Manager, Quality Systems Resume Samples
4.7
(112 votes) for
Manager, Quality Systems Resume Samples
The Guide To Resume Tailoring
Guide the recruiter to the conclusion that you are the best candidate for the manager, quality systems job. It’s actually very simple. Tailor your resume by picking relevant responsibilities from the examples below and then add your accomplishments. This way, you can position yourself in the best way to get hired.
Craft your perfect resume by picking job responsibilities written by professional recruiters
Pick from the thousands of curated job responsibilities used by the leading companies
Tailor your resume & cover letter with wording that best fits for each job you apply
Resume Builder
Create a Resume in Minutes with Professional Resume Templates
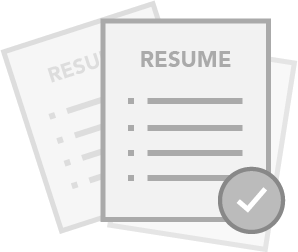
CHOOSE THE BEST TEMPLATE
- Choose from 15 Leading Templates. No need to think about design details.
USE PRE-WRITTEN BULLET POINTS
- Select from thousands of pre-written bullet points.
SAVE YOUR DOCUMENTS IN PDF FILES
- Instantly download in PDF format or share a custom link.
JS
J Stamm
Julius
Stamm
57224 Seth Hill
San Francisco
CA
+1 (555) 810 4802
57224 Seth Hill
San Francisco
CA
Phone
p
+1 (555) 810 4802
Experience
Experience
Philadelphia, PA
Manager Quality Systems
Philadelphia, PA
Rodriguez-Zulauf
Philadelphia, PA
Manager Quality Systems
- Continually develop the WITS quality systems and infrastructure to ensure compliance, effectiveness and continual improvement
- Actively recruit, develop and retain talent within the WITS quality organization
- Establish and drive successful fulfillment of WITS quality system objectives; monitor and report on progress to these objectives
- Ownership of the vendor qualification process, change control system, complaint program, training program, mock recall coordination, as well as SOPs / metrics and coordination of Quality Steering Committee
- Coordinate due diligence of vendors and coordinate on-site audit schedule
- Work with auditors to complete audits / reports in a timely fashion to support development, clinical, and commercial programs
- Ensure proper documentation of audit responses (corrective actions) and audit closure from each supplier
Los Angeles, CA
Manager, Quality Systems
Los Angeles, CA
Klein, Marvin and Conn
Los Angeles, CA
Manager, Quality Systems
- Supporting special projects requiring QA input
- Supporting Quality System Integration and Remediation
- Participate on teams and contribute to process improvement initiatives across the organization
- Other duties as assigned
- Implement and sustain a qualification and validation system
- Develops and maintains Quality Systems for commercial stage pharmaceutical products; ensures proper design controls and documentation are in place
- Develops or revises Quality Systems for research stage pharmaceutical products
present
Houston, TX
Senior Manager, Quality Systems
Houston, TX
Legros, Gleason and Mann
present
Houston, TX
Senior Manager, Quality Systems
present
- Assess product, compliance or operational risks and develop risk management strategies
- Implement improvements to the internal audit program, perform internal audits, and track completion of audit findings
- Provide independent audit support for CMOs, CROs, and critical suppliers to support Supplier Quality Management Program
- Drive continuous improvement efforts of the Intarcia Quality Management System
- Select, develop, and evaluate personnel to ensure the efficient operation of the Quality Systems group. Report to senior management
- Quality systems demonstrated knowledge in areas such as audits, quality risk management, and supplier quality management
- Drive continuous improvement efforts of the Stemcentrx Quality Management System
Education
Education
Bachelor’s Degree in Food Science
Bachelor’s Degree in Food Science
Colorado State University
Bachelor’s Degree in Food Science
Skills
Skills
- As applicable, strong knowledge of Health Canada GMPs
- Strong attention to detail. Ability to drive results
- Maintain programs and processes to ensure high quality products and compliance with current Good Manufacturing Practices
- Excellent verbal and written communication and strong interpersonal skills
- Ability to train technical, professional, and managerial level personnel
- Good interpersonal skills and be able to work effectively and efficiently in a team environment
- Knowledge of domestic and international quality systems and other standards such as FDA QSR, MDD, CMDCAS, JPAL, ISO 13485, ISO 14971, World Health Organization or other applicable standards and regulations
- Knowledge of US cGMP/QSR, ISO 13485, and related Quality standards
- Lead cross-functional activities related to Quality Systems and represent Quality Systems on project teams
- Demonstrates in-depth knowledge of Good Manufacturing Practices (GMPs)
15 Manager, Quality Systems resume templates
Read our complete resume writing guides
1
Senior Manager, Quality Systems Resume Examples & Samples
- Create and operate a new Quality System for novel medical imaging devices to comply with FDA/EU/and other country regulations
- Interface with Consultants, Regulatory agencies, and R&D throughout the development of the new quality system
- Oversee quality system from technology development through clinical trials to meet all regulatory, medical/ health, and legislative standards
- Plan and lead risk management efforts including hazard analysis and FMEA
- Organize quality-related documents required for clinical trials in compliance with all FDA regulations
- Select, develop, and evaluate personnel to ensure the efficient operation of the Quality Systems group. Report to senior management
- Bachelor’s Degree or equivalent experience. Advanced degree in scientific, technology, or legal disciplines preferred
- Experience with Quality Systems in the medical device industry, including proven experience fully bringing a medical device successfully from a concept to a FDA-cleared product
- Experience with managing regulatory affairs are plus
- Ability to work across functions/ cultures/ countries/ sites
- Strong problem solving and negotiation skills with the ability to develop and implement negotiating strategies that demonstrate political awareness
2
Manager, Quality Systems Footwear Resume Examples & Samples
- Supports Senior Manager Quality on all quality related themes in development, commercialization and production
- Guides LO and T1 Management in cost of bad quality reduction efforts
- Establishes and implements in collaboration with LO Senior Management QIP and Quality Assurance (QA) plans in development & commercialization phase
- Supports HQ to establish and implement Quality Assurance for Technology documents (QAT)
- In collaboration with SEA, identifies opportunities to improve Health and Safety of working environment in T1 and T2 chemical facilities and monitors implementation of improvements
- Knowledge of Footwear manufacturing and Quality testing processes and parameters
- Knowledge of laboratory testing procedures
- Understanding of chemical raw materials and bonding processes in footwear manufacturing
- Experience about athletic footwear
- Ability to work independently or with limited guidance
- Advanced MS office skills
- Ability to travel by aircraft/train/car, domestic and international
- Four-year college or university degree with focus on Footwear and/or Material Science and/or Polymer Science or equivalent combination of education and experience
- Minimum of 3 years of progressive work experience in the Footwear industry preferable in a technical department of a shoe factory or Footwear Brand
3
Manager, Quality Systems Resume Examples & Samples
- A minimum of a Bachelor’s Degree or equivalent degree is required
- A minimum of 8 years of experience in a highly regulated industry is required
- Working knowledge and a thorough understanding of Code of Federal Regulations on GMPs is required
- Prior experience working with controlled substances and interacting with the DEA is preferred
- Knowledge and experience in statistical analysis and reporting is preferred
- Specific knowledge of field action management is preferred
- This position will be located in Fort Washington, PA and may require up to 10% travelQuality Systems
4
Manager, Quality Systems Resume Examples & Samples
- A minimum of a Bachelor Degree is required preferably in Engineering, Quality or a related technology field
- A minimum of 8 years Quality experience in a GMP and/or ISO regulated environment is required
- Experience in the Medical Device and/or Pharmaceutical industries is preferred
- Experience with Management Review, Complaints, Non-Conforming Materials, and Document Controls sections of Quality Systems Regulation is preferred
- Direct interaction experience with the US FDA during investigations is preferred
- Data analysis and experience with basic statistical tools are required.Quality Systems
5
Manager, Quality Systems Resume Examples & Samples
- Supporting special projects requiring QA input
- Supporting Quality System Integration and Remediation
- Participate on teams and contribute to process improvement initiatives across the organization
- Ability to identify non conformances as it pertains to CAPA’s and provides guidance to resolve
- Detail oriented and capable of multi-tasking
- Ability to perform investigations and determine root cause
- Able to make judgment calls using combination of knowledge of regulations, knowledge of technology, critical thinking, and interpretation of intent of the regulations
- Ability to work in a matrixed environment
- Ability to change the thinking of or gain acceptance of others in sensitive situations
- Proven ability to drive results, work cross-functionally in a team based environment and foster teamwork
- Must possess recent experience in Quality Assurance, including working in a FDA regulated environment for medical devices/IVD
- Demonstrated experience supervising staff in a regulated environment
- Experience in ERP Systems
- Ability to represent the Company in the CAPA process in FDA inspections
- Experience with managing change within a Quality environment
- Experience with Master Controls
- Proficient in Microsoft Office, Word, Excel, PowerPoint
- Knowledge of domestic and international quality systems and other standards such as FDA QSR, MDD, CMDCAS, JPAL, ISO 13485, ISO 14971, World Health Organization or other applicable standards and regulations
6
Manager Quality Systems Resume Examples & Samples
- Continually develop the WITS quality systems and infrastructure to ensure compliance, effectiveness and continual improvement
- Maintain and continually improve the quality processes needed to ensure compliance, effectiveness, and continual improvement
- Establish and drive successful fulfillment of WITS quality system objectives; monitor and report on progress to these objectives
- Fluent in English – written and verbal
- Experience of working within a global, multi-cultural, matrix organization
- Experience of working in MedTech with solid understanding of the associated regulations
- Solid working knowledge of Lean Six Sigma principles
- Deep and current knowledge of Quality Management principles
- Proven success of building and leading a team and developing talent
7
Manager, Quality Systems Resume Examples & Samples
- Develops and maintains Quality Systems for commercial stage pharmaceutical products; ensures proper design controls and documentation are in place
- Develops or revises Quality Systems for research stage pharmaceutical products
- Implements and maintains Quality Assurance and Quality Control SOPs to assure compliance to regulatory requirements in Commercial and Research & Development operations
- Manages electronic Quality Systems to assure proper use, timely activity execution and control/robustness monitoring, including Document Control System
- Assures proper maintenance of Quality Records
- Coordinates CAPA, Deviations and audit findings activities
- Supports product complaints, withdrawals or recalls, as needed
- Reports to the commercial team and Quality management on outstanding Quality Systems concerns
- Attends and represents Quality at company Quality programs or training
- Assists in developing the Quality Manual for OPKO Renal Division
- Facilitates rapid issue escalation and resolution with appropriate risk management to ensure project continuity and compliance are maintained
- Proactively promotes cross-disciplinary and functional teamwork and quality culture throughout company
- Assists in internal and external GXP and vendor audits, as needed
- Conducts and coordinates GXP or Electronic Systems training as needed
- Monitors the regulatory environment for changing Quality policies, processes and procedures
- Provides Quality Assurance expertise to company personnel and senior management/executives, as needed
- Support Regulatory Submissions, as needed
- Performs other duties as assigned by the Director, Quality Assurance
- Minimum of a Bachelor’s Degree in a scientific discipline
- Minimum 5 years in a management position with commercial stage pharmaceuticals. Development stage experience a plus
- Strong electronic validation experience
- Excellent management, strategic thinking; risk-assessment, decision-making and interpersonal skills
- Strong quality, validation, analytical and production background
- Ability to generate new ideas, processes and strategies to improve Quality systems
- Proven track record of implementing validated/controlled electronic Quality systems
- Proven track record of building effective internal and external relationships
- Ability to work effectively with cross-disciplinary teams and with vendors
- Extensive knowledge of quality and CMC requirements regarding the development, production, testing, release, and distribution of marketed drug products in the US, Canada and EU
8
Manager, Quality Systems Resume Examples & Samples
- Minimum BA/BS with 10+ years or Master’s Degree in any Life Sciences discipline with 7+ years relevant experience
- Proven management experience with multiple reports is required
- Excellent organizational, presentation development and delivery skills
- Must have direct experience with Quality Systems within the Life Science industry
- Must be experienced in Microsoft Office applications, especially Word, Excel and PowerPoint
9
Senior Manager, Quality Systems Resume Examples & Samples
- Manage Deviations, CAPAs, Complaints, and Change Controls per the Intarcia Quality Management Systems to comply with applicable company, US and worldwide regulatory requirements
- Partner with the functional areas of Manufacturing, Facilities, QC, and Engineering to drive closure of Deviations, Periodic reviews, CAPAs, Complaints, and Change Controls
- Ensure that all required aspects of the Intarcia Quality Management System are trended on a routine basis and presented to senior management for review
- Drive continuous improvement efforts of the Intarcia Quality Management System
- Write and revise Quality Management Systems procedures and policies
- Author Product Quality Review (annual) and other Quality KPI summary and trend reports on a periodic basis
- Coordinate and lead Material Review Board meetings
- Provide review and approval of compliance documentation for utilities, facilities and equipment necessary for production
- Implement, and maintain systems, programs and processes to ensure compliance with GxP Quality functions through all phases of clinical and commercial manufacture
- Compile, track quality metrics for critical quality attributes and report to management on a quarterly basis (i.e., Periodic Reviews, Product Complaints, Change Control, OOS, Deviations, CAPA and audits)
- Organize and conduct training events related to Intarcia quality procedures, cGMP regulations and guidelines
- Provide support for all regulatory inspections and audits i.e., US FDA, EU, Notified Body for CE Mark, State Food and Drug, and partner audits
- Other QA duties as assigned by the manager
- A minimum of 10 years in the drug/device pharmaceutical industry and 5 years in QA managing GxP functions preferably for combination aseptic products involving all phases of clinical (Phase I to III) and commercial
- Proven track record of quality systems management with a strong knowledge of root cause analysis techniques
- Strong working knowledge of cGMP regulations (for e.g., 21CFR210, 211, Part 4, 21CFR820 and ISO13485), and ICH guidance’s
- Ability to work independently on QA projects and initiatives with minimum supervision
- Ability to work "hands on" in an entrepreneurial, fast paced environment
- Strong verbal, written communication skills and computer skills are required. Must be goal-oriented, quality-conscientious, and customer-focused
10
Manager, Quality Systems Resume Examples & Samples
- A minimum of a Bachelor’s degree (or equivalent degree) in Chemistry, Engineering, Life Sciences, Pharmacy or similar discipline is required
- Master’s or advanced degree is preferred
- A minimum of 8 years of experience working in a regulated industry is required
- Strong understanding of cGMP standards related to pharmaceutical, medical device and/or consumer/OTC products is required
- Previous experience with Change Control, Investigation / CAPA and Quality Agreements is required
- Previous experience managing a professional staff is preferred
- Fluent knowledge and ability to interpret the US and/or International cGMP’s and regulatory requirements for pharmaceutical, medical device and/or consumer/OTC is required
- Demonstrated skills navigating within a matrix environment, managing complexity, collaborating across boundaries and influencing with and without line authority is required
- Previous inspectional interaction with Regulatory Agencies (e.g., FDA, MHRA, etc.) is preferred
- Knowledge of production and pharmaceutical/OTC manufacturing operations is preferred
- Experience in the development and implementation of quality systems and continuous improvement is highly preferred
- Experience with Process Excellence/Six Sigma tools, training and/ or certification with experience in developing/monitoring performance metrics is preferred
- This position will be located in Fort Washington, PA and may require between 10-15% travel (primarily to Skillman, NJ) depending on business needs.Quality Systems
11
Manager Quality Systems & Compliance Resume Examples & Samples
- Lead and conduct audits; Issue audit reports and perform follow-up actions
- Review / audit compliance documents, SOPs, and protocols as assigned; report findings to management as necessary
- As required, participate in inspections and audits by regulatory agencies; investigate and resolve observations noted during audits / inspections; participate in inspection readiness activities
- Maintain a current GLP training program to ensure that personnel are appropriately trained to carry out assigned responsibilities
- Conduct audits to monitor the state of compliance of service providers
- Interact with and influence colleagues in Research division and Research Quality in order to strategically align and facilitate harmonization of quality systems, procedures, and processes where necessary
- Reading, interpreting and applying various regulations and guidance documents. Assessing compliance with said documents
- Minimum 5 years of experience in Quality Assurance; Pharmaceutical industry experience preferred
- Minimum 3 years GLP QA experience
- Good knowledge of international regulatory requirements and industry guidelines for global GLP
- Accreditations or certifications preferred (e.g. RQAP-GLP)
- Ability to read, interpret and apply references
- Ability to identify issues and offer solutions in a pragmatic way
- Demonstrated ability and willingness to learn new knowledge and skills
- General knowledge of drug development process
- Excellent business skills such as critical thinking, strategic planning, and self-management
- Must be able to handle multiple demands calmly and with patience
- Confidence to work alone or in a team
- Good attention to detail, with the ability to see the ‘big picture’
12
Senior Manager, Quality Systems Resume Examples & Samples
- Evaluates impact of CMC changes to product with complex supply chains for global products
- Manages interactions between CMC change activities and tracking requirements for regulatory filings to ensure compliance of product releases
- Manages tasks and deliverables from Quality Systems, with a focus on existing CMC changes needed by QPs for compliant release of products undergoing changes or launching in EU/ROW markets
- Manages the development, revision, and review of controlled Current Good Manufacturing Practice (CGMP) documents including standard operating procedures (SOPs), Work Practices, risk assessments, and reports, from both internal and external sources
- Manages interaction of data from Regulatory CMC systems with CMC Change Control data from multiple systems and evaluates compliance with change control principles, global standards and regulatory expectations
- Provides guidance and diection into configuration decisions for workflows and workflow automation in quality system tools related to areas of responsibility
- Provides training on department-specific procedures and systems
- Manages, analyzes, and reviews metrics concerning the product change control process and resulting records
- Interprets and executes operating policies, procedures and directives for the department
- Acts as a quality systems consultant, advising Oncology & Biology Quality project teams in planning and executing commercial product changes and product launch projects
- Conducts Supplier Quality audits as requested by Global Auditing
- Provides guidance and advice to management, peers, subordinates, and external stakeholders to assess and improve the adequacy of the quality management system processes and procedures
- Expert in current and emerging global regulatory requirements
- Applies knowledge of CGMPs and data integrity on a daily basis
- Presents viable alternatives within problem resolution and assists to ensure risk mitigation
- Routinely partners with senior management on critical issues impacting product compliance through control of changes
- Minimum BA/BS with 10+ years or Master’s Degree in any Life Sciences discipline with 8+ years relevant experience. Master’s Degree with 10+ years experience preferred
- Previous industry experience in a regulated environment
- Must demonstrate independent decision-making ability and sound judgment
- Ability to develop and deliver training on processes, procedures and systems
- Must be able to communicate effectively with employees, peers and management
- Excellent interpersonal skills and must be able to work effectively and efficiently in a team environment
- Ability to influence the functional strategy by defining, building, and communicating processes, relationships, and efficiencies in areas of accountability
13
Manager, Quality Systems Resume Examples & Samples
- Ability to understand and apply quality system standards
- Should possess knowledge and experience in a GxP regulated industry in multiple geographies
- Should have experience with implementing and validating computerized systems
- 3+ years of experience in pharmaceutical quality
- BA/BS, preferably in science
- Strong computer skills (e.g. Microsoft applications such as Word, Excel, PowerPoint, etc.)
- Self-motivated and good interpersonal skills with proven ability to communicate, both verbally and in writing, to all levels of the organization
- Ability to deal with ambiguity and a high rate of change
- Ability to work cross functionally as part of a global team
- Must be capable of handling multiple tasks and prioritizing work in a fast paced dynamic work environment
14
Manager, Quality Systems Resume Examples & Samples
- Lead continuous improvement of Quality Systems, such as (CAPA, Deviation Management, and Change Management), and direct the efforts to develop, implement and maintain compliant and effective Quality Systems
- Identify compliance gaps and lead focused teams to resolve compliance issues
- Lead department projects of varying complexity
- Assign, manage and review progress and accuracy of work for an individual, or a group of employees
- Lead by example to foster a commitment to quality in personnel, and a culture of quality within the organization
- Interact and influence peers to ensure successful project completion
- Maintain current knowledge of Compliance program and of applicable company standard operating procedures for areas of responsibility
- Provide guidance on interpretation and application of specified QA compliance regulations
- Represent Quality Operations on cross functional teams to promote and realize continuous process improvement
- Reviews manufacturing, environmental monitoring and quality control data for in-process and finished products
- Responsible for final release of manufactured products
15
Manager, Quality Systems Resume Examples & Samples
- Supports the design of the PDM Quality Management System to ensure that it meets regulatory and industry standards and expectations
- Lead cross-functional activities related to Quality Systems and represent Quality Systems on project teams
- Author and revise Policies, Standards and SOPs in alignment with regulatory, industry standards, and expectations
- Deliver training on new Policies, Standards, Standard Operating Procedures, and cGMP topics
- Maintain programs and processes to ensure high quality products and compliance with current Good Manufacturing Practices
- Provides expert guidance on regulatory and industry standards and expectations
- Serve as an subject matter expert on phase appropriate change management
- Facilitates meetings to notify Management of critical issues
- Evaluate the state of the Quality Management System
16
Senior Manager, Quality Systems Resume Examples & Samples
- Inspection Management including logistics, inspection preparation, maintenance of the regulatory inspection program, associated SOPs, and management of the backroom
- Provide technical response and expertise (written and verbal) during audits, inspections and due diligence on Kite Pharma quality related topics and systems
- Provide leadership and guidance during FDA or other board of health inspections
- Assist in the preparation of dossiers and data packages for interactions between Kite and Regulatory agencies. Interact with agents from Regulatory agencies and participate in Pre-Approval/License Inspections
- Monitor the GMP systems currently in place to ensure compliance with documented policies and regulatory guidance documents
- Review proposed changes to systems, procedures, methods, and submissions to regulatory agencies, as appropriate
- Implement improvements to the internal audit program, perform internal audits, and track completion of audit findings
- Identify compliance issues that require follow up or investigation; conduct or direct the internal investigation of compliance issues
- Assess product, compliance or operational risks and develop risk management strategies
- Develop and report on KPI for Internal Audit Program and Regulatory Audit results
- Provide independent audit support for CMOs, CROs, and critical suppliers to support Supplier Quality Management Program
- Gather and analyze information and regulatory changes to determine impact and recommend action based on regulatory intelligence
17
Senior Manager, Quality Systems Resume Examples & Samples
- Ensure that all required aspects of the Stemcentrx Quality Management System are trended on a routine basis and presented to senior management for review
- Maintain the GXP Training Program and provide training related to Stemcentrx quality procedures, US and EU cGMP regulations and guidelines
- Manage the internal and external audit programs. Collaborate with colleagues at AbbVie R&D QA on supplier qualification
18
Manager, Quality Systems Operations Resume Examples & Samples
- Complaints
- A Bachelor’s Degree in Engineering or related technical field is preferred
- A minimum of 8-10 years’ experience in a GMP and/or ISO regulated industry is preferred
- A minimum of 4 years’ experience with direct people management is required
- Experience working in both an FDA and European regulatory environment is required. Experience managing CAPA process is required
- Experience working in manufacturing/operations is preferred
- Product/process Risk Management experience is required. Advanced Technical Training and experience using Statistics, Lean and Six Sigma Methodologies is preferred, including Measurement System Analysis, SPC, DOEs, Reliability, etc
- Knowledge of statistical software packages is preferred, with the ability to preview, graph and analyze data and be able to present data that facilitates/drives decision making
- Technical understanding of manufacturing equipment and processes is preferred
- This position is located in Monument, Colorado and requires up to 25% travel.Quality Control
19
Manager, Quality Systems Resume Examples & Samples
- Manage staff supporting Document Control, Training, Supplier Quality, EQMS administrative support and Validation review
- Lead or participate in supplier audits
- Initiate, monitor and complete change controls related to Quality topics
- Review and approve supplier documents requiring Quality approval
- Initiate, revise, and review controlled cGMP documents including SOPs, specifications and reports
- Provide training on department specific procedures and systems
- Collect data, calculate, and report on departmental performance metrics
- Review and approve process, assay, and other validation protocols and reports as applicable
- Interpret and execute operating policies, procedures and directives for the department
- Identify and plan projects/studies/reviews/investigations to address a specific issue. Act as an advisor to specialists executing projects
- Assure quality and compliance of department work product
- Maintains knowledge of current applicable regulatory requirements, including FDA/EU/ICH and other global regulations
- Apply knowledge of cGMPs on a daily basis
- Manage day-to-day operations independently
- Delegate responsibility and projects to Quality Specialists based on their level of judgment and experience
- Meet with individual employees on a regular basis to discuss, prioritize, and assign work and projects
- Meet with functional group on a regular basis to discuss routine laboratory functions, individual projects and departmental goals
- Proactively looks for ways to challenge specialists and create career opportunities to enhance job satisfaction and improve the department as a whole
- Develop and maintain strong internal relationships both within the Quality organization and cross-functionally
20
Manager, Quality Systems Resume Examples & Samples
- Manages the tactical execution of short- and long-term quality systems objectives through the coordination of activities with a direct responsibility for results, including costs, methods, and staffing
- Provides leadership, coaching, and development plans for all direct reports to maintain an engaged and productive workforce; partnering with Human Resources on employee matters. Provides technical guidance
- Technically proficient in the specific quality systems department and knowledgeable of industry practice and business principles. Works on issues of diverse scope where analysis of situation or data requires evaluation of a variety of factors, including an understanding of current business trends
- Oversees development and implementation of standards, methods, and procedures for inspecting, testing, and evaluating the precision, accuracy, and reliability of company products
- Makes recommendations for corrective action necessary to ensure conformity with quality specifications. Ensures finished products conform to government and company standards and satisfy good manufacturing practices regulations. Selects, develops and evaluates personnel to ensure the efficient operation of the function
- Collaborates with internal and/or external resources to resolve problems of medium to high complexity in Quality issues
- May report quality metrics to senior/executive management, as needed
- In some locations/sites, may have the authority to issue a STOP NOTICE to immediately stop production when a concern regarding possible productions, stocking, or shipping of discrepant assemblies or product arises
- Represents functional expertise at relevant department and site meetings, as needed
- Follows processes and operational policies in selecting methods and techniques for obtaining solutions. Interprets and recommends change to policies and establishes procedures that effect immediate organization(s)
- Makes recommendations for process improvements and participates in planning and implementing changes
- Frequently interacts with subordinate supervisors, customers, and/or functional peer group managers, normally involving matters between functional areas, other company divisions or units, or customers
- Interacts with internal departments and external customers; particularly in problem resolution. Acts as an advisor to subordinate(s) to meet schedules and/or resolve technical problems. Responsible for hiring, coaching and counseling employees, including performance reviews, disciplinary action and terminations
- Assists with various projects as assigned
- Minimum 6 – 8 years of related quality systems experience in a medical device/pharmaceutical environment
- 3+ years of supervisory experience preferred
- Must be proficient with personal computer; strong skills with Microsoft Office software
- Knowledge in relevant federal regulatory requirements
- Strong attention to detail. Ability to drive results
- Ability to train technical, professional, and managerial level personnel
- Excellent verbal and written communication and strong interpersonal skills
- Requires ability to function effectively in multiple team settings as well as independently and to manage multiple priorities
- Knowledge of US cGMP/QSR, ISO 13485, and related Quality standards
- Strong knowledge of FDA regulatory requirements and of standard quality assurance practices for manufacturing operations
- As applicable, strong knowledge of Health Canada GMPs
- Remains current with industry standards and best practices
21
Manager Quality Systems Resume Examples & Samples
- Incumbent will work with a cross functional team located in the Bridgewater, NJ area to lead and continuously improve GLP, GCP and GMP compliance of internal systems and global contractors / suppliers
- To ensure appropriate and well maintained systems are in place to support the team with development, manufacturing, clinical trials, regulatory filings and commercial launch of sterile drug products
- Ownership of the vendor qualification process, change control system, complaint program, training program, mock recall coordination, as well as SOPs / metrics and coordination of Quality Steering Committee
- Coordinate due diligence of vendors and coordinate on-site audit schedule
- Work with auditors to complete audits / reports in a timely fashion to support development, clinical, and commercial programs
- Ensure proper documentation of audit responses (corrective actions) and audit closure from each supplier
- Upload Supplier Audit files from audit teams to Electronic tracking data base
- Ensure all original audit documents are properly stored and retrievable
22
Manager Quality Systems Resume Examples & Samples
- Provide technical expertise and leadership in food safety, quality, plant services, and risk assessment programs/policies/events
- Communicate technical information, opportunities and potential risks in business environment to facilitate effective decision making
- Manage internal audit/inspection and corrective/preventive action programs
- Support food safety continuous improvement efforts (complaint reduction, program reassessments, data collection system, training)
- Provide leadership and expertise to Product development/technology/business development, quality and plant services employees
- Develop and provide coaching, training and troubleshooting for Plant personnel
- Experience in the food industry plant environment with a solid understanding of manufacturing processes. Strong hands-on Quality Systems and field skills, with ability to act as a technical resource for operations, procurement, R&D and QA
- Expert abilities and decision quality in Food Safety, Regulatory, Process Improvement, Sanitation, Quality Systems and their application within food processing
- Expertise regarding Pepperidge Farm Quality Standards, and Quality Policies, with skills and ability to execute against requirements
- Knowledge and general business acumen to support and influence RD, Supply Chain, Procurement, and Category Management processes including supplier partnerships that leverage best practices and technologies
- Able to partner with supply chain to effectively manage Supply Base to Expectations and Requirements Manual, Specifications, Non-Conformance resolution, Sanitation, improvement in KPI's, NFPA-SAFE audit targets and resolution of audit action plans
- Practical knowledge and application of food safety principles (ex. Regulatory, HACCP, SQF, GMPs, AIB, food microbiology etc.)
- Strong interpersonal skills and leadership abilities
- Computer skills including proficiency with Microsoft Office software, able to master other software
- Promotes engagement & diversity
23
Manager, Quality Systems Resume Examples & Samples
- Develop and execute programs to improve quality system compliance and efficiency
- Focus on development of best practice policy and standard operating procedures
- Work with Senior Director Global Quality Excellence to support oversight QA/RA 20/20 Program and coordinate project management activities within the function
- Identify upcoming Standards changes and understand work needed to be done to ready the organization
- Drive Quality KPIs and Management reporting
- Support Quality IT function to ensure compliance needs are addressed, Quality team is appropriately represented and IT platforms are designed with quality in mind. Ensure QMS policies/procedures appropriately aligned
- Work with Senior Leadership Regulatory Compliance to identify upcoming/changing regulations and understand work needed to be done to ready the organization
- Develop and manage appropriate Quality training programs
- Perform as a Role Model Leader, acting in compliance with the Thermo Fisher Code of Ethics Administer the Division’s overall Quality System, management of the Company’s Quality Assurance and Quality Control departments, assuring that all Company policies and practices meet or exceed all regulatory requirements
- Demonstrated experience in Quality environment
- Ability to work in a matrix environment, utilizing influence
- Excellent verbal and written communication skills, comfortable in an executive environment
- Ability to handle conflict with confidence and integrity
- Sound organizational skills and a keen ability to multi-task in a detailed environment
- Extensive knowledge in Quality Systems and associated Regulatory knowledge in a Medical Device environment
- Experience with Computer Systems associated with Quality Processes
- Ability to travel approximately 20% of the time
24
Senior Manager, Quality Systems Resume Examples & Samples
- Evaluate personnel requirements of the quality assurance, as it relates specifically to investigations/CAPAs, complaints, training and data integrity functions
- Oversee site training
- Support, as necessary, product release and cross-train with other quality assurance counterpart
- Chair weekly CAPA/investigation meeting to assure timely closure
- Administer the site quality systems program as delegated by the Executive Director - Site Quality
- Chair monthly meetings of the Technical Review Board
- Administer and support program for annual product reviews for all commercial products
- Act as a delegate/assigned designee to perform functions on behalf of the Executive Director, Quality
- Host customer audits and provide responses to audit deficiencies and observations
25
Manager Quality Systems / Audits Resume Examples & Samples
- Plan, schedule, lead and document Quality Systems audits to assure compliance to DMFI QS, BRC and regulatory requirements
- In conjunction with other lead auditor, audit internal Del Monte facilities. Audit co-packers, vendors (domestic and international) and distribution centers as necessary
- Work with other department management, identify areas of improvement and evaluate quality programs to ensure production of products, services and processes are consistent with established standards
- Through analysis of audit results and working with Operations and Technical Services, close all gaps in audits by identifying and recommending best practice approaches to problem solving. Communicate findings to DMFI facilities to assist with adoption of best practices
- Administer Internal Quality Systems Audits (IQSA) and trainings completed by DMFI facilities
- Help Manager in maintaining, developing and implementing existing and new Corporate Quality Policies, Procedures and Programs necessary to meet DMFI QS standards, BRC and Regulatory requirements
- Act as a PDM administrator from Quality Systems point of view
- As SAP Super User, Quality Lead and Administrator, support QA organization and facility QA with Quality related SAP implementation and problem resolution activities; train end users
- Work as an administrator of Quality module in SAP; maintain up to date Quality related data in SAP and assign required parameters as demanded by new product, product changes and location assignments
- Work as a QA representative in fulfilling MMC form requirements within SAP by working with Item Master team
- Work in partnership with R&D and QA in writing and reviewing technical specifications and ensure consistency and accuracy. Identify omissions or discrepancies and resolve issues prior to issuance of specifications
- Collaborate with R&D, vendors and procurement to obtain necessary technical information in order to reach consensus on ingredient specifications
- Manage all the workflows to fulfill Controlled Process Change documentation is in place as per the standards
- Ensure communication and delivery of formulas and specifications to production facilities happen in timely manner prior to packing season
- Deliver, maintain and control issuance and maintenance of QA policies, procedures, formulas and specifications on QA team site. Manage archived documents
- Provide assistance to QA organization and DMFI facility personnel in navigating QA team site. Control site security/access
- Manage Master Variety Code List and be responsible for generating new variety codes for new products and product changes
- Manage various Master Lists including but not limited to Document Master List, Records Master List, DMFI and Co-Packer Facility Details List, Crisis Contact List
- Manage the Quality Records repository on RQS and Box including BRC certificates and Reports, QS Audit Reports, Gluten Free Assessments, Reports of Official Business
- Responsible for assuring customer documentation requirements are completed and requests are analyzed, gaps are identified and addressed in a timely manner. Develop and maintain most up to date information/documents on customer websites and databases as deemed necessary
- Assist in development of new systems or testing methodologies as required by Corporate QA
- Support Consumer Affairs requests for information or forward to appropriate area of expertise for timely response
- Collaborate with sales team in obtaining and delivering required product information
- BS in Food Science or related field. Advanced degree(s) highly preferred
- With BS, minimum 5-6 years with responsibilities in Quality & Food Safety and/or regulatory areas. With advanced degree, minimum 4 years with Q&FS and/or regulatory area
- Professional auditing experience of International Organization for Standardization (ISO) Standards and Global Food Safety Initiative (GFSI) Standards applying to food manufacturing facilities
- Knowledge of FDA FSMA laws and regulations
- Ability to deftly use Del Monte Technical, ERP, and routing systems. Knowledge and experience of working with ERP systems such as SAP is highly preferred
- Detailed and process oriented with strong problem resolution abilities
- Self-starter; take charge, positive and proactive attitude
- Good computer aptitude. Experience with MS Word, Excel, PowerPoint and Access desirable. Working knowledge with external databases, SharePoint sites
- 30-40 % travel required (depending on location), domestic and international, for audits at the production facilities, co-packers and vendors
26
Project Manager Quality Systems & Compliance Resume Examples & Samples
- Identify projects based on needs expressed by Quality and Regulatory leadership team
- Consults with management and develops project proposals to determine goals, time frame, funding requirements, and allotment of resources
- Formulates and defines scope and objectives of project
- Develops project plans specifying goals, strategy, staffing, scheduling, identification of risks, contingency plans, and allocation of available resources
- Identifies and schedules project deliverables, milestones, and required tasks
- Coordinates recruitment or assignment of project personnel including assignment of duties, responsibilities, and scope of authority
- Respond rapidly and flexibly to emerging issues or interruptions in production, quality, engineering, logistical operations and or supply chain
- Directs and coordinates activities of project personnel to ensure project progresses on schedule and within budget
- Establishes standards and procedures for project reporting and documentation
- Reviews status reports prepared by project personnel and modifies schedules and plans as required
- Prepares project status reports and keeps management, clients, and others informed of project status and related issues
- Coordinates and responds to requests for changes from original specifications
- Develops and maintains project documentation
- Coordinates project activities with Cross Functional Teams to ensure goals and requirements are met
- Reduce project delays by anticipating and resolving roadblocks
- May travel to manufacturing sites and vendor facilities as projects require
- 10+ years of experience in Quality Assurance and/or Systems roles in a medical device/diagnostics/biopharm environment
- Experience working cross-functionally and leading teams to accomplish goals
- Proven experience with Quality Management Systems, eQMS, Design Controls, Risk Management, and Post-Market Surveillance processes. Subject matter expertise preferred
- Exceptional troubleshooting and analytical skills
- Positive Attitude and good communication skills across all levels of the organization, customer oriented
- Ability to manage complexity in a fast-paced environment
- Experience with defined process improvement techniques beneficial
27
Manager, Quality Systems EXT MFG Resume Examples & Samples
- Responsible for ensuring standard systems and processes are in place to support the Americas External Manufacturing organization. These include but not limited to systems for audits, change control, investigations, metrics, complaints, SOPs and GMP training
- Performs site verification of SOPs and practices versus HQ policies, directives and regulatory agency observations. Manages department SOPs, including periodic review schedule
- Manages product quality complaint process and ensures timely closure of complaint investigations
- Acts as change control gatekeeper when needed
- Develops training curriculums for department and assists with training new employees
- Manages Annual Product Quality Reviews schedule
- Leads coordination and delivery of monthly Quality Council within ExM Americas
- Tracks and reports Quality metrics on monthly basis
- Leads coordination and execution of internal self-inspection audit program. Acts as lead auditor when assigned. Identifies and trains others to be auditors
- Represent Bristol-Myers Squibb during FDA/other regulatory inspections and corporate GMP compliance audits
- Leads back room during audits of ExM Americas
- Assist with preparation of audit responses
- Selects and retains staff. Accountable for allocating resources such that the right person is doing the right work at the right time. Develops and mentors staff. Provides feedback on performance against predefined objectives
- B.S. in Natural Sciences, Chemistry, Microbiology, Biology, or Pharmacy
- A minimum of 7 years’ experience in pharmaceutical, biologics, biotech or related industry with relevant experience
- Experience in a Quality Assurance or Quality Control function is required
- Experience in the manufacture of drug substance and/or drug product or quality control laboratories is desired
- Knowledge in solid dosage forms, parenteral technology, biologics, or combination products
- Knowledge of compendial and cGMP requirements, FDA regulations and the ability to interpret and apply them
- Trained in auditing techniques and skills such as observation, questioning, and assessment of complex problems
- Proficiency with the use of global systems (e.g., TrackWise, SAP)
- Good verbal and written communication skills essential
- Capable to manage multiple priorities
- Able to rapidly adapt to changing environment and circumstances requiring flexibility, tolerance and great sense of urgency while ensuring that all cGMP and Regulatory requirement are met
- Exhibits BMS BioPharma behaviors
28
Manager, Quality Systems Resume Examples & Samples
- Responsible for the implementation and maintenance of the Quality Documentation System
- Responsible for the implementation and maintenance of the Training System
- Responsible for the implementation and maintenance of Change Control, CAPAs, deviations, investigations and nonconformances System
- System administrator for EDMS/EQMS systems
- Write, review and approve documents (SOPs, protocols, technical reports, specifications, etc.)
- Review and approve batch records, associated testing records, and other documentation on a as needed basis
- Minimum education required: BS in a scientific discipline
- Experience in administration of an EDMS/EQMS system is a must
- Knowledge of quality concepts of the manufacturing and testing of pharmaceutical/biotech
29
Senior Manager, Quality Systems Resume Examples & Samples
- Develop, maintain and monitor Quality Systems to ensure they are compliant to cGMP
- Support GMP activities performed in the facilities in order to ensure their compliance to the highest level of regulatory requirements
- Ensure that the site is compliant to an “in-use” state of the process and system associated to SOP and Documentation control
- Ensure that the site is compliant to an “in-use” state of the process and system associated to training requirements, Annual Product Review, Change Control, CAPA Management, Stability Programs
- Develop SOPs as required
- Complete all GMP Documentation correctly and in a timely manner
- Initiate, and follow through with actions required to close Change Controls
- Ability to follow moving priorities
30
Manager, Quality Systems Document Control Resume Examples & Samples
- Establish and maintain a document management system compliant with regulatory, quality, and Kite requirements
- Responsible for the creation and management of all documentation and records issuance and archival processes to support clinical and commercial manufacturing
- Provides guidance and advice on methods, procedures, standardization and requirements associated with the document management system
- Responsible for maintaining the document change control system
- Manages the document change process so that only approved and validated changes are incorporated into effective product and process documentation
- Ensures accuracy by reviewing documents for completeness, proper authorization and impact to other quality systems
- Collaborates with cross-functional departments to ensure timely implementation of document change requests
- Provide work direction and guidance to staff to assure completion of assigned tasks and other duties
- Responsible for procedure reviews and facilitating procedure updates with process/system owners
- Assure that personnel are adequately trained in the principals, policies, and procedures of the document management system
31
Manager Quality Systems Resume Examples & Samples
- Provides Leadership to Quality Systems staff. Responsible for training, development, motivating and coaching of Quality Systems staff, assigning work, meeting completion dates, interpreting and ensuring consistent application of organizational policies
- Establishes and maintains comprehensive site quality management systems that are efficient, effective and compliant to applicable cGMP, regulatory requirements and expectations, and the Company’s Quality System policies and procedures. Work seamlessly with functional business groups to drive continuous improvement in system integration, interfaces with business processes, and efficiencies to ensure effectiveness quality system is maintained
- Responsible for incorporating best practices into the quality management system while maintaining alignment to Company Objectives. Leads and drives the effort of defining the standard work for consistent and reliable quality system execution and, provides direction for process improvement tools for Quality Systems
- Executes the initiatives for Quality Systems Excellence Programs & Deployment Management. Partners with Corporate Quality and other B. Braun sites on quality objectives related to quality systems and processes. Serves as the site Quality project leader and centralized team member for these initiatives. Ensures that user requirements are properly defined and documented, systems are structured to meet established requirements, and training is effectively executed to all affected personnel prior to implementation
- As part of Quality Systems accountability, manages the CAPA and Change Control programs to ensure quality records are thorough, comprehensive, well documented and accurate. Assures root cause investigations and risk assessments are appropriately conducted. Works with the organization to drive timely completion of changes and corrective and preventive actions in support of the manufacture of the highest quality products and business objects
- Creates standard informatics methods for introducing, updating, tracking and trending Quality Systems Metric. Oversees timely and accurate metric trending and analysis to assure the effectiveness of the Quality Management System. Compiles data and prepares presentations for site and executive management Quality System Management Review process
- Participates in regulatory inspections and customer audits; manages the support team during inspections and audits to ensure that appropriate documents and information are provided to auditors in a timely manner
- Keeps informed of all existing and new regulatory requirements, assures site Quality System continues to comply with changes in regulatory requirements and expectations, and works with other functions to ensure full compliance
- Maintains a high degree of personal professional development through a combination internal and external training and participation in professional associations as appropriate
- Selects, trains, motivates and develops staff with experience in defining and documenting a comprehensive quality management system that supports the scope of work conducted within the site
- Build and foster strong relationships and partnerships with stakeholders and support groups to meet the demands of a changing business culture and environment
- Serves as a key quality systems subject matter expert to the organization. Participate in organizational training to drive organizational competency in quality system requirements
- Experience in data analysis, trending and responding to adverse trends in quality system indicators
- Experience in performing internal audits and/or supplier audits
- Solid understanding of the efficiencies and criticalities of all of the quality systems elements
- Ability to use sound scientific judgment and risk management for the facility to prevent regulatory action
- B.S. in a Scientific discipline
- 8+ years of developing Quality Systems infrastructure or centralized processes experience in the medical device / pharmaceutical industry
- Experience in supporting FDA inspections as quality system subject matter expert and an ability to interpret regulatory requirements
- Travel to any B. Braun facility, domestic and internationally, when necessary
- To keep abreast of changes in the regulations, interpretation of the regulations and revising internal practices and written procedures to comply with the regulatory requirements
32
Manager Quality Systems Resume Examples & Samples
- Manage Quality System Development, Including HACCP and FSMA compliance, Maintenance and Continuous Improvement using the SQF model
- Manage document control activities, management review meetings, Corrective and Preventive action, external certification audits and internal system audits. Manage Formula and Procedures program employees using Optiva, RMS, Label control systems and plant floor automation
- Work closely with the Manager Laboratories on product start ups, testing and specifications reviews
- Key contact with the Logistics organization on coordinating new/reformulated product starts, daily releases and management of withheld product inventories Key contact with World Headquarters process safety and provides oversight for process Irregularity program insuring that accurate and timely reports are issued and dispositions received and properly handled
- Maintains the Process Review Program, provides training on the program
- Working with Thermal Process Safety, coordinate sterilizer testing and certification. One of the key contacts with regulatory agencies on Thermal Processing Controls and regulations
- Coordinates maintenance of all compliance records in this area,
- This position will be required to evaluate current formula and procedure management programs and procedures, verifying both accuracy and efficacy of the programs and procedures while recommending improvements or corrections for optimizing Campbell’s conformance to specifications to standards for products
- This position will be required to work cross-functionally with WHQ, Engineering and R/D to assist with food formulation/specifications issue resolution by coordinating the efforts of all responsible parties for the timely addressing of the problem
- This position will be required to keep abreast of new technologies and practices formula management and thermal processing technology by benchmarking with other network operations, suppliers, regulatory contacts, technical publications and reports. Any potential opportunities identified must be clearly communicated to the appropriate teams. This position will also be responsible for any trials or evaluations that would be necessary to identify cost and operational benefits associated with the new technology or practice
- Develop and maintain a working knowledge of regulatory requirements related to food safety/thermal processing, label compliance and formulation controls
- This position coordinates all QA related Logistic issues related to SAP controls, WMS and effectively management withheld product and assure accurate and timely dispatch of disposition’s
- Proven strengths and in-depth knowledge of computer based formulation controls, thermal process food safety and inventory management and dispatch. Strong food safety, microbiology and food science background is needed
- Ability to evaluate sanitation, formulation and food safety programs under for effectiveness, accuracy and adequacy
- Ability to partner with many diverse groups including Plant Operations, Supply Chain, Engineering, Quality Control, Purchasing, third-party auditors and other technical organizations/associations to effectively manage issues and operational savings opportunities within the quality system programs
- Strong written and verbal communication skills with experience in auditing and training a diverse work group
33
Senior Manager Quality Systems Resume Examples & Samples
- The Sr. Manager Quality Systems is the key liaison between Vogue, Consumer and Enterprise and accountable for communicating and where appropriate leading new initiatives from Quality Systems and the Enterprise. They are accountable for partnering with Business Quality to ensure all Enterprise policies, standards and procedures are effectively communicated and deployed into relevant standards and procedures for Vogue globally
- As a primary responsibility, drives all aspects of the quality systems including validation, nonconformance, complaint handling, CAPA, QRB, risk management, and change control, ensuring that all products manufactured under the manufacturing network worldwide meet the product requirements. In addition, this person will lead/facilitate the Vogue Franchise Management Review process. They will participate in developing and presenting departmental materials for Management Review
- The Sr. Manager Quality Systems has responsibility for working with EM, IM and key stakeholder functions for the following quality systems processes: Change Control, Document Control, Training, and Quality Review Board management
- They will also be responsible for ensuring harmonization activities for the QMS with Consumer and deployment of quality systems based initiatives
- Provide detailed or summary communication to QA and cross-functional management on status of key initiatives and issues
- Conduct, execute, and document thorough investigations and CAPAs for high-risk/high-complexity issues. Ensure timeliness of deliverables through independent, proactive intervention. May act as a CAPA owner or be assigned as a QA lead resource for a CAPA or investigation
- Troubleshoot high-risk/high-complexity quality/compliance issues, using experience, ingenuity, and creativity to provide solutions to a wide range of root causes
- Design and implement quality and compliance improvement programs and initiatives. Innovate solutions to significant quality system gaps and lead continuous improvement projects
- Subject Matter Expert (SME) for quality assurance processes, procedures, audits (internal and external), and activities. Develop and deliver training on QA-related topics. Remain current on assigned quality system training and seek out training and knowledge in adjacent areas. A mentor to junior staff
- Provides project leadership or participates as a team member on major initiatives that have high impact to the business
- A minimum of a Bachelor’s Degree is required. A degree in a science discipline is preferred. An advanced degree is preferred
- ASQ Certification(s): CQE, CRE, CQA preferred
- A minimum of 8 years of professional experience in a regulated industry is required. Experience in quality assurance and/or compliance is a plus
- People management experience is required
- Experience in Quality Systems, Product Safety, Enterprise systems rollout, or experience with complaint vigilance and/or complaint reporting is preferred
- Detailed working knowledge of cGMP requirements and current FDA enforcement issues preferred
- Demonstrated ability to lead cross-functional teams and collaborate with internal/external partners to enhance relationships and interactions, including interfacing with management to inform, drive change, and provide direct feedback is required
- Demonstrated ability to work on complex or ambiguous issues autonomously, with little/no daily direction is required
- Up to 25% domestic/international travel may be required
- This position will be based at a J&J facility in North America (US, Puerto Rico, Canada)