Director, Quality Systems Resume Samples
4.5
(114 votes) for
Director, Quality Systems Resume Samples
The Guide To Resume Tailoring
Guide the recruiter to the conclusion that you are the best candidate for the director, quality systems job. It’s actually very simple. Tailor your resume by picking relevant responsibilities from the examples below and then add your accomplishments. This way, you can position yourself in the best way to get hired.
Craft your perfect resume by picking job responsibilities written by professional recruiters
Pick from the thousands of curated job responsibilities used by the leading companies
Tailor your resume & cover letter with wording that best fits for each job you apply
Resume Builder
Create a Resume in Minutes with Professional Resume Templates
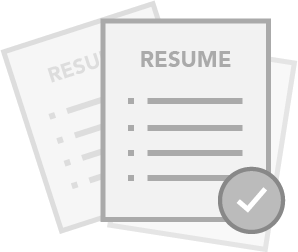
CHOOSE THE BEST TEMPLATE
- Choose from 15 Leading Templates. No need to think about design details.
USE PRE-WRITTEN BULLET POINTS
- Select from thousands of pre-written bullet points.
SAVE YOUR DOCUMENTS IN PDF FILES
- Instantly download in PDF format or share a custom link.
PB
P Boyle
Paul
Boyle
93272 Huels Plaza
Phoenix
AZ
+1 (555) 472 4843
93272 Huels Plaza
Phoenix
AZ
Phone
p
+1 (555) 472 4843
Experience
Experience
Dallas, TX
Director, Quality Systems
Dallas, TX
Crist Inc
Dallas, TX
Director, Quality Systems
- Proven track record in people management (developing, coaching, mentoring, directing) and budget management
- Represent company in interactions with customer meetings, sales support requests and trade associations, such as Independent Marketing Alliance (IMA), Markon Produce, National Restaurant Association (NRA), International Food Distributor Association (IFDA), etc
- Builds strategic partnerships to further Quality organizational objectives and collaborates with all levels in developing strategic direction for short and long term business planning
- Partners with management in the development and introduction of new products and processes into manufacturing through quality planning including verification and validation
- Participates in 2nd party agreements (e.g. contract mfg, distribution, acquisitions etc.) through due diligence activities of quality system assessment, contractual agreement, and quality system integration
- Coordinate quality and food safety expectations, compliance activities and quality improvement initiatives with partner groups such as Independent Marketing Alliance (IMA) and Markon Produce
- Instill robust corrective action tracking and proactively identify gaps in quality system to minimize food safety and customer quality concerns. Participate in cross functional Supplier and Co-pack selection, approvals and compliance
San Francisco, CA
Associate Director, Quality Systems
San Francisco, CA
Stracke-Hackett
San Francisco, CA
Associate Director, Quality Systems
- Proactively identify, develop and implement areas for work process improvement and efficiency
- Enhance and develop quality risk management tools and methodologies and apply to the commercial quality system
- Collaborate with IT in identifying and developing continuous improvement opportunities in Ironwoods validation programs, policies and procedures
- Drive continuous improvement efforts of the Stemcentrx Quality Management System
- Compile data, analyze data, draw data driven conclusions and develop risk based action plans through the CAPA system for management review outputs and annual product quality reviews
- Author quality system trend reports and develop metric control plans for management review reporting
- Partner with the functional areas of Manufacturing, Facilities, QC, and Engineering to drive closure of Deviations, CAPAs, Investigations, Complaints, and Change Controls
present
Detroit, MI
Senior Director Quality Systems
Detroit, MI
Simonis, Barrows and Gerhold
present
Detroit, MI
Senior Director Quality Systems
present
- Establishing, implementing, and maintaining a comprehensive and risk based Validation program with comprehensive and completed lists of validated equipment, utilities, processes, methods, and computerized systems for the site
- Ensuring equipment, utilities, processes, methods, and computerized systems for the site are validated to current standards and are maintained in a validated state
- Ensuring changes to equipment, utilities, processes, methods, and computerized systems for the site are documented, assessed, tracked and approved in a compliant Change Control system
- Implementing the Company Quality Management System and leads the Quality Management Review process
- Replacing, updating, and enhancing Quality Related IT systems and databases (e.g. Change Control, Discrepancy/CAPA, Batch Record issuance and tracking)
- Establishing and maintaining a compliant and efficient document management process and system
- Ensuring the timely creation and approval of an Annual Product Review for each product produced at the site
Education
Education
Bachelor’s Degree in Engineering
Bachelor’s Degree in Engineering
San Diego State University
Bachelor’s Degree in Engineering
Skills
Skills
- Proven leader with excellent collaboration and teamwork skills, including the ability to nurture a strong food safety culture
- Strong overall business acumen and ability to implement corporate and divisional strategy
- Knowledge of FDA, ISO, GMP/QSR and other Quality system recognized standards
- Ability to work with outside suppliers, medical and technical professionals
- Strong relationship skills to achieve sustainable partnerships and collaboration internally and externally
- Strong interpersonal, verbal and written (including email) communication skills with professional demeanor
- Good management and strong communication skills
- Proven leadership skills related to quality assurance and food safety in a manufacturing environment
- Demonstrated ability to successfully direct multiple functions in establishing and delivering consistent results. Timeline and performance driven
- Ability to handle a variety of projects and coordinate the efforts of direct reports at the same time
15 Director, Quality Systems resume templates
Read our complete resume writing guides
1
Director, Quality Systems Resume Examples & Samples
- BS degree -required in chemistry, microbiology or chemical engineering; Advanced degree is preferred
- ISO Certified Auditor and or Black Belt/Green Belt preferred
- Requires a minimum of 10 years of experience in pharmaceuticals or cosmetics including holding recent management or executive level positions
- The incumbent must be sufficiently knowledgeable to direct staff in product or process problem solving
- Must possess in-depth knowledge of current regulations, guidances and regulatory agency This would include in-depth knowledge of recall regulations
- A strong understanding of inspection techniques, including quality engineering principles and statistical methodology is
- Strong software system skills are required
- The incumbent must possess good interpersonal abilities to work with general managers, commercial and operations leaders across the respective business units
- Incumbent needs to possess excellent people skills to influence, motivate, teach and encourage direct staff as well as peers to understand and accept his/her
2
Director, Quality Systems & Compliance Resume Examples & Samples
- Performs all responsibilities in accordance with company policies, procedures, federal regulations and safety requirements
- Implements site programs and quality systems to improve knowledge and understanding of compliance requirements at all Alexion and contractor sites. Identifies compliance gaps and develops and implements plans to resolve issues and mitigate compliance risks
- Provides strategic direction to area personnel responsible for the quality management systems
- Leads and manages inspection readiness programs of all Alexion facilities including hosting consultant visits, preparation activities and managing project plans. Develops and maintains GMP Compliance Training Programs (procedures, records) to support inspection readiness at all sites
- Plans and manages strategy for all Alexion US regulatory inspections, including inspection process, regulatory interactions, providing strategic direction to staff to defend practices, approval of inspection responses and tracking corrective actions to closure. Ensures that post inspectional commitments are tracked and completed on time
- Provides guidance to all Alexion US facilities on interpretation of international regulations and provides regular updates on industry trends and their application to Alexion sites. Implements corrective actions as required
- Responsible for reporting requirements to regulatory agencies and leads implementation of corrective actions and quality system improvements
- Develops and implements a risk-based audit programs that meet regulatory requirements. Ensures adherence to a pre-approved audit schedule and ensures auditor qualifications allow accurate assessments of site compliance and risks
- Drives the development and continuous improvement of compliance initiatives. Manages development and maintenance of systems for tracking and trending pertinent compliance data for quality system performance and/or improvements. Provides recommendations to Senior Management
- Establishes realistic goals and objectives. Plans and directs work activities, and continuously monitors progress such that responsibilities goals and objectives are accomplished efficiently, completely and within established timeframes. Assures that work is performed in compliance with department SOPs and cGMPs
- Interacts effectively with site and company management and internal departments to ensure compliance requirements are understood and adhered to
- 10+ years leadership experience in a QA/Compliance role
- Thorough knowledge of international regulatory requirements for biotech products and extensive experience in interactions with regulatory agencies
3
Director Quality Systems Resume Examples & Samples
- Leads and ensures compliance with cGMP’s, DEA and OSHA regulations on the production shifts
- Partners with manufacturing in ensuring cGMP compliance, as well as delivery of quality products, including improvement efforts in quality production
- Oversees and manages the CAPA (corrective action, preventive action) system. Ensures actions and follow up are executed in a timely manner
- Manages and develops new functionality as the system owner for the Document Management software system
- Leads and manages the batch packaging Deviation program
- Leads the Quality Systems team through direct management of the Sr. Quality Systems Managers who oversees the shift Quality Managers in production
- Serves as lead regulatory escort, performs escort duties with contract packaging customers and FDA during audits
- Leads and manages the supplier audit/certification program
- Responsible for leading the efforts and compliance with Lean Six Sigma practices for the department. Provides support to continuous improvement activities as needed
- Functions as back up to departmental Sr. Director of Regulatory Affairs or Vice President of Regulatory Affairs and Quality Systems when needed
- BS in a scientific discipline preferred; minimum of five (5) years in a cGMP facility in a Quality Assurance/Quality Control role
- Certified LSS Black belt
- Excellent oral and written communication skills. Ability to interact and communicate with staff at all levels
- Ability to effectively lead, manage and participate in cross-functional problem solving teams; advanced collaboration skills
- Advanced computer skills required
- Ability to read and understand the English language for the purpose of following instructions
- Ability to work independently, as well as within groups
4
WW Director, Quality Systems Resume Examples & Samples
- Provide program leadership and direction to assure optimal execution of related programs and assure the QMS goals are achieved at all levels – DePuy Synthes segment, operating company and site - and they are aligned with those of the J&J Enterprise
- Develop and Execute the Quality Management Systems strategy and standards for DePuy Synthes related but not limited to Quality Manual, QSMR, CAPA, and all other elements of the quality systems regulations globally as applicable
- Oversight and management of all Information Technology (IT) solutions supporting the Quality Management System
- Establish and maintain the QMS and related IT strategy roadmaps to drive growth and value for DePuy Synthes in all aspects of the business impacted by the quality system
- Liaise with IT and IT Services departments to ensure adequate support is provided for existing technologies
- Create the business cases and value propositions for programs and manage capitol appropriation requests and project budgets
- Provide quality system subject matter expertise to the business and to the execution of related initiatives and external regulatory audit support
- Collaborate with technology vendors to develop future capabilities in support of the segments long-term strategy
- Champions the creation and maintenance of Credo based environment in his area of responsibility, living Credo values, building trust and caring for people
- Develop and executes plans for talent attraction, development and retention to enhance the talent pipeline
- Establish and maintain QS procedures and controls to ensure that the quality and performance of the product conforms to specified company standards and comply with the recognized Regulatory Standards for all markets in which our products are sold
- Support DePuy Synthes objectives while adhering to the values of the Johnson & Johnson Credo and local safety and environmental policy and procedure
- A minimum of a Bachelor's degree is required, preferably in an Engineering, Life Science, or related discipline. A Master’s degree would be an advantage
- A minimum of 10 years of quality and/or manufacturing experience in medical device field is required. A minimum of 3 years of people management experience is required
- Experience in Project Management, preferably related to Information Technologies/Data Management systems is highly preferred
- Working knowledge of Quality System processes required by 21 CFR Part 820, ISO 13485:2003 & CFR Part 11 regulation is required
- Strong communication, influencing and leadership skills. Ability to communicate at all levels of the organization is required. This candidate must be able to communicate effectively at all levels within Quality as well as cross functionally with departments such as Operations, Regulatory, Research and Development and Procurement
- This candidate should have a proven track record implementing Quality System improvements to meet compliance and overall business goal is required
- Demonstrated expertise in interpretation and pragmatic application of QA standards is preferred. Initiative in innovative approaches to QA solutions and applications in a fast paced changing global business environment are preferred
- The ability to continuously assess the effectiveness of functional processes and lead progressive improvement initiatives is required
- The ability to influence at senior levels and across functions building strong networks internally and externally is required. Experience delivering results through influence in a highly matrix environment are also required. Strong experience and proven record motivating leading and developing staff, in a highly changing environment is required. Must be a proven change agent
- This position can be located in Raynham- MA, West Chester- OH, Warsaw- IN, Leeds- England, or Cork- Ireland and will require up to 40% domestic and international travel depending on the location of the role
5
Associate Director Quality Systems Resume Examples & Samples
- Thorough understanding of regulatory requirements for drugs, devices, biologics, including risk management
- 5-10 years of manufacturing and/or quality operation management experience (or equivalent) within an FDA and/or EU pharmaceutical, device and biologics environment
- Ability to accurately interpret and apply regulatory expectations to the QMS in a drug, device and biologics manufacturing environment
- Must have strong project management and communication skills
- Model behaviors consistent with Merck’s Leadership behaviors, values and culture
6
Senior Director Quality Systems Resume Examples & Samples
- Establishing, implementing, and maintaining a comprehensive and risk based Validation program with comprehensive and completed lists of validated equipment, utilities, processes, methods, and computerized systems for the site
- Ensuring equipment, utilities, processes, methods, and computerized systems for the site are validated to current standards and are maintained in a validated state
- Ensuring changes to equipment, utilities, processes, methods, and computerized systems for the site are documented, assessed, tracked and approved in a compliant Change Control system
- Implementing the Company Quality Management System and leads the Quality Management Review process
- Replacing, updating, and enhancing Quality Related IT systems and databases (e.g. Change Control, Discrepancy/CAPA, Batch Record issuance and tracking)
- Establishing and maintaining a compliant and efficient document management process and system
- Ensuring the timely creation and approval of an Annual Product Review for each product produced at the site
- Assisting with the remediation of Quality Systems in association with the consent decree work plan
- Focusing internally and externally; interacts internally with subordinates, peers, and senior management and interacts externally with regulators, customers, and contract manufacturers
- Maintaining an external network of expertise and represents the division and company in professional organizations
- Providing effective leadership including: developing and implementing objectives and business strategies; selecting key personnel and motivating members of the functional area; challenging employees to develop as leaders while serving as a role model and mentor; assisting with performance calibration/talent pool management/succession planning; individual goal setting/performance reviews; training and development; supporting workforce diversity, quality and safety and supporting supervisors/managers in the management of their employees/department which support achievement of individual/department/business objectives
- Establishing departmental and individual goals and objectives in alignment with site goals and priorities. Identifying performance improvement targets and metrics. Ensuring capabilities and capacity in place to effectively deliver on all departmental commitments and performance targets
- Strengthening overall leadership and organizational capabilities in area of responsibility. Building and sustaining high performance management team and ensuring strong alignment and coordination with other functional groups at the site
- Ensuring effective utilization of resources by ensuring robust employee development, performance management, succession planning, and rewards and recognitions practices in area of responsibility
- Managing headcount and expenses in area of responsibility to meet approved spending plan while achieving all departmental commitments and project objectives
- Motivating, retaining and developing key employees. Building and sustaining employee engagement by creating an environment within which individuals and teams can excel
- Interacting closely with BU, relevant sites and functions to define production plans, yearly goals and budgets for reporting functions/operations as well as long range plans (LRP and LRCP)
- Bachelor's Degree in a science or technical field and12 years of experience in pharmaceuticals or a related industry with 10 years in management position
- Knowledgeable of biotechnology processing and testing
- Validation expertise with equipment, utilities, processes and computerized system
- Expertise in document management systems
- Thorough knowledge of GMPs
- Expertise and knowledge in GMP engineering facilities and equipment design concepts in order to review engineering projects for compliaace impact
- Knowledgeable of requirements for post approval changes and of information typically found in the CMC sections of regulatory submissions
- Knowledgeable and experienced with discrepancy investigation and lot disposition
- Skilled in achieving results and managing others to achieve corporate, site, and departmental objectives. Excellent collaborator
- Excellent communication skills, good presentation and influencing skills and the ability to interact and gain the support of senior management
- Driven with a strong focus on goals
7
Associate Director, Quality Systems Resume Examples & Samples
- Implement and maintain systems, programs and processes to ensure compliance with GMP Quality functions through Phase 1/2 clinical manufacture at Stemcentrx’ internal manufacturing plant
- Write and revise compliant Quality SOPs
- Manage deviations, CAPAs, complaints, change controls, and document management per the Stemcentrx Quality Management System to comply with applicable company, US and EU regulatory requirements
- Partner with the functional areas of Manufacturing, Facilities, QC, and Engineering to drive closure of Deviations, CAPAs, Investigations, Complaints, and Change Controls
- Drive continuous improvement efforts of the Stemcentrx Quality Management System
- Partner with IT to manage the implementation, validation and oversight of an Electronic Quality Management System (EQMS)
8
Director, Quality Systems Resume Examples & Samples
- Responsible for implementing and maintaining the effectiveness of the quality system including the resources to establish and support it
- Ensures the systems necessary to support effective application and monitoring of the quality system are implemented
- Provide leadership and technical direction to quality systems department staff in achieving department strategic, tactical, and quality goals and objectives
- Partner with outside suppliers and contract manufacturers; oversee and communicate the progress of production and quality projects to senior management
- Oversee and review non-conformances, deviations, and investigations to ensure corrective actions are implemented and process improvements are realized
- Establish and implement an internal and supplier quality audit program to ensure product specifications are met
- Ensure all quality system records, policies and operating procedures are appropriately maintained and archived
- Establish methods to monitor and communicate quality performance results
- Define and closely monitor short and long term quality objectives and increase quality awareness
- Assist with new product development and identify and justify enhancements for improved throughput, cost, and/or quality
9
Associate Director, Quality Systems Resume Examples & Samples
- Review and approve critical Quality complaints and Investigation extensions
- Support stock recovery activities
- Minimum 12 years experience in Pharmaceutical or related industry
- Strong leadership skills for the ability to lead teams of a cross-functional and multi-level nature, including senior management representatives
- Previous GMP Quality role (quality Systems, validation, compliance, audit, assurance)
10
Director, Quality Systems Resume Examples & Samples
- Identify and develop Policies and Procedures that include the Food Safety, regulatory and quality requirements needed for all manufacturing sites
- Maintain a process for approving, issuing and annually reviewing all Food Safety/Quality Policies and Procedures
- Manage the process for approval for all documents; reviewing procedures with affected departments for input or when differences of opinion arise
- Develop and maintain a SharePoint site, policy/procedure quality index and manual for Corporate Policies and Procedures and one for each manufacturing site
- Provide Policy/Procedure education and training for manufacturing sites
- Provide leadership in Special Situations/Escalated Events, i.e. data gathering, RFR development and submission, interfacing with FDA and State agencies
- Manage Crisis Commander for Special Situations – meeting notifications, contact lists, meeting notes, data upload
- Maintain SQF/BRC Audit schedule for manufacturing sites
- Maintain QI metrics and issue monthly reports
- Proven leadership skills related to quality assurance and food safety in a manufacturing environment
- Management of multiple and conflicting priorities
- Proven track record in people management (developing, coaching, mentoring, directing) and budget management
- Strong relationship skills to achieve sustainable partnerships and collaboration internally and externally
- Excellent negotiating skills when working through conflict resolution
- Demonstrated ability to successfully direct multiple functions in establishing and delivering consistent results. Timeline and performance driven
- Proficient in Microsoft Office products
11
Director, Quality Systems Resume Examples & Samples
- Develop and implement Quality System policies, procedures and processes that meet all applicable regulations and standards for product safety and effectiveness
- Advise BAS management board in compliance decisions and actions regarding product remedial actions, including recalls and/or regulatory citations
- Execute Field Actions and Recalls based on completed Remedial Action Plans
- Engage and support investigations of product quality issues
- Provide mentoring and leadership to the Quality Managers in Quality Assurance and/or Compliance areas
- Provides timely information to department and divisional management on issues which will affect the division's Quality Systems performance
- Coordinates resource allocation to insure appropriate quality support for new product development teams and BAS operations
- Develop and monitor departmental budgets
- Responsible for division Quality system and product failure investigations Establishes key performance indicators for the Quality engineering and ensures support of BAS operational objectives
- Provides Quality Assurance support during FDA, corporate and notified body inspections/assessments during Quality Systems reviews
- Develops, maintains, and implements department and division policies and procedures
- Assesses priorities and makes project assignments for employees to assure division and corporate Quality priorities are met
- Performs job reviews, recommends salaries and promotions, hires employees, and initiates disciplinary actions
- Participates in training and provides input to training of other employees on division procedures and policies, technical and managerial skills
- Maintain product risk files and management assessment for all products at BAS. Manage field assurance and document control functions
- Provide risk assessment reports to divisional management and Corporate RSSS to ensure all new products meet compliance to quality systems
- Ensure that employees are trained, motivated, and have work direction, and that divisional and corporate business and quality objectives are met
- Bachelor's Degree with preference in Engineering, Statistics, or one of the Life Sciences
- Eight (8) years progressively more responsible management experience in the medical device industry or equivalency in Quality Engineering/Quality Assurance
- Demonstrated human relations and communication skills
- Experience working in cross-functional team environment and a multi-level corporate environment
- Masters of Science in Engineering or Life Sciences
- Good management and strong communication skills
- Ability to handle a variety of projects and coordinate the efforts of direct reports at the same time
- Ability to work with outside suppliers, medical and technical professionals
- Strong Project management skills
- Strong leadership and decision making skills
- Ability to work with all levels employees
- Ability to analyze and use technical data
- Strong overall business acumen and ability to implement corporate and divisional strategy
- Knowledge of FDA, ISO, GMP/QSR and other Quality system recognized standards
12
Director, Quality Systems Document Control Resume Examples & Samples
- University degree required
- Minimum of 7 years quality assurance experience in the pharmaceutical industry
- Demonstrated leadership skills, including the ability to lead and manage projects and staff in a matrixed and global setting
- Experience in managing a Quality System within a Pharmaceutical environment. Comprehensive knowledge of GxP and other pertinent regulations and understanding of global quality standards relating to product development, submission and/or commercialization
- Demonstrated ability to assess the state of current business and QA operations to identify and recommend future state, improvements, and to implement action plans
- Demonstrated experience facilitating and leading global process improvement and harmonization activities
- Demonstrated competence to resolve complex and diverse problems with decision making responsibility that has a major impact within Quality and/or with functional groups globally
- Effective written and oral communication and interpersonal skills, facilitation and influencing skills with an ability to interface globally across multiple departments and across various levels of management with Astellas and with external stakeholders
- Demonstrated experience leading strategic development and successful execution of plans and initiatives for addressing complex and diverse Quality matters
- In-depth experience with Document Control systems, principles, and regulatory requirements and expectations
- Able to meet the availability requirements of the position and can travel for business needs as required: approximately 20%
- Experience in reviewing validation documents for an electronic document control system
13
Director, Quality Systems Resume Examples & Samples
- Effectively control the deployment of business strategies, the utilization of personnel and the scope and timeliness of responses
- Builds strategic partnerships to further Quality organizational objectives and collaborates with all levels in developing strategic direction for short and long term business planning
- Works to achieve the overall objectives of the company and ensures that quality strategies are aligned throughout the region for the areas of responsibility
- Oversees the quality system compliance through Global KPIs to monitor performance of key elements of the quality system according to internal and external requirements
- Accountable for Global Management Reviews – provides management with objective evaluation of overall Global QARA performance and provides guidance for implementation of improvements, corrective and preventive actions related to processes that affect Haemonetics Quality System
- Working with site and corporate management, ensures the effective implementation and maintenance for Quality System requirements, including but not limited to, MDD 93/42/EEC, ISO13485, CMDR, and 21CFR 820. Ensures organizational compliance with Quality Systems procedures and regulations
- Translates Quality System strategy into tactical plans and ensures implementation
- Partners with management in the development and introduction of new products and processes into manufacturing through quality planning including verification and validation
- Participates in 2nd party agreements (e.g. contract mfg, distribution, acquisitions etc.) through due diligence activities of quality system assessment, contractual agreement, and quality system integration
- Responsible for professional development for the Quality Systems group
14
Associate Director, Quality Systems Resume Examples & Samples
- Quality Assurance, GMPs, Health Authority Regulations and Validation practices/principles
- Strong knowledge of GMP, SOPs and quality systems
- Identifying, writing evaluating and closing CAPAs and experience with internal and external audit principals
- Strong knowledge of aseptic manufacturing processes
- Strong knowledge of change control practices/strategies
- Equipment and utility IQ/OQ/PQ/PV
- Proficient in MS Word, Excel, Power Point and other applications
- Ability to communicate and work independently with scientific/technical personnel
- Required: Minimum of 8 years of Quality Assurance experience in a GMP environment (Drug Substance or Drug Product). Working knowledge of quality systems and regulatory requirements (21 CRF Part 11/210/211, ICH 8, ICH 9, ICH 10)
- Minimum 3-5 years of management experience
- Education: Bachelor’s degree in technical discipline (Chemistry/Microbiology/Engineering or similar)
- Preferred: Experience in the medical and/or pharmaceutical industry. ASQ certifications
15
Director, Quality Systems Compliance Resume Examples & Samples
- Acts as Global Owner of the Janssen Adopting Regulatory Requirements (ARR) process. Leads cross-functional Council meetings and drives process improvements to ensure monitoring, identification, assessment, and implementation of new or revised regulatory requirements and standards impacting Quality Systems. Develops and reports metrics to ensure management awareness of risks and adherence to the process
- Leads implementation initiatives for new or revised external standards and regulations impacting Global Quality Systems. Develops and manages cross-functional matrix teams to ensure gap and impact assessments are executed and remediation plans are in place. Develops and reports metrics to ensure management awareness of status
- Manages the process for deployment of internal J&J Standards into the Pharmaceutical Segment. Identifies Process Owners and Functional Area representatives, trains owners on requirements for Sector-level assessment, and monitors the status of gap assessment and deployment across end-to-end functions of Janssen
- Participates in Enterprise Regulatory Outreach forum as a key link between Pharma, J&J Regulatory Compliance, and other Segments across J&J
- Participates as Pharma representative on Enterprise alignment projects related to external standards monitoring and audit standardization. Works to simplify and standardize processes across Janssen
- Leads integration activities to assure inclusion of new/emerging regulatory requirements (e.g combination products) into applicable Janssen Global Quality Systems and internal audit processes
- Ensures internal audit procedures remain current and up-to-date, and all applicable global and virtual organizations are subject to appropriate audit cadence. In partnership with J&J Regulatory Compliance, ensures audit planning and execution to ensure compliance with J&J policies
- Plans and manages budget
- As needed, provides compliance support in relation to new or emerging regulations (e.g. awareness training, supporting the development of remediation plans, attending and presenting at external conferences to shape external environment, etc.)
- A minimum of a Bachelor’s Degree with at least ten (10) years of related experience in the pharmaceutical or similarly regulated industry is required
- Experience in both medical device and pharmaceutical industries is preferred
- Minimum of five (5) years of experience working with Quality Systems is required (change control, CAPA, audit, etc.)
- Current Auditor Certification (CQA, ISO Lead Auditor, etc.) is strongly preferred
16
Director Quality Systems Resume Examples & Samples
- Develops and implements best-in-class quality management systems policies, processes and procedures in accordance with appropriate standards, requirements and regulations globally
- Leads organization to simplify, consolidate, and harmonize existing Quality Systems within Dental Platform to achieve business objectives
- As an SME, provide quality systems expertise throughout the organization and drive continuous improvement to ensure effectiveness quality system is maintained
- Assists in preparation for and support of external regulatory audits including FDA, notified bodies, etc., as well as internal audits
- Participates in platform RAQA level Policy Deployment, leads implementation of key quality objectives and plans
- This role is based in Orange Ca, and works within a cross-functional, matrixed global organization to drive dynamic performance in all areas
- Proven ability to establish strategy and to translate it into an effective, long-term action plan
- Comprehensive knowledge and experience with global regulatory requirements and product registrations
- Possess strong negotiation skills, the ability to interpret and apply regulations, and working knowledge of product development process
- Demonstrates knowledge of domestic and international quality systems and other standards such as FDA QSR, MDD, CMDCAS, SFDA, JPAL, ISO 13485, ISO 14971 and other applicable standards and regulations
- Possess a broad knowledge of surrounding areas including Quality Assurance, Manufacturing and Development
17
Director, Quality Systems Resume Examples & Samples
- Support Corporate and Supplier quality audit programs. Ensure that the audit programs are maintained as required by internal policies and procedures
- Provide oversight, manage and coordinate the global change control and customer notification process
- Oversee the Supplier Nonconformance process and ensure that supplier provides acceptable response to West’s complaint in a timely manner
- Support the Quality Management System Documentation in general and assure that the procedure requirements are developed and fulfill the policy guidelines of West QMS and Regulatory requirements
- Manage the customer specification review process and provide instructions when discrepancies are identified, so the specification can be mutually agreed to
- Support the Material and Supplier Qualification process. Evaluate the change notification associated with supplier changes and collaborate with other departments to address the changes in a timely manner
- Interface with customers for quality issues, technical information, specification, agreements, etc
- Coordinate with appropriate personnel/areas to identify new/ongoing projects for product and process improvement activities and support the completion of them in a timely manner
- Minimum of 8 years of experience in quality related field
- Demonstrate team building and problem solving skills
- Familiarity with tools, concepts and methodologies of quality systems
- Knowledge of cGMP requirements and ISO standards
18
Associate Director, Quality Systems Resume Examples & Samples
- Provide Quality validation leadership support as the Quality – IT liaison for computer system assessments, validation and change control, and provide effective Quality support for process improvements and compliance governance at all applicable support points of the System Development Lifecycle (SDLC). As required, support other non-GxP Ironwood systems validation and deployment activities to ensure consistency in approach of validation program protocols and execution
- Provide validation support for IT change management documentation review. Ensure Quality & Compliance requirements are considered in any IT change initiative or GxP change request
- Lead and perform Quality risk assessments and vendor audits of electronic system vendors, to ensure quality oversight and routine periodic review of vendor compliance performance
- Provide CSV support during regulatory inspections and be able to articulate Ironwood’s application of Regulatory and Industry standards to its System Development Lifecycle (SDLC)
- Perform timely and effective QA review of validation documentation such as SOPs, Validation Plans and Reports, Traceability Matrices, Testing deliverables, and Data Migration Plans
- Collaborate with IT in identifying and developing continuous improvement opportunities in Ironwoods validation programs, policies and procedures
- Proactively provide suggestions for solutions to process issues, and collaborate with appropriate stakeholders to drive productively towards completion and execution of solutions
- Provide timely updates on projects and deliverables to Quality Management and any other functions that support IT validation project deliverables
- Establish effective cross-functional partnerships with key internal stakeholders including IT, nonclinical research, clinical, pharmaceutical development, regulatory and global manufacturing teams and key external stakeholders including Business Partners, and vendors, as required
- Bachelor’s degree with at least 10-12 years’ experience in the pharmaceutical industry, including proven experience in managing validation programs
- In-depth knowledge of quality systems principles and applications to the pharmaceutical industry
- Direct experience in performing IT vendor audits
- Proven and effective communication, and interpersonal skills to influence, resolve conflict and leverage alignment with key stakeholders at all levels organizationally, internally and externally
- Ability to articulate advanced CSV concepts to all levels of the organization, as well as external stakeholders and educate on those concepts
- Ability to use objective measures to drive decision making and strategy and pragmatically apply appropriate tools to solve critical problems
- Ability to influence IT colleagues, illustrate gaps and provide guidance and path forward for GxP systems at Ironwood
- Ability to recognize opportunities to lead and teach others as well as play a team member role
- Should be active problem solver who has clear understanding of the relationship between individual, functional and corporate goals
- Ability to identify and clarify complex problems and constructively provide potential solutions to team
- Must have demonstrated managerial leadership skills in developing, providing value-added, fit-for-purpose subject matter expertise in validation
- Knowledge of GxPs and ICH Guidance is a must
- Advanced degree in technical field preferred
19
Director, Quality Systems Resume Examples & Samples
- Lead and manage activities which drive improvement and ensures all locations meet or exceed Reinhart quality and food safety standards, are operationally efficient, meet third party and customer requirements, and comply with government regulations
- As a Certified PCQI, oversee and continuously improve QFS programs, SOP’s and training materials to ensure compliance with FSMA, FSVP, HACCP, USDA, Preventive Controls, Food Defense, etc
- Designated interface with regulators regarding recalls, licensing, food safety issues and concerns
- Work with locations to create strategies to mitigate audit deficiencies and risks to prevent recurrence
- Develop, maintain and continuously improve departmental policies, standard operating procedures, work instructions, templates and other required documents
- Establish, conduct and oversee FSQA internal and/or third party GFSI scheme audits of high risk suppliers and co-packers, to ensure FSMA, FDA, and USDA compliance
- Train and develop FSQA team members to audit independently and carry out full internal audits successfully
- Instill robust corrective action tracking and proactively identify gaps in quality system to minimize food safety and customer quality concerns. Participate in cross functional Supplier and Co-pack selection, approvals and compliance
- Support product recalls and withdrawals, including during 24/7 night and weekends
- Analyze governmental, supplier and customer account food safety and security initiatives for incorporation into Reinhart operating procedures
- Coordinate quality and food safety expectations, compliance activities and quality improvement initiatives with partner groups such as Independent Marketing Alliance (IMA) and Markon Produce
- Provide oversight for the successful, aligned implementation of LIMS, and establish a change control process for the future
- Provide FSQ guidance regarding special situations (e.g. floods, fire, hurricane, power outages)
- Represent company in interactions with customer meetings, sales support requests and trade associations, such as Independent Marketing Alliance (IMA), Markon Produce, National Restaurant Association (NRA), International Food Distributor Association (IFDA), etc
- Analyze & negotiate resolution of food safety and quality issues
- Develop, support, coordinate and implement customer and sales oriented training related to quality programs and food safety/security programs
- Conduct routine, random, and competitive product cuttings to ensure products meet expectations
- Oversee clear and concise technical writing of SOP’s, Process Flows, Specifications and Programs
- Support Corporate Standards and Quality Assurance teams in regard to specialized knowledge in relation to allergens, product claims, and product labeling
- Provide Commercialization and Acquisition support within scope of responsibility
- Develop strong talent development plan for the QA function to support growth
- Bachelor’s degree required; Food Science or related with foods experience preferred
- Minimum of 10 years of work experience in food manufacturing and distribution systems
- Certified PCQI with 2+ years of internal auditing experience
- Skilled in risk analysis and mitigation, prioritization, problem solving and corrective action
- Proven program management experience
- Strong interpersonal, verbal and written (including email) communication skills with professional demeanor
- Demonstrated success in training and developing quality and food safety personnel
- Proven leader with excellent collaboration and teamwork skills, including the ability to nurture a strong food safety culture
- This position must pass a post-offer background and drug test
- Lean Quality Training with successful applications a plus
20
Associate Director, Quality Systems Resume Examples & Samples
- Author quality system trend reports and develop metric control plans for management review reporting
- Establish meaningful thresholds for quality system metrics
- Develop or enhance metric control plans for operational review areas including manufacturing supply management, quality system management, and product and process management
- Discuss data trends with functional departments, learn special causes and common causes for variation
- Teach teams how to interpret data trends and appropriate action plans for out of trend results
- Collaborate with cross functional teams to solve problems and analyze data
- Facilitate monthly metric review meetings at the commercial manufacturing site
- Enhance and develop quality risk management tools and methodologies and apply to the commercial quality system
- Facilitate and or lead execution of risk management activities at the commercial site
- Facilitate and lead complex investigations, utilize structured approach to root cause analysis and corrective action plan development
- Led development of the annual product quality review templates, data analysis and report creation
- Compile data, analyze data, draw data driven conclusions and develop risk based action plans through the CAPA system for management review outputs and annual product quality reviews