Manager, Quality Control Resume Samples
4.5
(135 votes) for
Manager, Quality Control Resume Samples
The Guide To Resume Tailoring
Guide the recruiter to the conclusion that you are the best candidate for the manager, quality control job. It’s actually very simple. Tailor your resume by picking relevant responsibilities from the examples below and then add your accomplishments. This way, you can position yourself in the best way to get hired.
Craft your perfect resume by picking job responsibilities written by professional recruiters
Pick from the thousands of curated job responsibilities used by the leading companies
Tailor your resume & cover letter with wording that best fits for each job you apply
Resume Builder
Create a Resume in Minutes with Professional Resume Templates
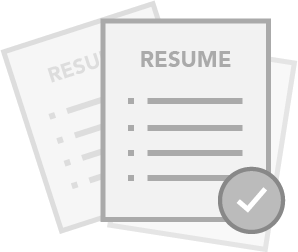
CHOOSE THE BEST TEMPLATE
- Choose from 15 Leading Templates. No need to think about design details.
USE PRE-WRITTEN BULLET POINTS
- Select from thousands of pre-written bullet points.
SAVE YOUR DOCUMENTS IN PDF FILES
- Instantly download in PDF format or share a custom link.
JD
J Dare
Jo
Dare
3034 Botsford Glens
Houston
TX
+1 (555) 835 4994
3034 Botsford Glens
Houston
TX
Phone
p
+1 (555) 835 4994
Experience
Experience
San Francisco, CA
Manager, Quality Control
San Francisco, CA
Walker Inc
San Francisco, CA
Manager, Quality Control
- Establish and maintaining effective working relationships with VP, managers, supervisors, employees, patrons, clients, service providers and corporate sponsors
- Develops and maintains collaborative working relationship with other managers
- Performance Management - Sets clear expectations & direction for staff; achieves team results consistently; coaches staff to improve; is a positive role model
- Support development, implementation, and analysis of quality measurements to improve organization and program performance
- Develop and manage standard operating procedures as they relate to third party vendors, work order completion, safety and inventory control
- Evaluate data for trends indicative of product performance, method performance, or analyst performance
- Applies Lean and Six Sigma tools to analyze and resolves problems, and assists others in solving work problems
Chicago, IL
Senior Manager Quality Control
Chicago, IL
Leffler, Wintheiser and Reynolds
Chicago, IL
Senior Manager Quality Control
- Develops a program evaluation framework to assess the strengths of the program and to identify areas for improvement
- Establishes and maintains professional working relationships with internal departments, engineers, subcontractors and suppliers
- Work with QC project management and other functions to determine sample forecast and priority
- Provide work direction, counseling, and coaching to hourly union staff
- Provides positive and strong leadership, coaching, and mentoring for employees as well as monitor performance and results
- Ensures that all safety procedures are understood and followed by providing up to date safety training to all employees and auditing procedures
- Ensures employees are apprised of program plans and changes in a timely manner through staff meeting and notices, memos, etc
present
New York, NY
Senior Manager, Quality Control
New York, NY
Schamberger Group
present
New York, NY
Senior Manager, Quality Control
present
- Continuously evolves the Quality Control system to take advantage of new and emerging automated inspection methods, manufacturing methods, and industry best practices
- Manages the operation of the Incoming, In-Process, and Finished Goods inspection and acceptance of electronic components, sub-assemblies, and finished products
- Promotes and encourages a work environment that challenges employees to constantly search for ways to perform their activities more efficiently and effectively, especially where automated and semi-automated methods can be employed
- Ensures timely inspection, acceptance, and Material Resource Board (MRB) activities, including prioritization
- Formulates response to internal audit findings and CAPAs
- Direct, plan, delegate and manage department staff including
- Manages the activities of the quality control department to create a culture of quality awareness, teamwork, and cooperation with all departments within the Facility
Education
Education
Bachelor’s Degree in Chemistry
Bachelor’s Degree in Chemistry
University of California, San Diego
Bachelor’s Degree in Chemistry
Skills
Skills
- Ability to focus attention to details and ensure high quality work while maintaining the big picture to lead/drive whole organizational success
- Ability to focus attention to details and ensure high quality work
- Quality & Safety - Adheres to all safety & security policies and regulations; demonstrates quality work that is accurate, thorough & efficient
- Focus on Results - Able to plan and organize work to achieve goals; achieves targeted results with minimal supervision; is accountable for own actions
- Knowledge of basic chemical and biological safety procedures
- Good verbal and written communication skills with the ability to work in a team setting
- Good interpersonal skills and be able to work effectively and efficiently in a team environment
- Knowledge of cGLP/cGMP, FDA, EMA, ICH guidance’s and industry standards for analytical development and characterization of proteins
- Strong interpersonal skills
- Strong verbal and written communication skills
15 Manager, Quality Control resume templates
Read our complete resume writing guides
1
Senior Manager Quality Control Resume Examples & Samples
- Leads the Quality team to produce precise, accurate and timely test and calibration data; act as the technical expert on Quality expectations for the park
- Leads a team that performs audits, tests and inspections
- Leads and manages the Quality team to maintain accurate and functional quality records, instructions and manuals in compliance
- Leads the Engineering Change Notice process
- Works closely with DOSH Inspectors, Rides Maintenance and Facilities Maintenance to ensure compliance, documentation, and training are completed as required. Involved in operations and maintenance management to ensure continual tracking process of training, safety audits, and inspections as it relates to ride and maintenance safety
- Coordinates annual DOSH inspections
- Works with DOSH personnel in determining “major modification” requirements
- Communicates to ensure any “notice to correct” action items are completed as dictated by DOSH to ensure compliance
- Provides technical support to department technicians and management in the use of applicable analytical equipment and methodologies
- Develops and implements new Quality procedures as needed; review, revise and improve existing systems on a periodic basis
- Provides technical support including root cause investigation of product failures and analytical service requests from technicians. Communicate trends and significant findings to management
- In conjunction with site leadership, manages communication to all levels of the organization, including regular reporting requirements
- Leads Quality department in customer, regulatory and certification audits
- Drives continuous improvements. Apply scientific methodology, use of root cause and statistical analysis tools to support recommendations for process improvements
- Analyzes, evaluates and implements recommendations on quality attributes
- Evaluates and introduces new equipment and methodologies to keep park performance up to date
- Evaluates new quality systems to support developing business needs
- Manages department staff as dictated by business need or management
- Directs the development and effective analytical training of park & department employees to comply with Quality programs
- Ensures compliance training requirements and proficiency testing to meet regulatory requirements
- Develops annual budgets and operating plans to support the programs; maintains the financial acumen to manage all the departments’ needs and budget
- Develops a program evaluation framework to assess the strengths of the program and to identify areas for improvement
- Ensures proper documenting of program activities; ensures reporting is completed as required; ensures that program activities operate within the policies and procedures of USH
- Establishes and maintains professional working relationships with internal departments, engineers, subcontractors and suppliers
- Works closely with internal clients to identify and correct operational issues quickly
- Ensures that collective bargaining agreements are upheld by partnering with HR and Labor Relations to maintain positive union relationships
- Assists in the implementation and maintenance of HR policies, procedures and practices of USH
- Recruits, interviews and hires; ensures training and mentoring; manages and maintains team of well qualified technical services personnel
- Provide work direction, counseling, and coaching to hourly union staff
- Ensures employees are apprised of program plans and changes in a timely manner through staff meeting and notices, memos, etc
- Provides positive and strong leadership, coaching, and mentoring for employees as well as monitor performance and results
- Assists HR in establishing and implementing a performance management process for all other management and employees. Carries out annual manager and technician performance evaluations: addressing performance concerns in a timely manner
- Acts as EHS Safety Team representative for employees
- Ensures that all safety procedures are understood and followed by providing up to date safety training to all employees and auditing procedures
- Ability to deliver results with little direction and lead others in a challenging, dynamic union work environment to improve overall Quality performance
- Well-organized, detail orientated and strong leadership abilities
- Demonstrate ability to effectively communicate with all levels of the organization
- Available for after-hour coverage and face-to-face employee coaching as business needs dictate
- Lean Six Sigma/Continuous Improvement experience
- Theme Park Operations knowledge and experience
- Experience managing in a union environment
2
Senior Manager Quality Control Biotech Resume Examples & Samples
- Responsible for short and long term goals of quality control (QC) laboratory efforts in support of NDA and commercial products
- Responsible for method transfers to routine use including adaption of all related quality systems and participation of QC staff in support of validation of methods and qualification of equipment
- Responsible for testing of biopharmaceutical drug products, QC inspections and auditing of these drug products
- Manage staff of Quality Control Biotech department ensuring timely product disposition: release and stability testing, in-process testing, QC documentation, equipment maintenance and calibration and QC laboratory design and maintenance
- Ensure compliance to regulatory requirements
- Ensure Safety and Quality standards are reliably maintained and comply with J&J global guidelines and regulatory expectation
- Develops departmental budget for quality assurance and quality control, including defining materials, equipment and personnel needs
- Drive continuous improvement
- Responsibility for training, development and performance of all Quality Control Biotech associates
- Establishes and directs QC control programs and GMP training programs. Reviews and approves quality reports and GMP documentation
- Lead proactive succession planning and a high performance culture through people training and development, targeted assignments and career planning
- Engage in sector and corporate initiatives
- Member of the Site Quality Control leadership team
- A Master’s or PhD degree or equivalent in a scientific discipline
3
Manager, Quality Control Resume Examples & Samples
- Evaluates operations and/or processes in the foundry and in manufacturing for opportunities to improve those operations and/or processes in the area of quality assurance while maintaining a high level of safety/ergonomics and productivity
- Drives efforts to meet Zero Harm requirements in the Quality department and plant as a whole
- Maintains agency approvals and certifications in good standing, including ISO Annual Surveillance audit
- Tracks and analyzes PPM for all customers of the business unit; uses data to provide for corrective action and continual improvement
- Solves practical problems as well as technical product and/or process problems for corrective action, preventive action and continuous improvement
- Interprets drawings, engineering and product specifications, supplier requirements, and customer requirements
- Presents information in one-on-one situations, in small group situations, as well as to customers, suppliers, and other employees at all of levels of the organization to include corporate personnel
- Manages the Quality Management System to insure ISO standards are met
- Manages the Quality Objectives
- Manages the CPAR and CAR system to provide for timely corrective action for both internal and customer issues
- Develops and manages department expense and CAPEX budgets to support the business unit
- Conducts annual Management Review
- Analyzes processes and process inputs, examines materials and products at various stages of processing to assure conformance to specifications
- Gathers/collects data as required or directed to analyze procedures or processes for improvement
- Establishes or adjusts work procedures to meet quality requirements
- Recommends measures to improve quality of product and production methods, equipment performance as appropriate
- Applies Lean and Six Sigma tools to analyze and resolves problems, and assists others in solving work problems
- Initiates or suggests plans to motivate workers to achieve quality goals
- Works with Materials Management to develop suppliers (Sales Reps or Technical Service persons) to improve quality of products and services to assure requirements are met
- Researches, requisitions, and inspects materials, supplies or tools for use by quality department personnel, as required
- Interfaces with and confers with managers and supervisors to coordinate and support quality activities of individual departments
- Understands the technologies and uses of machines and equipment used by quality department personnel
- Provides training instruction to all quality department personnel, as well as operations personnel, in support of the quality management system, as required
- Communicates, supports, and enforces company policies
- Interviews employees, appraises performance, rewards and disciplines employees, addresses complaints and resolves problems
- Maintains time, and pay records; submits for processing. Reviews time punches daily, makes changes, corrections, comments, documents errors. Enters employee pay and promotion changes
- Actively participates in Lean and Six Sigma Process Improvement projects
- Maintains a positive example of safety-first attitudes and practices
- Actively participates in Safety Programs and Improvement Projects
- Assists management and safety professionals in investigate accidents, incidents and near miss situations
- Participates in safety activities such as support for Suggestion Boards, Grass Root team projects, 5S projects, department ergonomic improvements
- High school diploma or general education degree (GED) required; Bachelor's degree (B. S.) in Engineering, Management, or Metallurgy from an accredited College or University is preferred
- At least five years functional experience working with foundry processes to include Melt, Molding, and Core making, Finishing, Metallurgy, and Metrology required
- At least five years of supervisory experience required
- Excellent interpersonal skills essential; ability to successfully deal with change, learn new skills, techniques and processes, and a positive attitude required
- Experience in Microsoft Office Word, Excel, and PowerPoint required
- Knowledge and skill in Minitab and other SPC tools is preferred
- SQC, AFS and other affiliations are a plus
4
Manager, Quality Control Lab Resume Examples & Samples
- Provide technical expertise to aid in making decisions on the release of raw materials, intermediates or finished products. In a timely manner, work with appropriate teams to make recommendations and/or formulate action plans for investigation and disposition of materials which do not meet release specifications
- Streamline product release activities and create efficiencies to assure rapid completion of lab testing with a minimum of staff while maintaining technical accuracy and correctness
- Ensure lab throughput meets business demand by effectively planning resource and equipment capacity
- Develop training and cross training plan of lab personnel to enable efficient lab throughput
- Effectively manage, develop and motivate a team of chemists
- Effectively lead projects as assigned. Plan, perform and evaluate experiments as needed
- B.S. or M.S. Degree in Chemistry, Biology or Clinical Chemistry with 10 years related experience of which five (5) must have been in a proven leadership role
- Knowledge of the diverse operations of chemical Quality Assurance and Quality Control principles, statistic and computerization
- Knowledge of QMS preferred (i.e. ISO 9001 or ISO 13485)
- Ability to rapidly and effectively resolve manufacturing and/or procedural problems
- Strong “people skills” to be able to deal with various personalities and levels within the organization
- Position will require occasional travel to Fair Lawn, NJ facility
5
Manager, Quality Control Resume Examples & Samples
- Direct QC testing of raw materials, intermediates and finished products requiring testing by automated chemistry methods. Assure compliance with site, divisional, corporate and regulatory guidelines, as applicable
- Work with Product Development, Quality Assurance and Regulatory Affairs to interface new products into QC operations so that appropriate systems are in place to control new products
- Develop qualification plans for changes in existing products or raw materials. Coordinate the qualification requirements with other QA teams; document the qualification recommendation
- Serve as QC representative on cross-functional, inter-facility and product integration teams
- Develop and maintain a flexible organization such that fast changing manufacturing priorities can be accommodated with a minimum of disruption. Work with manufacturing on a daily basis to meet their scheduling needs and avoid product backorders
- Assure that all lab instruments are audited in a timely manner and in compliance with appropriate regulations. Assure that software is adequately documented and validated
- Implement practical process improvements to reduce lead times and improve turn-around times for lab testing. This includes lab metric development and countermeasures (e.g. daily releases, backlog >5 days, equipment down time, COA releases …)
- In-depth knowledge of chemical testing/analytical support instrumentation for wet and dry chemicals
- Broad technical knowledge encompassing diverse product lines and a proven ability to troubleshoot complex problems
- Ability to use critical judgment in a very demanding environment to address product or process problems under immediate time constraints
- Ability to review current processes and implement productivity improvements
- Demonstrated leadership and supervisor skills, including the ability to effectively motivate and develop employees and delegate work assignments
6
Manager, Quality Control Resume Examples & Samples
- Manage Stability Program. Manage and supervise day-to-day activities for Quality Control staff in accordance with company policies and procedures
- Manage hiring, training, and coaching employees, as well as supervise department staff including necessary written evaluations and recommendation for promotion or termination
- Supervise department staff in accordance with company policies and procedures
- Manage the QC department budget and financial reporting efforts
- Provide independent scientific quality resource for product line QC testing oversight and provision of test plans to meet regulations
- Coordinate with the Technical Process Owner for final review of all test data for accuracy and passing performance and for training staff on new or revised testing procedures
- Perform product performance data review and release and participate in product failure investigations/CAPA implementations
- Perform trend analyses on product performance and provides feedback to appropriate functions to improve quality and performance. Identify the effectiveness by the review and analysis of the QC metrics and provide management with improvement recommendations based on tracking and trending reports
- Formulates area policies and practices and establishes/writes efficient product QC test procedures
- Manage the implementation and training on new product test procedures and documentation that assure systems, procedures, and people comply with quality standards
- Direct staff in the development, analysis, and preparation of reports to generate quality reports and conduct effective presentations for meetings
- Communicate issues proactively to management and identify gaps (compliance, safety, procedural) that can have an impact on quality and business objectives
- Develop a higher level of technical and quality guidance to individuals and/or functional groups on matters that relate to quality control issues in the manufacturing and product development cycles
- Ensure the maintenance of a safe work environment for staff
- Master’s degree in bio-chemistry or a related field of study
- 6 years of related working and lab experience in a manufacturing industrial Biotechnology/Pharmaceutical GMP/ISO regulated Medical Device environment
- 2 years of experience working in a Quality Control leadership responsibility role
- Proficient in relevant software such as Microsoft Office, Document Control System. Comprehensive knowledge of global ISO 13485, EU IVDD, CMDCAS, CGMP, cGLP requirements, as well as industry standards for IVD regulated products
- Business and management principles and practices, as well as the ability to read and interpret accounting and financial reports
- Strategic planning, human resource management principles and procedures, basic economic and accounting principles and practices, and office administrative procedures
- Basic principles of Good Manufacturing Practices (GMP). Understanding of a wide range of HLA laboratory testing protocols and performance characteristics of HLA test assays. Statistical process controls, including validation, and verification requirements
- Good Laboratory Practices and Management
- Statistical process controls, including validation, and verification requirements
- PhD in the biological sciences
- Lab experience in the field of HLA, Antibody testing and/or Molecular techniques
7
Manager, Quality Control Resume Examples & Samples
- Experience leading a Quality Control finished product testing group in the pharmaceutical industry with experience in parenteral and/or solid oral dosage forms preferred
- Must be able to work in situations where speed and sustained attention are essential, performing a variety of tasks without loss of production
- Prioritize tasks and responsibilities of laboratory employees
- Communicate with internal customers and external clients
- Accept responsibility for design and maintenance of cGMP laboratory systems
- Accept responsibility for state of compliance for the microbiological laboratories, as applicable
- Serve as a leader to teams of employees both within and between departments
- Act as a successful team member in non‑leadership roles
- Develop, implement and manage achievements of results within budgets
- Determine department goals consistent with Alkermes' strategy, develop plans to achieve those goals, and prioritize and execute those plans
- Maintain open communications and promote teamwork and employee participation in the work group
- Provide regular, appropriate feedback to subordinate personnel. Perform annual performance appraisals; co-create new goals and objectives; look for career developing opportunities when appropriate
- A Bachelor of Science or Master of Science with at least 10 years of pharmaceutical industry experience in the Microbiological laboratory, or 8 – 10 years of experience with a Ph.D. in a scientific related field
- At least 5 years of experience in a leadership/managerial role in a cGMP laboratory
8
Manager / Senior Manager, Quality Control Resume Examples & Samples
- Owns the procedures that govern the QC department and ensures that all documents are approved and in alignment with quality standards
- Ensure that the QC laboratory provides results consistent with timeline requirements
- Oversee laboratory investigations and assist with product impact assessments
- Supervise third party contract laboratories for execution of agreed upon studies
- Coordinate with other departments to ensure methods are transferred to QC
- Champions the continuous improvement process, defining process improvement/efficiency projects
- Select, train, and develop staff so that they realize their full potential and work in conformance to company and regulatory policies
- Work with Site Environmental Health & Safety (EH&S) representatives to ensure that QC laboratories meet standards, requirements, and best practices
9
Manager, Quality Control Resume Examples & Samples
- Drive activities at the Solothurn site to adhere to the construction or operational schedule
- Support execution of raw material strategy. Develop specific raw material control documents for materials to be utilized for GMP production. Support raw material handling and documentation specific for the Solothurn site
- Support execution development and implementation of the business process for material release at Solothurn, including consulting with IT for the development of the supporting information management systems
- Oversee the early (pre-GMP) environmental and utility support activities (e.g. water system sampling). Support monitoring activities and data review as required. Oversee Supplemental staff supporting pre-GMP activities
- Serve as a Quality team member representative during construction to address schedule and tactical aspects of project execution
10
Senior Manager, Quality Control Chemistry Resume Examples & Samples
- Manages day-to-day operations within the assigned functional group to ensure materials and products are tested, reviewed and approved within the accepted time frames. Interprets data and resolves technical issues for group
- Reviews, authors, and edits documents, including deviations, change control requests, SOPs, test methods, and laboratory test plans and related technical reports. Ensures compliance with current regulations
- Coaches, mentors, leads and manages employees. Ensures that training and other personal development programs are in place for succession planning and the development of subordinates. Ensures that performance opportunities are proactively managed through the performance management system
- Provides leadership for managers, analysts and technicians to optimize productivity and quality of work. Provides effective planning for department operations to include required resources, and the maintenance & communication of cycle times
- Actively participates on cross functional teams (may include facilitation) and shares information, as appropriate, with direct reports. Effectively communicate with stakeholders and/or managers in other departments. Actively leading in investigation issues and formulating action plans to resolve deviations
- Implements procedures and optimal infrastructure to ensure compliance with all regulatory agencies. Serves as the department representative on regulatory audits. Provides accurate and timely delivery of data and reports to support regulatory filings. Performs assessment of current systems, to provide guidance for improvements to or development of streamlined, scalable GMP systems
- Coordinates the reporting of KPI's and metrics and lead monthly QC functional reviews
11
Manager, Quality Control Resume Examples & Samples
- Proactively plan and prioritize lab operations and resolve quality and compliance issues
- Independently exercise judgment for broadly defined practices, procedures and policies to select methods, techniques and evaluation criterion
- Make decisions that have a high impact on future Quality Control processes and procedures and may affect other departments within the organization
- Use judgment and experience to troubleshoot problems and formulate solutions
- Use a variety of laboratory instrumentation and computer systems to review data (such as LIMS)
- Represent QC business processes and needs within the department and at cross functional forums as a technical expert
- Demonstrate an in-depth theoretical understanding of laboratory operations, systems, methods and regulatory compliance
- Demonstrate an understanding of company priorities, objectives and project timelines. This includes understanding how QC activities affect the business
- Apply scientific judgment to perform work and contribute to milestones related to specific projects
- Interact with management to review FTE requirements, annual budgeting and other business needs
- Responsible for maintaining a compliant training program to ensure analysts are trained on assays, equipment and procedures prior to executing tasks within the lab
- Proactively identify ways to improve systems, workflow and overall efficiency in the lab and take the appropriate action to implement change. This includes performing assay and laboratory system assessments, independently, or as a team leader
- Work with analysts to qualify, optimize and validate applicable assays, equipment and laboratory systems
- Work with analysts and employees from other departments to troubleshoot problems of broad scope that encompass multi-faceted project/experimental areas
- Ensure analysts have an appropriate functional and theoretical understanding of assays by establishing a training curriculum
- Review SOPs, studies, validation documentation, change controls and investigations to maintain compliance
- Demonstrate an understanding of how analytical method performance impacts the business
- Delegate responsibility and projects to QC Analysts based on their level of judgment and experience
- Meet with individual employees on a regular basis to discuss, prioritize, and assign laboratory work and projects
- Independently manage personnel development, annual performance reviews and performance issues with minimal guidance
- Proactively look for ways to challenge analysts and create career opportunities to enhance job satisfaction and improve the department as a whole
- Previous industry experience in a regulated environment highly desired
- Residual ELISA (e.g. Protein A, HCP)
- Binding and Functional Cell Based Potency
- Binding ELISA (Relative and Identity)
- SDS-PAGE
- IEF
- SEC
- CEX
- Protein A HPLC
- Oligosaccharide
- Polysorbate 80
- Peptide Mapping
- Content Uniformity
- Karl Fischer
- Appearance (Color, Clarity, Visible Particulates)
- Concentration
- CE-SDS
- CE-LIF
- IcIEF
- Particulate matter
12
Manager, Quality Control Resume Examples & Samples
- Develop analytical staff to ensure accurate and reliable data are generated to comply with Quality programs and FDA requirements
- Transfer finished product methods and ensure compliance with USP& ICH. Manufacturing process validation, enhancement and problem solving
- Working knowledge of laboratory computerized systems such as Labware LIMS, Empower, Trackwise, and Oracle
- Working knowledge of laboratory instrumentation such as GC, HPLC, UPLC, FTIR, Dissolution, TPW, Multidose Dissolution, kF, pH, analytical balance, and Fiber Opt-Dissolution
- Identify and resolve technical problems on a timely basis to avoid inaccurate assessments and make recommendations to lab management
- Develop and implement training and career development programs; conduct employee assessments including hiring, terminations, and promotions
- Represent the department during audits, meetings, and teleconferences regarding technical and analytical issues with key regulators as well as internal and external stakeholders
- Provide responses to FDA deficiency letters and audit observations
- Prepare technical reports, standard operating procedures, product specifications, analytical methods and compendia and NDA submissions
- Manage the analytical method development and transfer programs to support new product introductions by ensuring accurate analytical procedures are established for routine use in the QC Laboratories
- Manage the instrument calibration and analytical reference standard programs
- Manage the development and implementation of new automation, analytical methodology and
- Direct investigations and design testing protocols to resolve analytical, quality or production problems at Teva or at contract laboratories
- Establish disposition of product based on conformance to agreed specifications
- Develop validation, method development, and method transfer to ensure soundness of analytical methodology and regulatory compliance
- Evaluate and write Standard Operating Procedures and testing procedures to ensure clear and concise direction is provided to the analyst
- Understand the need to accomplish tasks with a sense of urgency
13
Manager, Quality Control Inspection Resume Examples & Samples
- Must be capable of demonstrating good communication and the ability to handle multiple tasks concurrently with interaction between suppliers, several levels of management, engineering and manufacturing groups. The position requires individual to provide project support and cooperation in cross-functional and concurrent engineering teams. Works with minimal supervision on managing of personnel processing, Receiving and Returned Product, Complaints and Warrantees, including the preparation of related reports and business correspondence
- Associates degree with Quality Assurance and Supplier Inspection experience. 7 years Quality experience in a mechanical , software or consumables medical device environment with emphasis in validation, documentation management and traceability. Knowledge in pre-production Quality Assurance, statistical tools , CNC and plastic injection molding
- Hands on experience related to the above requirements with a successful history of compliance in all phases related to FDA's QSR Regulations and ISO 13485, Federal / OSHA & Local Safety regulations and IT & Physical/Facility security. Must posses the ability to guide and/or lead internal and external audits in a professional manner
- Must be able to use Microsoft Word, Excel and Access and learn and apply other software applications. Must have the skills to train personnel, as required, in the software application SAP R3. Develops metrics, and presentations for Operations Status/Process Review Board meetings. Support continuous improvement of all procedures , processes and monitoring metrics.
14
Manager Quality Control Valuations Resume Examples & Samples
- Coordinate the valuation activities (Desktop, physical valuations and turnaround time) by interpreting and translating available management information (e.g. RVS) and implement corrective actions and processes if required to address gaps
- Obtain a thorough understanding of the business unit's strategy and valuation policies and ensure that the team understands
- Allocate duties to team members in order to achieve operational targets, including prioritisation and work schedules
- Manage the valuations completed by the Valuations Contractors within the agreed and contracted SLAs by studying the various performance reports on the EzVal system and during remediation action where required
- Optimise the service turn-around times by using best practice that is aligned to industry trends
- Conduct research of various residential markets (e.g. new Developments, Affordable Housing) to ensure the maintenance of a market supported structure in the region ensuring that the bank policy remains current and relevant
- Coordinate quarterly meetings with bank business partners (Private Bank, Business Bank, Home Loans and Collections) thereby ensuring that they are informed of service related issues, updates regarding new Valuations requirements and that service delivery is acceptable
- Attend external stakeholder meetings (e.g. Developers) to give advice on technical and administration requirements (e.g. occupational certificates) with regards to the bank’s policy and procedures
- Gather market information on residential transactions by drawing reports on the system e.g. Lightstone, as well as the Deeds Office. Analyse trends regarding property sales, new supply (developments) and forced transactions (defaults or auctions) in the region and provide quarterly report to PBS management
- Provide input and participate in the annual business planning session and ensure that all regional related activities are addressed and included in the stated objectives for the year
- Implement productivity improvement measures by coaching staff on any new processes or on their areas of improvement
- Participate in the measurement and reporting of internal and external Service Level
- Agreements on a monthly basis. Address any process failures specific to the department under management
- Manage all valuation complaints from clients and mortgage originators in terms of property values and turnaround time by analysing the sales data, inspecting the property and meeting the client if necessary
- Monitor daily the budget and minimise operational expenses of valuations performed by analysing the performance and valuation fee reports to ensure that there are no overpayments to Service Providers
- Manage the income recovery process (e.g. valuation completed) from Business Units
- Provide information in the preparation of the income and expenditure projections to support regional budget by analysing the market and economic data (e.g. tariffs paid in the market) which feeds into the overall Annual Valuation Unit budget
- Create and encourage a culture of continuous improvement by continuously reengineering business strategies, policies and processes to ensure optimal customer satisfaction and service delivery
- Display a pioneering strategic approach in continually seeking opportunities for operational efficiencies
- Provide guidance to the team in order to achieve world-class standards of efficiency and client service and to continually strive to enhance existing processes
- Champion process and technological advances by providing the necessary focus to ensure successful performance
- Develop, manage and maintain effective relationships with service providers from within the group to support world class delivery
- Build strong working relationships within RBB and the Regional Managers Home
- Loans, Agri business, Private Bank, Collections and Commercial Property Finance
- Encourage reward and propagate a culture of treating customers fairly and delivering on Voice of the Customer (VoC) through an enabling and business innovation culture
- Participate in regular joint root cause analysis with BUs to identify ways to reduce risk exposure by streamlining of processes, improvement in governance etc
- Maintain a high level of professionalism in stakeholder interactions, including written and verbal communications, based on sound knowledge of the industry and understanding of relevant regulatory requirements
- Manage stakeholder relationships across external valuation firms and other service providers of property industry data and technology
- Participate and contribute in joint business planning to ensure alignment of operational objectives with the business plans of RBB and business units
- Cooperate with engaging auditors, compliance and other risk officials
- Create a network and build relationships, strategic alliances and business partners (both internally and externally with vendors or counterparts (e.g. Sales, Credit, Group IT, Agencies, Attorneys and Value Add Product Partners)
- Manage and implement stakeholder relationships
- Keep abreast with compliance and regulatory requirements and liaise with all relevant stakeholders internally and externally in the organisation to ensure accurate implementation and adherence to rules and regulations
- Utilise knowledge of environment to continuously challenge status quo and provide input and support to business to enhance customer experience
- Provide high focus to problem resolution utilising diplomatic negotiation practices to ensure streamlined service delivery
- Manage a team that implements strategic outputs and creates central alignment for efficiency
- Perform people management functions, including but not limited to -
15
Associate Manager, Quality Control Resume Examples & Samples
- Supervise laboratory work of senior chemists, chemists, and chemist assistants to ensure testing of laboratory samples to meets commitments specific to assigned area. Responsible for general organization of the laboratory and personnel
- Enforce laboratory policies and resolve personnel issues
- Coordinate with senior chemists and project management to schedule assignments and projects
- Represent functional area in QC management, operations, and organizational meetings
- Perform data analysis, audit data and analytical procedures, generate metrics, prepare protocols, and summary reports. Prepare, review, and update laboratory analytical procedures, Standard Operating Procedures (SOPs) and guidelines
- Perform troubleshooting of functional area problems and issues
- Serve as group and/or project leader. Mentor senior chemists, chemists and chemist assistants. Manage and motivate technical and personnel career growth of personnel
- Provide direction and technical guidance in the initiation of analytical investigations. Organize and lead Analytical Investigations as well as perform composition and review of related Analytical Investigation Reports
- Minimum of a Bachelor's degree in Chemistry or similar science discipline (or equivalent) and 2-4 years of experience. However, a combination of experience and/or education will be taken into consideration
- Must possess excellent written and verbal communication skills, interpersonal skills, management skills, strong work ethic, consensus gathering skills, organizational skills, and a working knowledge of Microsoft Office including Word, Excel, and Lotus Notes. Must be accurate, detailed oriented, team focused, and possess the ability to multi-task and work in a fast paced, high output environment
- Ability to solve problems with a variety of concrete variables through semi-standardized solutions that require some ingenuity and analysis. Ability to draw inferences and follow prescribed and detailed procedures to solve moderately complex problems
- Normal office situation. Regular exposure to chemicals, solvents, fumes and/or gases
16
Senior Manager, Quality Control Resume Examples & Samples
- Continuously evolves the Quality Control system to take advantage of new and emerging automated inspection methods, manufacturing methods, and industry best practices
- Manages the operation of the Incoming, In-Process, and Finished Goods inspection and acceptance of electronic components, sub-assemblies, and finished products
- Manages the activity of the Material Resource Board (MRB) to meet the needs for the design, development, and manufacture of Masimo products
- Promotes and encourages a work environment that challenges employees to constantly search for ways to perform their activities more efficiently and effectively, especially where automated and semi-automated methods can be employed
- Ensures the Quality Control system records conforms to requirements of the Quality Management System (QMS)
- Ensures timely inspection, acceptance, and Material Resource Board (MRB) activities, including prioritization
- Formulates response to internal audit findings and CAPAs
- Develops and reports Quality Control (QC) metrics appropriate to monitor and improve QC activities
- Direct, plan, delegate and manage department staff including
- Seven or more years of experience with quality control inspection and testing of electronic components, sub-assemblies, and finished products
- Working knowledge of all aspects of manufacture of complex electronic products including but not limited to semi-conductor manufacture, injection molding, wire and harness manufacture, assembly line operations, and final product testing
- Proven ability to develop and implement innovative solutions to problems and/or improvements to existing systems, especially focused on implementing automated and semi-automated methods to replace manual operations and paper records
- Knowledge and experience working within a Quality Management System in a highly regulated industry (e.g., medical devices, aerospace, or automotive)
- Knowledge and experience with IPC 610, 620, IPC J-STD-001E and MIL-T-31000/MIL-STD-100E
- Knowledge and experience in electronic assemblies and cable/harness manufacturing
- Good interpersonal skills dealing with peers and other functional areas
- Ability to travel domestically and Mexico (within 25 miles of the Mexico border) up to 20% of the time
- Must be able to lift up to 50 pounds
- Computer Skills in Microsoft Office suite
- Prior experience in a Medical Device manufacturing environment
- Experience with Agile PLM is preferred
- Familiar with ISO-13485 requirements
17
Manager, Quality Control Resume Examples & Samples
- Working with purchasing staff to establish quality requirements from external suppliers
- Making sure that production processes meet international and national standards
- Validates quality processes by establishing product specifications and quality attributes; measuring production; documenting evidence; determining operational and performance qualification; writing and updating quality assurance procedures
- Maintains and improves product quality by completing product, company, system, compliance, and surveillance audits; investigating customer complaints; collaborating with other members of management to develop new product and engineering designs, and manufacturing and training methods
- Contribute as a subject matter expert and serve as a mentor on the Quality Management System, including root cause, corrective action and internal audits to ensure effectiveness
- Support development, implementation, and analysis of quality measurements to improve organization and program performance
- Provide the cross-discipline interface with Engineering with particular focus on process and product quality, organizational improvement and CMMI
- Drive continuous improvement through innovative improvements in IDS Mission Assurance methods and provide quality improvement expertise and leadership to adjacent functions
- 8+ years of increasing responsibility and management in the areas of quality, design & development, integrated supply chain or operations
- 8+ years’ experience in Six Sigma and/or other contemporary methodologies for process improvement
- 8+ years quality sciences; quality systems, concepts, and management and planning tools, or statistical process control tools
- 8+ years experience with general AS 9100 Quality requirements
- 5+ years experience with Earned Value Management
- ASQ CQM or CMQ/OE certification or demonstrate ability to certify within 4 months
- 12+ years’ experience improving organizational capabilities to achieve product and process quality
- 5+ years generating, reviewing, managing and implementing organizational policies and procedures, work instructions and testing procedures
- 10+ years of experience leading matrix organizations
- General understanding of construction regulations and standards
- Experience building teams, resource capability, capacity, effectiveness and efficiency through people development
- Proven analytical skills in Root-cause analysis, corrective / preventive actions
- Demonstrated success on large scale cross functional teams
- Ability to execute, and hold others accountable in results based environment
- Strong strategic thinking skills coupled with ability to align and link organizational objectives
- Effective leadership skills with strong influencing, negotiating and change management skills
- Certified Six Sigma Expert/Black Belt
- Excellent written and verbal communication and presentation skills with proven success in communications at all levels
- Working knowledge of Records Management
- Working knowledge of IPDS
- Risk and Opportunity Management
- MS Engineering / Science desired
18
Manager, Quality Control Resume Examples & Samples
- Hiring, organizing, training and retaining energized, motivated, team oriented staff. Will need to stress and carry forward operator training, education and advancement
- Identifies QC responsibilities, work to be performed and timelines pertaining to area of responsibility
- Understand regulatory requirements and Lonza policies pertaining to the area of responsibility. Ensure Quality Control policies or procedures are appropriate and establish and/or revise, as necessary
- Ensure regulatory and customer inspection readiness and represent the department and participate in audits as required
- Collaborate and prioritize with QC supervisors, other departments and/or customers to create an achievable work schedule and to ensure agreed upon timelines are met
- Represent QC and Lonza in customer meetings to receive/deliver information, request and requirements
- Measures throughput, performance and other appropriate metrics and report them to management
- Develop the technical, GMP and leadership skills of QC personnel and perform mid-year and annual reviews of supervised QC personnel
- Maintain laboratory budget
- Bachelor degree and/or Advanced Graduate degree (MS/PhD); Preferred area of study: Chemistry or equivalent Science Field
- Preferred 7+ years in a GMP/Professional environment; ideally 5 years direct supervisory/manager experience
- Use of Microsoft Suites (Word, Excel, PowerPoint)
- Use of Laboratory computer systems
- Potential previous use of GMP Quality Systems such as: TrackWise, LIMS, DMS,
- Use of laboratory equipment including, but not limited to: HPLC, GC, titration, pH, viscosity, FTIR, colorimetry
19
Manager, Quality Control Resume Examples & Samples
- Sample
- Projections
- Imputation
- Data Editing and Outlier Controls
- Calibration and Benchmarking
- Final data outcomes
- Design, build and implement QC/QA reports/tools focused on outcomes critical to client needs that are automated, standardized wherever possible and inclusive of advanced issue detection mechanisms to drive enhanced quality control
- Promote consistency and best practices in the implementation of QC/QA processes across different businesses within Hardlines/Food sectors across all relevant Geographies
- Work closely with Methodologists to build the appropriate checks/reports
- Maintain relationships with Research Services client teams to ensure adoption of QC/QA processes with close coordination on best practices and continuous improvment
- Align with Product, Commercial, and RBG members to ensure that we are focused on the most critical outcomes
- Communicate results and procedures to internal clients
- Fluency of multiple key Consumer and POS methodologies, processes and procedures
- Strong understanding of data collection and analytical processes
- Detail-oriented with strong organization/project management skills and the ability to manage multiple priorities/deadlines
- Ability to communicate ideas and analytic results effectively both verbally and in writing to both technical and non-technical audiences
- Proven success in ability to consult and to interact effectively with senior internal clients
- Proficiency in analytical tools such as SAS and R is preferred
- Proficiency in MS Office (Excel, PowerPoint and Word)
- BA/BS
20
Senior Manager Quality Control Resume Examples & Samples
- Manage multiple groups within department focused on routine testing
- Set laboratory testing schedule and communicate to reports and across organization
- Represent Analytical Sciences at interdepartmental deviation meeting. Set strategy for resolving department deviations. Update senior management as needed on progress
- Ensure data is reviewed and authorized in a timely manner
- Ensure GMP compliance within the group
- Lead laboratory investigations, driving to root cause
- Perform job duties with little to no direction from supervisor. Able to navigate ambiguity and changing priorities
- Strive for continuous improvement and operational efficiency within the group
- Work with QC project management and other functions to determine sample forecast and priority
- Maximize analyst and instrument productivity
- Write group SOPs and provides drafts of proposed test methods to QC
- Transfer methods to commercial QC organization
- Keep laboratory in inspection ready state
- Solid supervision and leadership skills
- Requires BS/BA in a scientific or engineering field and 8-10 years relevant experience, including 3-5 years of management experience
21
Section Manager, Quality Control Resume Examples & Samples
- Manage contract laboratory testing. Be a liaison for all contract laboratories
- Manages testing, reports, validations and release of results
- Provide supervision in the daily activities of personnel: Establishes priorities and coordinates activities of direct reports
- Responsible for people management activities including: coaching, performance reviews, resolution of personnel issues
- Coordinate training of direct reports
- Sample Life Cycle Management: e.g LIMS, Retains, Sample Metrics- etc
- Oversee Data Review and Archiving
- Oversees, appropriate disposition of all products and their component materials through the timely release of complete, accurate test results
- Oversees complete documentation of test records for all materials tested
- Assists in assuring laboratory is in compliance with appropriate regulatory requirements and understands Corporate and Divisional policies related to documentation, and ensure compliance
- Coordinates projects as directed by department manager to implement efficiencies in document/system automation and business process improvements
- Writes/revises procedures as necessary and provides support for department
- Develops and maintains trend reports, backlog report, and document error reports which support departmental performance
- Participates in selection, hiring, training, termination, promotion or placement of employee in their group
- Participates in all group performance reviews, merit ratings, and salary an increase
- Write Investigations
- Assist in troubleshooting assays
- Oversee samples sent to an outside contract laboratory. This can include shipping, receiving results and reporting
- May be responsible for one or more shifts. Facilitate department or shift communication meetings
- Participate with teams and projects as assigned by manger
- Conduct annual performance reviews with employees
- Assist with employee development
- Interview job candidates
- Bachelor's degree in Science or equivalent + 8 years of relevant experience OR Master's degree in Science or equivalent + 6 years of relevant experience
- Must be experienced and demonstrate high level of technical skill in technical lab operations and good understanding of related business
- Related knowledge in Product Quality, Quality Control Lab Operation and Regulatory requirements is required
- Ability to work independently to meet operational goals and business needs
- Ability to develop, design, execute and manage complex research programs
- Ability to interact and establish positive interaction with internal/external customers
- Shows broad understanding of the issues relevant to technical/science and business
22
Senior Manager, Quality Control Resume Examples & Samples
- Manages the activities of the quality control department to create a culture of quality awareness, teamwork, and cooperation with all departments within the Facility
- Assures compliance with Quality System Regulations and ISO regulations within the quality control department
- Conducts trouble shooting investigations and product support activities for in-house production and for customer requests
- Improve the customer experience regarding initial quality and long term reliability by working issues to root cause and implementing robust corrective and preventative action plans. This will likely involve strong cross functional skills to arrive at consensus as to most effective solution and implementation plan
- Ensures compliance with applicable laws and regulations including processes and systems related to cGMPs
- Monitor and trend quality data; ensure periodic cross-functional reviews, of quality metrics and implement corrective actions against adverse trends and non-conformances
- Identify and support Practical Process Improvements (PPI) initiatives within the quality control department
- Provides career development and training to direct reports
- Work with R&D to ensure product manufacturability and product reliability issues are addressed in the design stage of new product development
- Management and oversight of quality instrument maintenance
- Prepares yearly training schedules for the department and perform periodic employee reviews
- Establishes and Maintains SPC for new and existing products
- Bachelor of Science in Chemistry, Biochemistry, or Bioscience, Masters preferred
- Over 10 years Quality Assurance/Quality Control experience, preferably in the medical diagnostics/pharmaceutical industry
- Minimum of 5 years of direct supervisory experience
- Experience leading quality initiatives
- Ability to analyze data, summarize results, troubleshooting issues, and identify solutions
- High level of communication and presentation skills, with strong word processing and spreadsheet software skills
- The position does not offer Relocation Assistance
- Strong command of Quality System Regulations and ISO
- Experience with project management and process improvement practices
- Excellent organizational skills to manage multiple tasks simultaneously
23
Senior Manager Quality Control Resume Examples & Samples
- Pharmacist, Master in Engineering or equivalent through experience
- 10+ years of experience in the pharmaceutical industry
- In-depth understanding of analytical development, qualification, validation, technology transfer, testing and release processes
- Thorough knowledge of pharmaceutical legislation, cGMP regulations and guidelines
- Exposure to EU and FDA inspections
24
Stability Manager, Quality Control Resume Examples & Samples
- Lead the Stability Team and manage all activities related to establishing new stability studies as well as maintaining on-going stabilities for multiple Phase 1/2 clinical programs in a compliance with ICH, WHO, company quality guidelines and SOPs in support of the company’s timelines and goals
- Support the QC organization with regulatory submissions
- Ensure compliance with stability policies, regulations, procedures and protocols
- Author and/or review and approve Stability Study protocols and reports
- Manage and maintain the stability schedule and communicate the testing forecast to QC stability team and contract labs as applicable to maintain compliance with stability testing requirements
- Review data, perform trending and report stability status to project teams
- Initiate and participate in investigations as needed
- Work with Process Sciences and QC Validation to resolve technical issues in stability studies as needed
- Support and author appropriate CMC regulatory sections with regard to stability data and trends
- Oversee purchase and identify new equipment required for conducting stability studies and ensure that all stability equipment operates within appropriate parameters, including ensuring that calibration and qualification requirements are met
- Purchase, implement and maintain stability software and trending database
- Ability and desire to work in a dynamic, fast-paced team environment
25
Manager, Quality Control Resume Examples & Samples
- Experience in cGMP regulations
- Good verbal and written communication skills with the ability to work in a team setting
- Good interpersonal and supervisory skills
- Experience with cell culture and cell based assays
26
Manager, Quality Control Resume Examples & Samples
- Develops and analyzes statistical data and product specifications to determine present standards, and establish proposed quality and reliability expectancy of finished product
- Formulates and maintains quality control objectives and coordinates objectives with production procedures in cooperation with other managers to maximize product reliability and minimize costs
- Directs workers engaged in inspection and testing activities to ensure continuous control over materials, facilities, and products
- Plans, promotes, and organizes training activities related to product, quality, and reliability
- Must comply with company safety rules and regulations and wear proper safety equipment while on plant grounds
- Investigates and adjusts customer complaints regarding quality in order to maintain customer relations
- 4-10 years related experience and/or training; or equivalent combination of education and experience
27
Manager, Quality Control Resume Examples & Samples
- Implement all inspection functions as directed by the Director Quality Control
- Administer the weight & balance program ensuring accuracy and up-to-date data is used
- Supervise and schedule all Inspectors in coordination with production department requirements
- Administer the “Required Inspection Item” (RII) program in-country on behalf of the Director Quality Control
- Audit aircraft maintenance records ensuring accuracy, completeness, RII and proper Airworthiness Releases
- Ensure FAA Form 337 are prepared by inspectors for aircraft alterations and major repairs
- Administer the in-country Receiving Inspection Program on behalf of the Director Quality Control
- Administer the in-country Airworthiness Release Program on behalf of the Director
- Ensures maintenance and inspection personnel comply with GMM policy and procedure
- Ensures current Approved Data is used for the maintenance and/or modification of company aircraft
- Executes the Inspection Countermand process prior to elevating issue to the Director Quality Control
- Removes aircraft from service that do not meet regulatory airworthiness standards
- Position requires U.S. Security Clearance
- 5 years of Part 121/ 135 maintenance experience (see Qualifications below)
- Familiarity with inspection methods, techniques and equipment used in area of expertise
- Integrity - Committed to passionately and consistently promoting a professional culture that is trustworthy, honest, socially responsible, and where differences are respected and valued
- Expense Management - Plans budget appropriately, uses sound judgment; analyzes operation for improving expense efficiency; demonstrates knowledge of financial process & results
28
Manager, Quality Control Resume Examples & Samples
- Oversee the Global QC Instrument and Equipment Strategy team, including the Site Leads in RTP and Hillerod and supporting staff or contractors as applicable. Develop and manage a Lifecycle Strategy for all QC analytical equipment and instruments. Ensure global alignment on selection and implementation of analytical equipment, instrument systems, and software applications. Manage the annual capital budget for Global QC laboratories, including development of the budget proposal, sourcing strategy, creation of capital approval forms and purchase requisitions
- Direct validation/qualification projects for QC laboratory equipment, instruments, software applications and computer systems per applicable procedures. Review and approve system life cycle documentation including VP, RS, IOPQ protocols, decommissioning protocols, other compliance related protocols/reports, change control requests, validation protocols/reports as applicable. Plan, implement and direct core functions of teams related to equipment/instrument purchase, maintenance, and implementation or decommissioning projects; provide technical support as well as facilitation of investigations/compliance tasks; support QC staff and lab operations related to business; support global harmonization initiatives; training and completion of projects to milestones. Oversee the Global QC Instrument and Equipment Strategy team, including the Site Leads in RTP and Hillerod and supporting staff or contractors as applicable. Develop and manage a Lifecycle Strategy for analytical equipment and instruments. Ensure global alignment on equipment, instrument systems, and software applications. Manage the annual capital budget for Global QC laboratories
- Coordinate QC support activities/projects related to instrumentation/equipment with other departments & key contacts (internally/externally); provide updates to QC management. Work closely with QA, IT, Facilities, Instrumentation & Controls, etc. Support and help to design effective laboratory systems/life cycle to ensure integrity of all laboratory instrumentation/equipment programs. Participate in a leadership or membership role for site cross-functional teams as a representative of the QC laboratories
- Ability to flex and respond to unexpected situations/demands; effectively problem solve and raise issues appropriately as well as provide resolution as necessary. Support tracking of tasks and meeting Biogen deliverables. Training and mentoring of staff
- Experience with managing analytical equipment and instruments in GMP Quality Control laboratories
- Minimum of 3 to 5 years leadership experience
- Skilled in MS Office applications (Word, Excel, PowerPoint) as well as QUMAS DocCompliance, TrackWise, NuGenesis SDMS, MS SharePoint
- Familiarity with lab applications such as LabWare LIMS, Empower CDS, and vendor-supplied instrument control and data analysis software commonly used in QC laboratories in the pharmaceutical industry
29
Manager, Quality Control Resume Examples & Samples
- Lead the work order process by generating work orders to the appropriate department to ensure timely follow-up, generate weekly spreadsheets tracking work orders and project work status with associated costs and work closely with all departments to assess work order needs and provide estimates
- Manage third party service providers by enforcing the agreed upon scope of services within the various signed service agreements. Ensure the highest quality of service is being delivered at all times
- Perform daily inspections of the interior and exterior of the arena proper. Follow up with the appropriate vendor to address any issues that need immediate attention
- Review Manager on Duty event notes to follow-up on items that need immediate attention and incorporate into the work order process as required ensuring timely completion
- Work with Facility Services Manager to plan, schedule and price out various projects including the coordination with 3rd party contractors
- Work on Capital Project Team by generating payback sheets, track spending and coordinate work
- Establish and maintaining effective working relationships with VP, managers, supervisors, employees, patrons, clients, service providers and corporate sponsors
- Develop and manage standard operating procedures as they relate to third party vendors, work order completion, safety and inventory control
- Prepare and maintaining required reports/records/certifications for the city, code and/or corporate management
- Supervise cost accounting expenses for related budgets and on-going maintenance projects as required
- Continuously review the departmental needs and recommend repairs, maintenance or special projects
- Creating and implementing purchasing and inventory control systems as it relates to consumable items, tools and equipment within Operations and 3rd party vendors
- Projects as required by the Director, Arena Operations
- Bachelor's degree, or foreign equivalent, in any field plus 5 years of progressively responsible positions and/or post baccalaureate experience in the job offered
- Specific experience as it relates to an 18,000+ seat sports and entertainment facility; organizing and directing event requirements for sporting and entertainment arena events
- Experience working with Unions and the related trades
- Must be organized, detail orientated and have the ability to handle multiple projects simultaneously
- Working knowledge of tools and equipment related to managing a multi-purpose sports and entertainment facility
- Must have a continuous drive and passion for creating an exceptional experience for all guests, employees, tenants and teams
- Knowledge and previous experience working with NBA, NHL/AHL, NCAA (hockey and basketball), FELD Entertainment, AEG Live, Live Nation and other concert and family show promoters preferred
- Experience in developing and managing budgets
30
Senior Manager, Quality Control Resume Examples & Samples
- Master or PhD degree in chemistry, biology, bioengineering or pharmacy
- 10-15 years in the Pharmaceutical industry with experience in Quality Control, analytical development, regulatory, R&D and/or lifecycle management in the fields of biologics, vaccines and/or biopharmaceuticals
- Demonstrated leadership and transversal people management skills
- Knowledge of Vaccine testing and manufacturing environment
- Ability to evaluate product compliance and quality issues and make sound recommendations regarding problem resolution
- Ability to communicate complex information both orally and in writing. Ability to listen effectively
- Spoken & written English (communication, negotiation, facilitating, influencing)
- Lead, develop and coach one CQC product coordinator team accountable for GSK Vaccines analytical lifecycle product management
- Promote QC analytical product expertise within the QC product/stability coordinator team and ensure practices harmonization across the different products in terms of project management and coordination
- Accountable for the coordination of the timely redaction of the analytical and stability sections of the product quality review and the coordination of the implementation of identified improvements (CAPA’s)
- Accountable for the coordination of the timely redaction and approval (before submission) of the QC sections of regulatory files, variations and Question and Answer reports. Accountable for the analytical content of each GSK Vaccine product Regulatory file (qualitative data to sustain regulatory and authorities requirements, in due time)
- Accountable for the QC Change control management identified within Technical Team,
- Identify risks on technical feasibility and supply, timing and resources constraints and seek a remediation plan for identified risks and escalate any analytical technical and/or supply issues to the relevant body (project team, TDB, performance tower…). Consolidate a monthly progress status shared with the key stakeholders
- Coordinate the alignment of QC labs deliverables link to testing of lifecycle product improvement projects in line with Global supply chain objectives in terms of quality, time and cost. Negotiate with the laboratory heads the resources allocation and development activities to achieve the target. Consolidate and Adjust Priorities, Budget & FTE per project in cooperation with GQC team. Collect & Challenge demands for Demand & Planning (QC planning and prioritization tool) purposes
31
Manager, Quality Control Resume Examples & Samples
- Responsible for directing the activities of the Analytical Technology group including overall project management, timeline development, resource allocation, FTE and budget planning
- Responsible for development, implementing and ensuring best practices and overall company strategy for analytical methods validation, methods qualification, and approval of associated reports. Responsible for method troubleshooting and investigations of AR/OOS, method evaluation and optimization, implementation of new technologies in QC in collaboration with AD and AT groups for early stage clinical programs, support validation of analytical instruments and general GMP laboratory operation and compliance. Responsible for support of technical product compliant (TPC) investigations
- Responsible for GMP analytical testing for drug substances/drug products for new clinical programs (first manufacturing campaign and stability up to 1 year stability time point), and, as needed, support testing of new complex methods. Directly support authoring and review of regulatory filing and responses. Lead strategic initiatives that improve Biogen Idec’s business practices that support the Quality organization in accordance with company’s vision and culture
- Effective leadership and management skills
- In-depth scientific/technical expertise in analytical methodologies
- In-depth knowledge and experience in ICH and regulatory guidelines
- Statistical experimental design and data analysis
- Overall understanding of the business and units
- Mature leadership approach and understanding of their personal
32
Manager, Quality Control Resume Examples & Samples
- Oversight of QC Raw Materials program which includes but not limited to the reference standard program, calibration and maintenance, training, retention samples, Rockwell alarm monitoring systems, and specifications
- Supervise and provide guidance for troubleshooting instruments and wet chemistry assays
- Author and revise SOP’s. Write and review study protocols and final reports
- Oversee laboratory investigations related to raw materials release testing. Review and close lab investigation reports related to raw materials and components
- Coach and develop QC raw material staff and oversee the recruitment of new personnel. Provide daily supervision of the raw materials analysts, provide regular feedback, and conduct performance reviews
- Identify and implement clear objectives for the laboratory personnel, including the management of a diversity of projects in the QC area associated with the multiple product platforms, e.g., sterile injectables, solid oral dose, and therapeutic proteins
- Oversee the trending of the release data and present to senior management the metrics for the key performance indicators (KPIs)
- Ability to lead and facilitate a team atmosphere
- Experience with cGMP, ICH Guidelines and FDA Regulations (21CFR 210, 211)
- Knowledge and skills required include the specific understanding of the theory and practice of HPLC, capillary GC, and specialized analytical techniques relevant to the laboratory (such as GPC, particle size analysis, DSC, Karl Fisher titration, FTIR and wet chemistry)
- The ability to operate chromatographic data acquisition and analysis software and develop data analysis and reporting approaches
- The application of statistical concepts to the calibration of assays and interpretation of results
- Knowledge of LIMS, SAP, Empower and trackwise is desired
- Knowledge of AQL/inspections of vials
- Experience dealing with regulatory agencies during audits
33
General Manager, Quality Control Resume Examples & Samples
- Raising the profile of Quality and embedding quality as a core value and key priority, across all functions of the business
- Ensure that quality systems are OMS conforming at appropriate levels as defined by SPU
- Ensuring quality control is fully compliant contemporary guidelines, Global and Regional QA/QC standards and helping towards the development of best in class quality management processes for India
- Manage formulations for India plants in fusion and in ERP systems ensuring formulation integrity
- Ensuring SPU Quality & Compliance programmes are fully and effectively deployed across the India business
- Building functional capability in quality control across all manufacturing and logistics operations within India (including third parties)
- Supporting the development and deployment of appropriate Quality tools & systems
- Leading / assisting in Quality Incident investigations, as well as setting up monitoring systems to track and report incidents, set targets and ensure robust implementation of corrective and preventive actions
- Collaborating with Quality colleagues in other parts of the region and globally, to build quality standards/initiatives which drive improved performance
- Engage stakeholders of supply chain and businesses as appropriate to drive quality initiatives and get feedback from the markets
- Engage and collaborate with plant and GLT and make sure that new standards and regular audits are being done, standards are implemented and actions are implemented on time
- Participate in customer/dealer/distributor visits , act on feedbacks to improve the quality of the product delivered to them
- Drive quality related projects for Castrol India Business, Plants and third parties
- Graduate degree with Chemistry or Engineering Background and experienced in implementing quality systems. Preferable to have experience of having handled Country role and demonstrated ability in influencing change management at multiple sites
- B Education - Degree in chemistry or Engineering required and Post-Graduation would be advantage. Track record of leadership and change management
- Experience and familiarity with Supply Chain Operations or Technology
- Experience and familiarity with Quality Management Processes and Systems
- Effective leadership and influencing skills to deliver the accountabilities in this role, across the manufacturing assets and third party vendors in the countries
- Functional expertise to acquire and embed best practise in quality management processes and systems
- Ability to collaborate with peer group and other stakeholders is essential - to build strong engagement and alignment, not only within India& ME, but also across wider supply chain and technology organisation
- Performance Bias: Extremely pro-active to manage wide range of activities in complex non routine context. Must demonstrate Performance Management, dealing with conflicting priorities and demands effectively
- Wise Decisions: Systematically breaks down complex problems to solve them. Must have good judgment and be able to make sound decisions under pressure. Proven experience in driving Productivity & Investment decisions
- Partnership and Teamwork: Actively support Team activities and facilitates building team effectiveness between department teams in the plant. Seeks out sources of knowledge and best practices for team development for building a learning culture. Must demonstrate good communication and personal effectiveness. Actively demonstrate passion towards team building & development of team members
- Leadership: Proactively Lead people, Ability to lead teams even where there is no line authority. Must have demonstrated Networking & good influencing skills. Demonstrate significant personal autonomy and team leader authority in designated areas. Give specific coaching to others to assist their performance
- Business awareness- Demonstrates understanding of internal and external customer needs and exceeds expectations & High degree of Customer responsiveness
- Creativity & Innovative: Should be open to new ideas and constantly strive to look for and adopt newer ways of doing things in a safe and efficient manner
34
Manager / Senior Manager, Quality Control Resume Examples & Samples
- Responsible for managing QC Site Planners and QC Forecasting and Metrics
- Responsible for building, implementing, and maintaining the laboratory scheduling software (SmartQC). Responsible administrator of SmartQC globally which will require vendor interface, troubleshooting the software, adding new tests and analysts to the system, train new analysts, etc
- Responsible for level loading across QC labs and collaborating with Contract Lab group when use of contract labs is needed to balance workload
- Collaborate with Manufacturing, Global Operations Planning, and Stability to provide short term and long term testing forecasts to QC testing labs and Quality leadership team
- Collaborate with Stability to maintain a stability workload model to project resource needs for future stability testing
- Collaborate with QC Site Planners to balance workload globally
- Provide Global QC metrics reporting
- Collaborate with QC laboratories, site planners, and stability scientists to ensure stability testing metrics are consistently met across sites
- Strong Excel skills, Strong analytical / critical thinking, communication and interpersonal skills
- Experience in the biotech/pharmaceutical organization in stability or testing lab operations
- Proficiency with LIMS, Oracle, Trackwise
- Strong communication and presentation skills, both verbal and written, including ability to synthesize information for senior management
- Extraordinary attention to detail and ability to conduct and report analytic outputs with high level of precision / without errors is essential
- Sound knowledge of cGMPs and equivalent regulations
- Familiarity with scheduling software (SmartQC)
35
Manager, Quality Control Resume Examples & Samples
- Ensures Quality Control systems are compliant with corporate and site procedures, as well as industry standards
- Supports development of novel QC analytical methods. Works in conjunction with other departments to develop, qualify, and transfer QC analytical methods
- Ensures maintenance of QC equipment – qualification, calibration and maintenance
- Manages contractors as required
- Thorough knowledge of cGMP regulations related to Quality Control required. Phase III / Commercial cGMP regulatory knowledge preferred
36
Senior Manager, Quality Control Dispensing Resume Examples & Samples
- The first goal for employees is safety. The Sr. Manager, QC-Dispensing is responsible for ensuring safety messages are implemented and are fostered and sustained throughout the facility
- Ensure the regional QC teams successfully implement and execute quality controls, inspections, audits, and initiatives to the applicable cGMP/GDP standards consistently with documented QC records in accordance with specified timelines. Continually seek ways to improve the Quality Culture of the facility and specifically of QC, the quality of work performed by the QC functions, and to improve efficiencies throughout QC in regards to all tasks, but especially inspections, audits, and reporting tasks
- Ensure the regional QC teams successfully and consistently perform activities to meet specified timelines. Ensure the retention and reporting process is robust and continually seek ways to improve the process both in terms of effort expended, timeliness of completion, and quality of work performed
- Ensure the resources utilized throughout the QC organizations are appropriate for the tasks assigned, and ensure the cGMP requirement for appropriate staffing levels in all aspects of QC are continually met while simultaneously supporting efficiency improvements that reduce the amount of work/time expended on specific tasks
- Ensure the timely review of inspections and records, SOPs, investigations, corrective actions, and change controls
- Conduct strategic organization planning for the group for a 3 - 5 year look forward
- Coaching and mentoring of direct reports will be required on a regular basis
- Responsible for leading a regional QC Organization and managing & coordinating the safety and quality activities of the regional Quality Control management team engaged in the sampling, testing, and inspecting products, in-process inspection samples, raw materials in order to ensure compliance with quality standards, production, and delivery schedules end-to-end from order entry to product shipment and delivery
- Manages professionals within Quality Control. Hires, coaches, and develops employees within the Quality Control management team and ensures their continued career progression through advocacy and provision of learning opportunities. Provides feedback and coaching, provides opportunities for growth and takes necessary disciplinary actions for his/her direct reports. Ensures the QC management team does the same for their direct reports. Continues to assess the organization and best utilizes resources
- Coordinates/drives continuous improvement efforts focused on lean/waste, supply chain, and inventory initiatives within functional area and assigns resources as appropriate
- Collaborates cross-functionally with all functions within the organization
- Ensures adequate training and development opportunities (skills-based, cGMP / GDP, and Safety) of analysts within department, to support commercial production and Pharmaceutical Development needs through highly competent staff
- Reviews departmental documentation (e.g., Standard Operating Procedures). Participates in revisions, providing input, as necessary. Participates in State, Federal, and other Regulatory Authority Inspections and Customer Audits as needed for cGMP, policy, and procedure, and as an SME
- Provide leadership to the Quality Engineers/Specialist/Technicians at the various fulfillment sites (regional) to execute on the day-to-day inspections and floor controls
- Provide consistency with defined processes and practices across multiple sites
- Partner with fulfillment to identify, prioritize and execute on improvements to the back-end dispensing process to increase productivity and reduce Cost of Poor Quality (CoPQ)
- Advocate for the VOC (Voice of the Customer) ensuring customer requirements are realized throughout the life cycle of the products and processes used within the facility from development through product realization and support while in service
- Possess the ability to make decisions that always protect safety of the products and services provided by the business
- Ensure procedures for maintaining high standards of quality, reliability and safety are executed
- Organize and promote company-wide improvement efforts
- Be a business partner to Operations ensuring the Quality Management team drives leadership in both compliance systems and management as well as proactively working with the leadership at each site to drive continuous improvement to ensure on time delivery and quality
- Establish meaningful goals and metrics for groups in conjunction with the Site Head of Quality, and manage the performance to those goals
- Manage and operate effectively in a highly-matrixed organization while fully supporting cross -functional initiatives in the area of quality
- 10+ years of quality experience
- 3+ years of management of groups of 10 or larger, and a minimum of 5 years of experience in managing small regional QC groups
- 7+ years of experience in a GMP environment,
- 7+ years of experience in Quality Control of biopharmaceuticals, medical device, and or aerospace product
- Knowledge with processes involved in manufacturing and distribution: QA, QC, validation, and process development
- Customer-first mindset with the drive to understand internal and external customer expectations and requirements
- Capability to assimilate information and influence timely decisions that impact the functional areas
- Experience implementing various quality standards (ISO, cGMP, etc.)
37
Manager, Quality Control Resume Examples & Samples
- Develops appropriate reporting and subcontract management processes for projects
- Interacts with all levels of the organization
- Further education, A-Level minimum or equivalent and/or ability to demonstrate competence to successfully carry out the requirements of the role
- Experience of negotiating claims and variations to contract with subcontractors
- A strategic individual with good judgment and strong professional and ethical standards
38
Senior Manager, Quality Control Resume Examples & Samples
- Manage the transfer and validation of analytical methods from Analytical Development to QC as well as the transfer and validation of methods to OTL or other sites. Validation of methods will be phase appropriate
- Establish specifications and testing process of raw materials and cell therapy products
- Responsible for OOS, lab and protocol deviations, Implement corrective action plans when necessary. Provide updates at daily and weekly meetings
- Assist in the preparation of dossiers and data packages for interactions between Kite and Regulatory agencies. Interact with agents from Regulatory agencies and participate in Pre-Approval Inspections
- Responsible for QC’s training. Monitor the GMP systems currently in place to ensure compliance with documented policies
- Responsible for stability related testing and program
39
Manager, Quality Control Operations Resume Examples & Samples
- Manage laboratory resources (employees, instrumentation, computer systems) while collaborating with customers to ensure alignment of testing priorities with the business objectives
- Oversee testing activities in several of the following functions but not limited to: finished products testing, stability testing, raw material testing, component testing, cleaning vertification testing, validation testing, investigational testing, in-process testing, etc. Perform troubleshooting in functional areas and serving as subject matter expert. Lead, guide, and mentor analysts through the completion of daily activities
- Building a sustainable workforce by recruiting the best and brightest talent in industry. Providing guidance in the creation of individual development plans for the staff
- Lead and approve laboratory investigations making sure root causes are properly identified in order assign effective correction actions are implemented. Perform trend analysis and quality impact assesments
- Foster a culture of continuous improvement through active listening and leading. Lead periodic evaluations of analytical testing procedures, standard operating procedures, and best practices to ensure a cutting edge business model is deployed
- Perform the following functions as needed: write protocols, write reports, audit laboratory data, release laboratory data, scheduling analysts weekly schedules
- Maintain a safe work environment that is in a constant state of inspection readiness
- Minimum of a Bachelor's degree in Chemistry or similar science discipline (or equivalent) and 2-4 years of experience. A minimum of 8-10 years of pharmaceutical experience in combination with managerial experience preferred. However, a combination of experience and/or education will be taken into consideration
- Must possess knowledge of SOPs, Mylan Laboratory Procedures, USP regulations, Analytical Testing Techniques, cGMP, and OSHA regulations/procedures for disposal of organic waste and procedures for the safe handling of chemicals
- Must be proficient in several functions in a Quality Control analytical chemistry environment including but not limited to the following: finished products testing, stability testing, raw material testing, component testing, cleaning vertification, validation testing, investigational testing, in-process testing, etc. Must be proficient in several of the following analytical instrumentation including but not limited to the following: HPLC, UPLC, GC, IR, UV, kF, pH, Dissolution, TPW, Multidose, various wet chemistry instrumentation/testing, etc. Must have expertise in several of the following software application but not limited to the following: Empower I, II, or III, Labware LIMS, SAP, Trackwise, Omni, Chemstation, etc. Must have analytical investigation experience conducting OOS/OOT laboratory investigations
- Position functions semi-autonomously. Position directly supervises employees. Carry out supervisory responsibilities in accordance with the organization's policies and applicable laws. Responsibilities may include interviewing, hiring, and training employees; planning, assigning, and directing work; appraising performance; rewarding and disciplining employees; addressing complaints and resolving problems. Must be a leader, mentor, and self-motivated to develop a high performing team with the central focus on meeting business initiatives and being a servant leader
- Ability to read and interpret complex business and/or technical documents. Ability to write comprehensive reports and detailed business correspondence. Ability to work with groups of people such as other departments and communicate known concepts. Ability to present to a group of departments
- Ability to solve problems with complex variables through non-standardized solutions that require independent judgment and analysis. Ability to draw inferences and use deductive reasoning with no prescribed procedures to solve complex problems. Ability to solve equations, apply technical mathematical concepts, and perform complex computations
- Normal office situation. Regular exposure to chemicals, solvents, fumes and/or gases.Typically sitting at a desk or table. Intermittently sitting, standing or stooping. May be required to stand; walk; stoop; bend; kneel; and climb steps. May require use of hands and use of arms. Sedentary lifting requirements
40
Senior Manager, Quality Control Resume Examples & Samples
- Lead global teams including QC technology transfer teams
- Orchestrate QC release and stability testing of GMP drug substances and drug product materials associated with global R&D and commercial programs, including development and implementation of stability programs and collaborative interactions with CMO/CTOs for scheduling and performance of testing
- Review and analyze GMP test results, prepare interim and final testing reports, develop investigation protocols and reports, prepare summaries and other documents for communication with regulatory agencies. Present findings both internally and externally, including regulatory agencies
- Lead test result investigations and test method optimizations, manage GMP test method life cycle, and design strategic plan for process and product development
- Assess method and program for compliance with GMP requirements, guidance documents, and determine critical quality attributes. Implement strategies for adding new GMP test methods and verify suitability for company materials
- Survey global regulatory guidance and trends (e.g. ICH Q2R1), perform gap analyses relative to VBD current state, and formulate/implement improvement initiatives
- Minimum 10 years experience in Quality or Regulatory compliance (FDA, EMA or other) within the pharmaceutical, biologics or vaccine industry, with specific focus on developing and managing global GMP Quality Systems
- Minimum 7 years experience in GMP QA and/or QC
- Experience leading and managing complex and matrix project teams and processes in a virtual organization (e.g. change control, CAPA, deviations, product complaints, management review)
- Direct experience developing and assessing metrics and data, analyzing for trends, and reporting to global, senior-level management on GMP State of Compliance (Management Review)
- Regulatory Knowledge – in-depth understanding of global regulations governing the US and international pharmaceutical industries
- Proven leadership, team building skills and strategic problem-solving ability. Ability to manage and lead others through change. Demonstrated ability at managing matrix teams, influencing outcomes and key project decisions
- Proven ability to communicate and collaborate effectively with senior management. Experience interacting with external collaborators with ability to build strong relationships
- Knowledge of risk management, project reporting, and general project management experience/expertise required
- Strong interpersonal skills particularly motivational, negotiation, listening, judgment, and conflict management skills, demonstrated by ability to lead teams in a complex, matrixed and global environment
- Excellent organization, verbal and written communication skills to explain project goals and inspire support
- Ability to work well with cross-functional teams to accomplish objectives. Ability to work effectively in a fast paced, rapidly changing technology environment, and to work on multiple work streams and projects simultaneously
- Demonstrated analytical capabilities with the ability to analyze a wide variety of information and data to make management decisions regarding potential risks associated with regulatory compliance
- Demonstrated proficiency in MS Office applications required; proficiency in Quality Systems Databases such as TrackWise or similar systems highly desirable
- Proactiveness – ability to anticipate potential problems and risks related to quality system expectations and regulatory compliance, formulate action plans, and implement solutions
- Must have a fundamental understanding of the drug development process, scientific
- Methods and thought processes
41
Senior Manager Quality Control Resume Examples & Samples
- Excellent understanding of the framework within which a pharmaceutical product has to be developed and maintained in compliance with GMP’s and regulatory requirements
- Is accountable for preparation of advisory or governing bodies such as TLCB, Specification committee, TLCT,…bringing the analytical expertise to multi-disciplinary Technical or Governance bodies
- Act as key player during Regulatory inspection and meetings
- Has a full understanding of the overall strategy and roadmap on LC products under his/her responsibility
- Accountable for the coordination of critical product deviations, in cooperation with the key members of the multi-disciplinary Technical teams, to guarantee the continuity of supply and are in accordance with the current regulations
- Identify technical and supply risks, timing and resources constraints and seek a remediation plan for identified risks and escalate any analytical technical and/or supply issues to the relevant body (project team, TDB, performance tower…). Consolidate a monthly progress status shared with the key stakeholders
42
Manager, Quality Control Resume Examples & Samples
- Sets daily, weekly, and monthly team/individual goals required to meet corporate goals, demand, and regulatory requirements
- Develops and tracks applicable metrics
- Inspires the team to understand, meet, and exceed their personal and team goals, ensuring that everyone has the proper training and tools to do so
- Holds team accountable for results and takes quick, innovative action to recover when performance falls below target
- Selects, trains, and develops highly qualified and motivated inspectors to execute quality plans (QIRs) and competently operate various kinds of manual, automatic, and advanced inspection measurement equipment
- Eliminates waste in the department through deployment of lean manufacturing techniques and optimizes existing inspection processes through six sigma problem solving tools
- Defines, documents, and establishes quality procedures necessary for successful and compliant operation of the department
- Controls non-conforming materials and executes corrective and preventive action (CAPA) on related QC processes
- Identifies and deploys process improvements necessary to deliver year over year budgetary and product innovation targets
- Partners with Quality Engineering to qualify and validate inspection equipment and processes
- Confidently and successfully communicates performance and initiatives of the department to cross-functional team members at every level of the organization
- Personally grows through self-development initiatives such as cutting edge seminars or staying abreast of immerging trends in the industry
- Maintains confidentiality of information provided by company and shareowners
- Develops and maintains collaborative working relationship with other managers
- Partners with others to drive engagement throughout all levels of the facility
- Operates as a self-starter who doesn’t wait to be told what to do
- Demonstrates a willingness to roll up your sleeves and get your hands dirty
- Has an "Attitude of Gratitude"
- Embraces and promotes the unique NuVa culture
- Bachelor's degree in an engineering, technical, or business discipline
- 7 years of experience in an automotive, aerospace, or medical device environment in a Quality Inspection or Engineering capacity
- 3-5 years of experience in management
- 2 years of experience in an FDA regulated environment
- Demonstrated experience with the commonly used quality tools such as histograms, Pareto charts, and process flow charts
- Demonstrated experience with problem solving and continuous improvement tools such as DMAIC, PDCA, and Kaizen
- Proficient and accurate in Microsoft Office applications such as Excel and Access
43
Manager, Quality Control Resume Examples & Samples
- Review data from batch release and stability programs conducted at CMO
- Along with CMO, examines current analytical methods in order to investigate, create and potentially develop new and improved methods and technologies which can benefit ongoing programs
- Oversee, with Amicus and vendor Quality Assurance, the disposition of out-of-specification (OOS) and out-of-trend (OOT) investigations,with particular emphasis on the supporting analytical testing
- Evaluate data for trends indicative of product performance, method performance, or analyst performance
- Serve on departmental, interdepartmental, and project teams
- Adhere to all relevant compliance regulations
- Advanced understanding biopharmaceutical analytical testing, with specific emphasis on HPLC methods (including SEC, released glycans, etc), IC methods (including monosaccharides), plate based assays (included ELISA/HCP, enzymatic activity,and receptor binding)
- Problem-solving and troubleshooting skills
- Strong capabilities in experimental design and execution and data interpretation
- Knowledge of protein biochemical and biophysical techniques such as enzyme activity assays, receptor binding assays, cell based bioassays, ELISA, Western blot, qPCR, iCEF, CD, DSC, DLS
- Experience working with CMO’s and CRO’s for methods transfer, method optimization, and data and report review
- Knowledge of cGLP/cGMP, FDA, EMA, ICH guidance’s and industry standards for analytical development and characterization of proteins
- Familiarity with the USP, EP and other compendia
- Skills in statistics and statistical analyses of data
44
Associate Manager, Quality Control, BIW Resume Examples & Samples
- Develop & maintain Standardized Work Instructions used by the QC inspectors
- Support the development of Process Failure Modes Effects Analysis (PFMEA) to identify critical risks in the production processes with the Quality Engineers
- Support of control plans to assure critical features are controlled through the production process
- Manage production associates, Team Leaders and Supervisors
- Develop the team structures used in the Tesla Factory
- Ensure quality standards are being met throughout the entire production process and support no defects from leaving a station or team area
- Coordinates scheduled audits with cross-functional staff
- Acts as primary point of contact during department audits
- Monitor our manufacturing processes, quality data systems, first pass yield, scrap and continuous improvement opportunities in order to implement the best practices in our operation on daily basis
45
Operations Manager, Quality Control Resume Examples & Samples
- 5+ years of experience within cGMP/QC testing laboratory management, preferably with 3+ years of external vendor management experience
- Bachelors or Master’s degree in Chemistry, Biology or related science
- Direct experience with analytical techniques and methodologies including Atomic Absorption (AA), HPLC, GC/LC, TOC, FTIR, microbiological and/or general assays
- Proficient knowledge in current regulations and guidance documents including cGMP, ICH, FDA, and EMA requirements
- Ability to work in a virtual environment with external vendors and collaborators
- Excellent communication and written skills to successfully partner with collaborators and external vendors
- Previous experience with data trending and statistical programs (JMP, MiniTab, Excel, etc) a plus
46
Manager, Quality Control Resume Examples & Samples
- Expense costs for time and material as required
- Manage weekly timesheet entry
- 3 - 5 years experience implementing contemporary process improvement methodologies in an Operations environment,
- Experience with quality management
- Lean Six Sigma experiences in a transactional environment and/or service industry a plus
- Excellent PC skills within a Microsoft Office environment using Microsoft Excel and Microsoft Access. Experience with Minitab
- Demonstrated analytical skills with understanding of basic statistics. Strong project management and organizational skills. Strong focus on customer service. Excellent verbal and written communication skills. Ability to manage multiple timelines and deadlines
- 10+ year’s experience managing complex projects through lifecycle
47
Assistant Manager Quality Control Resume Examples & Samples
- 1 year experience in food safety or related field
- 1 year experience using basic Microsoft Office functionality (for example, Word, Excel, Outlook)
- 1 year fruit ripening experience
- 4 years experience in agricultural quality control, agronomy, food retail management, or related field
48
Manager, Quality Control Resume Examples & Samples
- Proven experience on QMS implementation (ISO/TS 16949, IATF 16949, VDA 6.3)
- Proven knowledge of Automotive Regulations (IATF, AIAG, etc.)
- Able to manage multidisciplinary teams
- Presentation skills for Sr Mgmt levels
- Hands on experience with Internal, External, and Third Party audits
- Develops complex analysis of processes to identify systemic problems and solutions
- Skills to evaluate processes effectiveness, risks and opportunities
- Hands on knowledge on customer requirements and portals
49
Senior Manager, Quality Control Resume Examples & Samples
- Serves a as Quality interface for manufacturing in Rajecko, Czech Republic and Seoul, South Korea
- Assumes Contract Manufacturing responsibility for SFO India, TE Connectivity New Zealand, wizMart China and any other Contract Manufacturers of scope
- Engage with Quality Director relative to Matamoros / Simplex Quality initiatives
- Working knowledge and understanding of ISO9001:2015
- New product introduction Quality background and proven experience driving Quality through a stage gate process
- In-depth knowledge of electronic printed circuit assemblies as well as final assemblies
- Proven problem solving and risk analysis tools
- Experience working with fire protection panels and associated peripherals a plus
50
Manager, Quality Control Stock Yards Resume Examples & Samples
- Food safety training, sanitation (SSOP & GMP), USDA quality troubleshooting and QA process improving skills preferred
- Perishable industry background/experience with food safety/quality knowledge in a perishable production environment required
- Experience with a HACCP plan design, measurement, documentation & training required. Formal HACCP training/certification preferred
- Excellent organizational skills and ability to prioritize required
- Critical thinking. Analytical skills. Written and verbal communication skills
- HACCP. GFSI
- Strong interpersonal skills required, including the ability to relate and positively influence employees & third parties at all organizational levels
51
Senior. / Manager, Quality Control Bioassay Resume Examples & Samples
- Implements in-house testing capabilities in the QC laboratory, including bioassay, qPCR, cell-based assays as required
- Manages laboratory personnel and oversees their selection, performance management, mentoring, and career development
- Assists in development of appropriate Standard Operating Procedures and training of personnel to ensure cGMP compliance
- Manages laboratory investigations, change controls, and CAPAs for relevant QC operations
- Contributes to budget and resource allocation
- Interacts with Manufacturing, Quality Assurance, Regulatory Affairs and other Departments to
- BS in a relevant scientific discipline with a minimum of 8-10 years Quality Control experience (minimum of 2-3 years management/supervisory experience) in a cGMP organization with a focus in Bioassay
- Familiarity with electronic databases (e.g. LIMS, EDMS) preferred
- Experience with statistical data analysis
- Excellent troubleshooting and ability to communicate issues in a scientifically sound and understandable way
- Ability to collaborate effectively in a dynamic, cross-functional matrix environment
52
Laboratory Manager Quality Control Resume Examples & Samples
- Responsible for the activities involved in conducting testing of validation, raw material, process intermediates and finished product samples, and is knowledgeable in the analytical techniques for the laboratory(s) they support
- Responsible for the supervision of hourly employees performing testing. Includes scheduling of work assignments based on priorities, being knowledgeable of cGMP, administration of local bargaining agreement, company personnel policies, OSHA requirements and company safety procedures. Promotes teamwork and open communication
- Act as a resource and liaison between technicians and support groups to represent the needs of the laboratory
- Responsible for performing lab work accurately and in a timely fashion. Responsible for critically evaluating data generated and recommending acceptance or rejection of samples
- Responsible for updating SOPs, Process Specific Training Modules, Test Methods, etc
- Required to facilitate relationship with Quality Assurance group
- Initiate and follow-up on equipment repairs and follow-up on facility work orders for laboratory modifications
- Represent the laboratory in various Safety and Compliance initiatives, including safety inspections
- Maintain records, develop productivity improvement plans, maintain adequate inventory of supplies, training records, tracking functions such as corrective actions, special projects, etc
- Supports deviation investigations, out-of-trend results, and test failures associated with product manufacture, release testing, and stability testing
- Responsible to improve laboratory quality and/or efficiency of assays, support regulatory inspections and train other Laboratory Operations managers and/or technicians
- Minimum of (3) years’ post-degree laboratory, manufacturing, or quality control experience
- Working knowledge of cGMPs
- Deep familiarity of laboratory methods and common instrument requirements for a laboratory
- Must possess strong communication, project management and problem-solving skills
- Demonstrated ability or aptitude for continuous learning and analytical problem solving
- Customer service mentality and process improvement experience
- MS in a science-related discipline
53
Manager, Quality Control Analytics Resume Examples & Samples
- Proficient use of computer software, including Microsoft Office Suite (excel, word)
- Proficient in HPLC method development and method validation with extensive experience with multiple other analytical techniques and analytical equipment
- Prior experience and knowledge in FDA GMPs (21 CFR, 211, 820, and/or 600); ISO 9001 and 13485
54
Associate Manager, Quality Control Resume Examples & Samples
- Supervise laboratory work of assigned employees to ensure testing of laboratory samples to meets commitments specific to assigned area. Responsible for general organization of the laboratory and personnel
- Coordinate with lab personnel and project management to schedule assignments and projects
- Serve as group and/or project leader. Mentor assigned employees. Manage and motivate technical and personnel career growth of personnel
- Minimum of a Bachelor's degree (or equivalent) in Chemistry or similar science discipline and 2-4 years of experience. However, a combination of experience and/or education will be taken into consideration
- Must possess excellent written and verbal communication skills, interpersonal skills, management skills, strong work ethic, consensus gathering skills, organizational skills, and a working knowledge of Microsoft Office including Word and Excel. Must be accurate, detailed oriented, team focused, and possess the ability to multi-task and work in a fast paced, high output environment
- Ability to add, subtract, multiply, and divide
- Standard laboratory environment. Regular exposure to chemicals, solvents, fumes and/or gases. May be required to stand; walk; stoop; bend; kneel; and climb steps. May require use of hands and use of arms. May be required to wear personal protective equipment including but not limited to: respiratory protection, safety glasses, hearing protection, safety shoes and protective clothing. Light lifting requirements
55
Manager, Quality Control Operations Resume Examples & Samples
- You are a thought leader, influencer and relationship builder
- You are a critical thinker
- You love checks and balances
- You have a keen eye for detail
- You treat others with dignity and respect while driving business deliverables
- You’ve got exceptional problem solving skills
- You believe in coaching and developing your team
- Process Improvement is your middle name and quality is your game
- You go above and beyond in your role because you want to, not because you have to
- 3 years of management/supervisory responsibility
- 3 years of insurance related experience and/or similar activity outside the organization
- 3 years knowledge of auditing responsibilities, insurance systems and/or operations processes with a strong knowledge of company products and services
- Six Sigma certification or experience in a process improvement environment
- Professional Certification (Compliance, Audit, Project Management)
- Able to plan and implement an Audit
- Ability to influence change and lead team to successful implementation of process or system changes
56
Senior Manager, Quality Control Resume Examples & Samples
- Generate, standardize and continuously improve Quality metrics across all supported businesses, Drive us of Salesforce.com and other automation to increase amount and validity of data collected from internal and external customers
- Ensure completion of Quality research of all reported outbound shipment discrepancies. Drive RCA methodology and subsequent process improvements
- Develop QMS regime to ensure continued and consistent Quality focus on the Voice of the Customer
- Deliver timely Quality support to Distribution to achieve performance targets, including inbound, internal and external audits, product rework and Quality Alert response and resolution
- Review and enhance the new product introduction process
- Engage all Distribution Center associates in Quality through promoting quality initiatives, addressing associates Quality needs and communicating Quality achievements
- Drive inbound supplier performance to L&D requirements, including conducting supplier audits, providing supplier scores and resolve product processing issues faced by Operations and Inventory
- Manage Quality cost measures through staffing in adherence to budget and allocating costs by projects and business
- Drive and address defect problems, product issues, supplier issues, quality working factories and communication with customers. Quality engineering position /risk manager/corrective actions
- Strong background in supply chain management and logistics and distribution operations
- A Bachelor's degree in Engineering or Management
- At least 7 years related experience with Quality Control Management is desired
- Requires skills in leadership organization and communication
- Demonstrated ability to develop and delver cross functional and optimized supply chain solutions within a matrix structure
- Proven track record in managing multiple teams across multiple locations. Leads functional teams and various levels of managers
- Must be able to handle stress caused in meeting deadlines with tight scheduling requirements as well as be able to shift priorities easily
- Must be familiar with Microsoft Office applications including Excel and Word
- 25% travel
57
Manager, Quality Control Resume Examples & Samples
- Accountable for GMP compliant laboratory operations according to EU GMP (Part 1 and 2), 21CFR part 210, 211, 820, 11 and other applicable GMP guidelines
- Responsible for management of QC Sample Control and Stability including planning and prioritization of Sample Control and Stability Activities
- Responsible for tracking/trending the test performance in QC lab INT
- Support the use of the new metrics and planning tool (Smart QC)
- Participate in GMP audit and inspections on Sample Control and Stability topics
- Accountable for the operation, optimization and GMP compliance of the INT QC Sample Control function
- Manage the personnel of QC Sample Control and Stability and ensure training and development
- Coordinate, optimize and harmonize global sample control activities
- 5 years of practical laboratory experience
- 5 years of experience from a GMP environment
- 5 years of experience from QC, Aseptic filling operations, API manufacturing or QA
- Good communication skills in English and Danish
- Previous experience as Supervisor / Manager