output in line with the established Quality Objectives
- Planning of and implementation of customer satisfaction effectiveness strategy
- Direct and coordinate all aspects of Lean Management in support of company goals and objectives
- The quality assurance manager is to lead and ensure the maintenance of the following items
13
Regional Quality Manager Resume Examples & Samples
- Quality and Compliance support for ANRD and ANSC laboratory functions
- Review and support of system life cycle for IT systems utilized in laboratories (LIMS/Empower/Qualtrend)
- Provide quality assurance support to regional R&D laboratories and third party laboratories within Asia and EMEA region including initial and requalification activities
- Liaison with Asia and EMEA site laboratories to ensure successful implementation on continuing operations
- Provide guidance and support for internal and external audits
- Provide support to investigations for specification excursions from third party laboratories
- Review and support of qualified laboratory instrument and equipment qualifications; change control documents and test method validations
- Implement and maintain the effectiveness of the validation change control system
- Review and approve validation documents, policies, procedures, and forms
- Maintenance of site validation master plan schedule
- Chair and manage effectiveness of Validation Review Board
- Oversee maintenance of the validation management
14
Regional Quality Manager Resume Examples & Samples
- To assure the overall quality of services rendered to laboratory clients within the regional in terms of reliability, accuracy, and precision
- To act in a proactive manner in the identification and rapid resolution of problem issues which adversely affect LabCorp quality
- To provide leadership within the region for LabCorp quality programs including the implementation of policies and systems which lead to continuous quality improvement
- Providing guidance for laboratories in implementing policies with respect to aspects regulatory and accreditation requirements
- Providing and ensuring training and support for LabCorp quality policies and procedures
- Auditing and inspections laboratories to proactively identified quality issues and non-conformities
- Collecting summary data for management reports regarding quality indicators, internal and external audit outcomes, complaints, and any issue that could jeopardize laboratory licensure
- Monitoring and responding to quality indicators, non-conforming events and regulatory citations, including root cause analysis, corrective action and effectiveness checks
15
Regional Quality Manager SH Resume Examples & Samples
- Drive Global Quality initiatives and goals
- Drive Continuous Improvement mentality across all sites
- Ensure the effective use of Quality tools across process design, operations, and quality in problem resolution. Provide training and mentoring as needed
- Drive continuous improvement using statistical tools such as Six Sigma and lean methodologies
- Support effective response to Customers on all major Customer issues and escalations. Ensure proper investigations are performed prior to closure of issues
- Facilitate and participate in problem-solving activities in support of 8D corrective actions, Kaizen Events and Lean/Six Sigma Projects
- Participate in Customer-facing discussions in response to issues or on quality topics
- Ensure that operational metrics (KPI) are accurately and effectively used, performance trends are tracked and actions are quickly taken to mitigate issues
- Analyze, interpret, trend and execute improvements on key metrics. Identify systemic performance issues ensuring root-cause analysis and corrective solutions are identified and implemented
- Provide a path of escalation for site Quality Managers and Quality teams
- Mentor and develop site quality managers
- Bachelor’s Degree Required. Degree in Engineering or Science preferred
- Minimum of 5 years experience in Quality Management
- Experience in Lean/Six Sigma. Six Sigma Black Belt certification preferred
- Experience in successfully leading projects and teams across functions and sites
16
Regional Quality Manager Resume Examples & Samples
- Minimum of fifteen (15) years experience in quality (or equivalent) within a manufacturing environment. Automotive OE experience required
- Strong leadership skills with the ability to lead people and achieve results through others
- Strong planning capabilities with the ability to think ahead and plan over a 1-2 year period
- Knowledge of regional and global operating standards and procedures such as ISO9001, TS/ISO16949 and the new IATF16949
- Excellent interpersonal and communication skills, including presentation skills
- Problem analysis and problem resolution skills, at both a strategic and functional level
- Ability to travel min 50% of the time
17
Regional Quality Manager Resume Examples & Samples
- At least 3 years clinical management experience in dialysis (for example as Clinical Manager, Area Manager, Education Coordinator, Charge RN)
- At least 2 years as a nephrology nurse
- Experience in quality, risk management, case management or infection control,
- Maturity and tact essential
- Good understanding of the relationship between providers of health care services and regulatory agencies
- Good critical thinking skills and proven quality improvement experience
- Able to analyze & propose alternate solutions, assist in resolving sensitive to complex issues/problems
- Able to differentiate between when coordination may be performed by telephone or written instruction, and requires approval by higher level authority
- Able to travel 50% - 80% of the time and valid driver’s license
- Preferred - experience in teaching/consulting and in complex organizations (with Corporate Regional, Area and Local management)
18
Regional Quality Manager Resume Examples & Samples
- Lead cross-plant teams to develop corrective actions on major quality events
- Represents Sonoco with customers on major quality and process improvement initiatives for all plants within the division
- Responsible for assuring productivity driven projects maintain standards and continue to meet customer requirements
- Trains new Plant Quality Managers
- Monitors, scores and develops improvement plans for Preventive and Corrective action systems
- Approves changes for product and processes within the assigned market
- Leads all third party and customer audit activities within the market segment
- Conducts field product audits for market segments to identify performance capability
- Assures product safety compliance for the market segment and sub-contractors
- Lead the supplier product safety audits
- Leads corporate quality process audit
- Provides Lean Six Sigma project leadership and/or mentoring for plants
- Provide quarterly reviews and scorecards for customers in the market segment
- Coordinates follow-up to VOC survey results
- Significant travel requirements
- 7-10 years experience in quality role
- Lean Six Sigma Black Belt Certification or CQE preferred
- Analytical skills; strategic selling education; statistical analysis expertise
- Excellent verbal & written communications skills; strong presentation skills,
- Proficiency in Word, Power Point, Excel, statistical software
- Experience within the plastics industry or packaging industry
19
Regional Quality Manager Resume Examples & Samples
- Education – Bachelor of Science Degree in Quality, Engineering, Metallurgy or related degree preferred. Equivalent experience may be acceptable
- Experience: Requires experience and practical knowledge of commercial heat treatment of aerospace alloys including steel, aluminum, titanium, nickel, copper, etc. Should be considered an expert in the industry
- Minimum of 10 years quality or technical experience in Aerospace industry including successful experience as Quality Manager of aerospace heat treat facility
- Six Sigma Black Belt certification required
- Certified Quality auditor in AS9100 and ISO9001. EMS 14001 certification a plus but not required
- Must be extremely familiar with NADCAP and able to conduct pre-NADCAP audits to assist sites as requested
- Must be capable of making written recommendations for improving Quality Assurance Systems and Procedures (BQS)
- Must be thoroughly familiar with commercial (AMS, ASTM), aircraft, and aerospace specifications, ISO, AS, QS and TS quality systems
- Must be able to read and interpret blueprints, specifications and purchase orders and provide guidance to sites on the same
- Considered the expert within Bodycote and capable of discussions both inside and outside of Bodycote
- Advanced knowledge of pc based computer operations is required to maintain the electronically managed and centralized BQS
- Ability to travel up to 75% of the time across Region with minimal notice to meet the business needs
- ITAR Compliant
- Develop and maintain Bodycote Quality System in compliance with 3rd party and customer specifications. A high priority is placed on NADCAP and AS9100 standards
- Acts as a member of the ADE Regional team. The position is expected to behave in in an open and collaborative way
- Responsible for the mentoring and coaching of quality team members across the region
- Performs other duties as dictated by position or required by the Regional GM/VP NA Operations
20
Regional Quality Manager Resume Examples & Samples
- Perform all work in accordance with the plant safety rules and participate plant safety activities. Be pro-active in identifying and performing tasks to maintain and improve safety, environmental performance
- Develop process quality control plans, work instructions, inspection and testing requirements and ensure plant operations personnel receive appropriate level of related training
- Lead the internal and external audit process
- Ensure that quality systems requirements are maintained and updated
- Responsible for tracking and reporting key quality performance metrics including PPM performance, Scrap Monitoring and Waste Reduction, 8D and Cost of Quality
- Report on timely basis to the Plant Manager on the performance of the quality system, any non-compliance issues and recommended actions
- Bachelor's degree in Manufacturing Technology, Engineering or a related field
- Comprehensive understanding of SQC, SPC, PPAP, FMEAs, 8Ds
- The ability to work effectively with all levels within the organization as well as with external parties, including regulatory bodies and customers
- Strong interpersonal skills -- the ability to build strong customer relationships to ensure partnerships and alliances
21
Asia Pacific Regional Quality Manager Resume Examples & Samples
- Establishes, maintains and develops processes and procedures related to quality systems, and ensures ongoing conformance with ISO 9000, Food Safety Standards (BRC, FSSC 22000), FAMI-QS, GMPs, HACCP and Kosher/Halal
- Supports regional plants in continuous improvement, best practices and reporting of KPIs. Works with regional plant QA/QC Managers in carrying out supplier, toll manufacturing, warehouse and plant audits to monitor best practices and conformance
- Ensures best practices for supplier and raw material approval process, including ongoing training of regional sourcing and plants
- Ensures best practices for the complaint management process and supports high level customer complaints and/or customer visits, closing of external warehouse logistic complaints and providing regional training to plants, supply chain and sales
- Supports Regulatory function including high level issues and questions related to compliance. Ensures regional specifications and requirements are translated into global specifications
- Supports the product recall procedure and mock recalls; conducting one mock recall within the region per year
- Supports plants on CAPA and traceability/troubleshooting from mock recalls
- Provides regional training on recalls to product management, sales and supply chain teams
- Works with Quality Coordinators and Quality Engineers to support product information for regulatory dossier submissions and product registrations
- Supports documentation management practices and language translation requirements for Product Descriptions, Labels and CoAs
- MSc/BSc in a scientific discipline (Biotechnology, Biochemistry, Engineering)
- Demonstrated knowledge of manufacturing processes and at least of 5 years of management experience in a manufacturing environment
- Experience in food manufacturing environment would be preferred
- Experience managing teams or improvement projects with a global scope
- Exhibit high ethical standard, possess excellent leadership, communication, interpersonal skills with strong team orientation
22
Regional Quality Manager Resume Examples & Samples
- Implementation the Quality Process and Quality System in the Region: and provide for Quality Teams and metrics
- Assure that employees receive required quality training
- Act as facilitator for district problem solving , corrective action, and BPI initiatives
- Act as ISO 9000/QS 9000 Program Manager and provide for all compliance audits
- Maintain records and reports on the status of the Quality Process for all departments and/or districts
- Facilitate district SPC efforts
- Coordinate and respond to customer quality audits and assist sales with quality presentations
- Serve as a quality director resource for districts assigned by area of internal audits of ISO audit facilitation
- Minimum of two years quality, administrative, and operational experience which includes knowledge of various methodologies (TQM, Lean, Kaizen, Deming, Crosby, etc.)
23
Regional Quality Manager North Resume Examples & Samples
- Support AQP processes - Lead the effort to move from corrective to preventive working closely with Engineering
- Drive the problem solving and corrective actions to the corresponding flow
- Manage areas that impact cost of quality such as sort, rework, ICIM project selection
- Provide leadership for the successful day-to-day operations
- Establish and direct Plants Quality Policies & Procedures
- Monitor plants quality on an ongoing basis and provide regular updates to senior leadership
- Work closely with quality personnel to review product consistency while monitoring scrap rates to determine trends and areas of improvement
- Review established production schedules for all manufacturing departments to insure established inventory levels are met while operating at the highest efficiency possible
- Monitor operation expenses and research ways to reduce costs while maintaining product quality
- Encourage and promote operating in a continuous improvement environment
- Develop strategic plan by studying technological and financial opportunities; presenting assumptions; recommending objectives
- Accomplish objectives by establishing plans, budgets, and results measurements; allocating resources; reviewing progress; making mid-course corrections
- Maintain quality service by establishing and enforcing organization standards
- Contribute to team effort by accomplishing related results as needed
- 7 years of experience in the related field in an automotive manufacturing environment
- Previous experience/strong understanding of budgeting/expense management with a basic understanding of financial and accounting practices
- Previous experience/best practices implementing and using continuous improvement/lean tools such as; Six Sigma, 5-S, Lean Manufacturing, Transactional Lean, etc. to drive improvement
- Previous experience/broad understanding of safety systems and enforcement of safety rules and policies
- Demonstrated strong leadership, team building and advanced coaching skills
- Demonstrated ability to motivate people, assess and develop employee skills
- Demonstrated understanding of the principles and applications associated with manufacturing operations, maintenance and engineering
- Excellent planning and organizational skills, with the ability to balance production and maintenance needs
- Excellent interpersonal communication and listening ability
- A strong ability to be adaptable and flexible
- Ability to work with teams and lead decision-making processes in a team environment
- Highly motivated, results oriented, driven
24
Regional Quality Manager Resume Examples & Samples
- Address current, significant quality issues in product supplied in their specific region to key customers
- Focus on serious events agreed upon with the business unit
- Assess quality systems health of all Global Valvetrain plants in the region and recommend/execute appropriate actions to remedy and/or prevent quality-production related conditions
- Develop and reinforce current quality standards and methodologies into the region that are driven by both industry standards and Federal-Mogul Corporate Quality expectations
- Support overall Quality initiatives driven from both central Corporate Quality and the BU quality strategies
- Audit Plants in the region as-needed in order to assess the quality operating systems and gaps to expected levels
- Maintain knowledge of customer requirements, as things change and evolve
- Assist with training of quality (and quality impacted) resources in the plants and technology centers
- Communicate actively and effectively with management, Corporate Quality and Senior Leadership, as-needed
- Lead problem solving teams
- Assess solution effectiveness, and report resolutions to customers
- Provide training to specific areas such as: FMEA's, SPC, Control Plans, Statistics, DOE, etc. The level of this training is to address what needs to be done to meet these specific requirements. It is also designed to provide hands-on assistance in how to meet the requirements
- Conduct Management reviews of the Quality System and other systems as required
- Travel to regional locations, primarily in North America
- Minimum of fifteen (15) years experience in quality (or equivalent) within a manufacturing environment
- Automotive OE experience required
- Excellent interpersonal and communication skills, including presentation skills
25
Regional Quality Manager Resume Examples & Samples
- Monitor the welding and mechanical activities at assigned sites to ensure compliance with applicable code, standards and job specific requirements
- Develop an understanding to the companies quality program and make recommendation for the betterment of the program
- Assist with the development and compliance on NBIC/ASME code projects
- Assist site Quality Managers/Inspectors in the development, qualification and/or revisions of weld WPS’s, WPQ’s and company quality program
- Perform welders verification testing, including verification of welder identification(s)
- Conduct random audits (as specified by corporate office) for compliance and adherence to company quality program. Utilize data collected from these audits to assist field operations in determining appropriate improvements
- Examine site KPI’s for improvements and cost saving measure that may arise or may be encountered. Take corrective actions as needed
- Coordinate and conduct quality training to site/field staff to improve ongoing quality and safety. Mentor, monitor and/or assist with personnel training with both mechanical and welding inspectors
- Review bid documents and provide recommendations to staff regarding quality compliance, client and/or manufacturing recommendations
- Listen to employees and supervisor’s suggestions, complaints, problems, safety concerns and recommendations. Evaluate each and devise and implement a plan of action based on that evaluation
- Accomplish quality assurance HR resource objectives by recruiting, selecting, training, assigning, scheduling coaching, counseling and disciplining employees; communicate job expectations, monitoring appraisals and job review; enforcement of company policies and procedures
- When required provide site T/A assistance with monitor and/or assisting with daily QA/QC work packages and procedures
- Properly review and interpret customer specifications, procedure, codes and material documents assuring that our techniques are in compliance with current codes and applicable customer requirements
- Have the ability to and willingness to provide inspection resources outside of normal working schedule
- 15 years’ experience in a welding/mechanical inspection QA/QC role within the petrochemical/construction industry
- 5 years as a Certified AWS Welding Inspector (CWI) additional certifications a plus
- Working knowledge of ASW D1.1, API-1104, ASME Sec, II, VIII, IX, B31,1, B31.3, B31.4 codes and/or specification(s)
- 5 years' experience with GTAW, SMAW and FCAW welding processes
- Proficient in Weld Pro-Write, Microsoft Excel, Word and PowerPoint
26
Regional Quality Manager Resume Examples & Samples
- Develop overall training programs in support of above and work with Human Resources to provide training curriculum and resources
- Bachelor of Science Degree in Quality, Engineering, Metallurgy or related degree preferred
- Certified Quality auditor in AS9100 and ISO9001
- EMS 14001 certification a plus but not required. Must be extremely familiar with NADCAP and able to conduct pre-NADCAP audits to assist sites as requested
- This position must satisfy ITAR compliance requirements, therefore candidates mus be U.S. Citizens or Permanent Resident Card Holder
- Ability to travel across Texas, Oklahoma and Kansas with minimal notice to meet the business needs
27
Regional Quality Manager Resume Examples & Samples
- Is accountable to provide direct support to EM’s for startups and new product production by establishing food safety and quality assurance programs aligned to Pinnacle Foods EM management systems
- Assures ongoing compliance with food safety and quality assurance standards
- Supports supply chain activities related to EM’s as necessary
- Provide training, education and support as requested for food safety, quality assurance and regulatory compliance to EM’s
- Minimum of 10 years industry experience with a variety of food processing– developing and implementing Food Safety and Quality Assurance programs required
- Experience with wide range of food manufacturing process is encouraged – PF current product EM network entails: Buttery spreads, bakery, frozen meals, snacks, IQF vegetable processing, bake mixes, dry blending and packaging, and sauce/dressing productions
- Experience with Gluten Free, Organic and Kosher product processing and certifications a plus
- Past experience with External Manufacturing is highly desirable
- Significant experience with food processing and packaging
- Experience in conducting inspections, audits, and program reviews and familiar with third party inspection/audit models
- Multiple manufacturing experiences under both FDA and FSIS regulated foods or food ingredients
- Trained and experienced in the GFSI standardsExcellent oral and written communication skills, interpersonal skills with high emphasis on flexibility
- Proficient with business office software, results oriented and self-directed
- Excellent organizational skills with ability to work in fast paced environment
- None – Independent Contributor