Quality Systems Manager Resume Samples
4.7
(110 votes) for
Quality Systems Manager Resume Samples
The Guide To Resume Tailoring
Guide the recruiter to the conclusion that you are the best candidate for the quality systems manager job. It’s actually very simple. Tailor your resume by picking relevant responsibilities from the examples below and then add your accomplishments. This way, you can position yourself in the best way to get hired.
Craft your perfect resume by picking job responsibilities written by professional recruiters
Pick from the thousands of curated job responsibilities used by the leading companies
Tailor your resume & cover letter with wording that best fits for each job you apply
Resume Builder
Create a Resume in Minutes with Professional Resume Templates
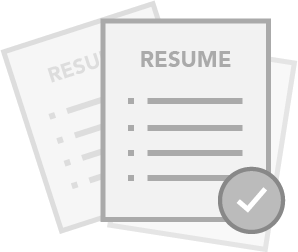
CHOOSE THE BEST TEMPLATE
- Choose from 15 Leading Templates. No need to think about design details.
USE PRE-WRITTEN BULLET POINTS
- Select from thousands of pre-written bullet points.
SAVE YOUR DOCUMENTS IN PDF FILES
- Instantly download in PDF format or share a custom link.
CS
C Stokes
Cletus
Stokes
3744 Gustave Estate
San Francisco
CA
+1 (555) 114 0899
3744 Gustave Estate
San Francisco
CA
Phone
p
+1 (555) 114 0899
Experience
Experience
Phoenix, AZ
Quality Systems Manager
Phoenix, AZ
Olson, Will and Okuneva
Phoenix, AZ
Quality Systems Manager
- Develop, manage, and continually improve Quality Assurance programs, policies, intranet applications and databases
- Review and/or develop and execute facility, software, process and equipment validations and risk management documents
- Work closely with the management team to support the growth and development of NorthStar
- Develops, maintains and execute the site wide strategy for Deviation Management Excellence, including Root Cause Analysis, CAPA, and Technical Writing programs
- Identifying and recommending to senior management areas for improvement in the quality management system and the wider company at large
- Perform other work-related duties, as assigned by site management
- Work with the local management team members in developing long and short-term business goals and strategies
Los Angeles, CA
Senior Quality Systems Manager
Los Angeles, CA
Smith-Schmeler
Los Angeles, CA
Senior Quality Systems Manager
- Leading continuous improvement of Siemens Molecular Imaging Quality Management System through the implementation of robust Internal Audit and CAPA programs
- Process owner for the Internal Audit program and procedures. Working on enhancing the efficiency and effectivity of the Internal Audit program
- Develop & maintain the Quality plan and metrics
- Provide oversight and maintain the Quality System
- Participate in the preparation and execution of site and BU management reviews
- Tracking implementation of corrective actions and performing effectiveness verification activities related to audit findings
- The noise level in the work environment is usually quiet to moderate
present
Houston, TX
Senior Corporate Quality Systems Manager
Houston, TX
Runolfsson, Jakubowski and Johns
present
Houston, TX
Senior Corporate Quality Systems Manager
present
- Create and deliver training presentations
- Collect and report on trends/metrics to proactively identify areas for improvement
- Perform ISO 9001 and other ISO process audits to determine business effectiveness, and implement and maintains ISO 9001 compliance for R&D
- Analyze current state and work with functional leaders and define business processes to meet defined business objectives
- Transform new designs to standardized work with assigned responsibilities
- Update, maintain and publish Audit Calendar; and organize and manage the process
- Manage, maintain and enforce internal audit control policies across the enterprise
Education
Education
Bachelor’s Degree in Engineering
Bachelor’s Degree in Engineering
Duke University
Bachelor’s Degree in Engineering
Skills
Skills
- Knowledgeable in industry Food Safety/Quality audit practices, and skilled in adapting to achieve business best practices
- Strong authorship and be able to critically review reports while effectively providing input and expressing Quality Risk management principles
- Excellent knowledge of quality management systems
- Experience in managing Quality Assurance and quality systems in FDA and HPRA based Pharmaceutical manufacturing essential
- Knowledge of IT technologies and their application to Quality Assurance objectives/programs
- Excellent organisational skills and attention to detail
- Capable of successfully engaging other business unit quality in the development and standardization of programs, policies, templates, standards, procedures
- Strong strategic vision/ability; Skilled at aligning business plans with strategic objectives
- Ability to manage multiple responsibilities with urgency via strong project/event management skills
- Ensures group is technically capable of handling non-routine quality system issues and that issues are thoroughly investigated, documented, and resolved
15 Quality Systems Manager resume templates
Read our complete resume writing guides
1
Quality Systems Manager Resume Examples & Samples
- Bachelor’s degree and 7+ years of cross functional responsibility in CSV in Quality Systems
- Excellent understanding of GXP and pharmaceutical regulations
- Experience in the validation of software tools in a FDA regulated environment
- Knowledge of regulations and software lifecycle approaches 21 CFR Part 11, Annex 11, risk management methodologies, GAMP, SDLC methodologies
- Working knowledge of auditing and validating SaaS applications in a GxP environment
- Working knowledge of global industry standards and regulatory requirements for quality systems
- Experience in interacting with FDA and International regulatory authorities
- Proficiency with MS Office and software programs for generating reports, presentations and statistics
- Working knowledge with TrackWise, EBS, Argus, etc
- Excellent planning and organizational skills required
- Experience with parenteral drugs
2
Quality Systems Manager Resume Examples & Samples
- Bachelor's degree in chemistry, biology or a related discipline (or an equivalent combination of education and relevant experience)
- Extensive experience (5 to 10 years) working in Quality supporting the manufacturing of drugs, biologics, or devices in the pharmaceutical/biotechnology industry
- Previous Quality and/or project management experience of the revision of the Quality Management System (Quality Manual and Quality Standards/Policies) preferred
3
Quality Systems Manager Resume Examples & Samples
- Manage daily activities related to the QMS
- Create and improve the supplier evaluation and qualification process
- Promote and support business excellence, lead by example, develop partnerships internally with the required business functions
- Ensure all new artwork and new products are in line with standards and ensure full adherence to production quality throughout the manufacturing process
- Represent the company to all external bodies
- Conducting Internal and External audits where required
- Preparing monthly quality reports, vendor ratings and management reviews
- Liaise with Manufacturing Engineers to conduct risk assessments and ensure all work instruction updates for any product line extensions, process improvements for new and existing products are delivered effectively
- Ability to effectively communicate highly technical information, both verbally and in writing, to both non-technical and technical associates internal to colleagues and external to regulatory bodies
- Extensive experience managing the QMS
- Degree in Engineering or Science
- Minimum of 4 years' experience in a Medical Device environment, ideally in a similar role managing all standards via the QMS for quality and regulatory
- Strong knowledge and exposure of ISO 13485 standards and regulations
- Strong exposure with problem solving techniques and working through CAPAs'
4
Quality Systems Manager Resume Examples & Samples
- Actively support the management of site Quality Systems
- Manage implementation & maintenance of Corrective Action, Preventative Action & Change Control
- Quality Systems Auditing to assure compliance to GMP and support site audit readiness activities
- Point of contact for all customer issues, queries or complaints as well as internal contact point for customer services, commercial, Department of Agriculture
- Status report metrics for the CAPA and Change Control systems and other relevant KPIs
- Co-ordination of quality related documentation for auditing (collation, filing, storage, presentation)
- Support process and product validation and compliance activity
- Documentation management and ownership of the document library
- Status report metrics for documentation lifecycle management process
- Ensure quality risk management documentation is complete and maintained
- Administrate the records retention program
- Drive Continuous Improvement of Quality System processes
- Support training on site document management and Change Control systems
- Support subject matter experts to create training material/programs
- Develop and review documentation as appropriate
- Execute local mock recall exercise
- Compilation of the Master Manufacturing Batch Records for compliance to cGMP
5
Quality Systems Manager Resume Examples & Samples
- Lead the HACCP team and ensure the HACCP platform is in place and maintained
- Ensure the technical policy, procedures and monitoring documents are in-place, maintained, document controlled, communicated, understood and reviewed
- Ensure customer technical requirements are reviewed and interpreted and communicated to the site teams and any gaps identified are communicated and actioned
- Review procedures and where necessary generate & implement new procedures
- Manage Internal Audit program which meets all legal and customer requirements; ensure it is maintained to schedule, conducted by a trained internal audit team and non-conformance and audit performance communicated
- Oversee Production due diligence records
- Document Control and Archive Management
- Calibration: ensure key equipment is calibrated within timeframes and certificates retained
- Ensure all paperwork (documents and procedures) are updated for new products where applicable
- Oversee Administration of computer systems including Price Sheets, Label Creation etc
- Work with the site teams to ensure the site is audit ready at all times in regards the technical systems and factory standards
- Proven experience, with proven results in quality systems role –essential
- Experience in Management of HACCP & Quality Systems - essential
- People Management skills - essential
- Efficient communication skills at all levels - essential
- Experience at Auditing – essential
- Auditor qualification – essential
- Practical Understanding of BRC & Retail Customer Standards – desirable
- Degree or equivalent in food related or science based subject – desirable
6
Quality Systems Manager Resume Examples & Samples
- Define, develop and deploy the common set of procedures, tools, methodologies and rules (the “Electrolux Quality Management System”) valid for all Functions and Sectors
- Develop, deploy and maintain the common templates required by the “Quality Management System”
- Ensure that the Quality Manual defining the ”Quality Management System” is applied consistently throughout each NA Product Line
- Set forth a scheduled audit program to ensure the correct application of the above Quality Manual to each NA Product Line
- Contribute to define and maintain a common set of Quality kpi’s, cross-functional, to track continuous improvement progress in Quality results
- Ensure achievement and maintenance of ISO 9001 Certification in North America, using common approach and Certifier
- Promote best practice and learning to ensure continuous improvement of the “Quality Management System”
- Academic Degree in Industrial Engineering or equivalent
- Master Degree in engineering or operations management\Business (preferred)
- 5 years minimum experience in activities related to Quality Management Systems, especially related to definition and deployment of procedures and methodologies
- Very good knowledge and experience in applying ISO 9001 Quality standards, related to all covered aspects (R&D, Operations, Purchasing)
- Plant or Sector quality engineering / process leadership experience
- Plant or R&D Experience strongly desired
- Proven record of success leading continuous improvement projects and activities
- Possess a high sense of urgency with the ability to make and implement tough and timely decisions
- Demonstrated leadership capability in communicating and influencing others, stakeholder management, change leader and driving project success individually and through teams
- Highly strategic in thought and behaviour, while driving also short-medium execution
- Superior mental agility, dealing comfortably and quickly with complex issues
- Leader and team player
- Strong cooperative approach
- Digital attitude
- Focused on results with a high sense of urgency
- Confidence and courage to champion change
- Characterized by integrity and high professional standards
- Able to see big picture and work on a strategic level
- A passion for analyzing data and making business conclusions and recommendations
- A fast thinker with ability to pick up and treat new information rapidly
- Multicultural experience
- Ability to work independently and produce results
- Enthusiastic, energetic and pro-active
7
Quality Systems Manager Resume Examples & Samples
- A minimum of a Bachelor Degree is required, preferably in Engineering, Quality or a related technology field
- A minimum of 6 years Quality experience in a GMP and/or ISO regulated environment is required
- A minimum of 2 years of supervisory (direct/indirect/project management) experience is required
- Experience with CAPA is required
- Data analysis and basic statistical tools are required
- This position is located in Palm Beach Gardens, FL and may require some travel
8
Quality Systems Manager Resume Examples & Samples
- Cell therapy/gene therapy is highly desired
- Experience in a lead role and interactions with federal agencies, i.e. FDA
- Expert knowledge of quality assurance in cGMP environment
- Knowledge of International Conference on Harmonization (ICH) standards
- Experience in developing and implementing multifaceted projects
- Excellent communication and organizational skills and superb attention to detail
- Experience with MS Office products and database applications required
- Expert knowledge of regulatory affairs, including IRB review and approval process and Good Clinical Practice
9
Quality Systems Manager Resume Examples & Samples
- Bachelor’s degree required (Engineering, Quality, Regulatory or Life Sciences preferred)
- 5+ years with Bachelors or Basic Degree
- 3+ years with Masters or other Advanced Degree
- 3+ years of experience providing work direction and leadership to people and teams in functional area or related field
- 3+ more years of experience in the CAPA process or Compliance
- Knowledge of the US and international medical device quality system regulations and standards (21 CFR 820, ISO 13485)
- ISO 13485 Lead Auditor certification (or willing to get within one year)
- Regulatory compliance experience with emphasis on Quality System Regulations
- MBA or Masters in Engineering, Quality, Regulatory or Life Sciences preferred
- 7+ years of experience in a medical device quality assurance and/or quality system preferred
- Experience with CAPAs and interpreting requirements for non-conformances, quality tools and process improvement techniques
- Experience interfacing with government auditing bodies, conducting/hosting quality system audits
- Project or program management experience
- Good computer skills using Excel, Word, and PowerPoint
- Experience leading/managing high performing teams and projects
- Experience with Class II and III medical devices
- Experience with capital products and field service
- RAC or CQM/CQE/CQA/PMP Certifications
- Facilitation and training skills
- Outstanding oral, presentation, and written communication skills. Ability to communicate / present complex and / or highly detailed issues / information in a way that is understandable cross-functionally and at all levels of the organization
- Excellent problem solving, and analytical skills, including knowledge of root cause analysis tools / methodologies
- Strong interpersonal skills are required. Must be an effective team player intra-departmentally and cross functionally
- Strong leadership, collaboration and relationship building skills. Must be able to work in a team environment and exert influence without alienating others
- Strong task and people management skills
10
Quality Systems Manager Resume Examples & Samples
- Broad knowledge in the following disciplines
- HHA / Post Market Vigilance
- Equipment Qualifications
- Computerized System Validation
- Regulations as: ISO 13485, 21 CFR Part 11 and
- 21 CFR Part 820
- In depth statistical knowledge is required
11
Senior Global Quality Systems Manager Resume Examples & Samples
- Ensures collaboration and builds partnerships with stakeholders to execute quality strategies for driving continuous process improvement through the Quality System
- Participates in the development and execution of the GCRQA internal system audit schedule, conducts audits, monitors adherence to company policies and reports findings to audited departments for issue resolution
- Actively participates in the maintenance of the Corrective and Preventive Action Program. Tracks completion of required corrective and preventive actions as a result of internal audits and External Regulatory Inspection commitments
- Develops and utilizes tools to track, trend and report compliance metrics to ensure
- Represents the company with regulatory authorities by facilitating regulatory inspections and third party audits, as required, in collaboration with appropriate functional areas, to ensure successful inspectional outcomes
- Minimum of a Bachelor of Arts/ Bachelor of Science degree
- Minimum of 5 years quality assurance experience in the pharmaceutical industry
- Minimum of 4 years project management experience, preferably in a multicultural, global
- Strong interpersonal skills and multi-cultural /intercultural awareness; able to negotiate
- Strong planning and organizational skills and experience managing multiple priorities
12
Quality Systems Manager Resume Examples & Samples
- Develops, maintains and execute the site wide strategy for Deviation Management Excellence, including Root Cause Analysis, CAPA, and Technical Writing programs
- Provides overall leadership in the management of critical (level I) investigation including establishment of investigation team, remedial actions, customer notifications and as appropriate establishment and support for restart activities
- Investigates and reports on deviations to the manufacturing process, customer complaints on finished product, and other manufacturing problems
- Provides remediation solutions to manufacturing sites on critical quality issues, crisis management, response to regulatory deficiency letters and other topics as required
- Provides the right level of follow up and scheduling to ensure investigations are completed in a timely manner consistent with the type and criticality of the event
- Works with process experts and production personnel to fully understand and provide guidance on appropriate and complete corrective actions to assure repeat deviations do not occur. provides technical expertise and recommends improvements
- Writes Impact Assessments and Investigation Reports, works within TrackWise
- Assigns corrective/preventive actions (CAPAs) as necessary in order to resolve problems
- Informs Management in a concise and complete manner on the progress of on-going investigations, and participates in meetings of the Deviation Review Board, providing status reports and updates on root cause assessments and CAPAs
- Possesses good technical writing and advanced critical thinking skills (to be enhanced by Catalent Certification program)
- Develops, implements, manages and tracks effectiveness of corrective action plans for exceptions, and assures all exception documentation adequately address root cause, corrective & preventive actions and product impact
- Aid in the continuous improvement initiatives of local site systems and global strategic projects for measureable deliverables
- Champion the Deviation, Complaint and CAPA management review board
- Responsible for monitoring and measuring and reporting deviation and CAPA performance and making recommendations for continuous improvement
- Responsible for tracking, trending and reporting metrics
- Responsible for the execution and tracking of change controls
- Developing a team of quality professionals to support quality systems and investigation management objectives and ensure continual quality improvement
- Ensure Quality systems are compliant with corporate and site procedures as well as industry standards including
- Regularly reviewing and evaluating new regulatory information
- Reviewing and evaluating new or revised corporate policies for compliance
- Evaluating all audit inputs systemically as potential CI inputs
- Effectively communicate Quality vision and expectations across site, including periodic site-wide GMP training in addition to focused trainings
- Function as a strong Quality liaison to other functional department, providing meaningful quality support and ensuring productive cross-functional communication
- Oversee training qualification programs for Pharmaceutical Technicians, QA Associates and Product Quality Specialists
- Drive systemic process changes as a result of Deviations/Complaints and other quality trends
- A Bachelor’s degree is required
- Bachelor of Science in pharmaceutical applicable field; examples may include Science, Biology, Chemistry, or Engineering is preferred
- Experience in quality and/or regulatory in the Pharmaceutical industry, or experience in a regulated industry with demonstrated understanding of manufacturing, regulatory and compliance is required
- Five (5) years of experience in quality and/or regulatory in the Pharmaceutical industry, OR seven (7) years of experience in regulated industry with demonstrated understanding of laboratory, manufacturing, regulatory and compliance is preferred
- Knowledge and experience in cGMP and FDA regulations is preferred
- Knowledge of Trackwise, ComplianceWire and Documentum software is preferred
- Demonstrated experience in successfully influencing others outside the incumbent’s department will be required
- Exemplary organizational skills for self and team management
- Ability to effectively present information and respond to questions from groups of managers, customers, and regulatory agencies
- Exemplary project management and organizational skills
- Ability to write reports, business correspondence, and standard operating procedures
- Ability to multitask with high efficiency
- Ability to work well under pressure and maintain efficiency
- Customer focused and performance driven
- Setting up office, desk and workstation for minimal ergonomic risk factors as deemed necessary
- Sustained sitting at desk or workstation with use of phones, computers and any other office equipment required for specified position
13
Quality Systems Manager Resume Examples & Samples
- Directs the development and improvement of a laboratory-wide quality system and manages system implementation with technical and non-technical departments
- Leads the establishment and improvement of an integrated laboratory quality system
- Ensures compliance with regulatory and accreditation agencies' requirements
- Identifies opportunities and implements processes and procedures to reduce laboratory risks
- Designs or assists in process development and improvement throughout the laboratory system
- Leads or facilitates continuous quality improvement projects and quality review processes
- Manages quality improvement projects, costs, or standardization
- Collaborates in developing quality strategies with the laboratory management team
- Manages and maintains all appropriate regulatory licenses and certificates for all laboratory testing, both in the laboratory and in non laboratory areas
- Ensures compliance for all POCT testing, manages the activities and performance of the POCT Coordinator of the laboratory
- Ensures required regulatory, quality, safety and compliance training and education for all laboratory employees and non laboratory employees performing laboratory testing
- Ensures laboratory quality and adherence to regulatory requirements through internal audits and tracers
- Extensive (usually five (5) years) experience in an acute care hospital clinical laboratory required including demonstrated ability to utilize principles and practices of quality improvement/system
- Bachelor's degree in clinical laboratory science or related field
- Valid current California Clinical Laboratory Scientist
- Other skills/experience should include demonstrable knowledge of statistical tools of quality, techniques of problem solving and improving work process, making presentations, and computer proficiency
- Knowledge of federal, state, local, and accreditation agency regulations. Must be able to work in a Labor/Management Partnership environment
- Master’s Degree or other certification in Quality Management, Lean, Project Management and/or Clinical Laboratory Management or related field preferred
- Experience qualifying, maintaining and/or calibrating equipment strongly preferred
- Experience with SharePoint, project management software and maintenance and development of electronic databases preferred
14
Quality Systems Manager Resume Examples & Samples
- Excellent communication skills, both oral and written are required
- Strong organization and multitasking skills
- Ability to prioritize and meet deadlines for multiple projects
- Bacheleor’s degree in Engineering or a related technical discipline
- Experience in a Distribution Environment
- Quality Certification (e.g., ASQ CQE, CRE, CQA)
- In-depth knowledge of the following: AATB, CMDCAS, PAL, ISO13485, ISO 4971, MDD 93/42 EEC, and CFR 21 Part 820
- Travel less than 10%
- Must be able to travel independently to various Medtronic buildings/sites
- The employee must occasionally lift and/or move up to 15 pounds
15
Quality Systems Manager Resume Examples & Samples
- Ensures compliance with all the requirements of an AS9100 quality system
- Establishes quality performance and process goals
- Follows corporate guidelines on determination and reporting of group measurements
- Communicates with other managers to coordinate quality related activities
- Host both internal corporate and external registrar AS9100 audits
- Guides and participates in all internal auditing activities including auditor training
- Monitors technical work and assists in the identification and resolution of any technical problems that might affect product quality
- Maintain the site quality manual in conjunction with corporate requirements
- Maintains corporate data bases for corrective and preventive actions, customer returns, “read across” audit & escape findings, and supplier score cards
- Effectively interacts with Production and Engineering teams to maintain customer product conformance
- Writes technical procedures and creates technical forms
- Reviews and ensures implementation of all customer and corporate specifications and product criteria
- Oversees inspection operations to ensure product conformance
- Works directly with customers to support product requirements
- Works directly with suppliers to ensure compliance of supplied materials and products
- Reviews supplier purchase orders to ensure product and corporate requirements are being met
- Works with purchasing staff to establish quality requirements for external suppliers
- Active participation in customer contract reviews to ensure product compliance
- Makes final determinations or dispositions related to non-conforming material with inspection staff
- Monitors calibration activities and tracks compliance
- Oversee all Corrective and Preventive Action activities with a focus on continuous improvement
- Responsible for all facility quality training including New Hire Quality Orientation
- Participates and oversees material testing activities
- Interface with and conformance to Corporate Quality and ABS systems
- Extremely detailed-oriented
- Able to work hands-on when required to solve problems
- Ability to develop, review, and maintain metrics
- Strong work ethics and positive team player
- Recognize and prioritize quality issues
- Ability to manage time
- Bachelor’s Degree from an accredited university
- At least 2 years of experience with quality systems
- This position is subject to the International Traffic in Arms Regulations (ITAR) which requires U.S. person status. ITAR defines U.S. person as a US Citizen, U.S. Permanent Resident (ie. Green Card Holder, Political Asylee, or Refugee
16
Senior Quality Systems Manager Resume Examples & Samples
- 7+ years' work experience including 5+ or more years of relevant quality system experience in a medical device manufacturer
- Previous experience with ISO/CE certification process
- Previous experience with US and international medical device regulations
- Effective interaction with personnel at diverse positions within and outside of the organization
- Previous experience the management of FDA Inspections
- Previous experience the management complex Quality System implementation projects
- Previous experience in Supply Chain or Distribution Quality
- Professional Quality Certification (e.g., ASQ CQE, CRE, or CQA)
- In-depth knowledge of the following: AATB, CMDCAS, PAL, ISO 13485, ISO 14971, MOD 93/42 EEC, and CFR 21 Part 820
- Must be able to travel independently to various Medtronic buildings/sites including internationally
- The employee frequently is required to stand; walk; and use hands to finger, handle, or feel objects, tools, or controls
- The employee is occasionally required to reach with hands and arms
- Specific vision abilities required by this job involve normal vision
- Travel up to 25%
17
Quality Systems Manager Resume Examples & Samples
- Ability to interpret an extensive variety of technical instructions in mathematical or diagram form and deal with several abstract and concrete variables
- Advocate a team concept. Proven ability to motivate personnel in order to balance staffing strength with profitability and growth
- High energy level, capable to handle multifaceted projects in conjunction with normal activities
- Well-developed interpersonal skills; ability to get along with diverse personalities
- BS/MS in Science or Engineering
- Six Sigma Black Belt and/or Lean Manufacturing certification preferred
- Experience: 8+ years of experience in a leadership role in QA/manufacturing environment in a medical device company or other regulated, critical end-use product industry. Mechanical assembly and chemical manufacturing processes
- Demonstrated analytical and data based decision making skills, statistical sampling and analysis and proficiency with Minitab statistical software. CQA/CQE
- Knowledge of medical device regulations, a plus
- Strong oral and written communication, computer (Word, Excel and Powerpoint)
18
Quality Systems Manager Resume Examples & Samples
- Knowledge of New Product Development processes
- Knowledge of engineering practices, test protocols, and documentation
- Skilled in problem solving and process improvement
- Ability to perform component engineering design and changes
- Ability to operate light machine tools and laboratory instruments
- Ability to interpret displayed results on laboratory instruments
- Minimum ten (10) years of experience in design, manufacturing, or quality engineering position (medical device experience preferred)
19
Quality Systems Manager Resume Examples & Samples
- At least 8 years of quality experience in medical device or similar environment
- Project management experience in global environment
- Knowledge of ISO13485 and its implementation is an advantage
- Project Management Skill and Lean Six Sigma Skill is required
- Operational Excellence experience is required
20
Quality Systems Manager Resume Examples & Samples
- A BS or BA in related technical or science field
- Expertise and Certified to ISO 9001 as a Lead Auditor is a must (updated certification to the 2015 Revision is preferable)
- Experience as Quality Systems Manager with 5 Years minimum
- Good written and verbal communication skills in both Spanish and English
- MS Office Software, Minitab, Data Base Management and Basic Statistical Technics Expertise, Troubleshooting Methods, e.g. 8D’s
- Experience Desirable on PED normativity for European Union
- Experience Desirable on ASME Code Section VIII for Pressurized Vessels Design and Fabrication
- Desirable (but not essential) qualifications: Member of American Society for Quality (ASQ), Certified Quality Engineer, Quality Manager, or Reliability Engineer
- MBA desirable, with focus on Quality Administration
- Six Sigma Green Belt Certification (minimum)
21
Quality Systems Manager Resume Examples & Samples
- Develop, manage, and continually improve Quality Assurance programs, policies, intranet applications and databases
- Manage Quality programs, systems,, PF internal & external audit programs, evaluations, assessment programs and databases. Provide Training and and guidance on Quality systems and programs
- Develop QA tools for continual improvement and assessment, lean sigma tools
- Standardize, deploy, and improve QA data structures and reporting tools/metrics across Pepperidge Farm
- Manage cross-functional matrix relationships with R&D, Supply Chain, and influence senior management to ensure alignment of Policies, systems, data, annual objectives, and project plans, act as project leader
- Provide leadership to Product development/technology/business development, and quality staff members within HQ organization and at the Pepperidge Farm manufacturing plants. Work with Pepperidge Farm supply chain leadership to provide guidance, support in the development of quality and supply chain staff
- Provide technical expertise and leadership in quality, food safety, and risk assessment programs/policies/events
- Expert abilities and decision quality in Food Safety, Regulatory, Process Improvement, Quality Systems and their application within food processing
- Knowledge of Global& Pepperidge Farm Quality Standards, and Quality Policies, with skills and ability to execute against requirements
- Able to partner with supply chain to effectively manage Supply Base to Expectations and Requirements Manual, Specifications, Non-Conformance resolution, Sanitation, improvement in KPI's, External audit targets and resolution of audit action plans
- Strong partnering and relationship development with external technical organizations and associations
- Ensures group is technically capable of handling non-routine quality system issues and that issues are thoroughly investigated, documented, and resolved
- Record of leadership and demonstrated success in collaborative development, documentation, planning, and implementation and continuous improvement of quality systems
- Ability to manage multiple responsibilities with urgency via strong project/event management skills
- Strong strategic vision/ability; Skilled at aligning business plans with strategic objectives
- Strong partnering and and relationship development with external technical organizations and associations
- Capable of successfully engaging other business unit quality in the development and standardization of programs, policies, templates, standards, procedures
- Knowledge of IT technologies and their application to Quality Assurance objectives/programs
22
Senior Quality Systems Manager Resume Examples & Samples
- Bachelor’s Degree in engineering discipline
- 7+ years of quality or manufacturing experience
- 5+ years management experience
- 7+ years experience in GMP medical device environment
- Working knowledge of Quality System Regulation (QSR 21 CFR 820), Canadian Medical Device Regulation (CMDR), EU Medical Device Directive (EU MDD 93/42 EEC), and ISO 13485:2003
- Internal and external auditing
- Corrective Action
- Process Improvement Methodology
- PC skills, work processing, spreadsheets, project management, etc
- Effective verbal and written communication, analytical, influencing and interpersonal skills
- Must be able to communicate at all levels and across company lines
- Advanced degree in business or engineering
- 3+ years Quality Assurance experience in a QSR (GMP), disposable medical device environment
- TQM
- Presentation and training expertise
23
Quality Systems Manager Resume Examples & Samples
- Responsible for the safety of all individuals within the quality control group, including disposal of the pertinent hazardous waste material
- Keep quality control laboratory employees informed of company / department plans, policies and procedures
- Responsible for developing fiscal expense budgets for the Quality Control/Quality Assurance responsibilities. Incumbent must possess the skills and knowledge in accounting to develop and maintain an effective budget. Responsible for cost control and associated production expenses within assigned area
- Presents a monthly report of the quality control/assurance performance criteria and comments on significant deviations. Incumbent must have knowledge of spreadsheet software and an above average understanding of personal computers and the SAP system
- Responsible for creating an environment of continuous improvement within the assigned area and developing awareness for product and production quality. Good communication skills (verbal and written) and an understanding of the process units are required
- Support the development of and assistance to lab technicians in troubleshooting equipment, test methods and any other functions as requested by staff members or as necessary, also ensure prompt notification of results. Assist maintenance personnel to insure the safe and proper upkeep of laboratory equipment and facilities
- Ensure lab procedures are up-to-date, complete and properly followed, report/coordinate any modifications, changes, additions or deletions with the DCUSA appropriate manager and corporate technical department (DCDK)
- Manage DUSM efforts for HAACP, ISO, AIB, Kosher, Grade A, GMP, Allergens, kosher for Passover) certifications and coordinate audits to ensure maintenance of above certifications
- Ensure maintenance of all specifications for all DUSM materials and packaging
- Serve on corrective action boards as the quality control representative, promote the use of the board as a decision making group for all non-conforming materials. Incumbent to use their knowledge of the applicable specifications for raw materials, packaging raw materials and intermediates, including disposition of these materials
- Ensure coordination of all outside laboratory testing needs and lab evaluation of quality on customer complaints, product studies, product history, competitor samples, etc
- Oversee distribution inspections and provide updates of inspection procedures and standards
- Compliance with applicable company policies, including maintaining a drug free work place is required
- Compliance with all Company policies is required
- Other functions as required and assigned by management
- In conjunction with IS, responsible for application/data ownership of computer systems, as designated. This includes existing and/or new implementation(s) of applications, user application training, and user authority in the application. Also responsible for accuracy and timeliness of data entry, data processing of transactions and related functions (individually or performed by staff)
- Responsible for adherence to all quality systems including, ISO and Food Safety, with an understanding of DuPont Nutrition & Health Cultor' Quality Policy and procedures. Responsible that these policies and procedures are implemented throughout the organization and all related activities under the position's jurisdiction
- Responsible to participate in the Quality Council, which reviews goals for advancement of DuPont Nutrition & Health Cultor's Quality Systems
- Maintain well-trained and productive Quality Control staff, including technician certification
- Maintain a safe working environment for all individuals within the quality control facilities
- Maintain the smooth operation of the DUSM quality systems, following established GMP’s, HACCP procedures and the ISO Quality System
- Ensure compliance with the FDAregulations and applicable test methods for Grade A, Allergens, Kosher, and Kosher for Passover. RSPO (Round table on Sustainable Palm Oil) supply chain certification system
- Ensure up-to-date procedures, documentation and statistical analyses that are consistently followed with instructional manuals and procedural guides
- Timely reporting of discrepancies to the operations management
- Ensure lot traceability of manufactured products
- Timely and cost efficient quality control laboratory services regulated within the approved fiscal guidelines
- Promote a focus of continuous improvement and customer satisfaction in the quality control operations
- Positive customer relations and timely meeting of quality control needs, including accurate and complete maintenance of customer information
- Support G&S, Pectin and the product Services groups through participation in formula/product reviews, changes and new product development opportunities
- Bachelor’s degree required: Chemistry or Biology degree preferred
- Minimum of 5 years in the food industry required
- Minimum of 5 years in supervision/management with increasing responsibilities is required
- HACCP; GMP and ISO Quality Systems experience required
- Ability to work independently with a mechanical aptitude to perform trouble shooting of equipment is essential
- Experience in supervising the activities of the QC Supervisor
- Must possess good organizational skills to accomplish all responsibilities
- Must possess strong management communication and interpersonal skills
- Knowledgeable about the analyses and tests performed in the Quality Control Laboratory
24
Quality Systems Manager Resume Examples & Samples
- Manage the NCR and CAPA processes and systems for the site
- Represent the site on the world wide NCR and CAPA teams
- Work effectively with other NCR / CAPA site leaders to ensure consistent systems and processes at Ethicon plants
- Drive the improvement and development of NCR and CAPA system for the facility
- Responsible for the overall management and effectiveness of the NCR and CAPA processes, including leading and facilitating of relevant data review forums
- Provide education and mentoring as needed regarding NCR and CAPA (beginners and continuous education)
- Develop and implement measures to monitor the effectiveness of the NCR and CAPA systems
- Lead quality systems and compliance improvement, which result from Internal / External Audits, Management Review and / or any other CAPA / NCR system indicator
- Serves as the initial point of contact for Product Complaints / Product Quality issues and ensures Risk Assessment is timely and adequately addressed
- Support site risk management process
- Oversees the complaint product evaluations activities for the site, and maintains track and trending of product performance / results of product evaluations for escalation to CAPA
- Participates as a key member in both external and internal audits and is responsible for the local NCR and CAPA processes and directed inspections
- Actively participates in Management Review
- Facilitates and leads the plant CAPA Review Board
- Report NCR and CAPA results / metrics to the Plant QA Manager and Management staff as applicable and makes recommendations for improvement
- Partner with management to develop and implement meaningful trending of NCR's and CAPA performance
- Ensure major non-conformances, trends, and near misses are escalated to management and prioritized commensurate with risk
- Lead major issues, when appropriate
- Responsible for ongoing CAPA process and CAPA system training (beginners and continuing education for experienced associates.)
- Opens new CAPA's and assigns the team leader in the computer system
- Ensure the appropriate resources are assigned and held accountable for nonconformance resolution and CAPA effectively
- Work with team leaders to establish and track an effectively measure for each CAPA
- Manage the NCR/CAPA system, to include monitoring and ensuring Due Date Adherence
- Leverage Process Excellence tools to effectively implement CAPA using a DMAIC approach
- Responsible to mentor both technical and non-technical resources in investigation, troubleshooting, escalation, and resolution of product and process quality issues, NCR and CAPA
- Works with CAPA team leaders to charter new CAPA's
- Provides guidance to team leaders and approvers and reviews all CAPA's to ensure documentation is complete before CAPA closure
- Communicate with NCR / CAPA leaders globally to ensure alignment, resolve problems, and share best practices
- Supports the continuous improvement of the CAPA process and computer system
- Partner with IM and the data warehouse team to drive improvements in business intelligence to facilitate effective tracking and trending
- Perform other work-related duties, as assigned by site management
- Minimum 5 years’ experience in Operations, Engineering and/or Quality Assurance is required
- Background in Medical Device Industry, preferred
- Experience leading CAPAs is an asset
- Knowledge of regulatory requirements (ISO, QSR, etc.), preferred
- Experience with external auditing bodies, preferred
- Process Excellence Green Belt Certification with demonstrated problem-solving and statistics skills, preferred,
- Demonstrated project management skills with strong results orientation, required
- Strong communication, influencing and presentation skills, required
- Bilingual, fluent in English and Spanish
- Physical Demands: Normal office environment, mental efforts
- Work Environment: Frequent travel, Flexible to work on different shifts
- Contacts: Frequent contact with Ethicon facilities and Executive Management required
25
Program Quality Systems Manager Resume Examples & Samples
- Develop and implement the program-level quality management framework for the entire program; includes design quality management, construction quality management, and adherence to all appropriate laws, regulations, and standards
- Oversee the development of quality management systems to include the comprehensive quality management plan as an essential component of the program management plan
- Evaluate and ensure successful administration of designer and construction contractor quality management programs to include the development and rigorous execution of project-specific quality management plans
- Conduct audits of designers and construction contractors to check compliance
- Establish a non-conformance management system to aid in the identification, tracking, and resolution of all deficiencies
- Serve as a key leader within the program and ensure that all program standards are maintained and enforced
- Develop briefings and presentations as necessary for client, stakeholder, and AECOM senior management
- Train subordinate leaders in quality and quality management practices and protocols
- Conduct audits of AECOM internal systems and ensure compliance with all AECOM policies, protocols, and the AECOM Project Delivery System
- Background in project/program management
- Able to work as a senior leader of a dynamic and fast moving team
- Experience in managing a small team
- Ability to systematically analyze complex problems, draw relevant conclusions and implement appropriate solutions
- Excellent negotiating and persuasive skills, both in one-on-one and group situation
26
Quality Systems Manager Resume Examples & Samples
- Recruitment of the quality team in conjunction with HR business partner assistance
- Development of detailed product and site transition plans that will ensure robust process definition and right first time product quality
- Manages the planning and execution of last article / first article activity for all parts being transitioned
- Act as the expert on various customer and industry quality system models such as ISO9000, AS9100 and D1-9000. Recent experience with the revision C version of AS9100 is preferred
- Adherence to the GKN Life Cycle Gate management process including the assessment of risks and identification of associated mitigations
- Ensure that technical expertise is provided to team members, suppliers and third parties ensuring compliance with contractual, company and regulatory requirements
- Ensures that export compliance, data protection and other relevant regulations and legislation for the region are followed
- 2+ years of experience leading quality teams/organizations
27
Quality Systems Manager Resume Examples & Samples
- Serving as a backup Management Representative for audits/inspections
- Maintaining communication with certification bodies
- Staying abreast of changes to QMS standards, ISO13485 and 21 CFR parts 820, 4, 11, 210& 211
- Providing direction and support to personnel regarding new/revised standards and regulations
- Facilitating the development and implementation of QMS improvements
- Assisting personnel with QMS issues
- Communicating QMS issues to management
- Supporting compliance to the Safety and Environmental policies and programs
- Aiding in setting priorities and participating in Lean Six Sigma initiatives and projects
28
Quality Systems Manager Resume Examples & Samples
- Lead the plant Quality staff to ensure compliance to the overall Quality Management System and to drive Continuous Improvement
- Provide coaching, mentoring and leadership to the plant Quality staff
- Lead and own the plant Management Review process
- Ensure and drive compliance with the domestic regulatory and international standards and requirements
- Lead the site’s quality improvement process; including data analysis, improvement projects and process capability to improve key metrics as measured by the product/process quality dashboard
- Manage the complaint handling processes to ensure customer responsiveness and product and process improvements
- Lead the quality plan development and execution for manufacturing site New Product Development ensuring successful product design transfer
- Lead qualification and monitoring tasks for manufacturing site key suppliers to ensure effective supplier performance in the manufacturing process
- The position requires a level of authority to conduct and direct required activities. Examples of this are: Quality planning, complaint management, production and process controls, CAPA management, supplier management and new product design transfer
- This position requires 5 – 10 years experience in a Manufacturing, Engineering or Quality/Continuous Improvement environment. Experience with supervision of technical and regulatory professionals is highly desirable
- This is a middle management position involving the supervision of a small team, composed of either technical or professional employees
- Proven leadership ability to manage a team, make decisions and deliver results
- Ability to solve problems at an operational and strategic level, manage multiple priorities and conduct data analysis
- Working knowledge of IS0 9000 and FDA GMPs
- Ability to set goals and meet project deadlines
- Effective communication skills, both oral and written are required
- Ability to establish and maintain an effective working relationship with subordinates, peers, and all levels of management
- Experience with Class III or significant Class II devices
29
Quality Systems Manager Resume Examples & Samples
- Must have expert GMP Compliance, Product Quality, and in-depth Risk Management knowledge
- Ability to effectively prepare communications to identify potential problems to management and the group with clarity and a high level of accuracy
- Provide guidance to other employees in the interpretation of compliance and technical/scientific issues across a majority of the job function. Develop employees and coach them to bridge knowledge gaps
- Strong authorship and be able to critically review reports while effectively providing input and expressing Quality Risk management principles
- Action-oriented, customer-focused and skilled in decision-making, building relationships, problem solving, conflict management, planning and organizing, resource allocation, coaching others, and analytical thinking. Must possess an independent mindset and tenacity
- B.A. in a related field; 7+ years experience in the pharmaceutical industry with >3 years experience in investigational drug development, GMP manufacturing packaging and/or labeling operations preferred
- Strong background in cGMP requirements
- Demonstrated skills in project management and handling multiple projects simultaneously
- Familiarity with regulatory requirements with respect to investigational drug products
- In depth knowledge of clinical trial documentation and retention requirements
- Demonstrated teamwork and collaboration skills
- Ability to lead, motivate, and develop employees
30
Corp Quality Systems Manager Resume Examples & Samples
- Develop and lead work plans and initiatives to achieve and sustain the ISO compliance of the quality management system across the organization
- Engage with the plants and Corporate Value Stream teams addressing quality management system gaps and corrective actions in order to develop strategic improvement plans
- Lead the development, maintenance and deployment of the Quality Manual, corporate SOP’s, and associated forms and records
- Manage the internal quality audit program to ensure the company is compliant to ISO standards, corporate SOP’s, process specs and best practices in order to achieve sustainable World Class performance
- Develop scorecards and reports to measure the effectiveness of Quality System
- Aid in the development, maintenance and assessment of the American Woodmark Operating System
- Organizational Development: Develop functional core competency training and training roadmaps
- Serve as a team leader or team member on cross-functional teams, as needed, in order to help the company continuously improve
- TEAMWORK: Support efforts by all members the American Woodmark team to continuously improve company performance
- Bachelor Degree required, Advanced Degree preferred
- Minimum experience of 7 years in a manufacturing field with some supervisory experience in a multi-site organization is required
- Experience developing, deploying and managing a recognized quality system, such as ISO or TS, is required; Knowledge of World Class Operational Excellence models, such as Baldrige or Shingo, are preferred
- Knowledge of Lean and Six Sigma methodologies and professional certification such as ASQ CQA or RABQSA Lead Auditor preferred
- Ability to work in a team environment as well as independently is required
- Ability to work internally and externally at all levels in domestic and international is required
- Track record of successful project management and team experience are required
- Personal computer skills in a networked environment, Microsoft products (Word, Excel, PowerPoint, Outlook, Sharepoint) are required
- Management style and duties must be consistent with and support AWC’s CITE Principles, Supporting Values, Mission and 2019 Vision
31
Quality Systems Manager Resume Examples & Samples
- Lead team to facilitate, and support Management Review, Internal Audits, Complaint Management, CAPA Management, Quality Metrics, Nonconformance Management, Field Actions, Software Validation, Training, Maintaining Certifications and Registrations. Maintain current knowledge of applicable cGMP/QSR, ISO, and other related regulations
- Manage department budget in accordance with Annual Operating Plan
- Write and maintain Quality Procedures, to include Work Instructions and SOP updates. Ensure the Quality functional requirements are compliant with corporate procedures as well as industry standards and regulations
- Implement, maintain, and/or improve the quality system to meet or exceed regulatory and ISO compliance
- Responsible for specific global processes as the Global Process Owner. Responsible for administering process improvement and evolution for the global process
- Other project work as assigned
- Solid oral and written communication skills
- Planning and organization. Ability to manage multiple projects/responsibilities at one time
- Experience in creating and implementing a quality system in a Medical Device Company preferred
- Leadership, Collaboration
- Driving Alignment, Empowerment, Accountability
- Technical or Life Science degree (BS) or equivalent medical device experience
- Minimum 2 years management/supervision experience
- Minimum 5 years working in Medical Device or Orthopedic company preferred
- Minimum 5 years in a Quality Engineering, Quality Systems, or Internal Auditing role, or combination
- Combination of education and experience may be acceptable
32
Quality Systems Manager Resume Examples & Samples
- Oversees and manages Quality Systems; develops detailed action plans, defines resource requirements, performance measurements, and aligns staff with the overall quality strategic objectives
- Responsible for planning, implementing, and reviewing the strategic quality goals
- Facilitates inspections and audits with regulatory and third-party agencies and follow-up responses to findings
- Facilitates and manages the internal and external proficiency testing program. Responsible for ordering external PTs and creating schedule for internal PTs
- Responsible for the complaints management program including trending and communication of issues to the complaints management team
- Manage a team of 1-5 direct reports on the Quality Assurance team under the following job profiles
- Quality Control Technician,
- Quality Systems Specialist,
- Sr. Quality Systems Specialist,
- Quality Systems Coordinator
- Bachelor of Science degree in a life science related field required
- Quality-related certification (i.e. ASQ, CPHQ, etc.)
- Proficient with MS office programs (Word, Excel, Powerpoint, etc.)
- Strong analytical, written/verbal communication, interpersonal, and relationship building skills
- Knowledge of applicable federal and state laws and regulations
- Minimum of 5 years experience in a clinical lab environment or equivalent
33
N Quality Systems Manager Resume Examples & Samples
- Direct development, initiation and monitor quality manufacturing techniques to track financial results and report on quantifiable goals and objectives
- Develop, implement and manage strategic / tactical programs to increase quality and reduce cost
- Integrate existing quality systems between the LR/CF product lines and elevate to a benchmark status
- Coordinate and review customer complaints for compliance with 8D process and timely completion. Monitor rates of receipt, analysis and completion
- Ensure alignment with field service team to measure and reduce COPQ
- Manage contracts and ensure all QA requirements and specifications are met or exceeded
- Interface with suppliers on specific contracts to ensure their adherence to QA requirements as they pertain the supplier scorecard
- Provide oversight to establish, initiate and monitor any internal control policies relating to quality performance initiatives. Develop and communicate quality performance data to all relevant plant personnel for corrective action
- Lead the development of all procedures required for ISO 9001 certification and re-certification. Maintain all quality performance records and documents. Coordinate ISO visits with necessary staff and manage any corrective actions that occur as a result of the ISO audits
- Manage the creation and implementation of the technical training programs for SPC, ISO 9001 procedures and problem solving. Ensure QA Engineers / Techs are conversant with all programs and can adequately train production or other Engineering staff to processes
- Apply performance, test and inspection data to investigate causes for product nonconformance. Identify issues and serve in the lead role to facilitate problem resolution. Develop internal / external inspection, gage calibration functions and the supplier quality program
- Define performance metrics to measure, compare or evaluate quality factors, such as cost of quality, on time performance, first pass yield, scrap, rework and warranty & customer complaints to ensure compliance maintains or exceeds metric standards
- Participate in VOC supplier meetings to share performance results, obtain supplier input, collaboratively analyze Nash & supplier feedback, develop shared solutions, implement new or improved processes and discuss Quality changes
- Effective management and leadership of Quality Team
- 10+ years’ experience, in a N. American operating environment, leading quality management and quality assurance programs preferably for large rotating equipment products or highly engineered industrial products/systems
- Bachelor’s Degree (or international equivalent) in Quality or related field, i.e., Mechanical, Industrial or Manufacturing Engineering,
- Proficient in computer software programs for business, such as Microsoft Office Suite & Lotus Notes, and relevant supply chain software, such as SAP and ERP software
- Demonstrated ability to effectively interface with all levels of the organization, as well as customers, government officials and vendors
- Demonstrated effective analytical and root cause problem resolution skills
- Demonstrated ability to coordinate cross-functional teams and effectively resolve process issues
- Demonstrated experience applying business and management principles involved in strategic planning, resource allocation & coordination [material, money & people], leadership techniques and production methods, end product knowledge, product & service competitors
- Demonstrated ability to leverage principles and processes that provide quality customer services, including customer needs assessment, meeting quality service standards and customer satisfaction evaluations
- Real world, practical application of engineering science & technology, which includes applying principles, techniques, procedures and equipment to the design & production of goods & services
34
Quality Systems Manager Resume Examples & Samples
- Demonstrated use of GSK Values
- Patient Focus
- Act with Integrity
- Transparency
- Respect for People
- Ensure Halal Assurance System is operating in accordance with General Guidelines of Halal Assurance System LPPOM MUI for applicable products/markets
- Ensuring that process needed for the QMS are established, implemented and maintained
- Reporting to Senior Management on the performance of the Quality Management System and any need for improvement
- Ensuring the promotion of awareness of regulatory and customer requirements throughout the site
- Liaising with relevant Regulatory Bodies e.g. Notified Body and Competent Authority
- Perform duties in a compliant manner and behave in accordance with site SOP’s, GSK EHS standards and guidelines and relevant legal requirements
- Read and understand Standard Operation Procedures applicable to role
- Report all accidents, incidents and any EHS issues using the appropriate process /system to your line manager or, if required, the Occupational Health Advisor
- Maintain work area in an inspection ready state and clean as you go to maintain good safe housekeeping standards
- Be aware of the impact of your job activities on EHS issues
- Ensure all engineering changes made have safety considerations and best practices as core attributes
- Ensure basis of safety files are available and up to date for processes
- Participate fully in our site’s quality initiatives and ensure that all relevant quality standards are adhered to
- Maintain GMP standards where appropriate to your role
- Read and understand relevant Standard Operating Procedures and Global Quality applicable to role
- Management Policies relevant to your job role
- Attend training and complete assessments as required
- Ensure Quality and GMP are at the forefront of changes proposed
- Ensure Inspection Readiness Every day
- Identify and co-ordinate the activities and resources to prepare for the
- GMP and Regulatory Compliance, Quality teams performance, Quality Systems departments on both sites, Suppliers, Health Product Regulatory Authority (HPRA) and SGS
- Recruit suitable candidates as required
- Effectively manage and develop talent of employees
- 3 – 5 years experience in a pharmaceutical / healthcare industry in a Quality management capacity
- Understanding of appropriate Directives, Standards, Quality Managements Systems related to the manufacture of Medical Device and Medicinals for required markets
- Understanding of Japanese Quality Requirements and Working Relations
- Ability to provide key input into Quality management decisions as management team member
- Ability to effectively lead, develop and motivate the QS team
- Understanding of and ability to implement GPS initiatives
- Ability to communicate with a wide variety of people at all levels both within the sites and GSK and externally through appropriate skills: - Verbal / written, Negotiation, Report writing, presentation, Empathy / affiliation and listening
- Demonstrated ability to problem solve
- Demonstrated ability to effectively plan work and to manage projects
- Third level science-based degree (preferably post graduate)
- Understanding of appropriate Directives, Standards, Quality Management Systems related to the manufacture of Medical Device and Medicinal for required markets
- Ability to provide key input into management team decisions
35
Quality Systems Manager Resume Examples & Samples
- Responsible for the consistent and correct execution of QS global procedures within the site to ensure the quality and compliance of processes and records for Change Control, Records Management, CAPA, NC, Customer Complaints Investigations, QPR and QSMR and Filed Action Investigations
- Develops competency of resources within the site that execute CAPA, NC, Customer Complaints, QPR and QSMR, by providing training and guidance on the execution and documentation of these processes
- In partnership with the site Quality leaders, oversees the timely and compliant execution of site NCs, CAPAs, Customer Complaints, QPR and QSMR, by championing collaboration across functions and sites and developing action plans, as required, in order to improve or sustain associated metrics at target levels
- In partnership with the site Quality leaders, oversees the Product Escalation process for non-conformances, complaints or other issues potentially impacting product in the field. Reviews related investigations and corrective action plans to avoid reoccurrence of the nonconformity. Ensures timely closure of escalations
- Identifies needs to meet and improve system performance of NC, CAPA, Customer Complaints, QPR and QSMR at the site level, and escalates to appropriate representative and management in a timely manner
- Collaborates with The Regional Quality System Leader in the deployment of QS initiatives impacting the site that promote the continuous improvement of the QS and ensure continuity of the application of globally shared processes and systems at site level
- Supports compliance activities by participating in audit readiness; assisting in Internal and External audits; serving as Subject Matter Expert for Change Control, Records Management, NC, CAPA, Customer Complaints, QPR and QSMR during audits; managing the investigation, response, and remediation of site-specific QS audit observations
- Oversees the execution of Document Control across the site. Partners with Global QS in the implementation of system improvements and training deployment, as required
- Other Quality Systems related tasks, responsibilities, and projects as assigned
- Universal Leadership Competencies: (Connect) Cultivate external relationships and partnerships, Forge internal collaboration across all levels of the enterprise, (Shape) Challenge the status-quo; lead and adapt to change, take and manage risks, (Lead) take ownership for talent acquisition, performance and development of self and others, Engage in transparent and constructive conversations
- Differentiating Competencies: (Connect) Be insight-driven to uncover unmet needs, (Shape) Translate insights into viable products and solutions that create value, (Deliver) Empower people to act with speed, agility and accountability
- Specific Technical Skills Required: Project Management; Technical Writing; Quality System Integration, Quality Auditing, and Risk Management knowledge. Ability to apply principles of logical or scientific thinking, root cause and statistical analysis. Presentation Skills. Working experience of applicable software (Microsoft Word, Excel, Power Point, Microsoft Project)
- At a minimum, BS degree in Engineering / Scientific or associated relevant technical / Quality discipline is required; Engineering degree preferred
- Five (5) years related experience in Medical Device or Pharmaceutical, or Aerospace environment, or equivalent combination of education and experience is required
- Solid knowledge of ISO and QSR regulations required; experience with front and back room leadership in third party inspections required
- Experience with root cause investigation and change management is required
- Direct supervision experience is required
- A Certification in process excellence preferred
- This position will be based in Elmira, NY and requires up to 10% travel4724170314
36
Quality Systems Manager Resume Examples & Samples
- Manager for the Quality System, Supplier Quality, Incoming Inspection and Calibration teams at SenDx
- Project lead on cross functional process improvement projects
- Help establish quality system at a new manufacturing site
- Collaborate with R&D as Design Control Specialist to deliver the right documents in the right quality in the development process to successfully register the products globally
- Continuously improve and develop processes for Design Control, Risk Management, Usability Engineering and Design for reliability
- Make quality related decisions and sign off on quality documents on behalf of the QA management
- Specialist in verification and validation of products and processes
- Support manufacturing value streams in quality related matters when needed
- Ensure the processes are in compliance with both relevant regulatory and internal requirements, and are implemented and maintained so the necessary governmental approvals are maintained
- Is up-to-date with standards, regulatory requirements and directives applicable for SenDx products
- Ensure the QA system is kept lean and updated and that the organization complies to the system
- Work with Radiometer Medical to develop and implement global procedures
- Benchmark with other Danaher companies to explore and align best practices
- Utilize Danaher Business System (DBS) concepts and tools in the performance of daily activities
- 5-7 years in the medical device, pharma, or dental industries; experience from managing teams
37
Senior Corporate Quality Systems Manager Resume Examples & Samples
- Manage, maintain and enforce internal audit control policies across the enterprise
- Drives R&D process review sessions across for all VZT brands (VZT, NWF, Telogis and Fleetmatics)
- Analyze current state and work with functional leaders and define business processes to meet defined business objectives
- Ensure that all IT processes and sub-processes are documented so that it enables maturity of operations practices
- Review and analyze IT process and sub-process documents and Approve or Reject them based on their adherence to documented policies, and assist in determining the corrective actions required to align them with industry standards
- Participate in determining long term planning and contribute to overall business strategy
- Document and report status of audit plans to appropriate technical and business teams to ensure that proper documentation and audit trails exist for all activities performed related to the audit process
- Assure that each process documents is approved by the required approvers before implementation
- Communicate high risk/high impact audit issues to the R&D leadership team as needed for their review and approval
- Measure effective execution of customer contracts
- Lead projects determined by the executive team to propose new solutions to business process problems based upon both quantitative and qualitative data within Corporate Quality
- Lead and coordinate the agenda for quarterly audit meetings
- Use Lean Six Sigma problem solving tools, including process mapping
- Update, maintain and publish Audit Calendar; and organize and manage the process
- Transform new designs to standardized work with assigned responsibilities
- Identify needed metrics to drive and sustain business improvement
- Create and deliver training presentations
- Perform ISO 9001 and other ISO process audits to determine business effectiveness, and implement and maintains ISO 9001 compliance for R&D
- Respond to quarterly and annual audit requested related to process documentation
- Collect and report on trends/metrics to proactively identify areas for improvement
- Capture, track and publish process efficacy using established Key Performance Indicators (KPIs) and Critical Success Factors (CSFs) through a measurement system that tracks adoption, utilization and proficiency of individual processes
- Maintain and improve process effectiveness (quality), process efficiency (cost), process performance (throughput) and process vulnerability (security) through providing knowledge, expertise and training on the use of the process and tools
- Collaborate with team members (especially Security Operations) to identify and operationalize IT processes and establish new KPIs as needed
- 7+ years' experience working with and improving processes within a standard ITSM framework such as ITIL and good knowledge of general IT concepts, e.g. applications, servers, network, database, etc
- Strong analytical, organizational, and problem-solving skills
- Excellent communication skills with the ability to communicate clearly and effectively
- Strong customer service orientation with a focus on meeting and exceeding customer expectations
- Ability to effectively manage client & staff relationships, promptly respond to queries, ensure promises are kept, and manage expectations
- ISO 9001 Internal Auditor or equivalent
- Six Sigma Green Belt or equivalent
- Disciplined problem solving skills with excellent follow-through using DMAIC process
- Advanced planning and organizational experience within fast-paced/dynamic business environments
- BS/BA required – business or computer science discipline
- Determined and committed to perform at highest quality and excellence
- Laser-sharp focus on goal of on-time and zero-defect delivery
- Highly energetic and strongly believes in on-going learning in order to optimally exploit his/her potential on the job
- Constantly works towards being the best and to succeed at current assignment/project
- Entrepreneurial mindset and successfully challenges existing paradigms
- Has a strong vision and thinks expansively and outside the box to consistently generate and evaluate highly innovative ideas and solutions
- Willing to take risks, anticipates the consequences of decisions and will generate plans to address them
- Willing to go against the grain, has courage to take calculated risks and will have the ability to present his/her point of view in a positive and effective manner
- Takes personal responsibility for ensuring customer satisfaction, takes customer perspective and will proactively work to address the customer’s current problem and future requirements
- Ability to effectively leverage diverse resources. Works hard to foster positive relationships and will develop win-win solutions when conflicts arise. Builds relationships by making self highly approachable, seeks input from others and will actively listen to concerns and alternate points of view and makes others feel valued and supported
- Team player – willing to take calculated risk
- Legal and/or Regulatory experience
- Familiar and comfortable working in a 24x7, high-availability service delivery environment
- No particular bias towards specific technologies, vendors, or products
- Effective at driving short-term results that are consistent with long-term goals
- Skilled at operating in a matrix environment
- ITIL Foundation Certification or higher
38
Quality Systems Manager Resume Examples & Samples
- Role is the Guardian of Q&FS compliance and challenger of all functions across the site to drive Continuous Improvements in support of the Site’s Innovation & Renovation process, while fostering a cross functional quality, compliance and performance culture
- Is responsible for the leadership and the development, implementation and management of all Site Q&FS programs and activities, including creating guidelines for testing novel products with Consumers in various venues
- Provides technical expertise and support to ensure compliance to NQMS, FSSC 22000 / regulatory requirements, product quality (PrIME) attributes, and new food safety standards with proprietary raw materials, innovative processes and new routes to Market
- Utilizes tools such as auditing, risk assessments/modeling, process evaluation, trend analysis to achieve Site and Global CT-PTD objectives, including providing expertise to Frozen & Chilled Factories in the Nestlé Group
- Leadership to the markets and factories is a key activity – communicate the latest scientific and technological information for practical application in the factory
- Reports to the Quality & Food Safety Group Manager
- Minimum of a Bachelor of Science (B.S.) degree in Microbiology, Food Science or similar discipline. Masters preferred
- Must be able to practically apply scientific knowledge to product quality and process safety
- Minimum 5-7 years Quality Management experience, preferably in food manufacturing or consumer goods industry. Within this there must be 2-3 years of factory QA experience, preferably at a QA Manager level
- Must have strong knowledge and understanding of food safety / HACCP, GMP’s, Allergen Controls, Sanitary design/controls, pest control, related food regulations, specifications, product release, analytical and microbiological lab methods and food technology processes
- Facility utilities support (QMS, HACCP, sampling, data management, troubleshooting)
- Competence in Quality & Food safety related systems & principles
- Competence in Microbiology and Hygiene monitoring
- Strong demonstrated verbal / written communications, influencing skills, analytical and problem solving skills. Must be detailed and results oriented
- Statistical analysis & Focus Improvement (FI) experience is preferred
- Nestlé NQMS, FSSC 22000, HACCP & FDA-PCQI training or similar Food Safety and Quality Systems training. Implementation experience on Food Safety and/or Quality programs is strongly preferred
39
Quality Systems Manager Resume Examples & Samples
- Ensuring Metal Coaters is compliance with Quality Policies established by the Metal Coaters Management Review Committee
- Analyzes KPI variables to diagnose chronic problems that result in poor quality, yield loss and field rejections of finished product. Provides corrective actions to eliminate chronic quality non-conformities or field rejections
- Monitors technical, product and process developments and serves as a company technical representative to relevant trade association committees. Ensures that the facility management group is updated with regard to product development changes and technological advances
- Plans and leads all plant-wide quality and yield improvement activities
- Responsible for specification and evaluation of all incoming raw materials to Metal Coaters (i.e. Paint, Metal Substrate, Chemicals, Solvents)
- Ensures the compliance of raw material suppliers to Metal Coaters Quality System requirements
- Responsible for all of the Quality Assurance Systems (i.e. technical standards and test procedures) in place to produce and evaluate finished products
- Ensures that all finished products meet or exceed customer requirements and that all non-compliant (HFI) material is diagnosed and handled properly
- Responsible for ensuring departmental employees are trained and available to safely support the production department through testing, evaluation and processing of raw materials and finished products
- Ensures all Metal Coaters employees are trained relative to their Quality Awareness responsibilities
- Assists Sales with all aspects of customer technical service, including product development (R&D), product specification issues and development of new customers/opportunities
- Responsible for the Customer Complaint Resolution process. Ensures timely resolution of customer complaints (claims)
- Responsible for understanding and complying with the fundamental principles associated with the Quality and Environmental Managements systems in place at Metal Coaters
- Responsible for communicating daily with all levels of employees in order to assist in resolving problems and achieving company goals
- Keeps equipment and work area clean and orderly
- Ensure compliance with federal and state laws
- Perform all duties in a safe manner
40
Quality Systems Manager Resume Examples & Samples
- Creation and maintenance of HICSE’s Quality Management System to ensure delivery of quality products and services and compliance with the relevant quality standards
- Maintenance and progression of HICSE’s Quality Accreditation
- Adherence to the HICSE Business Management System to maintain and enhance customer satisfaction through processes and leadership
- Identifying and recommending to senior management areas for improvement in the quality management system and the wider company at large
- Guiding and preparing the company through external and internal audits
- Ensuring that current and future HICSE products meet the quality requirements
- The creation, implementation and management of the HICSE Quality Plan
- Managing the HICSE Quality Team
- Implementing and managing the HICSE Audit Programme and Internal Auditors
- Managing the HICSE Quality Review Team and chairing Quality Review Meetings
- Maintaining, monitoring and developing the HICSE procedures and systems and ensure their compliance to BS EN ISO9001, TickIT+, BS EN 50128 and other relevant standards
- Measuring the application of quality processes and identification of areas for improvement
- Reporting of relevant quality issues to the HICSE Management
- Ensuring customer satisfaction through surveys to the HICSE Audit Programme
- Implementing agreed improvement plans
- Thorough knowledge of the HICSE BMS and other relevant quality standards
- Internal Auditor qualification
- Lead Auditor qualification
- Good knowledge of BS EN 50128
- Quality Management Qualification or relevant experience
- Ability to communicate at all levels of the business, customers and suppliers
41
Quality Systems Manager Resume Examples & Samples
- Bachelor’s degree or equivalent combination of educational background and work experience in Banking/Financial Services/Consumer Lending preferred
- 10 years of software quality assurance and test management experience and 5 or more years in a team leadership capacity with proven ability to lead testing projects of all sizes
- Technology consulting background preferred with ability to lead and manage concurrent projects/teams and customer expectations
- Strong background in development of solutions and/or supporting IT applications for diverse business needs
- Prior experience implementing enterprise wide process improvements in support of testing and software development
- Deep understanding of the software development lifecycle through deployment
- Proven ability to lead testing projects of all sizes
- Experience with Shaw Retail, Shaw Collections, or Shaw Leasing system or similar consumer lending platforms are highly desired
- Good written, oral communication and interpersonal skills
- Strong teamwork skills; ability to positively contribute to the overall success of the project team
42
Senior Quality Systems Manager Resume Examples & Samples
- Experience managing or working within Quality Management System
- Experience leading/receiving external inspections
- Experience working in a regulated environment
- Skill in multiple computer based tools and software programs such as Word, PowerPoint, Excel, Visio, MS Project or site builder etc
- 7+ years of quality, manufacturing, or regulatory experience
- 5+ years of progressive leadership experience
- Experience with ISO 13485 and FDA 21CFR820, Quality System Regulation
- 7+ years’ experience within Quality Systems or Quality Assurance responsibilities or equivalent
- Experience at managing large projects and influencing stakeholders at all levels
- Experience at facilitation, consensus building and/or conflict resolution
- Experience in business process development
- Master’s Degree (MBA/MAOL)
- Working knowledge of process improvement skills including Six Sigma, Lean Sigma, Knowledge Management and Process Design
- Strong project and time management skills
- Proven experience in achieving results through influence, management and motivating teams
- A thorough working knowledge of the following: ISO 14971; Medical Device Directive; and other applicable Standards that apply to medical device design, development and manufacturing
- Organizational Change Management Certifications or experience putting Change Management models into practice
43
Corporate Quality Systems Manager Resume Examples & Samples
- Manage Corporate Quality Document Control Product Configuration Specialist (Change Analyst) function, ensuring timely and accurate processing of Engineering Change Requests and Temporary Change Authorizations
- Provide quality system technical support for the Quality System Simplification Project team, including writing and editing procedures and related documents
- Provide project management support for the Quality System Simplification Project team, including overseeing the activities of the Quality Specialist responsible for coordinating the project team (e.g., scheduling meetings, issuing minutes and following up on action items, creating executive slide decks, maintaining repository of all project related documentation on Sharepoint site)
- Work on complex problems in which analysis of situations or data requires an in-depth evaluation of various factors
- Exercise judgment within broadly defined practices and policies in selecting methods, techniques and evaluation criteria for obtaining results
- Representing Quality System Simplification project team as designee of team leader to deliver executive updates and other communication activities
- Bachelor's degree required, preferably in a science or engineering discipline
- Requires a minimum of 10 years of experience (or Master’s degree with 8 years) in a medical device or pharmaceutical quality system (QSR/cGMP and ISO 13485) supervisory, decision-making role
- Project Management Professional (PMP) certification preferred
- Lean/Sigma Green Belt or Black Belt preferred
- ASQ certification (e.g., Biomedical Auditor, Quality Manager) preferred
- Results-oriented, positive “can do” attitude with demonstration of appropriate urgency
- Highly detail-oriented with demonstrated understanding of broader context, priority and significance
- A hands-on individual who enjoys challenge, is capable and dedicated to getting the job done with minimal direction
- Demonstrated track record of developing talents of self and others, including performance management
- Strong interpersonal relationship skills including negotiating and relationship management
- Ability to translate highly complex and technical information to all levels of the organizations via training module development and delivery
44
Plant Quality Systems Manager Resume Examples & Samples
- Develop and implement the site specific Quality Systems and Food Safety Plan including Quality Management strategies, direction, and policies with the goal of protecting the business, reducing variation and waste, and growing the business
- Accountable for ensuring compliance with Colgate /Hill’s Quality Standards, Local, Governmental, and International Quality and Environment, Occupational Health & Safety (EOHS) and Regulatory standards and guidelines and will interface with all agencies to communicate, address, and resolve any issues
- Responsible for execution of Environmental and Micro programs and the Cleaning & Sanitation (C&S) Program at the facility both on finished goods and processing / packaging equipment
- Responsible for reporting Key Performance Indicators (KPI’s) of Quality systems both internally and externally on a monthly basis or higher frequency as determined by business
- Accountable for the robustness of key Quality Systems including but not limited to Incoming Component & Finished Product Inspection & Release, Validation, Corrective and Preventative Action (CAPA), Change Control, Internal Audits, Laboratory Management and Documentation Management
- Manages the development and implementation of the site’s Quality Audit program to ensure conformance with standards, quality-related regulatory requirements, Good Manufacturing Practices (cGMP’s), and leads the development and implementation of Continuous Improvement (CI) and action plans to address any internal/external quality or food safety audit findings
- Support implementation of Quality Assurance and Food Safety Initiatives and ensure personnel adhere to Hill's policies, safety standards and cGMP's, including Quality Assurance and Safety
- Accountable for the site’s consumer satisfaction programs such as consumer complaint tracking and reduction of plant controllable complaints
- Administers all Performance Management and Coaching / Feedback activities and provides effective career development and planning for all members of the Quality Team at the site
- Participates with other Plant Managers and Corporate Quality on continuous improvement projects
- Functions as a key member of the Site Strategic Team which supports the plant’s vision, provides resources to achieve plant strategy, ensures decision making processes are consistent with guiding principles, establishes clear direction and CI expectations, leads and supports change for the plant
- Prepares and manages operating budgets for variable and fixed overheads for the Plant Quality Team
- Bachelors Degree in Chemistry, Engineering, Microbiology, Biochemistry, Food Science or a related technical field
- 8+ years' work experience in Quality, Supply Chain, Research & Development or other technically related field
- 3+ years' work experience in a food manufacturing facility
- 3+ years' supervisory experience
- Prior direct experience and active participation in an audit inspection by a regulatory agency
- 1+ years' project management leadership experience
- Master's Degree in Chemistry, Engineering, Microbiology, Biochemistry, Food Science or a related technical field
- 7+ years' experience in Quality, Supply Chain, Research & Development or other technically related experience
- 5+ years' experience in a food manufacturing facility
- 5+ years' supervisory experience
- 5+ years' experience with the Hill's product portfolio and business systems
45
Quality Systems Manager Resume Examples & Samples
- 1 In conjunction with other departments, creates and monitors QC systems which assure that all in-process and finished goods meet established government, Mondelez and internal specifications, as well as being manufactured in accordance to all Food Safety Measures
- 2 Maintains current knowledge of cereal chemistry, promoting and executing new application of analytical tools
- 3 Performs fact-based assessments/audits of Manufacturing Systems ensuring that all records, procedures, processing, packaging and equipment are in compliance with all federal, state and other regulatory requirements
- 4 Assists in the development of new quality/regulatory systems and personnel and also serves as a resource for plant quality and manufacturing functions
- 5 Responsible for leading facility internal audit process
- 6 Will lead the QA Pillar in an IL6S environment
- 1 Change management skill building
- 2 Enhanced knowledge of customer service policies, procedures and programs
- 3 Solid knowledge of IL6S/TPM with proven experience
- 4 Excellent change management skills and High Performance Work System
- 1 Motivating others
- 2 Developing direct reports & others
- 3 Problem solving refinement
- Bachelor in Quality, Business Administration, Food Science or related fields
- Proved experience leading and managing a diverse workforce
- Advanced experience in production manufacturing quality sanitation experience
- Leadership in a Team Environment
46
Quality Systems Manager Resume Examples & Samples
- Manage the Quality System team and ensure that both regulatory and business requirements are met in the daily running of the department. This includes motivation, training and appraisal of QS staff
- Responsible for processes within Document Control, Customer Quality and Master Data area
- To take a leadership role in driving improvement initiatives in the Quality Management system across the site
- Drive and enhance a compliance culture though-out the site
- Providing Quality Systems support for all business units and sites
- Preparing for and supporting external audits (TUV, FDA, customer etc)
- Ensure adequate monitoring and measurement of processes, and reporting same to management
- Ensure Quality System processes are lean, compliant, user-friendly and are well understood through-out the organization
- Be responsible for Health & Safety within assigned areas
- Any other duties assigned from time to time
47
Quality Systems Manager Resume Examples & Samples
- Quality Management and Leadership - Understand quality management philosophies (e.g. Deming) and tasks such as understanding customer and business needs, basic goal setting, planning processes and the use of results and customer satisfaction data for improvement. Able to demonstrate use of these approaches. CQE (Certified Quality Engineer), or with 2 years’ experience in this area
- Quality System Development, Implementation and Verification - Communicate quality management philosophies (e.g. Deming) and lead tasks such as understanding customer and business needs, basic goal setting, planning processes and the use of results and customer satisfaction data for improvement. Use of these approaches routinely. Passed ASQ CQM (Certified Quality Manager) exam and/or have 4 years’ experience in this area
- Plan, Control and Assure Product and Process Quality (was Inspection and Audit) - Knowledge of basic quality management philosophies (e.g. Deming) and tasks such as understanding customer and business needs, basic goal setting, planning processes and the use of results and customer satisfaction data for improvement
- Problem Solving - Understand quality management philosophies (e.g. Deming) and tasks such as understanding customer and business needs, basic goal setting, planning processes and the use of results and customer satisfaction data for improvement. Able to demonstrate use of these approaches. CQE (Certified Quality Engineer), or with 2 years’ experience in this area
- Five Core Tools: Advanced Product Quality Planning (APQP), Production Part Approval Process (PPAP), Failure Mode Effect Analysis (FMEA), Measurement System Analysis (MSA) and Statistical Process Control (SPC) - Understand quality management philosophies (e.g. Deming) and tasks such as understanding customer and business needs, basic goal setting, planning processes and the use of results and customer satisfaction data for improvement. Able to demonstrate use of these approaches. CQE (Certified Quality Engineer), or with 2 years’ experience in this area
- Six Sigma - Understand quality management philosophies (e.g. Deming) and tasks such as understanding customer and business needs, basic goal setting, planning processes and the use of results and customer satisfaction data for improvement. Able to demonstrate use of these approaches. CQE (Certified Quality Engineer), or with 2 years’ experience in this area
- Project management - Understand quality management philosophies (e.g. Deming) and tasks such as understanding customer and business needs, basic goal setting, planning processes and the use of results and customer satisfaction data for improvement. Able to demonstrate use of these approaches. CQE (Certified Quality Engineer), or with 2 years’ experience in this area
- Basic computer skills including MS Office, Notes, QSI and CQMS - Understand quality management philosophies (e.g. Deming) and tasks such as understanding customer and business needs, basic goal setting, planning processes and the use of results and customer satisfaction data for improvement. Able to demonstrate use of these approaches. CQE (Certified Quality Engineer), or with 2 years’ experience in this area
- Knowledge of the applicable standards for the organization (i.e., ISO/TS, etc.) -Understand quality management philosophies (e.g. Deming) and tasks such as understanding customer and business needs, basic goal setting, planning processes and the use of results and customer satisfaction data for improvement. Able to demonstrate use of these approaches. CQE (Certified Quality Engineer), or with 2 years’ experience in this area
- Internal Auditing - Communicate quality management philosophies (e.g. Deming) and lead tasks such as understanding customer and business needs, basic goal setting, planning processes and the use of results and customer satisfaction data for improvement. Use of these approaches routinely. Passed ASQ CQM (Certified Quality Manager) exam and/or have 4 years’ experience in this area
- Leadership (Persuade & Influence, Coach & Develop, Championing Change/Creating Global Mindset) -: Understand quality management philosophies (e.g. Deming) and tasks such as understanding customer and business needs, basic goal setting, planning processes and the use of results and customer satisfaction data for improvement. Able to demonstrate use of these approaches. CQE (Certified Quality Engineer), or with 2 years’ experience in this area
- Bachelor of Science (or equivalent degree) in Engineering required and 2 - 5 years’ experience in Quality Engineering
48
Quality Systems Manager Resume Examples & Samples
- Developing a team of quality professionals to support quality systems management objectives and ensure continual quality improvement
- Exemplary oral and written communications skills
- Working knowledge of cGMP’s and regulations
- Proficiency in Microsoft Word, PowerPoint, and Excel. Knowledge of Trackwise, ComplianceWire and Documentum software is required
49
Senior Quality Systems Manager Resume Examples & Samples
- In depth knowledge of applicable Medical Device Regulation including but not limited to: 21 CFR 820, 21 CFR 806, ISO 13485, European Medical Device Directive, Canadian Medical Device Regulation (CMDR), and Japan Pharmaceutical Affairs Law, Agencia Nacional de Vigilancia Sanitaria (ANVISA)
- Knowledge of effective root cause investigation including industry best practice methods, corrective and preventive action planning and execution and verification of effectiveness techniques
- Strong analytical and decision making skills
- Technical expertise facilitating front and back rooms for third party inspections
- Influence management skills; ability to work constructively across all functions/level of the organization as well as external customers and regulators
50
Quality Systems Manager Resume Examples & Samples
- Leads the QA function to ensure quality system development and compliance with FDA's Quality System Regulation, ISO 9001, ISO 13485/8, MDD, CMDR, Japan R-PAL and other quality requirements
- Establishes quality programs and initiatives to ensure products and assemblies are developed and manufactured in accord with applicable requirements
- Leads and/or supports initiatives to ensure effective quality reporting, quality systems and quality improvement efforts and Customer-Focused Quality; supervise the Quality System Policy/Procedures Manual
- Supports and develops systems for the identification, analysis, correction, and prevention of quality issues
- Contributes quality expertise to product development and manufacturing transfers initiatives to ensure effective compliance to the Product Development Protocol and other applicable requirements
- Oversees and lead key quality systems processes to ensure its effectiveness which includes Quality Planning, Document Controls, Training, Audits, Change Controls, Process and Software Validation, Nonconformance CAPA, Manage External Requirement, etc
- Manages, conducts and coordinates external (FDA, TUV, etc.) audits
- Manages the design and manufacturing documentation and traceability systems
- Provides QA support, participate and collaborate in division related projects
- Works with local management team members in developing long and short-term business goals and strategies
- Represents MSO on Global Quality Leaders Council, collaborate with peers across all BUs for global quality initiatives and works closely with peers on similar quality concerns between MDT sites
- Minimum of 6 management expertise in the Pharmaceutical, Medical Devices or any highly regulated manufacturing industry
- Overall operational and financial acumen, Business and Project Management skills and experience a plus
- Familiar with Quality System Regulation, MDD, and knowledge of Quality System Regulations and ISO
- Training in the following will be advantaged
- University or Master Degree in Engineering or Science with relevant experience
51
Quality Systems Manager Resume Examples & Samples
- Coordinate external audit program to ensure continued compliance with Medtronic, FDA’s QSR, ISO 13485, MDD, Guidelines on Medical Devices Vigilance System, CMDCAS, CMDR and other regulatory agency requirements. This includes audit scheduling, preparation, coordinating audits, preparing and distributing reports, follow-up activities for corrective actions and maintenance of external audit files and distribution of status reports to management
- Manages activities of the Quality Systems group with responsibility for results in terms methods and employees. Oversees CAPA, internal audits, quality system procedure changes and management review processes
- Frequent contacts with managers concerning projects, operational decisions and scheduling requirements. Conducts briefings and technical meetings for internal and some external representatives
- Acts as an advisor to staff members to meet schedules or resolve technical or operational problems. Directly participates in establishing and administering many functional projects. Develops and administers schedules and performance standards
- Exerts influence in the development of overall objectives and long-range goals of the quality systems organization
- Ensures applicable standards and regulations pertinent to Medtronic Orange County are effectively implemented and acts as an advisor to all managers
- Providing leadership and support for the development and implementation of internal audit root cause corrective actions
- Contribute quality systems expertise to assist in continuous improvement activities throughout the Heart Valves organization
- Establish and maintain a program for the training of employees on Quality System Regulations, ISO and Medical Device Directive, Corporate, and other regulatory standards
- Lead initiatives to ensure effective quality reporting, quality systems, customer feedback (internal/external/regulators) and quality improvement efforts
- Work with the local management team members in developing long and short-term business goals and strategies
- Coordinate external audits (Corporate, External Regulators, FDA, and Notified Bodies) of the quality systems and other compliance activities. Follow-up on audits to ensure implementation of corrective actions and timely closure
- Maintain facility certifications and establishment registrations to meet all regulatory requirements for the facility
- Develop proficiency in quality system and regulatory requirements
- Ensure effective and robust risk management for products and processes
- Manage the Learning Management System for Medtronic Orange County
- Approve site quality system changes
- 3+ years of progressive leadership experience in a quality functional area
- 5+ years medical device or highly regulated experience with 2+ years quality auditing, CAPA, quality management review and quality training
- 7+ years industry experience with 3 years quality auditing/CAPA/Training
- Regulatory compliance experience with Quality System Regulations
- Effective interpersonal skills
- Solid knowledge of quality systems
- Word processing skills
- Experience in biological field and / or related to tissue valves
- Knowledge in database management applications
- MBA or MS Degree in Engineering, Physical /Biological Sciences
- RAC or CQA Certification
- Knowledge in the application of risk management
52
Senior Quality Systems Manager Resume Examples & Samples
- Develop & maintain the Quality plan and metrics
- Provide oversight and maintain the Quality System
- Participate in the preparation and execution of site and BU management reviews
- Provide leadership for site readiness for FDA or other Notified Body inspections
- Provides leadership for the Configuration Assurance team
- Guide site to increased understanding of 21CFR 820 requirements
- Provide input and lead users in the effective and compliant use of the QMS architecture
- Manages audits for (Regulatory Agencies, Notified Bodies, and Internal Audits)
- Leads strategic Quality System initiatives. Responsible for establishing objectives, timelines and milestones
- Set and manage clear project priorities based on compliance risk assessment and business prioritization
- Drive the effectiveness of the Quality System by working collarboratively with other stakeholders to ensure effective and compliant processes
- Foster a high-performance culture through active leadership and create a strong sense of accountability within the department
- Ensure personal understanding of all quality policy/system items that are applicable
- 3+ years of progressive leadership experience
- Experience with Class III finished medical device manufacturing
- 10+ years’ experience managing the Quality System and departmental activities within medical device or pharmaceutical manufacturing companies
- Strong track record of successfully managing difficult tasks from start to finish. Independently determines and develops approach to solutions
- Successfully manages multiple priorities efficiently and effectively to meet or exceed customer expectations
- Excellent interpersonal skills and ability to influence others
53
Quality Systems Manager Resume Examples & Samples
- Establish and implement a Quality System that complies with domestic and international quality system requirements and guidelines
- Evaluate compliance of raw materials and processed product with specifications and customer requirements
- Develop and implement a continuous improvement program for product quality
- Review and approve process and product changes notices
- Product Release
- Document Control
- Experience in a regulated industry
- Knowledge of medical device regulations, statistical sampling and analysis, CQA/CQE
- Strong oral and written communication, computer (Word, Excel)
- Demonstrated leadership and communication skills
54
Quality Systems Manager Resume Examples & Samples
- Responsible for managing and reporting on the quality systems and tools within NH including: deviation, change control management, CAPA, rsk management, document control and records management systems at NH
- Develop and refine quality processes and NorthStar’s electronic QMS to meet business needs and continuous improvement
- Co ordinate quality metrics and management review meetings. Actively participates in the meetings and follow up on actions
- Responsible for ensuring systems are in place to ensure NH maintain compliance with quality and technical agreements and regulatory expectations
- Manage the system for internal audits of the NorthStar group and ensure timely compliance
- Ensure readiness and manage external audits of the NH quality systems
- Manage a system for training for all NH personnel and the delivery of GMDP training
- Set up and manage mock recalls and assist the Quality Director in the set-up and/or running of recall activities
- Ensure a process is in-place for approval, oversight and management of outsourced services
- Co-ordinate quality change control approvals from contract manufacturers
- Create & maintain a culture of quality & continuous improvement throughout the organisation
- Assist in the preparation of quality and technical meetings and prepare reports and metrics as required by the business
- Oversee and provide direction to the Quality Systems personnel
- Work closely with the management team to support the growth and development of NorthStar
- Proven management experience
- Full understanding and knowledge of cGMP, quality Assurance and regulatory principles in a pharmaceutical manufacturing environment
- Excellent knowledge of US and European regulatory requirements
- Experience in managing Quality Assurance and quality systems in FDA and HPRA based Pharmaceutical manufacturing essential
- Strong knowledge of pharmaceutical manufacturing in at least one dosage form
- Proven auditing skills while not a requirement are an advantage
- Ability to manage and direct the cross-functional quality function team
- Excellent knowledge of quality management systems
- Strong communication skills with ability to communicate at all levels within the Organisation
- Proven analytical skills and problem solving skills
- Technical writing ability and strong presentation skills
- Ability to work effectively with others to accomplish goals
- Understanding of customs and beliefs of other groups or cultures is an advantage
- An understanding of relevant directives, standards, policies and guidelines and the ability to implement appropriately is also required
- Excellent organisational skills and attention to detail
- A self motivated and results orientated individual with the ability to meet deadlines
- Knowledge of computer system validation while not essential is advantageous
55
Senior Quality Systems Manager Resume Examples & Samples
- Process owner for the Internal Audit program and procedures. Working on enhancing the efficiency and effectivity of the Internal Audit program
- Process owner for the CAPA system and the CAPA Board meetings held with MI management
- Leading continuous improvement of Siemens Molecular Imaging Quality Management System through the implementation of robust Internal Audit and CAPA programs
- Scheduling, planning, and conducting of internal audits at Molecular Imaging sites in Illinois and Tennessee
- Communicating audit results through closing meetings, Management Review updates, and audit reports
- Actively managing CAPAs that result from Internal Audits. Providing feedback and guidance to CAPA Owners on corrective and preventive actions
- Tracking implementation of corrective actions and performing effectiveness verification activities related to audit findings
- Supporting external audits including interfacing with regulatory agencies such as FDA, ANVISA, TUV, and BSI
- Staying informed of new and upcoming regulations and industry trends and gathering industry intelligence through reviews of publications, regulatory conferences, and FDA 483s and Warning Letters issued. Properly adjusting the compliance activities at Siemens Molecular Imaging
- Supporting CAPAs related to external audit findings
- Conducting site planning and training in preparation of notified body audits and FDA inspections
- Performing and presenting trending related to the CAPA and internal audit processes
- Must be familiar with all elements of a Quality Management System, in particular the Corrective and Preventive Action sub-systems
- Must be knowledgeable in FDA’s QSRs, ISO requirements, MDD, and CAMDCAS requirements
- Must have experience with CAPAs as an owner and/or approver
- Must be reliable and capable of working with minimal supervision to manage audit planning, execution, and follow-up activities
- Must be able to manage controversial issues that may arise from internal audits through constructive communication with cross-functional teams
- FDA and Notified Body audit exposure is preferred
- Must be highly compliance oriented to firmly adhere to the principles of the regulations and standards
- A Bachelor's Degree in a technical discipline such as Electrical Engineering, Mechanical Engineering, Nuclear Medicine or a clinical discipline
- Medical Devices regulations knowledge and experience required
- Internal Auditor Certification preferred
- Travel Required: About 25%