Quality Manager Resume Samples
4.7
(85 votes) for
Quality Manager Resume Samples
The Guide To Resume Tailoring
Guide the recruiter to the conclusion that you are the best candidate for the quality manager job. It’s actually very simple. Tailor your resume by picking relevant responsibilities from the examples below and then add your accomplishments. This way, you can position yourself in the best way to get hired.
Craft your perfect resume by picking job responsibilities written by professional recruiters
Pick from the thousands of curated job responsibilities used by the leading companies
Tailor your resume & cover letter with wording that best fits for each job you apply
Resume Builder
Create a Resume in Minutes with Professional Resume Templates
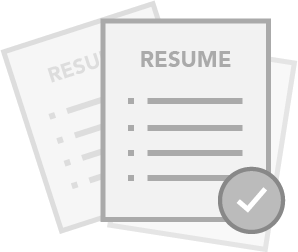
CHOOSE THE BEST TEMPLATE
- Choose from 15 Leading Templates. No need to think about design details.
USE PRE-WRITTEN BULLET POINTS
- Select from thousands of pre-written bullet points.
SAVE YOUR DOCUMENTS IN PDF FILES
- Instantly download in PDF format or share a custom link.
GP
G Pouros
Garrett
Pouros
406 Cartwright Forks
San Francisco
CA
+1 (555) 869 2572
406 Cartwright Forks
San Francisco
CA
Phone
p
+1 (555) 869 2572
Experience
Experience
Houston, TX
Quality Manager
Houston, TX
Casper and Sons
Houston, TX
Quality Manager
- Working knowledge of ISO 9001 an ISO14001
- The Quality Systems Manager is responsible for the implementation and execution of the Kraft Heinz Quality Chain Management System at the plant level, including distribution and local storage sites. It controls all products and processes in the plant, through strict adherence to policies, specifications, and standards. It utilizes methods, tools, and procedures to deliver zero defects from incoming raw materials to outgoing finished goods in a food safe environment. The position ensures that facility personnel are properly resourced and trained to efficiently and effectively execute their quality responsibilities. It leads Continuous Improvement of conformance quality and best in class cost of quality by utilizing L6S tools. The position has significant managerial responsibilities, including hiring and developing talent as well as budget management
- Acting as an advisor or consultant to senior management
- Implementing the new National Quality Program in all Transportation offices across Canada including providing the training associated with its implementation
- Ensure that the operations, processes and procedures that affect products quality and/or integrity comply with ISO 9001, ISO 13485 and 21 CFR 820 including but not limited to: customer complaints, quality metrics, approval and release of finished products, incoming inspection of raw materials, management reviews, internal audit program, host external regulatory, corporate, and customer audits, quality holds, customer notifications, market corrections or withdrawals, non-conformances and CAPA system, quality support for Design Control and New Product Introduction, QA Validation and equipment lifecycle support, Change Control, Customer requests and interactions (C of As, Quality Surveys, Quality Agreements)
- Liaising and regularly meeting with Buildings Quality Network staff; assisting in periodically updating quality procedures and policies
- Manage and drive bottom line improvements in Quality performance in line with business objectives. - Cost of Poor Quality (% COGS), Warranty (ICQ and Standard Warranties for new completes and parts), Internal Failures (scrap, reworks), Supplier Failures, (rework, return to Vendor and backcharge). This is accomplished through development of AOP for the site in coordination with other Plant Staff Managers deploying quality culture utilizing strategic and innovative approaches
present
Phoenix, AZ
Quality Manager
Phoenix, AZ
Shields Group
present
Phoenix, AZ
Quality Manager
present
- Perform quality assurance & in process audits on the installation of Ericsson or customer supplied products & services in the Outside Plant (OSP) including: a) traffic control, excavation & safety, b) site restoration, c) aerial fiber, d) installation of passive optical components (splitter cases, splice cases, vaults, flower pots, duct, fiber), e) fiber splice and testing and f) hut installation
- -Provides support to functional leadership by gathering and analyzing Quality information, programs, and initiatives. Responsible for monitoring and analyzing processes and/or product outputs, identifying systemic problems and opportunity areas, providing data and direction to the site(s), and work with team members to drive process improvements to work toward zero-defect quality performance
- Contribution/Leadership - Provides ongoing technical /operational guidance to lead professional work teams, conducts special projects, or manages department(s) (national or international). Understand department/ functional mission and vision. Defines and decides objectives within specified business concept or project and may have responsibility for tools and assigned resources. Utilizes expertise to directly influence people outside department or function. Sometimes no precedent exists
- Develops and implements a quality system, ensuring both compliance to high standards and a quality focused workforce, including the design and management of basic policies, programs, standards and methodologies for the assurance of quality production. Sets standards of performance for quality and measures progress. Analyzes progress and takes corrective action. Implements Lean Six Sigma processes wherever possible
- Directs and coordinates a team of Quality & Production Leaders to achieve continuous auditing of the quality levels in the plant. The management of those departmental employees includes training, evaluation, discipline, and resolution of personnel grievances. Enforces rules, regulations, and policies to ensure a safe, firm, fair, and consistent work place environment
- Supporting activities to attract and develop quality talent through hands-on recruiting, hosting information-sharing sessions, and mentoring of early talent
- Working with senior leaders across the business to implement and embed the company’s assurance model
Education
Education
Bachelor’s Degree in Engineering
Bachelor’s Degree in Engineering
University of California, San Diego
Bachelor’s Degree in Engineering
Skills
Skills
- Basic Quality knowledge in Quality tools, methods, systems
- ASQ recognition as a Certified Quality Manager or Certified Quality Engineer is highly desirable
- Certified Quality Manager (CQM) or Certified Quality Auditor certification from ASQ highly desired or ability to obtain within one year
- Excellent working knowledge of Quality and Environmental Management Systems. Registered Auditor qualification desirable
- Basic quality system knowledge (Document Controls, process audits, SPC, Sampling plans)
- Able to provide excellent leadership example, able to coach, motivate and build self-confidence within work
- Knowledge of Test Automation tools and standards highly desirable
- Drive skill enablement cross pollination of knowledge and help to build assets and strive continuously to build strong collaborative agile teams
- Advanced knowledge of quality related tools including, but not limited to SPC, GD&T, DFMEA, DOE, ISO, Quality Systems and measurement tools
- Ability to lead detailed current state assessments of LOB Quality programs and determine improvement methodologies
15 Quality Manager resume templates
Read our complete resume writing guides
1
Quality Manager Resume Examples & Samples
- Provide leadership and strategic direction to a team of Test Leads and Test Engineers within their functional area of responsibility
- Direct motivate and develop staff through coaching and mentoring so as to maximize their individual contributions, professional growth and ability to function effectively as a team
- Accountable for managing human capital management functions which may include: recruitment, development, mobility, performance objective setting, performance evaluations, promotions and terminations
- Manages multiple, large-scale client and business testing initiatives through cross functional teams to ensure the highest quality delivery
- Identify and communicate risks during test planning and execution and identify contingency needs
- Proactively communicate and collaborate with project teams, test teams, support partners and IT leadership
- Ensure project meets quality standards by providing technical guidance in planning, designing, and executing tests and developing procedures relating to product quality on multiple complex programs
- 5-10 year of management and program management experience
- 10+ years of solid software testing background through extended quality assurance experience
- Experience working in both a formal Waterfall SDLC environment, as well as an agile environment
- Experience working within Web Technology, Oracle, SQL, batch processing, ALM
2
Quality Manager Resume Examples & Samples
- Lead the quality and training teams to be industry leading, giving world-class support service across all channels
- Establish an in-house quality management process that will drive continuous improvement in a multi lingual contact centre environment
- Set clear objectives and measures of quality of service to work alongside SLAs
- Use all data available to proactively manage guest expectations and requirements and ensure these are driving service offering improvements
- Work with the operational staff (Team Leaders, Grad Bay coaches) to establish objective measures, procedures, expectations and the Disney Magic standard
- Review regular feedback from operational staff to identify training needs
- Partner with the Training Manager and Team to create a closed loop improvement process to drive quality of service and address knowledge gaps and improve Help
- Be a catalyst for change and improvement in performance and quality
- Manage and lead the incentive program to reward Guest Service staff with Magic Points
- Think innovatively about how to drive and maintain quality standards in email, phone and web chat support and proven industry quality improvement initiatives
- Assess how guest’s expectation may change over time – or dependent on their position in the subscription cycle – and feed that back into the training team to constantly evolve the service we offer
- Continues to think innovatively to solve problems and works cross-teams to achieve results
- Work closely with the Escalations Manager to set strategy for all types of escalated calls; forecasting outcomes, retention planning and customer satisfaction
- This position is accountable to the GX Director for the creativity, innovation and magic that leads to the highest quality guest support
- The Quality Manager will be accountable for the execution of all escalations to ensure guest satisfaction and brand loyalty
- They will be accountable for the engagement of the staff, motivation and incentives program to enable cast members to feel empowered and driven to deliver
- Proven experience of delivery high quality customer service
- Strong understanding of customers, their behaviours; trends and expectations
- Able to inspire and motivate to a high level
- Passion for high quality customer service
- Excellent eye for detail
- Proven ability to drive success and change in an organisation
3
Quality Manager Resume Examples & Samples
- Knowledge of HIPPA/geriatrics
- PACE program experience
- Quality Improvement, MLTC, Medicaid/Medicare, Home Care, Geriatric
4
Quality Manager Resume Examples & Samples
- Developing and maintaining quality world class system while developing employee efficiencies,
- Direction for quality in all manufacturing areas
- Direction of the relevant quality engineers in areas of responsibility
- Direction of the relevant inspectors in areas of responsibility
- Playing a role in the plant annual objectives
- Ensure continued compliance with all Regulatory Standards including:ISO 13485, FDA QSR,ISO 14000
- Ensuring continued compliance with DMR
- Monitor production process for compliance to implemented process controls to ensure quality product is shipped to customer
- Support the RCA meetings to ensure that internal and customer concerns are handled and dealt with in an appropriate manner
- Review and ensure that for areas of responsibility (and those of direct reports) documents listed below are approved in an appropriate and timely manner
- Develop and maintain a program ensuring only correctly validated equipment is used in production process
- Supervision of quality engineers to ensure compliance for their areas of responsibility
- Project meeting attendance as required
- Attend and participate in daily cell meetings
- Ensuring information for PMR and Management Review meetings is maintained and available on time
- Manage and minute PMR KPI meetings
- Maintain training records for all reports
- Ensuring all quality reports are of required standard and issued on time
- Maintain Core records for all direct reports and raise issues concerning timekeeping should they occur
- Carry out a documented monthly evaluation with the quality engineers as well as an annual review
- Ensure open communication exists between the quality engineers and all other groups in order to facilitate the speedy dissemination of relevant changes and improvements to both products and processes
5
Quality Manager Resume Examples & Samples
- Lead Site Quality Management teams & systems including CAPA, Documentation and Complaints Management
- Drive continuous improvement and best practices in site Quality systems
- Co-ordinate Management Review and act as relief Management Representative
- Responsible for ensuring adherence to all external regulatory requirements
- Manage Quality System audits
- Maintain and follow up CAPAs
- Prepare reports on Quality System performance as required
- Be a key driver of cGMP practices within the Quality division
- Provide support for the ISO9001/2000 and ISO13485 Quality System
- Manage and develop the staff in the Quality Systems team through involvement, delegation and regular reviews of performance as established
- Drive key changes and continuous improvement in site Quality systems and procedures
- At least 8 years post graduation experience in Quality environment with at least 5 years at a similar level
- Experience in management of Quality Systems in a Medical Devices/Pharmaceutical Industry
- Excellent knowledge of an ISO 9001/2000 or ISO 13485 environment
- Experience in the preparation of Technical Documentation
- Knowledge of Statistical Process Control and Six Sigma methodologies (Greenbelt Certification would be advantageous)
- A working knowledge of FDA requirements and managing FDA audits
- Demonstrated ability to lead, direct and influence people
- Six Sigma training desirable
- Strong planning and organizational ability
6
Quality Manager Resume Examples & Samples
- Developing, revising and implementing quality standards and policies in the organisation
- Maintaining strong levels of customer satisfaction
- Setting KPIs for the department and individuals within the department
- Develop an effective CAPA system to ensure that corrective actions are effectively closed out
7
Quality Manager Resume Examples & Samples
- Responsible for the coordination, planning, implementation, maintenance, and compliance of contracted services
- Responsible for the consistency and the validity of such quality programs, processes, and systems
- Identifies, recommends, and implements new procedures to ensure the best quality processes and programs, which meet customer needs and requirements
- Identifies and implements practices that result in successful quality program delivery. Identifies and analyzes alternative program solutions. Recommends changes for programs that are not effective, time and cost efficient, or in compliance with company policies. Implements new quality programs to ensure company policies and requirements are met
- Reviews and analyzes documentation and reports reflecting inconsistencies. Ensures the initiation of appropriate investigation and problem resolution strategies for identified non-conformities
- Creates, utilizes, or implements tracking and reporting procedures. Provides reports to team, management, executives, and/or customers
- Creates presentations for senior management on all quality initiatives
8
Quality Manager Resume Examples & Samples
- Create coaching plans to address individual performance needs
- Drive 100% completion of monthly monitoring targets for all Fraud
- Lead daily call and case monitoring alignment and completion targets
- Manage all aspects of the Universal Quality Monitoring Procedure & respective functional customer interaction cycles/CTQ’s
- Oversight of team/site calibrations, reporting, trend analysis and process enhancements to drive process adherence and consistency
- Facilitation of call monitoring sessions with leadership teams, PRM’s and client teams
- Engage Stakeholders and Communication teams as needed to improve processes
- Prepare monthly Quality and Compliance Reporting
- Drive Quality Workflows to Support Central platform, UAT and Launch
- Facilitate transition to Verint call recording system for all sites
- Partner with Compliance to ensure proper Critical to Compliance and Policy requirements are aligned with Call Interaction Cycle and Case Audits
- Drive VOC initiatives for the Fraud function and prepare monthly reporting to highlight issues and drive better customer experience
- Perform special projects and additional assignments as assigned
- Bachelor’s degree plus 1 year of work experience in the Financial Services industry. In lieu of degree, minimum of 5 Years work experience in the Financial Services industry
- Proficiency in Microsoft Office Suite applications
- Thorough understanding of the Universal Quality Monitoring Procedure & respective functional customer interaction cycles/CTQ’s
- Strong knowledge of GENIUS/Standard Operating Procedures
- Call Quality or Performance Monitoring experience is a plus
- Prior Experience Using NICE, VERINT and Support Central Database
- Good analytical skills to analyze quality data and present findings to Fraud Solutions leadership
- Demonstrated ability to communicate effectively to multiple stakeholders
- Strong business process mapping and MS Visio skills
- Experience working independently and cross-functionally
- Demonstrated ability to manage multiple tasks/projects
- Demonstrated leadership skills with internal and external customers
- Clear, concise and effective verbal and written communication skills
- Proven decision making and problem solving skills
9
Quality Manager Resume Examples & Samples
- A Bachelor’s degree in metallurgist engineer or Materials engineer is requiredwith an excellent understanding of quality management practices or equivalent experience
- Knowledge of shop operations and maintenance procedures is required. In addition, seven to nine years of progressively responsible job-related experience are typically required
- Jobholder initiates communication with others outside immediate work group to work on new ideas or to counsel others, etc
- English Proficient
10
Quality Manager Resume Examples & Samples
- Lead and direct the Company health and safety objectives and support the companies health and safety directives to provide a safe and healthful workplace for all employees, this includes
- Act as the senior representative of the company to establish and maintain mutually beneficial partnerships with all suppliers
- Develop and implement operating policies, procedures and systems to support division operating objectives
- Responsible for the development and implementation of quality standards to ensure compliance to the designated ISO/TS16949 responsibilities, environmental management system and health and safety guidelines. Ensures that systems and processes are identified and any non-conformances are corrected in a timely manner
- Establish and monitor the effectiveness of quality management system
- Develop supplier performance measurable indicators and monitor performance
- Support the development of Control Plans for manufacturing and sequencing operations
- Lead problem solving activities to correct
- Manage Supplier Quality standards to ensure meets and/or exceeds customer compliance
- Manage Supplier Auditing Program. Including supplier assessments, communication of supplier quality issues and confirmation of follow-up closure of corrective actions
- Manage Root Cause analysis, closure and determine appropriate action based on data
- Manage corrective actions in response to root case analysis and trends
- Manage component quality including incoming inspection, sample plant, test methods, gauge R&R studies, validation, etc
- Support process/product validation through sample studies, normality testing and data analysis. Review data for Out of Specification conditions, data integrity, etc
- Assure appropriate justification of Change Requests
- Manage department continuous improvement activities including new technology, procedural changes to improve process and/or equipment, etc
- Support Lean, 5s and other division processes
- Partner with division production and engineering to insure compliance throughout current program(s) and new program launches
- Maintain monthly quality Q – Report
- Maintain quality file and document control system including
- Bachelor degree in Engineering or related field or equivalent combination of education and work experience
- Minimum 5 years as a Quality Manager in an ISO-9001 certified organization
- TS-16949 lead assessor qualification or equivalent
- Minimum of 7 years of diversified automotive manufacturing environment including statistics and Q.A. systems
- Minimum of 5 years of supervisory experience desired
- Demonstrated oral and written communication skills, as well as, strong organization skills
- Understanding of manufacturing, assembly, sequencing and equipment principles
11
Quality Manager Resume Examples & Samples
- Directs, implements, and maintains operational-level strategies and objectives. Develops short to moderate-term goals and translates them into short-term plans in support of operational goals and objectives. Monitors performance against plan and ensures that goals are met
- Manages, monitors and controls material, labor, and overhead costs in respective area. Develops, reviews, and maintains budgets and expenses for department
- Leads the effort to internalize quality systems that meet or exceed ISO9001/2000 and ISO 17025 Standards both
- Performs other duties as necessary in support of business objectives. Ensures that facilities are in full compliance with all safety regulations
- Directs, promotes and reviews programs relating to safety, quality and productivity in the division and recommends changes where desirable. Performs regular workplace inspections and monitors compliance with all Health and Safety policies and procedures
12
Quality Manager Resume Examples & Samples
- Ensure effectiveness Quality Management System
- Managing all QM activities with regard to execution and achievement of corporate Quality goals
- Executing the global, quality strategy and goals, in particular the achievement of certified QM systems in the plants
- Track and maintain data analysis of key metrics and performance data as it relates to the global quality strategy and results
- Support Plant management in executing and spreading quality policies; improve the sense of quality of employees by corresponding measures incl. establishing standards
- Support divisions to achieve plant targets and ensure Lessons Learned / Best Practice in respect of Quality
- Drive for continuous improvements and stretch Quality targets
- Support divisions in cases of containments, customer - and warranty claims; executing documentation, root cause analysis and corrective actions and verification of effectiveness
- Ownership in change management systems with respect to all quality-system related subjects
- Engage in internal Program , Project reviews of Program Mgmt. and customers meetings in aspects of Quality
- Interact with Plant Quality, Production Operations and Product Development to meet or exceed internal and external customer quality performance targets
- Support the sales and purchasing team in customer negotiations and supplier quality relevant topics
- Engage in Quality advance planning and execution and support launch activities to meet timing and quality standards
- Execution of in-company-trainings and workshops with regard to quality-related subjects and mind-set
- Ensure QM systems corresponds to Magna Corporate and MPT/ME Group Requirements
- Technical Degree in Mechanics or Electronics required
- Experienced in Quality Operations; Quality Manager
- Must have a minimum of 5 plus years quality management experience working within the automotive electronics industry
- Excellent knowledge in effective quality standards within the automotive industry
- Knowledge of implementing and maintaining QM systems and its Auditing / Assessment internal and external , dealing Suppliers and Customers
- Experienced presentation and moderation techniques
- Comprehensive knowledge of APQP / PPAP
- Excellent knowledge in use of statistic methods and Quality Core Tools (e.g. SPC, 8 D, 5 Why, Ishikawa, FMEA & CP etc.)
- Comprehensive knowledge of Root cause analysis and Problem Solving Methods ( e.g. Shainin; Red X; Six Sigma etc. )
- Comprehensive knowledge MS Office package and Statistics tools
- Advanced knowledge in FMEA Tools (e.g. APIS-IQ etc.), Configuration Mgmt. System (e.g. MKS) and Document Mgmt. Systems (e.g. Compl. Pro etc.)
- Fluent English. (speak & write)
- Other languages desirable
13
Quality Manager Resume Examples & Samples
- Define and drive quality metrics and develop projects to reduce cost of quality through improved processes in manufacturing and repair centers, to include process yield improvements, customer ppm reductions, root cause analysis and warranty cost reductions
- Interface with suppliers, engineering, customer service, manufacturing and sourcing teams to drive quality improvements, minimizing the costs of quality, specifically DOA, field failures, and factory defects
- Analyze customer complaints, returned-material data, and develop action plans to determine root cause and corrective action. This also includes oversight of quality at key suppliers of products
- Ensure regulatory compliance; maintain internal audit schedules and ISO9001 standards
- Lead and motivate a team of quality engineers and technicians across multiple shifts
- Develop quality metrics and provide training on quality system and tools
- Develop and maintain data records and analysis tools to support improvements
- Manage reliability and ongoing conformance testing requirements
- Work closely with plant operations managers to drive QA/QC efforts and drive traditional quality initiatives such as RCAs, CIRs, Process Audits, and QMS procedures
- Support continuous improvement using ACE processes
- Organize and assign resources to support all quality functions
14
Quality Manager Resume Examples & Samples
- This position will report to Operation Manager, The incumbent will assure the facility’s products meet the Caterpillar specifications. Communicate and promote the quality philosophy and provide guidance to various quality areas such as manufacturing, torque support, gage lab, heat treat and/or met lab personnel
- Conducts product evaluation tests on all new product. Determines and orders the product configuration to be tested, designs and directs the test program, coordinates the test and tear-down of each model, and identifies problems. Recommends solutions to Product Group Engineering, Customer Service, Operations and Logistics
- A Bachelor’s degree in Engineering/Manufacturing with an excellent understanding of quality management practices or equivalent experience
- Knowledge of shop operations and maintenance procedures is required. In addition, seven to nine years of progressively responsible job-related experience are typically required. Jobholder initiates communication with others outside immediate work group to work on new ideas or to counsel others, etc
- The ability to listen to others is important to the job
- Engine related product and mechanical industry is highly preferred
- General understanding of the Caterpillar organization, products, policies, and procedures
15
Quality Manager Resume Examples & Samples
- Manage and coordinate the activities of the Quality team
- Act as Cleveland Quality focal for Customer interaction and managing customer program elements, such as QIP (Quality Improvement Plan), Integrated Supplier Information System (ISIS) reporting and data accuracy, NOE (Notification of escapement) completion, etc
- Act as focal for Cleveland Quality Clinic, NCM (non-conformance material) process
- Planning, managing and executing actions to ensure compliance with regulatory, quality management systems, customer and process approval
- Provide leadership to the Quality staff including mentoring, coaching, and training, recruiting, performance management and employee development
- Act as the Quality Team focal for Achieving Competitive Excellence (ACE) on the Shop Floor, including working with the team to drive continuous improvement through driver measures, open team dialogue and bias for action
- Coordinate with other departments to achieve on time delivery & operations commitments
- Follow UTAS/LS quality procedures and specific instructions
- Ensure First Article Inspection (FAI) of Landing Gear are planned & completed to drawing as per AS9102
- Schedule and conduct internal/product audits using AS9100 Quality Management System
- Manage Cleveland Quality System to conform to AS9100, customer and UTAS/LS requirements
- Responsible for the inspection process & conformity assessment of Landing Gears
- Evaluate products & processes for acceptance criteria, initiate Corrective Actions as required to remove (or mitigate) root causes
- Act pro-actively to ensure safe work environment through formal audits & continuous contact with Quality team
- Coordinate overtime, vacation schedules & necessary coverage
- Ensure Quality team members have clear expectations, focus & sufficient resources to complete assigned tasks and direct 5S workplace organization
16
Quality Manager Resume Examples & Samples
- Responsible for North America Quality System and harmonization of standard practices
- Deploy and standardize the global TPM Certification program across Europe
- Quality release of EXO Coty products
- Manage TPM and Component suppliers audits (training, audit management, audit tools, etc
- Responsible for adhere to the audit plan by performing assigned audits according to latest regulatory requirements (FDA OTC, EU 1233/2009, ISO 22716)
- Host external Bodies and Health Authorities in Europe for any inspection on ExO finished goods
- Build and sustain CAPA programs and communication with the TPM’s
- Responsible to deploy Coty QA policy and strategy across the TPMs network
- Assign Quality KPIs to TPM’s and follow ups
- Responsible for creation and global deployment of quality training modules for the ExO NA organization
- Coordinates the collection of Quality KPIs and drive continuous quality improvements (systems, processes, capability)
- Responsible for the creation, review, finalization and adherence to the budget for QA related activities
- Collaborates cross functionally in the supply chain to achieve all KPI’s
- Plans, conducts and supervises assignments and is ultimately responsible for meeting objectives within the area of responsibility
- Conducts the review and evaluation of the personnel in the department
- Ensures that all company and departmental policies and procedures are implemented by the department personnel
- Ensures that all personnel are aware and trained on the Quality System procedures and processes
- Other duties and responsibilities as assigned by supervisor
- Knowledge of quality standards
- Strong Knowledge of the QA Guidelines is needed as well as the local regulations regarding Good Manufacturing Practices
- Deep knowledge of the industrialization processes especially for new products, mainly on the success criteria setting
- Knowledge of TQM methodology and processes management
- Knowledgeable of customary quality assurance testing schemes
- Knowledgeable of customary Bulk and finished goods testing schemes
- Knowledgeable of GDPs, GMPs
- Must possess a thorough understanding of Production Packing Processes, filling and finishing techniques and Industrialization Processes
- Possess budget management and statistical knowledge
- Excellent analytical and problem solving skills with the ability to identify root-cause, recommend options, prioritize and implement appropriate solutions
- Effectively work and communicate with other departments in the organization as well as external parties (TPM, Suppliers)
- Anticipates and resolves problems before they become a crisis
- Works to continually improve work unit performance
- Monitors individual performance/workflow and takes appropriate action
- Leverages diversity to enhance teamwork
- Encourages creative ideas and innovative approaches
- Seeks and applies new tools that advance work unit performance
17
Quality Manager Resume Examples & Samples
- Assists with the development of TS 16949 policies, procedures, and work instructions; enforces implementation
- Participates in the development and implementation of a quality assurance strategy including the preparation of respective instructions and manuals that ensure all materials, product parts, and components meet all standards
- Manages the quality assurance systems including inspections, sampling, and the testing of incoming material as well as the products, components, and parts produced by the company, according to established standards
- Corresponds with customers on product problems
- Develops new test equipment, as required, and ensures department is properly equipped
- Manages and coordinates all activities of the quality assurance department
- Monitors SPC reliability results and ensures correct use of analysis method and corrective action is implemented
- Initiates action to prevent the occurrence of any nonconformities relating to the product, process, and quality system
- Identifies and records any problems relating to the product, process, and quality system
- Initiates, recommends, or provides solutions through designated channels
- Controls further processing, delivery, or installation of nonconforming product until the deficiency or unsatisfactory condition has been corrected
- Minimum of seven (7) years relevant experience in manufacturing and production processes
- Minimum of two (2) years supervisory experience in plant quality
- Demonstrated successful performance with independent and team problem solving, presentations, leadership, and coordinating and completing multiple tasks within and across departments to meet changing deadlines
- Experience with Six Sigma, Lean Manufacturing/Kaizen Events, Problem Solving Disciplines (5D, 7D, 8D)
- Strong communication skills: verbal, written, and technical presentations. Ability to manage customer communications
- Experience with Statistical Process Control (SPC), Design of Experiments (DOE), and Process/Design Failure Mode Effects Analysis (PFMEA/DFMEA)
- Ability to read and interpret blueprints applicable to the process
- Knowledge of flexible polyurethane foam process is a plus
18
Quality Manager Resume Examples & Samples
- Work with suppliers to ensure parts quality meeting the company specs and workmanship
- Develop supplier's capabilities of manufacturing for consistent and repeatable quality, such as step-by-step SOP or BKM, risk analysis and mitigation, etc
- Assist suppliers to go through First articles, setup baseline process, Pre-production within batch and batch-to-batch, and Production ramp phases
- Understand engineering design criteria, tolerance, materials, special process, target applications and requirements; etc
- Maintain and motivate positive relationship with suppliers and know their QC systems, know their management strength and weakness
- Communicate with company internal groups or staffs effectively; obtain help and support in a timely manner, provide inputs to the 180- procedures
- Team up with IQC staffs to ensure smooth quality inspection, including help to setup SOP
- Conduct quality audit at supplier sites, tooling and equipment requirement, cross-calibration, BKM, SOP and improvement plan
- Score cards and supplier performance summary and improvement plans
- Supplier's parts specific production capacity
- Manufacturing cost control, analysis and cost reduction
- Handle non-compliance, corrective actions, stock purge and recall process
19
Quality Manager Resume Examples & Samples
- Third level qualification in Food Science or equivalent
- Minimum 3 years in a large Food or Pharmaceutical company
- Proficient in Quality Assurance management, Food Safety & Process Improvement
- Strong leadership ability to motivate and encourage people to get best results
- Demonstrate high technical ability and attention to detail
20
Quality Manager Resume Examples & Samples
- Leading organization in ensuring product and process compliance by providing guidance and direction with regards to quality systems and requirements
- Working closely with PCI’s Operations Management team to meet short term customer requirements while implementing business strategies in support of long term demands
- Ensure appropriate inspection capacity by achieving productivity goals, cross training of inspectors and implementation of new inspection methods
- Foster and maintain a cooperative relationship with our key customers
- Drive product and process improvements that ensure PCI’s quality metric goals are met (Escapes, Scrap, Rework and Process Cert)
- Work with PCI’s Manufacturing Engineering team to ensure production readiness on new engine programs through the use of UTC’s Production Part Approval Process (UPPAP)
- Drive a culture of continuous improvement through the use of ACE tools to implement change that supports PCI’s Lean Transformation plan
21
Quality Manager Resume Examples & Samples
- Perform 100% quality reviews on all cases
- Coaching and feedback to Client Liaisons on each case
- Encourage Process Improvement identification on cases
- Provide regular, formalized feedback for performance improvement
- Create developmental plans for each team member
- Handle all escalation calls
- Participation on Complaint Governance Committee
- Participation on RSM calls for ERU conversion to new database
- Participate and contribute to Policy & Procedural Manual (PPM)
- Write departmental procedures for ERU Training Guide
- Oversight/maintenance of Credit Bureau reporting
- Interface with business partners of Client Research, Mortgage, Credit/Collections, Bankcards, Retirement Plan Services, branches, Citiphone, etc
22
Quality Manager Resume Examples & Samples
- Leading the organization in ensuring product and process compliance by providing guidance and direction with regards to quality systems and requirements
- Key member of the Operations leadership
- Lead the manufacturing quality team on passport deliverables for all new programs
- Has ownership of supplier quality, factory in-house quality and total customer quality
- Provide leadership to solve value stream quality challenges to ensure Chiller Operations success and customer satisfaction
- Localization of corporate quality strategy for implementation
- Drive product and process improvements that ensure Chiller Operations’ quality metric goals are met (Escapes, Scrap, Rework, Cost of Poor Quality, and Process Cert)
- Drive a culture of continuous improvement through the use of ACE tools to implement change that strives for ACE Gold performance and supports the Chiller Operations factory transformation plan
- Create a safe work environment by promoting a safe culture and driving EH&S improvements that reduce ergonomic and other injury risks in inspection processes
- Attract, develop, and mentor diverse talent in Operations Quality
- Define and drive quality metrics and develop projects to reduce cost of poor quality through improved processes in manufacturing, to include process yield improvements, customer ppm reductions, root cause analysis, and warranty cost reductions
- Interface with suppliers, engineering, customer service, manufacturing, and sourcing teams to drive quality improvements, minimizing the costs of poor quality, specifically DOA, field failures, and factory defects
- Ensure regulatory compliance; maintain internal audit schedules, ISO9001, ASME, PED, and CRN standards
- Drive overall product improvement
23
Quality Manager Resume Examples & Samples
- Ensure that all Telecom implementation activities are performed according to the quality standards, specifications, and requirements set by Ericsson, Ericsson’s Customer, manufacturers or standards bodies
- Generate and distribute audit reports to Service Providers and Ericsson management and communicate results and requirements to other quality management, operations, installation and engineering functions
- Mentor new Ericsson auditors and supplier installation groups and auditors on processes and procedures
- Ensure that the Service Providers meet all the technical specifications with respect to the Telecom and Civil Works issues
- Coordinate with other Departments and Project Organizations and externally, as required in order to accomplish above functions, work tasks, and achieve the objectives of the company, the organization, and the project
- Initiate analyses of any quality problem, to monitor the implementation of corrective actions and to verify that these actions obtain the desired results
- At least 10 years Outside Plant experience with a manufacturer, operator or construction company
- Ability to read & red line construction drawings
- Familiarity with traffic control and safety
- Understanding of permitting & locate processes
- Ability to use Excel and PowerPoint proficiently
- Ability to use Apple or Android smart phones or tablets
- Thorough understanding of Telecommunications Industry Quality and Installation standards
- Attention to detail and the ability to be unbiased with respect to Quality Audits and Audit results, including evaluation, preparation, tabulation, and reporting on results to internal and external customers
- Must have excellent oral and written communication skills, including proficient use of spreadsheets and word processing software
24
Quality Manager Resume Examples & Samples
- Provides Quality leadership / guidance on all QMS matters as well as product compliance to the facility. Ability to make decisions that always protect product safety for products and services provided by the business. Ability to properly balance good compliance practices with other business initiatives to avoid conflict and allow all objectives of the business to be satisfied
- Is the advocate for the VOC (voice of the customer) ensuring customer requirements are realized throughout the life cycle of the products and processes used within the facility from development through product realization and support while in service
- A proactive leadership role that drives the development of robust processes that are used by the business to control all aspects that may affect Quality of the product or service being provided
- Usually the top management representative with authority to ensure that a QMS system is established implemented and maintained within the facility. Reports to top management: Quality Director and Plant Manager
- Manages the daily activities of the functional Quality organization ensuring adequate resources are in place for compliance, cross training is happening to maximize the Quality staff. Daily interface with operations staff on Quality matters
25
Quality Manager Resume Examples & Samples
- Ensure that operational quality is controlled, managed correctly and achieves the required level of quality performance achieving target PPM and ensuring customer satisfaction
- Management of Quality engineers and customer quality accounts
- Support continuous improvement activities
- Provide expert support to ensure customer quality satisfaction
- Interface with purchasing / suppliers on quality concerns
- Maintain and improve quality systems in line with TS16949 requirements and oversee auditing of quality standards
- Smooth transfer of new products from engineering at the start of production
- Previous senior management experience of managing a quality function
- Strong influencing skills with a high level of strategic and commercial awareness
- Fast moving manufacturing or automotive industry experience
- In-depth working knowledge of TS16949
- Experience of customer / supplier interface
- Experienced in problem solving tools and techniques
- Knowledge of Injection Moulding processes
- Good Communicator
- Must have excellent customer service skills
- Proven negotiation skills with verbal and written communications
26
Quality Manager Resume Examples & Samples
- Bachelor of Science Degree in Engineering
- 8+ years experience in engines or equivalent related quality/process experience
- Requires demonstrated leadership qualities and the ability to effectively direct people; should be aggressive, and capable of making decisions based on thorough data-based analysis
- Must be results-oriented and able to drive issues to closure. Demonstrated change agent, who excels in a team environment, is customer focused and able to consistently measure performance and meet commitments
- Excellent problem solving ability and highly developed skills in oral and written communication, computer software, and statistical technique application
- ASQ recognition as a Certified Quality Manager or Certified Quality Engineer is highly desirable
- Knowledge of ISO certification is preferred
27
Quality Manager Resume Examples & Samples
- Provides leadership and direction for all members of the Quality Assurance Work Team and coordinates the team’s efforts with other support areas
- Leads the development of DQS (Magna Sealing and Glass Systems) philosophy and procedures that support the manufacturing of high quality products through continuously improved processes
- Leads the effort to internalize quality systems that meet or exceed QS9000/TS16949 Quality Assurance Standards both internally as well as with suppliers
- Performs other duties as necessary in support of business objectives
- Performs all work in compliance with Magna and Magna Sealing and Glass Systems Health, Safety and
- Bachelor’s degree in Engineering, Physical science, or Quality Control
- 7 years diverse professional and managerial experience including financial/budget responsibility, management leadership, and strategic decision making/leadership in a manufacturing environment
- Demonstrated employee relationship and management skills to develop, lead, support, and motivate a cohesive, world-class quality assurance team
- Demonstrated strong communication skills to work with internal and external contacts at all levels within the organization. Able to represent the company in a professional manner with customers and suppliers
- Demonstrated skills in using statistical control tools and the ability to teach these to others
- Complete training to Work Instruction in MAGnet
28
Quality Manager Resume Examples & Samples
- Coordinate all site document control databases
- Ensure all customer quality requests are addressed
- Conduct site internal audits and keep the programme updated
- Manager the CAPA programme through the company database
- Ensure all product specs are completed to the highest standard and quality
- Facilitate and manage all accreditations, third party audits and certificates
- Develop and maintain the Quality function GPS KPI Processes
- Conduct training across the plant for QA, QC and Food Safety
- Third level qualification in Food Science, Quality or engineering
- Over 4 years' experience in a food or pharmaceutical plant
- Over 3 years' experience in a QA or Food Safety senior role
- High technical ability in a busy food/pharma/FMCG plant
- Proven track record meeting and exceeding expectations for internal and external customers
- Excellent attention to detail, strong communication and interpersonal skills
29
Quality Manager Resume Examples & Samples
- Ensuring that all products and processes are safe and in compliance with specifications statutory obligations, customer requirements and best in class from new product development handover to the site right throughout the product life cycle
- The development and management of an effective Quality Management System ensuring adequate training and development of the entire factory team
- On time delivery of all Quality requirements e.g. Audits, K.P.I reports, QAS's, sampling compliance etc to meet business and customer timelines
- Achieve budgeted overheads
- The receipt, review and introduction of new products and Policies into QMS in conjunction with the Technical team
- Ensuring that all products and ingredients meet customer technical requirements
- The co-ordination of customer technical audits and first production runs
- Ensuring the production facility meets food safety requirements to allow GMP to meet and exceed customer and Department of Agriculture standards
- Ensure an adequate internal audit system is implemented across the business to facilitate continuous improvement
- Liaise with all customers and audit bodies in relation to product safety and quality issues in a timely manner
- Identify & Implement profit improvement initiatives including: alternative ingredient sourcing and trialling, line efficiency improvements and yield improvement
- To understand the company's HACCP plan and to monitor and control this
- Management and up keep of SCADA
- To ensure that all relevant site team members are appropriately trained in food manufacturing standards, quality and food regulatory and legislative standards,
- Customer policies and safety standards to allow them to conduct their duties in an appropriate manner
30
Quality Manager Resume Examples & Samples
- Understand customer expectations and ensure they are consistently met
- Create and assist in delivering a training plan to teach key skills to new employees affording them to have the opportunity to perform their job safely, efficiently and meet customer expectations
- Manage the quality department personnel
- Set up quality systems and processes to ensure customer expectations are consistently met. These systems include
- 1) A customer support system
- 2) A supplier management system
- 3) An internal quality system
- Ensure each process above is managed and followed through with everyday. Continuously improve the above processes based on feedback from key stakeholders (management employees, customers and suppliers)
- Communicate quality processes, concerns and initiatives to the entire plant daily
- Create and follow through on a plan to achieve or maintain TS 16949 and ISO certification
- Responsible for ensuring appropriate APQP activities are taking place
- Administers and ensures compliance with the Quality and Material Management System requirements as outlined in the policy manuals
- Ensure all safety and non-safety plant rules and regulations are followed
- Ensure adherence to established quality and housekeeping standards
- Respond immediately to items brought to his/her attention with respect to hazards, defects or non-compliance issues
- Taking appropriate corrective action when substandard performance is observed
- Review and adhere to Chattanooga Seating Systems’ health and safety, environmental, and quality standards, operating procedures, policies and forms
- Must be familiar with Quality Systems and tools (i.e. QOS, FMEAs, Control Plans, Statistics, APQP)
- Must have knowledge of a variety of computer software applications in word processing, spreadsheets, database and presentation software
- Strong Management skills including management of people, resources, money and time is essential
- Minimum of three years experience with progressive supervisory responsibility in a related field
31
Quality Manager Resume Examples & Samples
- Ensure world class quality standards that produce products and processes at a competitive cost to meet and exceed customers’ specifications and expectations
- Respond immediately to customer inquiries/concerns and builds a good working relationship with the Customer
- Evaluate Process capability together with manufacturing & engineering through regular SPC audits on the shop floor, providing feedback to employees
- Act as STT’S TS16494 Management Representative: Champion Implement, and Communicate, Quality Systems based on the Customer’s Quality Standards
- Assist in resolving manufacturing problems with non conforming material
- Evaluate the design of new products for gauging/testability and reliability
- Conduct performance on worker health and safety performance
- Participate in product team meetings
- Follow positive employee relations: hiring, training, career development, disciplinary action and conducting regular and timely performance appraisals
- Co-ordinate supplier surveys, certify suppliers, rejects or accept supply of components from suppliers in respect to quality specifications
- Establish and adhere to the department’s budget by reviewing department statements (monthly) and monitoring the cost of quality work with the buyer on vendor selection
- Engineering Degree in Mechanical Engineering, Electromechanical Engineering or equivalent
- Significant knowledge of TS16949
- Must have complete knowledge of APQP, PPAP, Control Plans, SPC, FMEA, QFD, Design of Experiments
- Blueprint Reading & Geometrical Dimensioning and Tolerancing
- Must be familiar with OEM quality procedures
- Work experience in a mass production automotive environment with at least five years in quality assurance and preferably three years in a supervisory role
- Good leadership, analytical and problem solving skills
- Ability to communicate and interact well with people in all departments
- Demonstrated presentation skills
32
Quality Manager Resume Examples & Samples
- Coordinate and communicate strategic quality plans; lead and assist with the execution of quality system and process audits related to the ISO 9001, ISO 20000-1, ISO 27001, ISO/TS 16949, A-SPICE etc., to maintain and enhance the Quality Management System, including new certifications
- Take ownership of JIRA bug management system within Core Platform Group including the following tasks
- 3-5 years experience in working with, and setting up processes / Quality Management Systems according to ISO 9001, ISO 20000-1, ISO 27001, ISO/TS 16949, A-SPICE, CMMI, ITIL, or similar
- Typically 8+ years relevant experience; recognized expert in their field (depth & breadth)
- Master degree in Computer Science, Engineering, Business Administration, Management, or similar
- Solid understanding of IT business processes and tools and Quality Management Systems
- IT Process engineering and Quality Assurance
- Ability to translate the IT environment into business terminology
- Ability to maintain the relation between the process and the tools supporting it
- Ability to function in a fast paced and multidimensional role, where interdependencies are many and the effects from NOT managing them result in business impacts
- Able to work under pressure & still keep schedule/results/quality levels, with good communication, organization and keeping dependencies in mind
- Ability to lead teams and personnel from several line units and geographical locations
- Customer facing experience is essential
- Certified ISO and/or A-SPICE auditor/assessor
- IT Training experience is an advantage
- Knowledge of HERE processes is an advantage
- Strategic thinker with tactical execution
- Innovative, strong problem solving skills with team approach
- Ability to collaborate in a multi-national, cross-functional environment
- Customer-focused
- Excellent attention to detail and quality orientation
- Self-directed, self-motivated and accountable for results
- Delivering quality results
- Understanding the HERE business, processes, products, tools
- Strong documentation skills (grammar, spelling, punctuation, etc.)
- Extensive working experience of JIRA, Confluence, SharePoint, MS Office (incl. MS Project and MS Visio)
- Knowledge of SW Requirements, SW Development, SW Testing, CI/CD tools is a plus
- Strong Project management skills, PMI certified is a plus
- Six Sigma Green Belt Certification is a plus
33
Quality Manager Resume Examples & Samples
- Manage and provide technical guidance / direction
- Participate as a key member of the departmental staff team contributing to the overall effectiveness of the business
- Assign resources and responsibilities. Set direction and identify priorities
- Provide leadership and development to the organisation to maximise effectiveness and provide career development
- Control budgets and spending and insure compliance to financial requirements. Insure budgets are adhered to and accurately established
- Project manage and schedule key projects and initiatives insuring timely execution and goal achievement
- Integrate with corporate requirements and promotes consistency with other sites and corporate
- Assist Quality Director in developing strategies for the quality function and with execution of agreed functional / global strategies and goals
- Implement and insures compliance to the quality requirements per the site and corporate quality system
- Demonstrates through management style respect for the core values and a commitment to teamwork and communication
- Compile and analyse operational, test and validation data to establish technical specifications and performance standards for newly designed or modified products and processes
- Take a leadership role in developing and implementing new techniques and initiatives to enhance the Quality management system on site and across the Corporation where possible
- Develop staff on new quality initiatives and assist in the understanding and rollout of quality initiatives across the department/site
- Be recognized as champion of behavioral/GMP and cultural initiatives with strong quality related problem solving and decision making skills demonstrated
- May lead a group or team of employees in the achievement of organizational goals.Guide, coach, direct, and develop direct reports, and if applicable, drive those practices throughout their organization
- Foster a diverse workplace that enables all participants to contribute to their full potential in pursuit of organizational objectives
- May direct and control the activities and budget of one or more functional areas, divisions, product groups, projects/programs and/or operations
- Monitor and ensure compliance with company policies and procedures (e.g. federal/country and regulatory requirements)
- Monitors company-wide indicators such as market share and profitability
- Provides direction and guidance to professional specialist employees or subordinate managers, supervisors and engineers
34
Quality Manager Resume Examples & Samples
- Responsible for leading all technical activities (set-up the quality technical schedules, recipe, quality, process design, packaging and finished product acceptance)
- Accountable for Q&EHS incidents in external factories
- Lead the manufacturing line trials on existing/new production lines e.g. raw material testing/recipe changes etc. and/or scaling-up of production for new products/varieties in order to ensure that the agreed product design characteristics are achieved
- Develop risk assessment based on their quality systems and processes
- Develop KPIs and prepare/present reports on performance against set KPIs, communicate issues, provide solutions, and manage quality reports
35
Quality Manager Resume Examples & Samples
- Education: Must have a Degree Food Science: Food Technology, Process Engineering, Chemistry or Physics
- Experience: 8 to 10 years' experience within Quality Environment and Technical depth and knowledge of Quality Assurance systems, techniques and ISO systems
- Food Safety (HACCP), GMPs, Food Safety Risk Management, auditing and incident management experience is a must
- A capable leader of indirect teams and individuals and able to motivate and engage superiors, peers, indirect teams
36
Quality Manager Resume Examples & Samples
- Plans, directs, and develops direct reports and supports the work efforts of indirect employees including overseeing the training of Inspectors and Quality Engineer's within the their assigned area of responsibility in the application of inspection processes, customer requirements, etc. Provide leadership in the balancing of compliance practices with other business initiatives to allow all objectives of the business to be satisfied
- Provides support to functional leadership by gathering and analyzing Quality information, programs, and initiatives. Responsible for monitoring and analyzing processes and/or product outputs, identifying systemic problems and opportunity areas, providing data and direction to the site(s), and work with team members to drive process improvements to work toward zero-defect quality performance
- Ensure that the site and suppliers’ quality management systems consistently meets or exceeds customers’ and companies requirements
- Prepares, monitors, and responsible for budget, staffing, and business results of the Quality team
- Lead and/or assist internal product and systems audits
- Support and follow all rules/guidelines/standards set by EHS, Quality, and CI functions as set by your leader and position
- Position requires access (on-call) at all hours and all day
- Potential need to work during company designated holidays
37
Quality Manager Resume Examples & Samples
- Responsible for regulatory and compliance including implementation and maintenance of GMP+, HACCP and all Quality SOP's
- Ensure all products are registered and full compliant with global standards
- Conduct audits internal and external
- Oversee laboratory testing to ensure all required testing is performed on each product
- Responsibility for the overall quality team including targets and KPI's are adhered to
- Training of quality and production staff
- Strategic planning and development for Quality across the plant
- Minimum of 3-5 years' experience in the food or related industry
- Degree in Food Science/Science discipline
- Ability to manage, supervise and lead a growing quality team
- Strong time-management, decision-making and organizational skills
- Organised with very strong attention to detail
- Excellent team player with strong capability to work on own initiative
- Ambitious, hardworking and driven to achieve at the highest level
38
Quality Manager Resume Examples & Samples
- Report on quality performance on a weekly and monthly basis & discuss issues with site management with a view to continuous improvement
- Represent quality function at the daily Visual Management meetings and manage the QA department on site
- Developing suitable in process test programs to ensure deviations from normal standards are detected promptly, to ensure potential to produce conforming product is maximised
- Oversee the general hygiene and GMP program and co - ordinate the weekly report on hygiene standards
- Upgrade the QMS from ISO 9002 standard to ISO 22000
- Liaise with customers on technical issues and represent their requirements at site forums
- Liaise with customers re resolution and close out of customer complaints and maintain metrics on same
- Liaise with Supply Chain - Purchasing, re standards of purchased materials and changes to same
- Liaise with accreditation bodies and Dept. of Agriculture inspectors on site quality issues
- Pivotal role in representing customer requirements for production planning with plant managers and Supply Chain to delivery customer requirements
- Manage and continuously improve the entire QA Program for the site including sampling plans, policies, procedures, and specifications,
- Develop and instil recognition of a Quality culture across the Site management team and operations team
- Communicate quality issues and quality developments (i.e. legislation changes effectively across the site team
- Develop, train and up skill employees in conjunction with site team
- Manage non routine happenings including the coordination of customer complaint investigations and verification of corrective actions
- Role in highlighting any deficiencies in operating/plant standards by scheduling and completing system and hygiene audits on a regular basis
- Grade Finished Product as per customer requirements
- Approve new specification as per plant capability
- Clearance to plant / warehouse re: product release
- Liaise with Supply Chain re: stock status
- Other duties as required from time to time
- Delivery of quality reports as per defined frequency
- Performance in customer audits and regulatory inspections
- Response time to solving quality issues
- Delivery of the site quality budget and contribution to the delivery of the site budget
- Design and implementation of and effective QA Management system including adherence to sampling / testing plans, Weekly Hygiene audit scores
- Customer complaint metrics
- Downgrade reports
- Product Release Compliance
39
Quality Manager Resume Examples & Samples
- Acting as the representative of Quality Management in Wroclaw for Products IT
- Managing all aspects of Quality Management and associated KPIs
- Working with the PMO team in WRC
- Strategizing with the QM team on planning, policy compliance, ensure internal process engagement
- Attending and participating internal meetings on behalf of the to provide insight and help answer questions as well as advocate for various points of view. Provide briefings back to team as needed
- Champion activities to improve the efficiency and internal processes of the department
- Enforcing organizational rules, policies and procedures
- Monitoring and reporting on internal KPIs
40
Quality Manager Resume Examples & Samples
- Assess both product and customer specifications and requirements ensuring compliance to standards
- Directs, implements, and maintains operational-level strategies and objectives. Develops goals and translates them into plans to support the operational goals and objectives. Monitors performance against such plans and ensures that goals are met
- Acts as a key contact with customers, suppliers, auditors, manufacturing, and support resources to ensure the execution of corrective actions and that the Quality Assurance systems are meeting objectives and continuously improving
- Ensures that facilities are in compliance with all safety regulations
- Directs, promotes and reviews programs relating to safety, environmental, quality and productivity in the division and recommends changes where desirable. Performs regular workplace inspections and monitors compliance with all Health and Safety policies and procedures
- Demonstrated strong communication skills to work with internal and external contacts at all levels within the organization. Able to represent the company in a professional manner with both customers and suppliers
- Bachelor’s degree in engineering, physical science, or quality control
- Ten years diverse professional and managerial experience including financial/budget responsibility, management leadership, and strategic decision making/leadership in a manufacturing environment
41
Quality Manager Resume Examples & Samples
- Ensure repair station is in compliance with all associated quality procedures and policies including quality requirements driven by the FAA/EASA/CAAC and future regulatory agencies
- Lead internal and external quality audits
- Periodic review and updating of all repair station manuals and procedures
- Coordination with the DCMA for all government source inspection product lines
- Oversee the Quality Clinic
- Oversee all activities associated with supplier quality, warrant process, part purges and MRB activities
- Champion process improvements
- Perform RRCA for any quality issues within repair station
- Participate as key member of leadership team
- Participate on cross functional quality teams within Rockford and other repair centers within worldwide repair network
- Maintain all levels of certifications for the repair station including FAA/EASA/CAAC/AS9110/ISO9001/ISO14001
42
Quality Manager Resume Examples & Samples
- Quality Assurance – Responsible for working with manufacturing facilities and suppliers to ensure all LFI footwear products are built to LFI’s high quality standards
- Manage LFI’s Sourced Quality Team and Program – Responsible for overseeing entire quality team and program for LFI’s source product. This included alignment of corporate, Asia office and manufacturing facilities to LFI’s quality processes and goals
- Quality Manual Ownership – Responsible for creation, implementation and maintenance of LFI’s sourced quality manual. This is a living document in which the Quality Manager will be responsible for its ownership
- Data Management and Reporting – Compile data, generate reports, make recommendations, and help implement solutions for quality and production teams to improve product. Must be active participant in all quality and manufacturing programs
- Material and Finished Product Testing – Oversee and/or perform testing on materials and finished products to make certain boots meet expected quality standards
- Material and Finished Product Inspection – Oversee and/or perform finished product inspections to make certain boots meet expected quality standards and aesthetics
- 3+ years footwear experience required
43
Quality Manager Resume Examples & Samples
- Ensure that all products manufactured meet required quality specifications
- Management and development of staff in the Quality department
- Ensure Customer requirements are achieved by modifying processes / equipment / operating standards as necessary to eliminate defects
- Liaise with customers, manufacturing, engineering, R&D, and sales & marketing staff on all quality related issues
- Manage quality metrics and ensure adherence to quality targets
- Responsible for ensuring adherence to all Company, external and appropriate regulatory requirements (ISO, FDA)
- A third level qualification in a Quality, Engineering or Science Discipline
- At least 9 years' post-graduation experience in a Quality environment, with at least 5 years' at a management level
44
Quality Manager Resume Examples & Samples
- Responsible for overall management of all quality systems at the Union,WV and two OH locations, Uniontown and the Service Center
- Manage quality staff and provide support for the manufacturing operations
- Manage internal project reporting for the reduction of CoPQ and DQ. (Cost of Poor Quality and Delivered Quality)
- Establish and maintain a Quality Assurance Standard and Program that monitors, identifies, records and recommends possible solutions of any non-conformities and/or inconsistencies relating to the manufacturing process, final product, and quality system
- Assist in formulating and establishing new products that coincide with the current market or customer demands
- Works closely with the Plant Manager, Production Lead Manager, Engineering, and CSR personnel to maintain information on customer demand and needs
- Provide customer requested documentation including but not limited to Quality Improvement Plans and complete customer questionnaires. Act as point person for Level 1, 2 & 3 audits
- Provide management support in the development and maintenance of the EH&S program
- Contribute to overall Company quality initiatives, collaborating with other plants within the SIS Group (Sensors and Integrated Systems)
- Responsible for implementation of necessary resource & identifying training needs within the plant QA area
- Leads plant Management Review process to identify improvements and monitor progress of C.I. activities
- Confers with Engineering and Manufacturing personnel to assist with resolution of any internal or external quality concerns (including: scrap, suspect material, non-conforming material requiring deviation, etc.)
- Ensures the maintenance, updating & compliance to specific requirements necessary to support the business model (e.g. AS9100, ISO 14000, Customer-specific requirements, etc.)
45
Quality Manager Resume Examples & Samples
- Execution of the CRM Quality Assurance steps, for fee-based, services proposals and resultant projects within a business unit, in compliance with the World Wide Quality Assurance / Management Discipline (WWQA/MD)
- Independently review for fee-based, services engagements, assess and makes recommendations to influence the viability, risk, project management, profitability and customer satisfaction in services solution design and delivery
- Reviews and approves qualification and validation life cycle documents
- Guide, police and implement FDA Compliance procedures
- Provides advice and counsel to project managers, line managers, and executives regarding opportunity bid decisions, risk mitigation and containment, proposal quality, project health, and business management practices and procedures
- Guide functional objectives or technologies
- Communication/Negotiation - Advise other professionals. Effectively utilize group dynamics. Negotiate to define approaches and goals
- Problem Solving - Recognise complex problems related to functional objectives. Analyse situations and implement solutions, or develop new system elements, procedures or processes. Creativity and judgment applied to developmental work on different projects within the business environment
- Contribution/Leadership - Provides ongoing technical /operational guidance to lead professional work teams, conducts special projects, or manages department(s) (national or international). Understand department/ functional mission and vision. Defines and decides objectives within specified business concept or project and may have responsibility for tools and assigned resources. Utilizes expertise to directly influence people outside department or function. Sometimes no precedent exists
- Impact on Business/Scope - Accountable for department results and for activities and/or projects involving multi-functional teams. Regularly participates in overall functional program planning. Activities are subject to business measurements, impact customer satisfaction, and impact project costs or expenses
- The position requires extensive GxP pharmaceutical skills & experience and detailed knowledge of FDA Compliance processes
46
Quality Manager Resume Examples & Samples
- Leads Oakley’s In-house Manufacturing Quality Program related to eyewear finished goods and related pre-assembly operations such as lens molding, lens cutting, lens tinting, eyewear frame painting / graphic, Frame injection molding and related quality engineering functions. Manages approximately 10 direct reports (Quality Engineers and Supervisors) and 50 indirect reports (QA Leads, Technicians & Product Inspectors)
- Drives analysis related to Oakley's Internal Quality Cost of Quality & Topics of Extra Consumption (Scrap) & alignment for improvement projects
- Leads efforts & focus on product quality problems and gives direction to systematically drive improvements for those problems (Related to LQS ( outgoing Quaility), and Quality Service Levels)
- Drives improvement projects based on Market data and After Sales input
- Is able to organize and work a wide range technical issues and understands product performance requirements and the efforts to manage the Quality Team in meeting expectations
- Can work globally with other Lux Facilities producing Oakley products and align the brand expectations for quality and be a resource from Oakley Headquarters to assist those facilities as needed
- Annual Budgeting to align with Annual Operating Plan and / or 3 to 5 year manufacturing forecast
47
Quality Manager Resume Examples & Samples
- Advocates for the role of Global Quality and the importance of Product Safety, Quality and Regulatory compliance with colleagues across the business
- Acts as department lead for communication with key internal customer groups. Assesses project requests, determines work required and assigns to team resources. Develops best practices methods and incorporates into development processes
- Manages quality teams in selection and evaluation of suppliers and in commercializing merchandise
- Manages the development, implementation, and monitoring of an integrated program to assure that quality, product safety and regulatory compliance standards are met for merchandise
- Selects and manages third-party auditing and inspection services to verify supplier and product compliance. Uses audit and inspection data to identify risks and opportunities for improvement. Monitors effectiveness of ongoing corrective actions
- Creates structure and organization of quality records required to show compliance to supplier and product requirements
- Stays up to date and builds expertise in product regulations and best practices
- Executing global quality management program for merchandise or relevant supplier management & auditing (7 years)
- Experience in planning, developing and managing merchandise quality systems and risks (7 years)
- Progressive experience within a global quality organization including quality systems, product quality, supplier quality, and retail quality (5 years)
- Management of technical professionals (5 years)
- Familiarity with non-food requirements including: ISO 9001, CPSC, ANSI, etc
- Ability to work with cross-functional teams
- Ability to apply knowledge of multidisciplinary business principles and practices to achieve successful outcomes in cross-functional projects and activities
- Ability to manage and investigate complex issues, draw conclusions and make recommendations
- Ability to communicate with and effectively influence senior management, facilities, retail operations team, supplier management team, internal customers and peers
- Ability to remain calm under pressure
- Ability to solve quality and regulatory issues through data, processes and influencing skills
- Ability to articulate and sell quality programs and continuous improvement goals, and to influence indirect resources in achieving results
- Familiarity with quality documentation needs and systems
- Knowledge of quality program methodologies and implementation within manufacturing and retail operating environments
48
Quality Manager Resume Examples & Samples
- Develops a culture focused on member safety while ensuring cost-effective and appropriate medication therapies are delivered to members following state and federal laws
- Assists in the planning, organizing, and controlling of quality related programs adhering to governing and accreditation bodies including, but not limited to, CMS and URAC
- Manages activities and resources of the Quality Program and provides direction and guidance to cross-functional business partners regarding quality performance, improvement, outcome management, and member safety
- Coordinates interdepartmental and intradepartmental quality programs and committees
- Creates and implements policies and procedures related to quality oversight including, but not limited to, audit procedures, claims monitoring and validation, quality metrics, analytics, and quality performance goals
- Reviews quality reports, summarizes, interprets, and reports findings to governance committees
- Leads the development of comprehensive agendas to facilitate various governance committees
- Ensures the accurate reporting of all quality errors as defined by the overarching quality program and assists in maintaining the Quality Database
- Performs root cause analysis of errors and assists in developing and implementing corrective actions or rapid process improvement plans
- Three years PBM experience or equivalent
- Three years in a leadership role; preferably in quality management with direct reports
- Six Sigma Green Belt or Lean Sigma
- Currently licensed as PTCB or RPh
- Prior experience in quality management, accreditation and CMS guidelines
49
Quality Manager Resume Examples & Samples
- Analytical Problem Solving
- Confidence
- Impact and Influence
- Product & Technology Expertise
- Dealing with ambiguity
- Must have a degree in business with at least 5 years in quality / risk management experience
- Quality certification expertise (e.g. ISO, CMMI, Six Sigma (strongly preferred. PMP (PMI) certification
- Candidate must possess excellent demonstrated decision-making, analysis, and problem solving and communication skills
- Willing to travel within the [area] frequently for quality audits, coaching and connecting with local management
- Familiarity with policy and procedure writing and a strong understanding of and skills in the financial - risk-reward - trade-offs in good project management
- Strong self-motivation, the ability to work independently, and within a team environment with strong follow up, organization and prioritization skills and excellent attention to detail helps too
50
Quality Manager Resume Examples & Samples
- Responsible for daily quality functions such as auditing, compliance, receiving inspections, condition inspections, in-process inspections, return to service inspections, and functional testing to support operations
- Functions as the Chief Inspector, and final airworthiness authority for the facility
- Responsible for the facility training program and ensuring that only properly trained individuals perform maintenance
- Provides oversight for compliance to the FAA Drug and Alcohol Testing Program
- Manages and directs activities related to the Technical Library, including the purchase of required technical data, specifications, and manuals
- Oversees quality improvement projects and teams
- Provides quality leadership / guidance on all QMS matters as well as product compliance to the facility. Ability to make decisions that always protect product safety for products, and services provided by the business
- Ensures compliance with all regulations and/or standards related to FAA, EASA, ISO, CASE, etc
- Functions as the primary contact with outside agencies, including the FAA, AS9110 registrar, and customer quality representatives
- Provides proactive leadership that drives the development of robust processes through continuous improvement/ACE, which are used by the business to control all aspects that may affect the quality of the product, or services being provided
- Interprets, executes and establishes operating policies and processes, and participates in establishing and administering many division-wide initiatives
- Acts as a liaison between internal and external customers, departmental representatives, and agencies
- Has the organizational authority to resolve all issues pertaining to quality
- Manages the daily activities of the functional quality organization ensuring adequate resources are in place for compliance, and that cross training is occurring to maximize the functionality of the inspection staff
- Daily interface with operations staff concerning quality matters
51
Quality Manager Resume Examples & Samples
- Manage all Plant quality activities
- Act as the main point of contact between the Company and customers
- Monitor performance of quality control systems to ensure effectiveness and efficiency (KPIs)
- Develop team in quality control and analytical procedures in relation to TS
- Actively participate and lead efforts towards using Total Quality Management tools such as Team Oriented Problem Solving, SPC, QS9000
- Produce reports regarding non-conformance of products or processes, daily production quality, root cause analyses, or quality trends
- Review statistical studies, technological advances, or regulatory standards and trends to stay abreast of issues in the field of quality control
- Identify critical points in the manufacturing process and specify sampling procedures to be used
- Meet customer expectations including process data, material certification, documentation, and other requirements as specified
- Maintain effective communication and coordination with all internal customers; plant management and team members, external customers and suppliers, through prioritised work lists, plant meetings, daily and weekly meetings
- Direct Quality Assurance staff to effectively monitor production quality performance
- Establish procedures and develop quality assurance program as defined in the Quality Assurance Procedure Manual, including MAFACT, policies, objectives and plans
- Conduct vendor quality system surveys and assist in vendor selection; Maintain positive vendor relations and assist vendors to consistently and reliably to meet the Divisions quality requirements
- Maintain and continuously improve department organisation and housekeeping standards
- Support new program launches
- Determine, achieve and improve productivity, quality, environmental, health and safety goals
- Provide motivation and results-oriented environment
- Report on status of departmental projects as required
- Conduct performance evaluations of assigned staff as specified by company goals
- Promote and facilitate Open Door Process without reprisal, effective communication and Fair Treatment
- Participate in Continuous Improvement activities
- Degree in technical field preferred or equivalent experience
- Advanced Quality systems development
- ISO/TS requirements
- Automotive fabrication processes
- Advanced Product Quality Planning methods
- At least 5 years in a Quality Manager Role
- Experience managing suppliers and related supplier issues
- Chemical composition, structure and properties of substances
- Chemical processes and transformations. This includes uses of chemicals and their interactions, danger signs, production techniques, and disposal methods
- Production processes, quality control, costs and other techniques to maximise the effective manufacture and distribution of goods
- Excellent mathematical and analytical skills
- Able to demonstrate understanding of how job performance affects product quality and customer satisfaction
- Able to provide a results orientated environment and set high standards for self and department
- Able to provide excellent leadership example, able to coach, motivate and build self-confidence within workforce
- Able to prepare, read and interpret written reports, instructions, procedures and guidelines
- Able to effectively present information and respond to questions from Senior Managers, Team Members, Suppliers and Customers
- Excellent computer and software skills including Microsoft Office, SAP, Hyperion
- Able to work flexibly and additional hours as needed
- Honest with high integrity
- Able to work well with others and build and maintain positive relationships
- Current UK Driving Licence
52
Quality Manager Resume Examples & Samples
- Approval of new suppliers along with maintenance of current approved supplier
- Strong knowledge of managing allergens within production
- Corrective and preventive actions where required
- Internal auditing of quality systems
- Managing customer complaints
- Document data control
- Preparing Reports for management review
- Identification of training requirements
- Reporting to senior management on food safety and quality issues
- Supplier approval & management
- Responsibility for testing of final products and raw materials
- Maintenance and verification of daily and weekly quality records
- Organisation of Management Review
- Management representative for company on food quality and safety issues (BRC & HSE Audits)
- Sign off of production schedules
- Matching of raw materials
- University degree. Food science discipline preferred
- Relevant experience (5yrs +) working in the food industry and 2yrs+ managerial experience
- Proven abilities in decision making
53
Quality Manager Resume Examples & Samples
- Effective management of the facility Quality Management System (QMS) ensuring the system is established, well maintained and improved upon
- Acts as the functional management representative responsible for compliance of products and processes used by the location internally (& possibly externally) in the production of aerospace products
- Manage the daily activities of the functional Quality organization ensuring adequate resources are in place to support all compliance matters, audits, investigations, and reviews
- Direct and regularly interface with receiving inspection, quality engineers, NDT inspection, Operations and Engineering staff
- Act as a key internal consultant to the leadership of the business on all Quality matters
54
Quality Manager Resume Examples & Samples
- Quality system development, implementation & maintenance
- Ensuring that processes meet with ISO and AS requirements
- Assessing product specifications and customer requirements and ensuring that are met
- Agreeing in-house standards for quality
- Development, Maintenance and Approval of Standards
- Managing quality issues to ensure timely and effective corrective actions to prevent re-occurrence
- Monitoring the ongoing performance and outputs of the quality process and providing updates to managers and directors around quality issues
- Supplier and Customer Liaison on Quality Issues
- Oversee the design and execution of commissioning and validation protocols on manufacturing equipment, software and process, and approve validation documentation
- Maintain an understanding of cGMP regulations and guidance in relation to all aspects of qualification of process and equipment
- Coordinate validation team activities to ensure schedule adherence and compliance
- Using statistical analysis, measure, control and improve on product and process robustness
- Minimum 10 years work experience with at least 5 years within a medical/pharmaceutical environment with experience in Quality Assurance, Validation & Process Improvement
- Knowledge of ISO13485 and AS9100 standards
- Working Knowledge of SAP or equivalent ERP system is desirable
- Knowledge and experience of problem solving techniques
- Strong and assertive personality
55
Quality Manager Resume Examples & Samples
- Assess systems and processes are compliant and measures are in place to operationally report quality performance
- Monitor policies and procedures supporting our business
- Model the effects of process changes by quantitatively and qualitatively measuring against internal and external benchmarks
- 2+ years of quality audit and/or compliance experience
- Understanding of laws and regulations as it relates to commercial health insurance
56
Quality Manager Resume Examples & Samples
- Promotes the division’s commitment to Quality by organizing and implementing all quality systems and policies in order to meet Magna standards, customer standards and achieve customer satisfaction
- Develops division’s Quality Program including: policies/procedures, standards, training requirements, etc
- Develop, organize and implement all Quality System requirements for: existing product lines. quality improvements, engineering changes, new product launches
- Participates in engineering design review and product costing
- Ensures appropriate Quality representation at customer locations to effectively meet issue response requirements
- Develops control plans for pre-production phases Including prototypes, tooling capability studies, setting key characteristics (process & product), checking fixtures and inspection techniques in conjunction with all A.P.Q.P procedures
- All aspects of P.P.A.P
- Provides Training to all Production and Quality personnel for product development and inspection requirements, etc
- Liaises with production, engineering and customers to initiate, investigate and resolve non-conforming product using effective preventative and corrective action in a timely manner
- Develops/maintains a calibration schedule for the calibration of checking fixtures and gauges
- Develops/maintains Statistical Process Control for all products and communicate results as required and ensure training to all employees in SPC process
- Establishes process improvement criteria in conjunction with Production and Engineering to support continuous improvement efforts
- Develops a Quality Business Plan aligned with the divisions Business Plan
- Participates in the development of the Company Goals and Objectives to support the annual Business Plan
- Develops department action plan and leads their team to achieve strategic goals and continuous improvement objectives in alignment with the Company’s Vision and Guiding Principles
- Prepares and supports the budget planning process and takes responsibility to meet the financial targets
- Makes decisions in the scope of their responsibilities that are in the best interest of the department, Division and Cosma/Magna
- The Manager reports directly to the General Manager/Assistant General Manager and is responsible to provide communication and reporting of their Department progress/results in achieving divisional goals; and the regular operation of the department
- Ensures confidentiality in all matters pertaining to both business and employee relations
- Conducts monthly department meetings to communicate Safety, People, Quality, and Production information and to promote involvement in issues affecting employees or their work areas
- Participates in manpower requirements planning, overtime scheduling, and assists with capacity planning to meet future objectives
- Directs and distributes the work for their area of responsibility
- Completes Payroll activities for employees
- Ensures fairness to direct reports, and encourages and participates in the Open Door Resolution Process for employee relation issues
- Supports and models the Divisions operational procedures/policies, Employee Handbook, Leader Guideline Booklet, and Magna Employee’s Charter, and the Magna Corporate Constitution
- Follows and complies with all operational procedures/policies as stated in the Employee Handbook, Quality and Environmental programs (e.g... TS16949, ISO14001)
- Post-secondary education of either a University degree in Engineering or a College certificate in Engineering Technology, Manufacturing Technologies preferred, or equivalent experience, and/or 10 years work experience in the Quality Management field
- Minimum 5 years in a leadership role
- Must possess knowledge and proven skills in one of the following: Lean Manufacturing, Six Sigma, or Kaizen; Project management and prioritizing
- Prior experience implementing TS 16949 procedures
- Must have Quality training and experience in; GD&T, 8-D, AIAG standards, Customer Quality Standards, APQP, PPAP submissions, FMEA’s, Control Plans, Statistics and fixture development
- Demonstrated ability to use precision measurement tools (height gauge, vernier, micrometer, etc)
- Computer skills; knowledge of Microsoft Word, Excel, Visio, and Powerpoint
- Must possess human relations skills and maturity of judgement
- Must possess time management, leadership, communication, organization and presentation skills
- Promotes/recommends continuous improvement suggestions including environment, people, processes and equipment/machinery
- Assists in the development of procedures and methods which improve quality/productivity/cost to their area of responsibility
- Provides guidance and support to the Leadership Team
- Ensures employees are trained or certified, as required and participates in training programs as required
- Develops and maintains peer relationships
- Ensures Supervisors/Lead hands follow the Accident/Incident Investigation Procedure
- Ensures subcontractors are performing work safely while in their work areas/zones when applicable
- Continuously develops their leadership skills
- Approaches each day and each challenge with a positive attitude
- Implements 5S principles and in still’s pride in their team to keep their work area clean and tidy
- Required to adhere to all Health and Safety programs in accordance with the OSHA. Follows and ensures the Company’s procedures regarding safety rules and regulations are followed throughout their assigned area. Ensures all Supervisors/Lead hands are adhering to all the above and problem-solving issues that arise in the area of safety and ergonomics
- Equipment: PC, Quality Measuring equipment, etc
- Software: Microsoft Office Products, Database Applications, etc
- Performance Management - Observe, understand, teach, coach and mentor direct reports for enhancement of knowledge, skills and succession planning
- Effectively builds and fosters high performing teams by ensuring teamwork within the department
- Conducts and/or ensures that all Supervisors/Lead hands Investigate all non-conformance to Company polices/procedures/rules/regulations and apply the applicable corrective action. I.e. coaching, counselling and feedback documentation, discipline, performance management, etc
- Conducts performance reviews informally or formally as required and ensures performance reviews are completed for all employees
- Works cooperatively with HR Health & Wellness to return employees (STD/Workers Compensation) to work under the Return-to-Work program and ensures the leaders within their area of responsibility monitor employees to ensure they work within their R-T-W plan
57
Quality Manager Resume Examples & Samples
- Ensure that the Quality department is effectively staffed and internal labs sufficiently equipped to meet the needs of the business with regards to internal and third party service provision
- Ensure that the Quality function is effectively identifying and mitigating product risk during the product creation process. Report the risk to the business and put strategies in place to effectively manage that risk through production
- Drive the creation, upkeep and distribution of quality procedures, policies and manuals such as: Testing and Acceptance Criteria, Inspections process, Metal contamination policies and other necessary vendor management documentation. Lead internal and External Capacity building
- Ensure that the Quality Assurance field staff are effectively training and educating the supply chain on Fanatics Apparel’s requirements, are effectively executing internal audits at the suppliers facilities during production and are communicating real time with the US based Product Creation team
- Build solid relationships with the Fanatics Apparel supply chain both overseas and domestic embellishment and leverage those relationships as needed to bring quality issues to resolution
- Manage 3rd party quality service providers, manage pricing to ensure efficiencies and ensure budget adherence
- Bachelors Degree in Textile Engineering or related subject required
- At least 10 years of relevant textile industry experience required
- Strong project management plus the knowledge of the product creation lifecycles and calendar timelines are required
- Experience evaluating supply chain facilities from a Quality Management perspective required
- Ability to communicate new processes and procedures both internally and externally required
- Must be able to work independently and make quality based business decisions
- Must possess strong management skills
- Strong influencing and communication skills a must
- Strong computer skills in excel and word needed
58
Quality Manager Resume Examples & Samples
- Manage all facility activities and personnel reporting to this position
- Act as primary liaison between CCMi Systems and all customers, maintaining effective communication
- Understand and stay current to carry out customer expectations including process data, material certification, documentation, and other requirements as specified
- Maintain effective communication and coordination with all internal customers, plant management and associates; Maintain positive employee relations; Listen to issues and concerns and respond (C48) within 48 hours
- Follow the principles of the Magna Employee Charter
- Promote and practice “safety first” by immediately addressing any hazards, defective equipment or unsafe conditions within the department
- Assist Quality Assurance staff to effectively monitor production quality performance
- Establish procedures and develop quality assurance program as defined in the Quality Assurance Procedure Manual, including Mafact, policies, objectives and plans
- Actively participate and lead efforts towards using Total Quality Management tools such as Team Oriented Problem Solving, SPC, QS-9000 / TS 16949
- Conduct vendor quality system surveys and assist in vendor selection; Maintain positive vendor relations and assist vendors to consistently and reliably meet CCMi’s quality requirements
- Maintain effective department communications through prioritized work list, plant meetings, daily Supervisor and Lead hand meetings, and weekly department meetings
- Maintain and continuously improve department organization and housekeeping standards
- Facilitate cross functional teams
- Establish, achieve and improve quality and safety goals
- Interface with Quality vendors to insure purchase of proper materials
- Utilize lessons-learned philosophy in continuous improvement activities
- Complete correspondence, forms and reports in Word, Excel, Access and other required programs
- Ensure all employee documentation is maintained
- Prefer Bachelor’s degree in technical field
- Minimum 5 -10 year progressively more responsible quality experience in automotive manufacturing
- Knowledge of automotive customer requirements
- Knowledge of Quality processes and procedures to include SPC, GD&T, VE, APQP, DOE, etc
- Must have excellent human management skills, be decisive and always set a good example
- Must have positive attitude
- Excellent verbal and written communication skills high ability to comprehend both
- Excellent quality procedure skills
59
Quality Manager Resume Examples & Samples
- Manage site Quality Assurance team
- Manage Product Quality Assurance including calibration, electrostatic discharge (ESD) prevention, and all inspection activities (Incoming, In-process, Outgoing)
- Manage Supplier Quality including supplier-performance monitoring and supplier qualification
- Execute the site Escape Management Process resolving all quality non-conformances and escapes. This task includes managing the Returned-Merchandise Authorization (RMA) management process, serving as the site Quality Clinic lead and effectively interfacing with all appropriate parties including customers and suppliers
- Review contractual quality flow-downs and insure they are adequately addressed in appropriate internal and supplier documentation
- Train personnel when required
- Track and report business analytic data associated with the Quality function
- Provide expertise in QA and use of process improvement tools
- Insure compliance to the site’s Quality Management System (QMS) including conducting first party audits and serving as the Point-of-Contact for all external auditing agencies and parties
60
Quality Manager Resume Examples & Samples
- Annual bonus
- Up to date training & knowledge in automation technology
- Staff appreciation events
61
Quality Manager Resume Examples & Samples
- Ensure that the company conforms to all customer requirements related to part quality
- Lead and maintain the Material Review Board per established policies
- Ensure that appropriate corrective action is in place where non-conforming part issues arise in house or at customer locations; coordinate / participate
- Continually review and upgrade policies, standards and procedures for quality related issues in the department and the company
- Provide clear direction and leadership in the attainment and maintenance of the business system standards
- Ensure that the company responds to customer complaints in an appropriate and timely manner via Customer Service department
- Oversee the maintenance of the quarantine/containment areas to ensure a steady turnaround of material including proper disposition
- Work with the Corporate Quality Manager to ensure prompt attention to all customer concerns
- Develop a divisional culture that recognizes the role of customers as an integral part of the business, deserving of respect and high quality service
- Adhere to Magna Techform of America’s policies and procedures
- Ensure all suppliers of components and materials adhere to the quality requirements of the organization
- Ensure the on-time completion of all departmental projects
- Aid in the conceptual development of manufacturing processes associated with new and existing products
- Ensure the proper education of subordinates in the areas related to the function and goals of the department
- Oversee the proper calibration of all measuring equipment including attribute check fixtures
- Post-secondary degree or diploma in Mechanical Engineering, a trades certification or equivalent
- Strong written and verbal communication skills particularly in the area of report writing are required
- Attention to detail is key
62
Quality Manager Resume Examples & Samples
- Serve as Management Representative for TS16949 (Quality System) Audit
- Measure level of quality and provide management with accurate and timely data
- Raise quality level by reducing rejected PPM (Parts Per Million) toward goal of
- Work with Engineering personnel on Advance Product Quality Planning (APQP)
- 8-10 years of progressively increased responsibility for quality management systems
63
Quality Manager Resume Examples & Samples
- Maintains quality assurance objectives and metrics
- Maintains customer relationships, including scheduling of customer visits
- Insure that company policies and procedures are followed
- Responsible for implementation and compliance to TS16949 as the Management Representative
- Directs and develops employees engaged in quality assurance activities including PPAP, FMEA, SPC, Gage R&R, Supplier qualification, Calibration systems and Corrective Action and Preventative Action
- Audit and track supplier quality performance
- Provides preventive measures for in-process part qualification through random inspection, dock auditing and maintenance or a statistical process control program, as well as, analyzing data to evaluate the current process and changes
- Operate CMM to inspect and perform studies on components
- Oversees layered audit procedure and process
- Prepares and presents technical, program and operation information to the management team
- Implements quality assurance training programs for personnel in conjunction with Managers, Supervisors and Leaders
- Maintain documentation and records of Quality department functions
- Involvement in Advanced Product Quality Planning
- Develop, implement and control all procedures directly relating to product quality
- Control and maintenance (calibration) of all quality devices (gages, fixtures, tools)
- Investigate nonconformities and develop, initiate and verify corrective action
- Record and track the measurement of quality using the cost of quality with is a reflection of the price of nonconformance
- Manage the Quality department budget
- Commitment to quality and a safe and healthful work environment for all employees
- Assist the organization in implementation of Mafact, including lean, standardized work and continuous improvement activities
- Attends and participates in the Fast Response, Mafact, Departmental and Manager meetings
- Follows MIOSHA and MPTSH safety regulations and policies, including wearing required P.P.E. (Personal Protective Equipment). Reports unsafe conditions
- 7 years’ experience in an automotive environment. 3-5 years’ experience in Quality. Minimum 5 years’ experience in supervision. Extensive knowledge of production metal stamping and CNC machining. Must be a results-oriented team player, effective at problem solving and project planning/organizing, with excellent interpersonal and communication skills, high energy level and good attention to detail. Must be well versed in the following: dimensional layouts, safety requirements, statistical process control analysis and up to date industry standards. Core training. Working knowledge of PPAP, FMEA, SPC, Gage R&R, Supplier Qualification, CMM, interpretation of technical drawings and specifications, Quality Systems, Calibration systems and Corrective and Preventative Action
64
Quality Manager Resume Examples & Samples
- Department supervisor, responsible for the work group independence, lead or support and supervise subordinate's work
- Formulate and implement the product quality control plan, in order to achieve the quality target
- Organize and implement the quality supervision and inspection, formulate the quality inspection standard, and inspect the production department obey the quality standard
- Formulate and implement inspecting, testing and analysis policy, ensure each process of product is match quality standard
- Summarize the product quality problem and push relative department to solve problem in time
- Proposed quality improvement scheme, to optimize the product quality, controlling cost, improve the production efficiency
- Responsible for collecting competitor's product information and after-sales service information
- Build and preserve the quality management system. Setting up and maintaining controls and documentation procedures. Setting standards for quality as well as health and safety; work closely together with headquarters
- Customer complaints handle, and improve product quality control according to feedback information. Reviewing customer requirements and making sure they are met
- Supplier quality management and process audit
- Responsible for evaluation subordinate's performance, formulate and implement the performance improve plan
- Other temporary work assigned by the supervisor
65
Quality Manager Resume Examples & Samples
- Works cross functionally with Production and Engineering Manager to manage and deliver business goals and objectives
- Responsible to deliver Business Unit 9 Panel Metrics (Safety - Quality - Service - Cost )
- Champions key Quality Metrics for the Business Unit - CAPA, Quality Incidents, manufacturing complaints, RFT, Audit results etc
- Monitor and ensure compliance with company policies and procedures, the corporate Quality System and regulatory requirements
- Responsible for developing a world class-manufacturing team that is proficient in problem solving issues using Six-Sigma tools
- Manages the Quality team for the Business Unit and coordinates all quality related activities. Coaches and mentors staff on daily issues and technical issues
- Key focus on Talent Management and People development and Succession Planning within the area and department to help develop future business leaders
- Develops and executes departmental budgets. Control spending and insure compliance to financial requirements. Insure budgets are adhered to and accurately established
- Leads and represents function in periodic business metric reviews
- Initiates cross-functional partnerships to identify and resolve production/Quality issues
- Prioritizes and drives execution of multiple complex department projects
- Active participant at departmental and manager/director business meetings focused on continuous improvement and driving ideal behaviours within the site
- Lead or supports the site Strategic Quality Process (SQP) and key site-wide projects
- Develop strategies for the quality function and execute agreed functional / global strategies and goals
- Integrate with corporate requirements and promote synergy/consistency with other sites/corporate
- Champions and supports the introduction of key New Product for the business. Works closely with Design Assurance & Process Development on all New Product activities
- Requires a minimum level 8 relevant Engineering / Science degree
- Ideally 8 years experience within the medical device or pharmaceutical manufacturing industry, with at least 4 years' experience in a leadership role
- Experience/training in problem solving and process improvement methodologies
- Excellent interpersonal and communication skills with good leadership abilities
- Ability to work as part of a team and meet targets/goals efficiently
- Strong knowledge of quality principles and the ability to utilize these methods in a manufacturing environment
66
Quality Manager Resume Examples & Samples
- Provide leadership to the Quality Engineering Team and instill a sense of urgency
- Drive problems towards resolution to ensure that quality systems, procedures and instructions meet Customer requirements, Co Ex Tec’s objectives, and regulatory compliance in the following areas
- Create an environment that encourages active process improvement discussion within the business goals
- Identify opportunities, scope projects and forecast resources to achieve productivity, quality and service improvement targets for the business
- Develop the annual Business Plan for the Quality Department
- Identify key weaknesses within the business and lead the transformation of existing processes to a higher quality operation
- Leverage the capabilities, ideas and processes within the team
- Lead and manage staff including resource planning; training; and performance management
- Ensure enforcement of Customer Specific Requirements and compliance to QMS (TS16949), EMS (ISO 14001), Health and Safety (OHSAS 18001), and security (PIP) requirements
- Perform regular workplace inspections. Perform accident investigation. Correct unsafe acts or conditions. Train new/transferred/temporary employees on safe method of conducting their job. Correct or commend Health & Safety performance
- Attend authorized training in order to develop and/or maintain relevant job-related knowledge, techniques, skills, and/or certification
- Perform, direct and/or carry out any reasonable assignments required by Management
- Post Secondary Bachelor Degree in technical field or equivalent, required
- ASCC Certified Quality Engineer/ Certified Auditor, Certified Quality Manager preferred
- Excellent working knowledge of Quality and Environmental Management Systems. Registered Auditor qualification desirable
- Strong leadership, problem solving (including root cause analysis), project management, presentation; and facilitation skills
- Sound computer skills, including knowledge of software in current use
- Lean Manufacturing experience, formal training an asset
- Able to understand timelines and current program status
- Independently designs and implements procedures and quality systems particular to manufactured products/processes that meet registration as well as Customer and Co Ex Tec requirements
- Able to use statistical techniques/applications to solve quality, productivity, application cost and/or safety issues. Able to strategize and implement solutions
- Required to travel to any Customer and or Supplier on short notice
- Minimum 10 years experience in high volume manufacturing environment, preferably automotive
- Minimum 5 years experience in management or supervisory position
67
Quality Manager Resume Examples & Samples
- Ensuring that processes meet with ISO requirements
- Assessing product specifications and customer requirements and ensuring that they are met
- Undertake and supervise the program of internal auditing
- Oversee the design and execution of commissioning and validation protocols on software and processes and approve validation documentation
- Implementing health and safety policies into the overall quality management process
- Direct staff and teams across the business to ensure quality frameworks are implemented
- Determining training needs to ensure compliance with the Quality System regulations
- Acting as a catalyst for change and improvement in performance/quality
68
Quality Manager Resume Examples & Samples
- Strategic project portfolio management in support of the quality management system
- Execute high impact projects through 6 Sigma methodology
- Facilitate high impact rapid improvement workshops
- Deploy Lean principles throughout extended value stream
- Coach quality team members as required
- Educated to a degree standard or have equivalent previous experience
- Significant progressively responsible job-related experience
- Demonstrable project management capabilities and process improvement techniques
- Engineering knowledge and capability
- Leadership capabilities
- Cross functional leadership demonstrated through project management
- 6 Sigma Black Belt experience
- Quality Management systems
- Knowledge of engines
- Previous leadership experience
69
Quality Manager Resume Examples & Samples
- Bachelor’s Degree in a related field of study
- TS-16949 lead assessor qualification or equivalent preferred
- Micro-computer software training
- Sound knowledge of statistical methods
- Minimum five years experience in quality and process control in automotive manufacturing
- Minimum three years of supervisory experience
70
Quality Manager Resume Examples & Samples
- This role is responsible for championing facility quality programs in adherence with the Caterpillar QMS at the Denison, TX facility
- This role is responsible for Built in Quality Implementation
- Provides leadership and expertise in setting Quality measures for the Facility, and reporting progress toward meeting goals
- This incumbent will support the Facility Manager and Product Managers in setting quality policies, indicators and promoting quality policies throughout the BU
- Formulate, develop, and implement quality strategies to accelerate Durability and Reliability improvements to achieve product goals
- Provides leadership to BU teams to provide statistical control, audit and systems support for internal certification
- Organizes teams, leads and/or participates in solving various problems, determines the root cause of the problem and proposes solutions
- The position supervises or manages a work unit of management or salaried employees where planning, scheduling, and monitoring and reviewing work of subordinates is required
- Bachelor degree in engineering or manufacturing related field of study with a strong background in manufacturing facilities, equipment, and processes
- 8-10 years of progressively responsible job-related experience in Quality
- Excellent interpersonal skills are required in order to deal with sensitive issues, develop others, or persuade others inside and outside the department to take specific actions
- 6 Sigma experience as a Green Belt or Black Belt would be highly desired
- American Society for Quality (ASQ) or global equivalent certification as a Manager of Quality (CMQ), Quality Engineer (CQE), Quality Auditor (CQA), Mechanical Inspector (CMI), or Reliability Engineer (CRE)
71
Quality Manager Resume Examples & Samples
- Be responsible for internal quality control, ensure raw material and finish goods are corresponds to related standards
- Participate supplier audit, and offer suppliers necessary guide for quality control aspect
- Build- up and maintain quality system
- In charge of customer complain collection, analysis, and handling
72
Quality Manager Resume Examples & Samples
- Working closely with hardware, software engineering, manufacturing, data operations and global support teams while advocating issue resolution through streamlined processes within testing protocols
- Collaborate with leaders and product owners to develop and prioritize a project portfolio to improve key performance indicators across multiple projects
- Lead project through all the phases of the continuous improvement framework (DMAIC/DMADV/PCDA)
- Ability to perform analytics around trend analysis, sensor life cycles, regression tests, failure modes and effects analysis (FMEA)
- Manage and develop all quality processes for on-going support and repair procedures (RMAs)
- Accelerate improvement efforts with the use of proven quality tools and methodologies
- Provide technical and statistical expertise to teams
- Formulate, document and maintain quality control standards and on-going quality control objectives for on-site manufacturing and supplier chains
- Leadership role in building a culture of continuous improvement across multiple projects
- Drive Culture Change – Drive fact-based decision making throughout the organization
- Review test plans/scenarios and ensure conformance to testing standards, software requirement specifications, and architectural recommendations
- Work with project teams to review and accept requirements and set project testing priorities
- Bachelor's degree in Engineering or other related technical field required
- 3-5 years management experience in a highly technical environment
- Experience applying Lean and Six Sigma tools, applications, methodologies specifically: Value Stream Mapping, Kaizen Blitz, Theory of Constraints, Quality Functional Deployment, Pugh Matrix and Kano Analysis
73
Quality Manager Resume Examples & Samples
- Define program objectives and establish program deliverables
- Lead the QSE internal audit and corrective action team
- Collect/Compile data and drive Continuous improvement initiatives for audits and corrective action process
- Maintain key relationships with suppliers’ Quality and Operations Management teams, as well as other organizations
- Lead customer reviews related to audits and corrective actions
- Support various business reviews and external audits
- Monitor, control, and report program progress
- Manage audit schedule and identify and control audit scope changes
- Escalate risk and issues for resolution as appropriate
- Track program deliverables and ensure timely completion
- Manage audit program and corrective action closure activities
- Manage audit an corrective action standard work and related procedures
- Support software/supplier project plans
74
Quality Manager Resume Examples & Samples
- Ownership of the UTC Quality Council process which requires facilitation of strategic planning and Policy Deployment, development of processes in support of key initiatives, and ownership of the standard work for council management
- Serving as Quality Council liaison to chartered sub-councils and workgroups to drive one company solutions
- Serving as link between Quality Council and other functional councils ( i.e. Supplier Performance, ACE, Supply Management, Tech), by effectively establishing open and effective communication channels
- Ownership of UTC Corporate Quality Procedures which requires coordinating strategic planning and execution, management of multiple technical writing teams, and ownership of the standard work for document management to assure UTC documentation supports customer and regulatory requirements
- Coordinating UTC engagement on industry work teams in order to assure UTC interests are included when creating industry standards
- Supporting Business Unit processes by facilitating communications across UTC for escapes and other systemic quality issues
- Managing corporate quality communications via the UTC website for suppliers, and SharePoint sites for UTC employees
- Supporting activities to attract and develop quality talent through hands-on recruiting, hosting information-sharing sessions, and mentoring of early talent
- Serving as quality expert in support of quality/compliance investigations, as required
75
Quality Manager Resume Examples & Samples
- Owns and Drives reduction in total cost of quality metrics including but not limited to Scrap, Warranty, and Concessions
- Leads quality-training activities and certifications
- Leads Return Material activities (both customer and vendor returns) & Non Conforming Material Review Board
- Leads & coordinates with area Quality Engineers the quality audits. (both internal and external)
- Leads the evaluation of new suppliers through site audits, first article inspections, and other appropriate activities identified in the Event Tracking project test plan
- Monitors and audits nonconformance and work with key stakeholders to drive resolutions
- Drives usage of quality control reporting, performs analysis of data to identify systemic issues and engages with marking, customer service center and customers to develop and implement effective corrective actions to address defined issues
- Drives closure/resolution of customer issues
- Completes projects focused on improvements in quality & customer satisfaction
- Integrates and shares Best Practices with other GE businesses to drive improvement of process and
- BS Degree in Engineering or Technology Field
- Minimum 5 years manufacturing experience with a background of ISO or QA/AC
- Desire for hands on approach to resolving opportunities/issues
- GB Certified
- Ability to communicate in English
76
Quality Manager Resume Examples & Samples
- Work with operation team to operationalize lean in GO Asia, including visualized management, standard work, process re-engineering, problem solving, issue/waste identification, workload optimization etc
- Drive culture of lean, FastWorks and continuous improvement
- Deploy FastWorks every day and lean on philosophy, theory and application tools/tactics
- Deliver breakthrough levels of process simplification in GO processes, lead/coach simplification projects
- Drive strategic initiatives with our Business Partners
- Provide advanced solutions to support cross-function team in process management
- Constantly seek, share and implement best practices
- Support record and information management
- Other ad hoc projects assigned by manager
- Bachelor degree or above, major in finance, supply chain, IT preferred
- Above 7 years’ experiences in a multinational enterprise, minimum of 4 years of experiences in lean management, process improvement position
- Strong interpersonal and leadership skills at cross business/cross country level
- Project management/process improvement experiences
- Capability to handle multiple stakeholders within a complex matrix environment
- Strategic thinker; proven ability to anticipate, and resolve complicated issues
- Excellent communication, influencing & presentation skills (including fluency in English)
- Cultural awareness & sensitivity
- Shared service experiences
- Finance, supply chain experiences
77
Quality Manager Resume Examples & Samples
- Audit product through the production process and perform product audits to verify production assembly is adequate in meeting design and customer specifications in regard to Quality
- Reviewing customer requirements and ensure that they are met
- Set the standards for Quality and communicate this information to any individual involved with the project
- Travel locally and possibly internationally for customer and supplier visits
- Working with Purchasing, General Manager, and Project Managers to establish quality requirements from external suppliers
- Making sure that manufacturing or production processes meet international and national standards
- Establish and maintain controls and documentation procedures
- Monitoring performance by gathering relevant data and producing statistical reports and contributes to the team effort by preparing and providing such reports to all team members
- Make suggestions for changes and improvements and how to implement them
- Maintaining and improving product quality by completing product, company, system, compliance and surveillance audits; investigating customer complaints; collaborating with other members of Management to develop new training methods
- Maintains professional and technical knowledge by attending educational workshops, reviewing professional publications and establishing personal networks
- Oversees the Quality Department (CMM Operator & Quality Technicians)
78
Quality Manager Resume Examples & Samples
- Ensure that all devices manufactured meet required quality specifications, through moulding, assembly, packaging, sterilization and release
- Lead the following Quality functions: Quality Management Systems, Quality Engineering, Microbiology, and Validation
- Provide leadership and direction to the quality group and work to align the quality systems between plants
- Manage and develop the staff in the Quality department through involvement, delegation, and regular reviews of performance as established in IIGs
- Analyse customer complaints and modify processes/equipment/operator standards as necessary to eliminate defects
- Responsible for ensuring adherence to all external and appropriate regulatory requirements (e.g. ISO, FDA and PAL)
- Become the contact person with IMB, NSAI, FDA and other Regulatory Bodies
- Be a key driver of cGMP practices across the site
- Manage quality metrics across the site and ensure adherence to site quality targets
- Liaise on a worldwide basis with quality, engineering, R&D, marketing, and manufacturing staff
79
Quality Manager Resume Examples & Samples
- Maintaining a culture of continuous improvement to build the customer experience and support the business
- Overseeing and coordinating customer audits and regulatory inspections in various 3M plants where Med Tech products are manufactured
- Assuring all products released to the market meet their specification and the regulatory requirements of global Health Care markets
- Developing solutions for highly complex and multi-faceted problems, which require ingenuity, creativity, innovation, and strong analytical skills
- Taking initiative to proactively create cross-functional collaboration and engagement to more effectively implement programs and process in support of meeting the business team’s plans and objectives
- Actively participating in the division Quality leadership team as well as the Med Tech business operating committee
- Bachelor's degree or higher in a science or engineering discipline from an accredited university
- Minimum of five (5) years combined experience in a manufacturing, quality, laboratory and/or production environment
- Minimum of five (5) years of leadership experience
- Experience in the Health Care Industry
- Demonstrated ability to operate in a Business to Business (B2B) model
- Demonstrated skills in customer experience management
- Knowledge of Medical Device or Pharmaceutical Quality Systems
- Proven ability to lead cross-functional teams and create excellent collaboration
- Ability to lead internal and external audit activities
- Change Management experience of programs with significant strategic importance
80
Quality Manager Resume Examples & Samples
- Will be overall incharge of Quality department
- Develops Key Operating Indicators (KOIs) in accordance with all relevant parties
- Develop the Quality organization and deploy the quality systems, policies, procedures and related processes
- Promotes quality achievement and performance improvement throughout the organization
- Sets QA compliance objectives and ensuring that targets are achieved
- Handle all customer engagements on quality aspects of new program development, production model quality and after sales service
- Handle after sales service through an effective warranty management system. Work with service partners as required for deployment / implementation of service network
- Establishes standards of service and clearly defined quality methods for customers or clients
- Manage supplier quality - new part development, PPAP / PSW, ongoing supplier quality and improvement. Supplier quality issue resolution
- Works with supply chain/sourcing team to establish quality requirements from external suppliers
- Implement and qualify to all quality systems certifications - ISO/TS16949 and other customer specific certifications and systems such as VW VDA, Renault – ASES, M&M MSES / MMA, GM - QSB etc
- Ensures compliance with national and international standards and legislation
- Considers the application of environmental and health/safety standards
- Ensures compliances to defined manufacturing processes by periodic audit process ( Product, System and Process audit)
- Ensures LAYERED process audit is effectively implemented
- Work with Regional teams for process alignment, benchmarking and best practices
- Defines quality procedures in conjunction with manufacturing and engineering
- Develop; train the teams on all quality processes / tools, as required
- Drive a continuous improvement culture through Kaizen, 6 Sigma, DMAICR approach
- Conducts monthly Management review meetings and tracks the open points for closure
- Prepare and report periodic quality measurable reports in line with standards
- Highest levels of personal integrity and safety mindset
- First Bachelor’s Degree in Mechanical Engineering or an equivalent to and engineering degree
- Minimum 12 years of experience in quality function, of which last three years should be handling the function independently
- Should be certified TS Lead Quality Auditor and VDA 6.3 auditor
- Demonstrated experience in Quality Management Systems and Continuous Improvement
81
Quality Manager Resume Examples & Samples
- Quality Manager for Ammunition Supply Point Operation in Kuwait. Responsible for day to day receive, store and issue management of ammunition
- Responsible for the management, integration, and coordination of work-groups and/or units associated with quality management functions
- Maximizes project quality under ISO 9001:2008 standards; identifies root cause corrective action and clearly communicates recommended courses of action
- Makes recommendations to the customer and Honeywell leaders on ways to improve project performance
- Implements company policies; determines program or contract objectives; implements program or contract quality management policies, processes, and procedures; ensures compliance with the corporate quality policy
- Through supervisors, directs the performance of functional tasks; oversees the technical, financial, quality requirements associated with the organization(s)
- Participates in the department strategic planning process, develops long-term plans and ensures appropriate skills are available when needed
- Focuses on processes to enable continuous improvement across multiple units; ensures effective horizontal and vertical communications to facilitate continuous improvement
- Develops, assists in the evaluation, and implements changes in work operations and processes to improve operating efficiencies
- Maintains and uses a vector of customer satisfaction metrics to manage the reorganization; interacts with customers on issues needing technical guidance, redirection, and/or resolution
- Leads initiatives designed to improve the organization's quality baseline and to reduce or eliminate non-value producing functions, processes, and procedures
- Anticipates and plans for skills and human resource requirements, and develops staff to meet those needs
- Recommends candidates for employment
- Minimum four (4) year college degree required from an accredited educational institution, recognized by the U.S. Department of Education
- Minimum of ten (10) years of quality management experience which demonstrates increasing levels of responsibilities, and knowledge of ISO International Standards
- Effective written and oral communication skills are required to work with all levels of the organization and the customer
- Proficiency in Microsoft Office, with intermediate to advanced knowledge of MS Excel is required
- Must be familiar with the methodologies, tools and concepts of quality management
- Six Sigma Black Belt or Lean Expert Certification a Plus
- Project Management Professional (PMP) certification a Plus. Demonstrated commitment to continuous improvement through team participation and results
82
Quality Manager Resume Examples & Samples
- A minimum Bachelor’s Degree in a Technical or Scientific discipline is required, preferably in Engineering. An advanced degree is highly desirable
- A minimum of 5 years’ experience working in a quality system framework (ISO 13485 or similar) specific to Medical Devices is required
- 2 years’ experience in managing people, either directly or through projects is preferred
- Experience with Risk Analysis, Investigations, and/or third party inspections is preferred
- Knowledge of process and design excellence tools and Green or Black Belt training is preferred
- Able to work independently and prioritize multiple projects
- This position will be based in Raynham, MA and will require up to 10% travel, including potential international.Quality (Eng)
83
Quality Manager Resume Examples & Samples
- Develops and implements a quality system, ensuring both compliance to high standards and a quality focused workforce, including the design and management of basic policies, programs, standards and methodologies for the assurance of quality production. Sets standards of performance for quality and measures progress. Analyzes progress and takes corrective action. Implements Lean Six Sigma processes wherever possible
- Directs and coordinates a team of Quality & Production Leaders to achieve continuous auditing of the quality levels in the plant. The management of those departmental employees includes training, evaluation, discipline, and resolution of personnel grievances. Enforces rules, regulations, and policies to ensure a safe, firm, fair, and consistent work place environment
- Works with production personnel across the plant to identify, solve quality issues and improve overall quality
- Directs and coordinates the customer return process and assists in determining the validity of claims
- Directs and coordinates laboratory activities for incoming inspection and finished products testing; acts on results
- Coordinates communication for supplier quality problems and maintains strong connectivity with other Unilin plants to ensure worldwide compatible quality standards
- Ensures adherence to and facilitates employee training and compliance with all company safety rules and procedures
- Follows safety procedures, standard operating procedures and quality policies and regulations
- Develops and implements a quality system, ensuring both compliance to high standards and a quality focused workforce
- BS degree in electrical engineering, chemical engineering, mechanical engineering or other relevant field. Six Sigma Black Belt Certification desirable
- Knowledge of production processes, quality control concepts, and other techniques for maximizing the effective manufacturing of goods
- Knowledge of business and management principles involved in strategic planning, allocation of resources, and coordination of personnel
- 3-5 years quality control experience in an automated manufacturing environment
- Lean and Six Sigma tools experience desirable
- Excellent computer skills including advanced knowledge of Microsoft Office products
- Strong math skills, including the knowledge of arithmetic, basic algebra, geometry, and statistics, and their applications
- Excellent written and oral communication, organizational, analytical, problem solving and time management skills
- Strong interpersonal skills, with the ability to work effectively with all levels of the organization, and the ability to motivate, develop, and direct subordinates
- Possess exceptional attention to detail
84
Quality Manager Resume Examples & Samples
- To ensure Nestlé Quality grades and responds to green coffee sample analysis, meeting all Nestle standards within defined response time
- Provide support for Green Coffee Technicians, including: Receipt of samples, doing physical defects, issuing both notification and approval letters to suppliers and more
- Supply reports on delivered quality, to Suppliers and Overseas Quality Control Centres to ensure contracted quality is delivered on a long term basis
- Have Line Manager responsibility and manage the day to day operation of Nestlé Coffee Quality team
85
Quality Manager Resume Examples & Samples
- Degree in scientific discipline
- 3-10 years operational experience within a food manufacturing environment
- Trained auditor: ability to audit supplier operations and internal operations
- Food Hygiene Certificate (Advanced preferred)
- IOSH Managing Safety Certificate (or equivalent)
- Technical expertise and understanding of relevant market leading food manufacturing processes; pragmatic analytical problem solving and decision-making, in an operational environment
- Leadership standard knowledge of HACCP food safety and practical implementation
- Change management – ability to introduce and embed significant change
- Technical leadership on impact of legislation and Company guidelines on manufacture, supply chain and its customers
- Weight control expert
- Ability to influence and direct suppliers, customers, EHO’s
- Specification and recipe administration systems
- Working knowledge of analytical and microbiological testing methods
- Track record in team leadership
86
Quality Manager Resume Examples & Samples
- Define and implement quality improvements to improve operations and unit cost
- Act as a role model to team members and be recognized as the plant’s quality expert
- Provides direction and guidance to team members to ensure that day-to-day quality support needs and goals are met
- Communicate and work with appropriate personnel to support and achieve global/corporate goals and metrics
- Assist production on a daily basis with quality related issues
- Assist Technical Manager with assigned projects
- Oversee the coordination and evaluation of plant development trials from the quality perspective
- Work in a team environment with operators, mechanics, and exempt professionals
- Review and implement engineering and quality change orders affecting the production line quality
- Establish and direct teams to Corrective/Preventative action for field or internal failures
- Shift Process Technicians
- Various Quality Personnel
- Various Production Personnel
- Support Personnel (i.e., Production Control, RD&E, Training, Human Resources, Accounting/Finance, etc.)
- Customer (End User)
- Vendors
- Bachelors Level (Engineering/Quality) Degree or Closely Related Degree
- Extensive technical experience/knowledge: (1) material & product quality specifications; (2) test methods; (3) data analysis & report writing; (4) quality control systems; (5) critical to quality attributes
- Results focused – shows a documented track record of consistently using data based decision making to achieve desired results
- Be able to follow and give high regard to safety rules and housekeeping procedures
- Ability to pay close attention to detail and coordinate various activities simultaneously
- Able to operate with considerable latitude
- Good understanding of lean manufacturing principles
- Experience with high volume operations
- Strong organization and planning skills
87
Quality Manager Resume Examples & Samples
- The Quality Manager will provide leadership, expertise, and continuous improvement to the Quality Assurance function in the Kirksville, MO factory. Lead the development, implementation, and maintenance of the factory Quality Management System in compliance with the Kraft Heinz Quality Management System. Assure that all products processed, packaged, stored, and distributed are manufactured in compliance with all Regulatory, Customer, and Kraft Heinz requirements
- Develop and administer the factory Quality Management System in accordance with current protocols and provisions, as defined in Quality Management System Program
- Communicate the factory Quality Management System expectations to all personnel and defined stakeholders, and provide training accordingly
- Provide technical support to Operations, Maintenance, Sanitation, Logistics, Procurement, and Sales / Marketing
- Manage the factory Pre-Requisite Programs (PRPs), Operational Pre-Requisite Programs (OPRPs), and Critical Control Points (CCPs), as defined in the Food Safety Program
- Participate in the QRMP yearly audit and assist in the development of procedures and corrective actions
- Oversee and lead the implementation of the QRMP (Quality Risk Management Process) system and operational standards as outlined in the plant accountability list in order to achieve targeted RCR
- Verify and Validate manufacturing processes comply with regulatory requirements
- Represent the factory on the communication and interaction with local, state, and/or federal regulatory agencies (v.gr: Health Department, FDA, and USDA)
- Represent the factory with interfaces with customers
- Retain and maintain documentation and records associated with Kraft Heinz and factory Quality Management Systems, Quality Risk Management Process, and Food Safety Systems Certification (FSSC 22000)
- Train personnel in techniques and procedures for the Food Safety Program, Quality Assurance activities, Quality Control activities, Raw Materials and Finished Goods Inspections, and Sensory Taste Panels
- Responsible for the administration, execution and maintenance of the internal audit program
- Manage and maintain the factory microbiological and analytical laboratories
- Review all Process Sheets and Specifications for acceptance or variance to capability
- Serve as the factory primary contact for all customers’ and third party audits, including management, preparation, and corrective actions
- Represent the factory in the New Product Development Process (NPD) to ensure factory capability for new products and line extensions
- Champion quality improvement initiatives and waste reduction projects to center line processes and reduce variation
- Manage and report on key issues, trends, customer / consumer complaints, and incident investigations to local and HQ Quality and Food Safety management. Communicate and report on key quality performance metrics as defined by HNA Quality and local management
- Develop and manage the department’s operating budget
- Assure that all non-conforming products are managed (including identification, segregation and timely final disposition) in accordance with current applicable policies
- Interface with contractors (pest control, cleaning chemicals, engineering, etc.) and raw material suppliers to ensure compliance with quality and food safety requirements
- Partner with business leaders on implementation of process improvement (Six Sigma / Lean/Heinz Global Production System (HGPS)), including leading change initiatives, planning, and facilitation
- Manage and evaluate the Quality Assurance staff including but not limited to performance management and employee development, etc
- Leverage Six Sigma tools and processes
- Inductive reasoning: The ability to combine pieces of information to form conclusions (includes a relationship among seemingly unrelated events)
- Pro-Active Problem Solving Approach: The ability to tell when something is wrong or is likely to go wrong
- Deductive reasoning: The Ability to apply general rules to specific problems to produce answers
- Multi-Task: Should be able to balance multiple projects at one time and prioritize to meet deadlines
- Ability to train salaried and hourly employees
- Grow and develop salaried personnel for Promotability
- Ability to Lead Teams and Team activities to achieve business results
- Advanced computer and presentation skills: Must be able to make oral and visual presentations to small and large groups that effectively communicate to the intended audience
- Quality Management Systems
- Food Safety Risk Management
- HACCP
- Sanitation and Environmental Monitoring
- Statistical Process Control and Data Analysis
- Technical problem solving (root cause analysis and corrective/preventive action development)
- Must demonstrate moderate knowledge of the following
- Managing raw material suppliers and incoming materials
- Food regulations
- Customer centricity
- The applicable processing method at the factory; e.g.: LACF, Acidified, High Acid, Frozen/ Chilled,
- Aseptic, and/or Pasteurization
- GFSI audit scheme implementation
- Incident Investigation and Reporting
- Must demonstrate basic knowledge of the following
- Scientific techniques for investigating complaints
- Microbiological and Analytical Methods
- Commissioning, Qualification, and Verification of new products / processes
- Minimum 5 years’ experience in Quality Assurance, Food Manufacturing, or other technical environment
- Supervisory and/or Managerial experience
- Demonstrate ability to work with cross-functional groups
- Demonstrate ability to supervise and train others effectively
88
Quality Manager Resume Examples & Samples
- The Quality Systems Manager is responsible for the implementation and execution of the Kraft Heinz Quality Chain Management System at the plant level, including distribution and local storage sites. It controls all products and processes in the plant, through strict adherence to policies, specifications, and standards. It utilizes methods, tools, and procedures to deliver zero defects from incoming raw materials to outgoing finished goods in a food safe environment. The position ensures that facility personnel are properly resourced and trained to efficiently and effectively execute their quality responsibilities. It leads Continuous Improvement of conformance quality and best in class cost of quality by utilizing L6S tools. The position has significant managerial responsibilities, including hiring and developing talent as well as budget management
- BS Food Science/Engineering/Chemistry or other relevant sciences
- CQE experience
- Food Safety and USDA Regulatory requirements
- Fundamental statistics (DMAIC Process/DFSS/Lean/metrology/MSA/sampling procedures)
- HACCP certified preferred
- Sanitation knowledge
- Development of quality knowledge for all plant employees; coaching, guidance, role model quality standards
89
Quality Manager Resume Examples & Samples
- ThisQA Mgr. will lead a team that ensures effective implementation and execution of the Kraft Heinz Supplier Quality Management System across an assigned product category. The position provides visible quality leadership ensuring that KFG supplier quality standards are understood and met through on-site assessments. This position also ensures that best practices are replicated across the category. This position requires travel up to 70%
- BS Degree in Food Science, Microbiology or other related field
- 5-10 years of experience in food or CPG industry is required
- 1-5 years of leadership/supervisory experience is required
- Lean Six Sigma to support Supplier Integration
- Fundamental statistics (DMAIC Process/DFSS/Lean/Metrology/MSA/Sampling Procedures)
90
Quality Manager Resume Examples & Samples
- KAM and OOH product guidance and use (40% time allocation)
- Establish the QA programs for trade Assets (beverage solution, Food quality)
- Define right sensory methodology for NP products at points of consumption
- Define the right quality monitoring scheme for NP products at the point of consumption (KAC shops)
- Provide quality supports to all KACs and NP Customers in collaboration with QSR team and CCSD team (15%)
- Participating in customer auditing schemes (when required)
- Yum star audit following up with NP factories in collaboration with Market quality function
- Drive end to end quality improvement for Nestle Professional products (30% time allocation)
- Customer complaints handling procedure optimization in collaboration with Market Quality function
- Customer compliant investigation (in collaboration with market quality function and factory team)
- Correctly setting, monitoring and managing, enforcing and maintaining the quality system in supply chain in collaboration with Market Quality function
- Business Review of Quality for Nestle Professional
- Ensure the co-manufacturing activities comply with Nestle Standards (15%)
- NFSMS (Nestle Food Safety Management System) is implemented at Co-Manufacturers
- Well acquired Problem Solving Skill
- Fluent English both in speaking and writing
- Networking skills
- Listening and convincing skills
- Can communicate in English both speaking and listening
91
Quality Manager Resume Examples & Samples
- Ensures the effective implementation of the quality program at the program/project level
- Ensures that the appropriate materials and equipment are supplied
- Provides program/project specific indoctrination and training to the quality program
- Monitors quality assurance activities to determine conformance with corporate policy and procedures
- Establishes and maintains client relationships at program/project levels to assure free communication of information and reasonable resolution of quality problems so that quality goals are attained with minimal rework and repair
- Performs periodic audits and assessments of the effectiveness of the quality program on programs/projects of the business unit/business line
- Provides periodic reports to the Director QA/QC and the program/project manager regarding the effectiveness of the quality program on programs/projects of the business unit/business line
- Prepares program/project specific quality plans and procedures, under the direction of the Director Quality to ensure that the appropriate elements of the Quality Management Program Manual have been addressed
- Prepares the quality scope definition for proposals as directed by the Director Quality
- Has formal supervisory responsibilities
- Working Knowledge of Microsoft Office Suite
92
Quality Manager Resume Examples & Samples
- Leads the site quality organization to ensure quality standards are implemented and sustained
- Assures raw materials, packaging materials, finished goods & distribution activities meet specifications
- Provides technical guidance & works closely with Corporate Quality, R&D, & local Manufacturing & Distribution on major new product introductions & acquisitions
- Represents plant to regulatory agencies
- Selects, trains, develops, retains & manages associates
- Works cooperatively with Plants, Distribution, Engineering, R&D & Corporate Quality to identify root causes of quality issues & implement processes to resolve & prevent issues
- Generates & implements ideas that improve quality indicators, in line with cost, investment & service goals
- Maintains Quality Management System and the sites ISO 9000 certification
- Leads internal & external audits & provides training on auditing tools to associates
- Sets up & administers audit system for internal & external providers of products
- Works with Purchasing to qualify and rate local vendors of raw materials, packaging materials & finished goods
- Provides quality system performance updates to local plant management and corporate management
- Bachelor’s degree in Chemistry, Chemical Engineering or related scientific area
- 7+ years quality experience in chemical manufacturing or R&D
- Experience with regulated (EPA and/or FDA) product manufacturing
- Immigration sponsorship not available for this role
- Demonstrated experience in the Quality Pillar of Total Production Management (TPM)
- Advanced technical or business degree
- Strong written & oral communication skills and experience with ERP and electronic specification systems
- Expertise in ISO 9001, GMP & in managing quality improvement projects
- Manufacturing supervisory experience & regulated production expertise
- Experience with CAPA System plans and records
- Lean Six Sigma Green Belt or Black Belt certification
93
Quality Manager Resume Examples & Samples
- Bachelor’s degree in chemistry, chemical engineering, or closely related physical sciences
- 5+ years experience in a chemical manufacturing environment in a related industry, including specialty chemicals, food products, or health and hygiene products, working with mixing and packaging equipment
- 2+ years experience in quality management
- No Immigration Sponsorship available for this opportunity
- Mainframe and/or PC experience and computer literacy
- Motivated to develop personally and professionally; willing to assume other position for developmental purposes and to relocate
- Working knowledge of QC practices and quality assurance tools such as SPC, CpK, pareto diagrams, scatter diagrams, histograms, cause and effect diagrams, etc
- Strong computer literacy including extensive computer skills with experience in Word, Excel, Powerpoint, and Access
- ISO experience in an internal auditor role
- Experience in the specialty chemical industry or related industries such as food processing, pharmaceuticals, or health and hygiene products
- Experience in other functional areas of operations, including production, distribution, planning, or purchasing
- Experience in R&D or process engineering
- CQE with ASQ
- Experience managing quality or production in a regulated production environment
- TQM orientation
94
Quality Manager Resume Examples & Samples
- Manage and Improve Quality Systems
- Prior experience in chemical manufacturing
- Proven interpersonal/leadership skills & the ability to interact with people at all levels of the organization
- Proven problem solver (process ad quality improvement problems) and Six-Sigma Black Belt preferred
- Some knowledge of Lean Principles and the Toyota Production System
- Experience managing ISO system, iPEC Excipient cGMP requirements and Quality Lab
- Proficiency in MS Office, SAP preferred
95
Quality Manager Resume Examples & Samples
- Effectively hire, motivate, supervise, and develop the Quality organization
- Lead Quality Engineers, Quality Inspectors, Auditors and Calibration/Metrology personnel in achieving department and company goals
- Formulates, plans, and implements systems and assigns resources for establishing Quality Assurance priorities in support of the total work effort within the company, ensuring on-time delivery of quality products
- Plan, organize, direct, and control organizational elements to ensure the efficient functioning of the Quality department, the accomplishment of quality assurance and company goals or policies, and the innovative support for business development activities, including proposal development
- Prepares responses to RFI’s, RFP’s, and ROM’s. Develops budget estimates, writes task descriptions, and summarizes Quality activities in accordance with requirements
- Makes quality a central element of the program culture, ensuring that quality is a central focus of design
- Ensure that quality assurance processes, tools, techniques and technologies are planned and implemented in the context of a program’s engineering functions and design processes
- Interfaces with a cross-functional team, including all business and project offices, and maintains effective and professional relationships with each
- Responsible for the effective oversight of subcontractors’/vendors’ Quality organizations
- Interface with customer quality management and government inspectors, ensuring a good working relationship and proper interpretation of contract requirements
- Implement quality goals and perform metric trending for customer reporting and continuous improvement
- Responsible for the development and implementation of Quality Management System processes, ensuring compliance and continued certification to ISO 9001 and AS9100 requirements
- Leads the audit team for both internal and subcontractor/vendor audits, ensuring that vendors are approved per contract requirements. Also serves as the primary point of contact for customer audits of the Quality Management System
- Prepares and presents reports on quality metrics, including trend analyses and corrective actions, in support of customer requirements
- Manage the nonconformance reporting (NCR) system, ensuring timely and effective closure of reports
- Assumes accountability for quality processes within the business segment
96
Quality Manager Resume Examples & Samples
- Plans, coordinates, and directs the quality control program designed to ensure continuous quality of maintenance service consistent with established standards
- Implements and maintains a quality management system program-wide in accordance with the applicable ISO Standards
- Analyzes develops, evaluates, advises and promotes improvements in logistical programs
- Establishes program objectives or performance goals and assesses progress
- Manages all aspects of ISO compliance and the establishment of internal processes/controls
- Ensures quality standards established in the contract are met
- Plans, schedules and coordinates (preparatory, initial and follow-up tasks) to ensure all required audits/inspections are performed and documented
- Define corrective measures for any problem areas identified
- Conducts special evaluations, quality surveys and audits. Compiles reports and findings of surveys and audits for review and makes corrective action recommendations as required
97
Quality Manager Resume Examples & Samples
- Develop the Construction Manager’s Quality Management Plan
- Audit the implementation of the Construction Manager’s Quality Management Plan
- Oversight and auditing of the Contractors Quality Management Plan implementation,
- Review testing, inspection plans and reports to verify compliance with contract requirements
- Document non-conforming work through the issuance of a Non-Conformance Report (NCR)
- Manage audits and inspections
- Verify that corrective actions have been implemented by the contractor
- Verify that all work has been corrected prior to recommending closure of an NCR
- Audit the contractor’s project records as required to verify compliance with the contractor’s approved Quality Management Plan
- BS in Engineering, Architecture, or Construction Management
- 10-15 years of construction experience, preferably in a QA/Inspector role
- (5) years of experience in providing QA/QC services for heavy civil construction projects, including experience in managing audits and inspections
- Experience providing quality management services for power & way renewal or facility renewal projects on an existing, operating transit system preferred
98
Quality Manager Resume Examples & Samples
- Gather the necessary documents and reports in order to present them at time of inspection or at any other time to the CHDO Inspector. These documents shall include, but are not limited to, work order packages, purchase orders, training records, and calibration records
- Work with the Accountable Manager establishing standards to ascertain that adequate safety
- Related work experience shall be a minimum of 5-10 years
- Experience with the policies and procedures of the following regulatory agencies; FAA, EASA, and DOT, relative to Aircraft Fire Suppression and Safety Systems including Oxygen and Stored Energy Systems
- Proven team player who has demonstrated capabilities in the following areas: excellent communication, presentation, leadership and interpersonal skills, well developed problem-solving skills; solid organizational skills; and the demonstrated ability to be self-directed and effectively relate to all levels of an organization
- Looking for a hands-on individual with the ability to see the big picture
- Ability to work well under pressure, multi task and meet deadlines
- Demonstrated ability to set goals and objectives to meet Business Unit expectations
- Computer skills to include Word, Excel, PowerPoint, and Quantum experience a plus
- Is appropriately certified under 14 CFR Part 65
- Implement and maintain a quality management system (QMS) by flowing down customer/government quality clauses & requirements into internal procedures, i.e. a sustainable QMS that supports Business Unit objectives via ISO 9001/AS 9100 certifications
- Coordinate internal quality audits and report status of QMS compliance to management
- Participate on cross-functional teams to implement Operational Excellence Initiatives (6 Sigma, Continuous Flow Manufacturing, 5S, Kaizen, etc.) in any manufacturing shop
- Provide status of internal and external corrective actions; ensure responses are adequate to prevent recurrence of nonconformance and report progress to management
- Has a thorough working knowledge of the applicable parts of 14 CFR that govern repair station operations
- Understands Airworthiness Directives and their application
- Understands manufacturer maintenance manuals and other data acceptable to the FAA
99
Quality Manager Resume Examples & Samples
- The Quality Manager will provide leadership, expertise, and continuous improvement to the Quality Assurance function in the factory. Lead the development, implementation, and maintenance of the factory Quality Management System in compliance with the Heinz North America Quality Management System. Assure that all products processed, packaged, stored, and distributed are manufactured in compliance with all Regulatory, Customer, and Heinz requirements
- Develop and administer the factory Quality Management System in accordance with current protocols and provisions, as defined in HNA Quality Management System Program
- Serve as the factory primary contact for all customer’s and third party audits, including management, preparation, and corrective actions
100
Quality Manager Resume Examples & Samples
- Participate as an active member of the Quality Advisory Board
- Develop standard operating procedures, work instructions, forms, and local operating procedures
- Manage all aspects of audits including
- Prepare and submit yearly audit plans
- Report audit findings to appropriate management with request for root cause analysis and corrective action
- Review and approve root cause and correction action plan. Perform follow up as needed
- Close out audits
- Maintain audit files
- Prepare and submit required monthly reports to the Operations Manager/Director of Quality
- Represent Intertek during 3rd part audits/assessments
- Advise management on training and implementation needs
- Monitor, control, and consult in support of compliance and continuous improvement efforts
- Report metrics results to the Director of Quality/Operations Manager
- Audit and qualify subcontractor service providers
- Participate in and support periodic quality system management reviews
- Monitor, coordinate, report, and close out internal and external complaints
- Provide timely responses for client feedback and metrics initiatives
- Oversee Metrology activities, i.e. instrument calibration and certification
- Bachelor’s Degree in Chemistry, Chemical Engineering, Biology, Bio-Chemistry or Physics
- Minimum of two years related quality or operations experience
- Experience in a regulated environment such as Pharma, Food, or Test Labs is desired
- Ability to read, analyze and interpret common scientific, technical, and engineering reports, standards and journals
- Successful completion of auditor training, ISO/IEC 17025 (preferred), ISO 9001, or equivalent is desired
- Knowledge of regulations related to operations, i.e. cGMP, GLP, HAACP, FDA, ISO, etc
- Ability to communicate effectively in both verbal and written format
- Ability to travel 25%+
101
Quality Manager Resume Examples & Samples
- Managing the Transportation Quality Program including the coordination of the team of Quality Network Individuals located in most of our offices across Canada
- Assisting in the development of a new National Quality Program for all business lines
- Implementing the new National Quality Program in all Transportation offices across Canada including providing the training associated with its implementation
- Liaise and regularly meet with other corporate quality management staff; assist in periodically updating quality procedures and policies
- Direct and oversee timely Quality Audits to ensure project services and deliverables meet Quality Plan requirements and prepare corresponding reports
- Direct and oversee the preparation and submission of project quality documentation to clients, and when necessary, prepare and submit the quality documents personally as required
- Direct, oversee and/or identify and document non-conformances and manage Corrective and Preventative Actions in accordance with WSP's Quality Program
- Provide QC process and procedures training to staff
- Provide QC procedures guidance and support to office and field staff
- Identify and recommend improvements to the National QA/QC documents and procedures
- Participate on project teams as Quality Manager and Auditor
- Assist design teams in developing Project Specific Quality Plans
- Liaise with clients regarding quality management matters, including maintaining and updating quality plan registrations
- Develop/maintain Quality Community of Practice
- Maintain and manage client's interactive quality portals and systems including MTO RAQs for the Transportation Business Line
- Produce and present regular reports summarizing the results of QC/QA training, implementation, auditing and all other activities undertaken or recommended
- Undergraduate degree or college diploma in an engineering, or quality assurance discipline or related field
- Registration as a Professional Engineer is an asset
- Minimum 5 years of related experience in a project environment, including understanding and implementation of quality management principles and procedures (ISO 9001 or similar)
- ISO Internal / Lead Auditor certification from recognized service provider is an asset
- Bilingual in English/French would be an asset
- A self-starter with strong organizational skills and the ability to take initiative and work with minimal supervision
- Detail-oriented with strong analytical and problem-solving skills
- Experience with MS Office suite and other computer skills. Familiarity with road and highway design software an asset
- Strong interpersonal skills and the ability to communicate to all levels of the company
- Technical background in design or construction of roads, highways and related infrastructure a definite asset
- Some travel is required for the purpose of training at other offices or site audits
102
Quality Manager Resume Examples & Samples
- Site Quality Head, this position is the appointed Management Representative
- Ensure that the operations, processes and procedures that affect products quality and/or integrity comply with ISO 9001, ISO 13485 and 21 CFR 820 including but not limited to: customer complaints, quality metrics, approval and release of finished products, incoming inspection of raw materials, management reviews, internal audit program, host external regulatory, corporate, and customer audits, quality holds, customer notifications, market corrections or withdrawals, non-conformances and CAPA system, quality support for Design Control and New Product Introduction, QA Validation and equipment lifecycle support, Change Control, Customer requests and interactions (C of As, Quality Surveys, Quality Agreements)
- Interact both vertically and horizontally in a way that commands both personal respect and mission acceptance and possess the ability and interpersonal skills to influence all levels of the organization
- Interact with Customers and Suppliers, when required, including hosting of customer audits, applying these same attributes as required to promote external relationships and properly represent the interests of Thermo Fisher Scientific
- Manage a team of Quality Engineers and Quality Assurance professionals providing meaningful and timely training, development and feedback to enhance their growth
- Experience in a quality role governed by International Standards ISO-9001, ISO-13485 and/or 21 Code of Federal Regulations (CFR) Part 820 Food and Drug Administration (FDA) Quality Systems Regulation (QSR)
- Bachelors Degree in Scientific field (i.e., Chemistry, Biology, Bio-Medical, Engineering)
- Thorough knowledge of the medical device or pharmaceutical requirements
- Experience in world class Quality practices including LEAN Leadership methodologies, root cause analysis, preventative action deployment and quality function tools
- Experience in leading teams in the implementation of quality improvements systems resulting in reduced cost and cycle times with improved quality of products and services
- Analytical ability is require to make competent decisions based on review of analytical data
103
Quality Manager Resume Examples & Samples
- Drive the CAPA-process, Non-Conformity Handling and Out-of-Specification processes according ISO 13485 and also ISO 14971 requirements
- Implement and support Risk Management and Complaint Handling activities
- Implement EDMS Solution as replacement of a paper-based CAPA system
- Establish Quality Dashboard / Key Performance Indicators to monitor measures/actions and CIP processe
- Interface for CAPA-Product Care activities, coordinating and monitoring compliance activities
- Head of CAPA-Board; control all CAPA, NC and OOS activities during the whole Product Lifecycle for Freiburg
- Project Lead to establish Electronic Data Management System for CAPA, NC and OOS process (Short -/Mid-Term Solution)
- Project Lead for implementing MasterControl System, as required by ThermoFisher (Long-Term Solution)
- Bridge Person to Risk Management and PPI activities
- Subject Matter Expert for the Freiburg site for CAPA, Non-Conformity and Out-of-Specification processes
- University degree/certificate or Master (health science, biology, biochemistry area)
- Fluent English (written and spoken)
- 3-5 year experience in GMP business, preferred Diagnostics or Medical Devices
- Experience in IT applications, preferred EDM-Systems and Excel
- Experiences with CAPA and Continuous Improvement Processes, 8-D Problem solving and Risk Management according ISO 14971
- Potential for manager position in 1-3 years
104
Quality Manager Resume Examples & Samples
- Leadership & management of all Quality Functions including Sustaining Quality Engineering; Reliability Engineering; Receiving Inspection; and Calibration
- Demonstrate improvements in overall Quality, Delivery, and Productivity of products within Platforms
- Provide leadership by promoting team concepts, coaching, counseling, retaining, mentoring, training, talent management, and individual development
- Drive a culture of accountability and results through strategy deployment and effective performance management
- Establish the key strategic activities required to align the Platform manufacturing to the achievement of Zero Harm, Zero Defects, Zero Late Deliveries, and Zero Waste
- Ensure full support for Monroe budgetary targets, and specifically develop and achieve Monroe manufacturing budgetary plans
- Develop a continuous improvement philosophy with goals and timelines
- Design, implement and maintain processes necessary to create a quality management system, which meets international standards. Prepare Quality Reviews for management
- Evaluate and improve key business processes; such as, Customer Complaint, Warranty, Service Level
- Manage a process which generates a Master List of product quality issues and includes a method of prioritization, regular communication and closure verification
- Conduct regular surveys with customers, both within LSP and externally to gather opinions and information on the quality of products and services
- Manage a process to measure and improve product reliability and quality by evaluating trends, failure modes and opportunities. Work with responsible departments and teams to improve results
- Design, manage and improve the New Products Quality Planning Process. Measure and evaluate new product field performance and replacements; initiate corrective action and improvement programs as required
- Develop and support quality related communication and training programs
- Interface effectively with internal and external customers to provide the highest level support
- Maintain and develop the emphasis on ownership and accountability throughout the department
- Promote and support health and safety guidelines
- Communicate, liaise and negotiate internally and externally using appropriate methods to facilitate the development of profitable business and sustainable relationships
- 8-10 years in Quality Assurance, Manufacturing or Industrial Engineering
- Proven management experience and strong track record of achieving strategic business objectives within a senior operations role
- Strong understanding and experience using Six Sigma and Lean Manufacturing Principles (Six Sigma certified preferred; GB or BB)
- Demonstrated understanding and experience with ISO & OHSAS requirements
- Demonstrated understanding of poke-yoke implementation in design and manufacturing
- Demonstrated results with directing reliability engineers and writing test procedures to validate and verify design / process requirements
- Familiarity and general understanding of P&L principles
- Strong communication skills – very customer focused
- Strong problem solving techniques, experience with 8D problem solving
- Strong computer and data collection system literacy, analysis and presentation
- Ability to prioritize and organize tasks
- Experience and overall understanding of MRP/ERP systems
- Highly driven for results
105
Quality Manager Resume Examples & Samples
- Bachelor degree in Bio-science or management or engineering required
- Understand industry regulations
- 8 years experiences on quality management, 3 years on managerial role, 5 years in multi-national company
- Fluent speaking, reading, listening and writing in English
- ISO9000/ISO13485 internal auditor certified
- Must be able to multi-task
106
Quality Manager Resume Examples & Samples
- Support the safety program in assuring a safe working environment for all employees. Initiates action and follow up on all safety concerns raised by employees. Ensures all employees under his/her direction clearly understand all safety rules and regulations, appropriate training has been received and work performance is in accordance with all applicable OSHA and EPA regulations
- Ensure that processes needed for the Quality Management System (QCMS) are established, implemented and maintained
- Establish continuous improvement activities which will deliver reduction in consumer complaints and ongoing process control improvement
- Facilitate external and internal assessments related to Quality programs and regulations affiliated with accreditation processes
- Act as the primary liaison between corporate Quality/Sanitation and the Chicago Bakery
- Responsible for direction, implementation, and maintenance of the facility’s food safety and regulatory programs
- Ensure that processes needed for the Sanitation Program are established, implemented and maintained
- Ensure that processes needed for the Pest Control Program are established, implemented and maintained
- Develop and implement Quality Improvement agenda
- Develop quality goals and targets in alignment with plant/business goals and strategy
- Meets quality assurance financial objectives by estimating requirements; preparing an annual budget; scheduling expenditures; analyzing variances; initiating corrective actions
- Provide leadership and technical assistance to operation by aggressively managing food safety and compliance system, instilling regulatory awareness and commitment
- Support the commercialization process and provides technical expertise for the Quality perspective
- Provide quality support for plant projects and initiatives in the manufacturing environment
- Build and lead high performance teams who share common visions, goals, metrics and who collaborate, challenge and hold each other accountable to achieve outstanding results
- 5 years experience in Quality Systems (Design and Manufacturing Quality)
- 5 years experience as a leader in a high team environment
- 5 years experience leading and managing a diverse work force
- 3 years experience in Regulatory & Compliance
- 2 years experience Continuous Improvement
- 2 years experience Quality IT Systems
- Be cognizant and knowledgeable of quality standards and models
- Be strategic, methodical, logical and detail oriented
- Be an excellent communicator
- Be multitalented and able to perform different roles
- Have good supervisory, management and networking capabilities
- Have superior mathematical and numeric skills
- Have proficient interpretation skills for figures, statistics, regulations and policies
- Be able to investigate, document, and maintain records accurately
- Be extremely professional, customer friendly and amenable
107
Quality Manager Resume Examples & Samples
- Management of Quality Engineering, Inspection, Calibration, Dynamometer, Auditing, Test Lab and Configuration Control functions to ensure carbon quality meets customer and FAA requirements
- Assure the preparation, retention, and control of all objective evidence of conformance to requirements including records of inspection, test, process control, audit, etc
- Conduct and/or supervise studies to determine the cause, effect, and corrective measures necessary to remedy quality deviations
- Plan, organize, and coordinate implementation of quality improvement activities
- Accountable for establishment and control of an annual budget for the Quality Department
- Enforces compliance to UTAS Internal Policies (e.g. Business Conduct, EEOC, EH&S, Security, etc.) within the Quality Department
- Responsible and accountable for setting departmental short and long-term objectives that support and meet the strategic long-term objectives of the business
- Manage capital projects within and across departments and/or business units
- Accountable for the control of output, control of quality performance, budget development and spending, labor efficiency, and human utilization to provide a continuous reduction in product cost and a corresponding increase in quality and on-time-delivery
- Responsible for evaluating subordinates’ performance
- Define/communicate duties, responsibilities, authority, and accountability of all direct reports. Identify training needs, nurture, challenge and develop all direct/ indirect reports in their positions and preparing them for career opportunities
- Create and implement new techniques and procedures including development and the implementation of process improvement methods in the assigned areas
- Responsible for coordination of activities inside and outside the assigned areas of the Quality Departments including adherence to purchase order requirements
- Consults with all segments of management responsible for policy or action and ensures compliance within area of responsibility. Provides recommendations for improving effectiveness of policies and procedures
- Reviews and interprets UTAS, customer and FAA specifications and requirements for product acceptance
- Perform and oversee basic quality functions (i.e. internal and external audits, assisting in conducting corrective action investigations) necessary to support areas
- Establish business objectives, set Departmental goals (cost, quality, etc.) and assist in removing obstacles to complete those goals
- Interaction with the FAA, Troy Quality and Engineering Organizations, and other Carbon Products Quality and Engineering organizations
- Drive program issues to a resolution
- Provide decisions on the acceptability of material as far as meeting fit, form, or function
- Manage and assure the site’s Quality Clinic program is effective and maintain its certification status
- Provides leadership to Quality and manufacturing organizations on product compliance, customer, and UTAS business expectations
108
Quality Manager Resume Examples & Samples
- Responsible for sites regulatory compliance. Ensure that the Plant is working according to the Quality Assurance procedures as outlined in the Site and Corporate Quality Manual (ISO 9001), including as appropriate, excipient, food ingredient, nutraceutical & cosmetic ingredient cGMP
- Responsible for developing, implementing and approving Quality Assurance policies, pocedures and processes to assure regulatory compliance
- Optimise resources within the QA/QC function to provide an effective and uninterrupted service level
- Routinely, measure, trend and report quality performance
- Provide valuable problem solving and project management abilities to lead or participate in continuous improvements in product quality, cGMP compliance and the quality management system
- Serve as standards and regulatory resource for quality issues, providing guidance to plant management
- Lead the site audit program, publish an annual plan, facilitate customer audits and ensure follow through on the schedule and remedial actions
- Evaluate & provide change management approval, as appropriate
- Corrective and Preventive Action (CAPA) Management
- Assure that the CAPA process progresses and improves the QMS
- Manage quality disposition of global inventory sourced from the facility
- Manage product stability program
- Build organizational strength. Ensure all employees have clear objectives and feedback, complete appraisals and establish development needs to support the business
- Oversee the site Quality / GMP training program
- Promote a zero incident culture
- 10 years + in the specialty chemical, food additive or pharmaceutical industry, mostly within the Quality/technical/regulatory functions
- Must have cGMP, risk management, validation, auditing and quality management systems approach
- Must have 3 to 5 years supervisory/management experience
- Manufacturing operations and laboratory experience desired
- IPEC, USP, BRC, EXCiPACT, FSMA, HACPP knowledge and ISO900 certification programs is an advantage
109
Quality Manager Resume Examples & Samples
- Organizational Development: Develop and maintain an effective work force of quality assurance/engineering personnel to facilitate accomplishments of quality assurance goals. Responsible for proper training of employees as well as development of employees’ skills and abilities for more responsible positions
- Establishment of Specifications and Standards: Develop appropriate information and participate in the establishment of quality specifications and standards for raw materials and for process and finished goods. Coordinate with Engineering and Manufacturing personnel to ensure product standards are in accord with all testing, certification, and standard requirements
- Quality Control Procedures and Techniques: Develop recommend and implement inspection and sampling techniques, quality control plans or process control procedures that will ensure production of acceptable products
- Research: Direct and assist in conducting research on product defects in conjunction with engineering personnel and recommend modifications to meet product quality standards
- Product Relations: Work with technical engineering assistants or suppliers when necessary to confer on and help alleviate specific quality problems. Review customer complaints/job problems or supplier problems to determine validity and initiate corrective action
- Technical Assistance: Provide quality assurance expertise to materials management personnel engaged in the procurement of raw materials, supplies and equipment
- Receiving and Inspection Functions: On an indirect basis (dotted-line responsibility) review, revise and insure that receiving and inspection functions at all Cooper-Fluorescent Operations facilities are performed in a manner that meets the quality standard
- Quality Awareness Training: At the direction of the Fluorescent Division Management, plan and implement quality awareness training for all Cooper-Fluorescent Operations employees through utilizations of the Quality Facilitator and other management employees
- Quality Improvement Actions Teams: At the direction of the Fluorescent Division Management and through the activities of the Quality Engineers, organize, assist and train Quality Action Teams to develop solutions to quality problems
- Quality Improvement Departmental Action Plans: At the direction of the Fluorescent Division Management and through the activities of the Quality Engineers assist department managers in developing and implementing a quality action plan for their department
- Manufacturing System Implementations: As directed by the Fluorescent Operations, plan, develop and coordinate the implementation of new manufacturing systems
- Bachelor’s degree from and accredited institution
- Minimum Three (3) years of Quality experience in a manufacturing environment is required
- Minimum Two (2) years leadership or management experience in quality, manufacturing, or engineering
- Quality Management System knowledge and experience (ISO 9001, TS16949)
- Knowledge of machining, assembly operations, problem solving, gauging, process capability, SPC, APQP, and quality management systems ISO/9001:2008
- Experience using PC configured with MS Windows OS and Office software is desired
- Knowledge and experience with AIAG Core Tools (SPC, PFMEA, PPAP, APQP, MSA, QSA)
- ASQ Certified Quality Engineer (CQE), Certified Quality Auditor (CQA), Six Sigma Greenbelt (CSSGB) is preferred but not required
110
Quality Manager Resume Examples & Samples
- Ensure Continuous improvement of the Quality Leading Indicators strategy including the best practice refinement
- Develop, implement and monitor performance against short and long-range plans to achieve quality engineering objectives
- Main point of contact for Customers for any Quality
- Own the customer scorecards for quality
- Implement short and long-range plans relative to quality assurance
- Identify needs, and develop the quality engineering function
- Develop or modify quality procedures, metrics and processes to achieve quality and on time delivery goals
- Select and develop competent quality engineers and in plant auditors to ensure quality goals are achieved
- Provide reports as required and drive corrective action and preventive action for timely and effective completion
- Assist as required in all technical qualify functions as necessary
- Assure effective communication and reporting to customers
- Assure compliance with control phase of quality systems and initiatives such as internal auditing, statistical process control and testing
- Provide support and leadership to Quality Organization in new product development
- Support the development and utilization of quality feedback tools to maintain and implement "lessons learned"
- Support the achievement of Cost of Quality, goals as identified by the Plant Manager
- Minimum 5 year’s experience in a Quality position
- Minimum 3 years experience in a management or leadership role
- Thorough knowledge of Divisional policies, objectives and procedures regarding detection and analysis of product nonconformance to specification. Basic understanding of statistical quality control, and Eaton Engineering systems, components and product applications
- Thorough knowledge of cost control techniques as they apply to the total quality concept, budgeting and fixed asset planning for return on investment
- Administrative skills required to guide product quality, employee involvement and productivity programs
- Highly developed human relations, communications and internal consulting skills necessary to establish and maintain effective work relationships with the various plant functions and Division staff, customer and supplier personnel, and to promote and motivate employee involvement in, and acceptance of, new methodologies, etc
111
Quality Manager Resume Examples & Samples
- Managing team activities
- Ensuring that day to day tasks are on track and maintained
- Setting of goals in line the business needs
- Build on team strengths ensuring that business requirements are met
- Identifying and promoting procedure improvements
- Liaising with internal and external customers on quality related activities
- Driving improvement through Quality best practices
- Hosting and maintaining regulatory approvals EASA part 21 / EASA part 145 / TCCA / FAA / CAAC
- Hosting and conducting internal / external audits
- Supporting product investigations
- Facilitation of PPAP, 8D, FMEA FRACA, PFMEA
- Drive improvements through CI and quality analysis
- Generation of Quality metrics
- Development of team
- Educated ideally to degree or equivalent in a quality or engineering related discipline
- Understanding of Key quality tools (six sigma, gauge R & R, etc)
- Regulatory knowledge as well as AS9100
- Knowledge of all auditing techniques
- Change management
- Lean manufacturing
- CI tools
- Lead auditor
- Supplier controls
112
Quality Manager Resume Examples & Samples
- Deploy quality plan at the operational level in conjunction with the Division Quality group to provide overall quality leadership to the site
- Transform the organization from one focused on conventional detection and containment to one focused on best-in-class prevention
- Guide, direct, maintain and monitor all activities associated with the successful application of Eaton Business Excellence
- Provide support in Total Quality Leadership to customers, suppliers, business partners, and the other support service functions such as, materials, mfg. Engineering, Information Technologies, and other Division resources
- Manage the Quality strategy to facilitate continuous production of products consistent with established industry standards, government regulations and customer requirements
- Implement systems and processes that deliver improvement toward 100% conformance to customer requirements
- Drive rigorous metrics related to the BSC to evaluate performance and drive reduction in variability/defects in critical business processes
- Develop systems for managing supplier performance. Provide Quality interface, expertise and support to the organization’s suppliers and partners
- Build relationships with other Division and Corporate resources in order to support identification, review, prioritization and execution of key improvements opportunities/projects to drive results
- Provide a leadership role in the plant’s continuous improvement activities
- Minimum 5 years’ experience in Quality Management in a Manufacturing environment
- EBE Examiner or organization leader
- 6 Sigma qualification
113
Quality Manager Resume Examples & Samples
- Develop and implement a OpEx organizational structure capable of supporting the strategic initiatives of the local Plant and lead the efforts to integrate quality needs into the development of short and long-term improvement plans. This includes leading/supporting the operation in the implementation and improvement of the local Quality Management System and Lean/Six Sigma initiatives
- Provide Quality interface and expertise between the operation and its customers to proactively identify or anticipate their needs and expectations and ensure they are understood and satisfied. This includes the complaint management system and the corrective/preventive action process related to customer issues – with feedback (Customer and Division) – and the coordination of customer visits and audits
- Develop a thorough understanding of the Eaton Business System (EBS) with expertise in the tools related to OpEx (e.g. – EQS, OpA, EBEA, EPM, Ethics, Vision, Mission, Values, Philosophy, Organizational Capability Assessment, and Corporate Accounts). Appropriate levels of this knowledge must be transferred to all subordinates as part of their personal development
- Lead the deployment and integration of the Eaton Quality System (EQS) into the local Quality Management System
- Analyze key organizational quality and continuous improvement metrics related to EPM (e.g. – Customer Returns DPPM, Internal Quality, Scrap, Warranty, Cost of Nonconformance, and Supplier Quality) and perform periodic reviews to evaluate results and establish action plans to close the gaps at an operational level
- Actively participate as a member of the leadership team in the deployment of the Eaton Business System (EBS) tools process to integrate initiatives into an overall comprehensive site strategy
- Provide support to the Supply Chain Management organization relative to Supplier Quality activities of the operation as well as provide Quality interface, expertise and support to the organization’s suppliers and partners. This includes the feedback of supplier performance to suppliers and the Division
- Lead the internal Quality System Audit program for the organization and manage the corrective action system in conjunction with the management review process
- Provide expertise in Quality Assurance and process improvement tools/methods to the other functions of the organization to support them in their continuous improvement activities
- Recommend new or leading-edge technologies, methods, tools and procedures on the fields of quality assurance and continuous improvement to proactively address changes in the business environment
- Develop and analyze statistical data and product/process specifications to determine standards and establish proposed quality and reliability requirements for the finished product
- Manage the performance and provide career development opportunities to all the employees within the OpEx function of the organization. This includes the development and implementation of training programs to build “bench strength” in the organization
- Manage the budget of the OpEx organization
- Lead the development and implementation of the site Lean and Six Sigma strategy, actions, and cross-functional activities to eliminate waste, drive customer satisfaction, reduce cost, and improve working capital performance
- Provide Lean and Six Sigma support across the organization to drive short-term and long term business improvements by identifying performance gaps in assessments such as OpA, EBS Pull, EBEA, etc. and work with the leadership team to prioritize improvement activities and close gaps
- Promote plant wide culture of continuous improvement and learning and facilitate cross-functional continuous improvement teams and other project teams to accomplish improvements throughout the facility
- Bachelor’s degree in engineering or business from an accredited institution required
- Minimum of 5 years of experience in manufacturing, manufacturing engineering, product engineering, or quality assurance
- This position requires use of information or hardware which is subject to the International Traffic in Arms Regulations (ITAR). All applicants must be U.S. persons within the meaning of ITAR. ITAR defines a U.S. person as a U.S. Citizen, U.S. Permanent Resident (i.e. ‘Green Card Holder’), Political Asylee, or Refugee
- 2-3 years of manager of people experience
- Lean/Six Sigma training or certifications
- Previous role in Quality Assurance
- Quality Management System experience
114
Quality Manager Resume Examples & Samples
- Plan, develop and initiate positive actions to improve product and service Quality that Eaton provides to its customers
- Develop and integrate quality performance measurement systems, considering world-class benchmarks and report results to operation management
- Apply principals and initiatives of the Eaton Quality System and Eaton Business System to the plant’s business and manufacturing processes for continuous improvement
- Develop, implement and maintain corporate quality policies, procedures, and instructions
- Assist, approve and communicate major problem corrective actions face to face with customers
- Coordinate and lead the “Fresh Eyes” audit process for the plant
- Bachelor or Master degree preferred in Mechanical Engineering or equivalent
- 7 years of experience in Automotive Engineering or quality environment and 5 years supervisory experience
- Thorough knowledge of ISO/TS 16949:2002 requirements and statistical process control techniques
- Knowledge of manufacturing processes and procedures including lean manufacturing tools
- ASQ Certified Quality Manager and/or ASQ Certified Quality Engineer is preferred
- Fluent in English and Italian
115
Quality Manager Resume Examples & Samples
- Provide leadership in achieving plant quality objectives with adequate planning, organizing, integrating, measurement and analysis of plant quality performance
- Manage the company Quality system and co-ordinate with other departments according to company SOPs and guidelines
- Lead cross-functional team do internal audit and process audit
- Conduct effective quality meetings within functional departments. Monitor and follow up C/P actions Work closely with others in Operation, Logistic, and Sourcing to ensure the Orders are completed according to quality standard
- Evaluate pre-shipment inspection results and determine the disposition of products while communicating with inspection staff, and suppliers
- Investigate customer complaints, identify corrective actions at technical aspects and work with suppliers and sales team to implement
- Build and develop Quality team. Evaluate the performance of Quality team members and be responsible for their performance
- Plan and implement annual budget approved by the plant management team for the sake of cost control
- Issue Weekly/Monthly reports, Quarterly Sales meeting report for manager team review
- As the plant quality functional leader, coordinate plant resources to fully deploy EQS system. (Eaton Quality System)
- Satisfy customer requirements through the use of the EQS. (Eaton Quality System)
- Set up and deploy international Quality Management System (such as ISO 9001, TS16949). Lead 3rd party certificate process
- Bachelor’s Degree in Engineering, or any related discipline or equivalent experience
- At least seven years related quality management experience preferably in electronics manufacturing environment
- Must have working knowledge of quality systems including ISO 9001 / TS16949 & basic skill of statistical methods used to analyze and control products variations, capability studies, Gage R&R’s, Control Planning and FMEA
- Must have working experience with layer process audit, internal and process audits, certified lead auditor for ISO/TS preferred
- Failure analysis skills and familiar with failure analyze tools e.g. turn on and off, DOE, repeat and simulation, process mapping
- Customer issue handling experience, knows how to effectively lead and communicate with various function team/s
- Leads customer audit, assessment, query response
- Lean manufacturing experience, with several lead project that using 6 sigma tools to achieve the lean / cost out on manufacturing process
- Ability to work effectively with others and be a participative team player, self motivated, result-oriented, knows how to handle several conflicting issues and projects while getting positive results
- Strong experience in Quality tools, PPAP, FMEA, APQP
- Strong leadership skills
- Skills on time management, project management, and supplier management
- 6-Sigma certification-green below / black belt is preferred
- With experience in a high mix organization
116
Quality Manager Resume Examples & Samples
- Develops the plant quality training plan and leverages EBS resources for execution of training plans. Provides for training on related Quality Tools, Systems, and Processes such as
- Drives the principles of a performance-based organization. Analyzes quality performance, sets the plant goals for all quality metrics, and cascades goal setting through APEX to individual goals and development plans. Ensures alignment with the parent-organization defined strategy. Performs managerial reviews to evaluate results and establishes action plans to close gaps
- Leads the implementation and improvement of the Quality Management System to foster a culture of customer focus and continuous improvement while maintaining compliance with internal and external requirements. Serves as the Management Representative on ISO-based requirements. Participates in enterprise forums and teams to improve the Quality System
- Actively works with all appropriate levels of the Supply Chain / Supplier Development organization to ensure quality of purchased products and services meets Eaton requirements
- Develops, implements, and manages a product warranty system that captures and provides feedback to responsible departments and assures permanent corrective action to support the delivery of quality products that enhance customer satisfaction
- Other Responsibilities assigned by immediate manager
117
Quality Manager Resume Examples & Samples
- Manage the preparation, implementation, and maintenance of a Quality Management System to comply with the published plant Quality Manual and the global divisional vision for quality
- Develop and implement strategic projects to continually improve the overall Quality of products, information and services
- Interface with customers, suppliers, partners, and internal stakeholders in both the plant and at customer locations to enhance their perception and understanding of the plant Quality systems. Facilitate customer Quality audits and inspections as appropriate to demonstrate compliance
- Develop, coordinate, and implement process improvements at Eaton Golf Pride in addition to training programs relative to the Quality Management System
- Manage the development and implementation of statistical feedback programs and attribute inspections required to effectively evaluate the Quality Management System
- Act as the management representative managing ISO 9001 certification activities including authority on ISO 9001 requirements. Develop, implement, and manage a product warranty system that provides feedback to responsible departments and assures permanent corrective action
- Accountable for QA duties and has the authority to take the necessary actions to resolve Quality issues
- Manage Incoming, Final and In-Process inspections necessary to ensure Quality products to customers. Drive error-proofing solutions at the source to address issues found during inspections
- Lead the deployment and support of the Eaton Quality System throughout the organization. Provide Quality leadership and support in development of new products, processes, and services (PROLaunch). Lead plant Supplier Quality activities to ensure the incoming Quality of purchased materials
- Analyze organizational Quality metrics and perform Management Reviews to evaluate results and recommend countermeasures to close gaps at the operational level
- Develop and maintain an appropriate departmental budget and ensure the operation of the Quality Department within budget. Evaluate the performance of the Quality Team to facilitate performance management, merit increases, promotions, job transfers, disciplinary action, etc
- Minimum five years’ experience in Quality Engineering
- Minimum two years of leadership experience of a quality function
- Demonstrated ability to communicate effectively in Mandarin and English both written and verbally
- Bachelor's degree in Engineering from an accredited institution
- Six Sigma Greenbelt certification. (Blackbelt a plus)
- Four years Quality Management experience
- Two years of people management experience
- Two years working in an environment using and understanding of ISO9001 requirements
- Identify, evaluate and implement cost effective resolution of complex Quality issues arising in sales, engineering, materials, and manufacturing
- Rapid response to permanently resolve customer product warranty issues which may include identifying the customer’s own improper application or operation of product shipped
- Facilitate Field Campaigns and develop containment actions to replace suspect materials shipped over a period of time which minimizes impact to customer operations
- Plan and direct field retrofits or equipment upgrades at customer sites
- Solutions often require in-depth research and understanding of product design, supplier processes, and customer application to properly achieve resolution of Quality and product warranty issues
- Ability to find and liaise with external test laboratories for specific testing when required
- Passion for quality and attitude in problem solving. Demonstrated performance results, and a continual improvement mindset
- Strong analytical skills and understanding of creative problem solving techniques/tools
- Possess good interpersonal skills and a team player
118
Quality Manager Resume Examples & Samples
- Develop and deploy the Quality strategy for the Filtration Division supporting the implementation of global Hydraulics and Industrial Sector Quality programs and goals
- Drive continuous improvement efforts through Quality Functional Reviews, the deployment of the Eaton Quality System and Self-Assessment, Balanced Scorecard (EPM), and other quality tools including Six Sigma
- Provide support in Total Quality to customers, suppliers, partners and the support service functions of the organization
- Ensure the Filtration Division plants comply with applicable Eaton, customer, and industry-specific
- Quality requirements by conducting the necessary audits and assessments to determine system effectiveness
- Manage the implementation of Six Sigma in accordance to Corporate and Group guidelines
- Ensure the Filtration Division plants comply with applicable Eaton, customer, and industry-specific Quality requirements by conducting the necessary audits and assessments to determine system effectiveness
- Champion the Eaton Quality System (EQS) within the Division. Identify and lead initiatives across the organization to address common barriers for the plants and enable improvement in effectiveness and efficiency
- Overall ownership of the Quality Alert and Escape Management process for the Division. Ensure
- Timely escalation and communication of customer quality escapes and work with Group, Plant Quality /OpEx, and Supplier Development colleagues to ensure appropriate containment, root cause, and corrective actions are undertaken with the utmost urgency
- Bachelor’s degree in Engineering (Mechanical, Industrial, etc.), business or similar
- Solid experience in senior quality function in a manufacturing industry
- Ability to drive results in the area of Quality, continuous improvement, etc
- Experience in a role with multiple site responsibilities is preferred
- Demonstrated knowledge of quality assurance and continuous improvement
- Methods, approaches and tools, including strategic management and project
- In-depth experience with the practical application of Quality tools, Six Sigma,
- And Lean Manufacturing methodologies
- Demonstrated knowledge of Quality Management Systems such as ISO-9001,
- TS-16949, AS-9100 etc
- Ability to work in a matrix environment, get results, and drive change through others
- German
119
Quality Manager Resume Examples & Samples
- Supervises workers engaged in inspection and testing activities to ensure high productivity and high technical integrity. First-Time In-Process Quality
- Develop and analyze statistical data and product specifications to determine standards and to establish quality and reliability expectancy of products. Provides technical and statistical expertise to teams
- Ensure participating groups adhere to quality policies, plans, and work instructions
- Participate in meetings and negotiations with customer, programs, and cross-functional teams/management
- Participates in surveillance of subcontractors’ manufacturing processes and controls subcontractor quality performance system
- Develops customer courtesy visits and communication schedule, and completes accordingly
- Serves as liaison between Customer and facility
- Interfaces with both customer and subcontractors as required in such areas as: APQP, Part Number Control Plans, PPAP
- Reports and analyzes quality metrics including NCRs, CARs, and 8Ds
- Communicates and continuously improves in-process quality—ppm, gage R&R, and cpk
- Develops course of action with Management, Quality Engineers, and Cross-Functional Teams for evaluating complaints and resolving problems
- Develops, and implements TS16949 Certification Action Plan thru manuals, related documentation meetings, and training. Performs consulting on all aspects of TS16949
- Serves as TS16949 Management Representative for the facility
- Sets quality performance goals and metrics
- Reviews quality concerns with engineering personnel, and assists with action items to correct defects. Prepares periodic and special reports concerning departmental activities, problems, subcontractors’ quality system, schedules, and rejected items
- 10+ years of Quality Supervisory/Management experience in a plastics/molding environment
- Technical Capacity—Problem solving, root cause analysis, SPC, and Measurement Systems analysis—measuring equipment and gages
- Understanding of inspection methods—CMM, micrometers, calipers, and thread gauges
- First-Time In-Process Quality philosophy
- Performance Management
- Computer Literacy—Microsoft Office, and Mini-Tab software
120
Quality Manager Resume Examples & Samples
- Driver of cross-functional operational excellence and works with plant and corporate staff on process improvement activities and projects
- Ensures conformance to ISO standards by managing the internal and external audit program
- Works directly with Purchasing Department and suppliers when issues arise from supplier quality
- Works directly with OEM customer quality assurance staff when solving customer quality issues
- Maintains quality compliance by developing and enforcing plans, programs, policies, procedures; managing audits; qualifying vendors; evaluating documentation; developing improvement plans; preparing and delivering training courses, as needed
- Reports on Cost of Quality
- Reports on achievement of Quality Objectives
- Responsible for daily/weekly monitoring of customer scorecards and online portals
- Demonstrated track record of implementing new and better ideas, driving best practices and benchmarking externally
- Experience and proficiency with technical drawings, specifications, APQP, and the OEM core tools
- Possesses a thorough understanding of ISO standards, Lean and Six Sigma methodologies
- Updates job knowledge by tracking emerging trends in manufacturing practices, and regulatory requirements; participating in educational opportunities; reading professional publications; maintaining personal networks; participating in professional organizations
- Champions the Company’s Quality/Environmental Policies and Objectives
- Promotes overall awareness of the Company’s Quality & Environmental Management Systems
- Proven organizational and planning skills; excellent written/verbal presentation and listening skills with the ability to present complex technical information in a clear and concise manner to a variety of audiences
- Proven ability to communicate difficult/sensitive information tactfully
- Understands basic revenue models, P/L, and cost-to-completion projections and makes decisions accordingly
- Responsible for Arkansas Quality Assurance Department budget
- Assists strategic business leaders in quality and operational improvement as it relates to business strategy
- Proven ability to inspire coworkers to attain goals and pursue excellence
- Identifies opportunities for improvement and makes constructive suggestions for change
- Strong partner with other key functions
- BA or BS degree, in a technical field, preferable
- Minimum 5 years’ experience in comparable manufacturing/distribution environment
- Must be wiling to travel 25 – 30%, including international (as necessary)
- Preferred experience working in the automotive industry or with automotive industry customers
121
Quality Manager Resume Examples & Samples
- Strong leadership competencies
- Must be able to interact positively and communicate effectively with all levels of the organization
- Must have a high degree of initiative, influence, and problem-solving capability
- Requires regular, dependable attendance
122
Quality Manager Resume Examples & Samples
- Must have a thorough understanding of the Code of Federal Aviation Regulations (CFAR), FAA requirements, AS9100/AS9110 standards, and European Aviation Safety Administration (EASA) regulations. Must be able to train others
- Must be able to apply a thorough knowledge of inspection practices, and procedures in the field of aircraft repair, assembly and installation
- Must be able to demonstrate knowledge of quality policies, engineering procedures, blueprint reading, continuous improvement techniques, shop procedures, and shop planning
- Must have a working knowledge of precision measuring equipment, functional and continuity test tools/equipment, and be familiar with shop mathematics, including decimals and fractions
- Must have intermediate computer skills, and be able to operate various software programs, such as MS Word, Excel, PowerPoint, Outlook, etc
- Must possess an advanced knowledge of technical data information systems, blueprints, aircraft manuals, CAD drawings, manufacturer manuals, material specifications, process specifications, regulations, as well as other pertinent information
- Must have the ability to properly balance good compliance practices with other business initiatives to avoid conflict, and allow all objectives of the business to be satisfied
- Demonstrated problem solving skills, using root cause analysis tools
- Must be able to work effectively across functional boundaries, and have demonstrated time management skills in order to handle multiple priorities
- Must possess excellent communication skills, both written and verbal. Must also possess excellent interpersonal skills
- Must have the ability to utilize computer systems, including input of data and retrieval of information for inspections, configuration purposes, and data analysis
- Must have the ability to effectively present information to team, local GMT, and personnel at all levels of the organization
- Must possess the ability to define problems, collect data, establish facts, and draw valid conclusions
- Good understanding of Lean principles and/or ACE tools preferred. Ability to lead continuous improvement events preferred
- Ability to provide verification of US Citizenship or permanent residency to satisfy ITAR/EAR restrictions
- Must read, write, speak & understand the English language
- Ability to work under pressure and within time constraints
- Ability to work cooperatively with supervisors, co-workers, customers, and others in a team environment displaying mutual trust and respect
- Ability to be regular and predictable in attendance
- Ability to sit, stand, walk, reach, twist, climb, crouch, stoop, kneel, and lift up to 10 pounds for 8+ hours per day
- Ability to follow rules and policies of the company
123
Quality Manager Resume Examples & Samples
- 3-5 years' experience in a manufacturing or production environment, 2-5 years' experience in Quality
- Demonstrated experience managing a team of direct/indirect reports
- Basic understanding of the Carbon Manufacturing Process and plant operations preferred
- Knowledge of and background in AS9100 is preferred
- Skilled in computer applications such as the MS Office Products
- Basic Mechanical and Electrical understanding
- Strong work ethic and motivation and ability to work with limited supervision
- Ability to problem solve, exercising creativity with practical solutions
- Sound administrative skills
- Proven ability to recruit, train, and motivate personnel in order to balance staffing strength with profitability and growth
- Ability to pass pre-employment physical and drug screen
- Ability to read, write and communicate effectively in the English language
124
Quality Manager Resume Examples & Samples
- 3-5 years of working knowledge of FAA regulatory requirements for repair stations (FAR 145 including knowledge of FAR 21, 43, and 121 subpart L)
- 3-5 years experience managing quality personnel and complex activities
- Strong quality systems background
- Six Sigma and or CQE preferred
- Expert level root cause investigation and analysis
- Must have strong technical writing skills and a strong work ethic with demonstrated leadership, business judgment, innovation, teaming skills, and communication skills
125
Quality Manager Resume Examples & Samples
- Bachelors in Engineering or related technical field
- At least 8 years of experience in Quality, Manufacturing and/or Engineering with a minimum of 5 years in the aerospace industry
- Demonstrated ability to interface with all levels of management and external customers Defense Central Management Agency or FAA)
- 8 years of experience in using quality tools to make process improvements in a manufacturing environment
- MS or MBA are highly desirable
- Knowledge and experience with Six Sigma and process control tools
- Leadership background with ability to lead projects, develop and mentor other leaders
- Responsible for communicating within a large manufacturing environment
- Experience in supervising bargaining unit hourly associates is highly desired
126
Quality Manager Resume Examples & Samples
- Coordinates the development and the administration of the site’s Design Quality Assurance and NPD QA Sustaining Engineering programs
- Identifies the opportunities for improvement of the Product Development Process and initiates activities to support the improvement process
- Participate in the development of the new products and processes, issues resolutions and design reviews participation
- Formulates quality engineering policies and procedures
- Manages, supervises and provides direction to quality engineers on professional, personnel issues, and provides development opportunities
- Participates on teams, projects and assignments, facilitating or leading teams as necessary
- Manages department budget
- Provide guidance to test methods, equipment acquisition, sample plan definition, and validation development
- Participate in technical documentation of the international submissions
- Assures product and process adherence to applicable medical device and electrical safety standards
- Presents data to upper management related to departmental metrics and key project milestones
- Bachelor's degree plus 7-9 years of related quality and/or design assurance work experience in the medical device industry or an equivalent combination of education and work experience. Advanced degree preferred
- Strong interpersonal/management skills
- Demonstrated experience with Design Assurance
- Strong Collaboration skills
127
Quality Manager Resume Examples & Samples
- Works with the Production Unit Team to run production / repair operations / service in a manner which ensures service level and quality goals are met
- Provides Quality Engineering support for production / repair operations issues; addresses non-conformances through the NCEP system, driving PIR escalation and PIR processes when risk level warrants it
- Collaborates with cross-functional teams on new product introductions, transfers, and sustaining projects with a focus on Design for Manufacturability / Testability / Reliability / Serviceability
- Leads Quality Planning activities related to transfer projects, acquisitions / divestitures, QMPs & other site projects as needed
- Drives improvements in product quality based on out-of-box failure / complaint / service data analysis
- Leads corrective and preventive actions as required; proactively identifies and executes on opportunities for preventive actions
- Leads cost reduction projects, using Lean / Lean Business Process methodologies; contributes annually to the VIP savings program through Quality-driven projects as well as supporting projects driven by other functions
- Ensures successful outcomes for factory / product safety inspections by external notified bodies
- Participates in site internal and external audits; acts as Subject Matter Expert in Quality Engineering processes
- Contributes to Quality Management Reviews
- Leads, coaches, and develops department team members as necessary to support changing business needs
- Ensures training plans and records for direct reports are compliant to Company-specific policies
- Assumes shared responsibility and accountability for the continuous improvement and performance of the business
- Experience with major systems (e.g. eCAPA, PDM, SAP, CRD, Filemaker, VIP, Clarizen) desirable
- Substantial understanding of Capital Equipment and Service business model and associated processes preferred
128
Quality Manager Resume Examples & Samples
- Qualification level and discipline: Educated to Degree level. Post Graduate qualification in Quality Assurance desirable
- No. of years work experience: 10+ years
- Industry type: Medical Devices or other similar regulated industry with a certified Quality Management System
129
Quality Manager Resume Examples & Samples
- 2-year degree from an accredited university in Business Administration, Hotel and Restaurant Management, or related major 3 years experience in the guest services, front desk, housekeeping, sales and marketing, management operations, or related professional area
- Responds to and handles guest problems and complaints
- Models service behaviors that meet or exceed guest expectations
130
Quality Manager Resume Examples & Samples
- Monitors and advises on how the system is performing, which may often include the publication of statistics regarding company performance against set measures
- Determining how customers’ expectations will change over time and what the organization needs to do to meet these changing expectations
- Responsible for supporting the development and maintenance of a guests-focused culture within the organization
- A knowledge of statistics is required with general numeracy, coupled with good interpersonal skills and requires the ability to assimilate and analyze information
- Must be flexible in terms of working hours
131
Quality Manager Resume Examples & Samples
- You will be responsible for monitoring the organization’s compliance with Part-145, and requesting remedial action as necessary by the Operations Manager or the Accountable Manager
- You will be an independent function and reports directly to the Accountable Manager and will be directly accessible to and for Certifying Staff
- You will perform management responsibilities for the QA department, for example: hire/fire, disciplinary actions, PMP, salary adjustments, work assignments, approving and scheduling vacation
- You are to ensure functions at the QA Department who are performing work affecting product quality are knowledgeable on the basis of appropriate education, initial/continuation training, skills and experience
- You will develop strategic plans for the continuous improvement of Quality, Health, Safety and Environment
- You are to achieve monthly BSC objectives on relevant AES levers
- You will collect, analyse, and summarize quality-related information and trends to prepare reports on product and process quality
- You will attend the daily Stand-Up meeting Maintenance Projects
- You will interpret EASA regulations into company policies and procedures and maintain the MOE
- You shall act as a liaison between BAN B.V. and CAA-NL on all matters pertaining to the Part-145 approval and continued airworthiness
- You will issue requests for capability extension (aircraft and aircraft components) when required, including the evaluation of the 4 M’s and notify CAA-NL of changes
- You will implement a quality audit program, in order to monitor compliance with all implemented standards, among which Part-145
- You will gather and compile data from audits and report to the Accountable Manager
- You will raise Quality Issue Reports (QIR) and monitor that any observed non-compliances or poor standards are brought to attention of the person concerned via his/her manager and that corrective actions are taken
- You will report un-airworthy conditions to operators, manufacturers and competent authorities
- You will issue and withdraw Part-145 Certification Authorisation document to/from Certifying Staff
- You will perform other duties as assigned
- You have many years’ experience in quality management
- You hold a Bachelor degree or working level in Business, Aviation, Engineering or related field
- You poses an Initial audit course
- You have thorough knowledge of applicable EASA regulations, and have held a CAA Form 4 Post Holder position as a Quality Manager
- You have working experience with In-Service, certificated business aircraft processes, certification and programs
- You have several years working experience as a Quality Manager within a Part 145 organization
- You have the ability to promote the safety and quality policy
- You have thorough knowledge of process improvement methodology and application
- You have thorough knowledge of Environmental, Health & Safety rules, Human Factors, Human performance/-limitations, and regulations as they apply to safety and environmental aspects of aircraft maintenance operations
- You have interpersonal skills necessary to develop and maintain effective communication with employees, customers, and all levels of management
- You have presentation skills necessary to effectively communicate, update, persuade, and/or facilitate discussions and training
- You poses research and analytical skills necessary to collect, analyze, and interpret the quality management system processes, and survey data, among which customer satisfaction surveys
- You have previous experience with SAP, which is an asset
- You have working knowledge of non-EASA regulations applicable to MOE supplements to other authority / CAA agreements (e.g. FAA / TCCA / Bermuda) which is preferred
132
Quality Manager Resume Examples & Samples
- Act as the lead project QA
- Manage Sub-Contractor’s Quality team
- Establish necessary processes and procedures for quality assurance including its implementation in the organization
- Audit and review the projects and project processes
- Review inspection and test plans and verify alignment with quality requirements
- Initiate necessary actions to mitigate quality risks and non-conformance’s including the reduction of Non Conformity Costs
- Initiate and perform continuous improvements within projects for quality assurance
- Manage measuring, analysis and reduction plans for Non Conformity Costs and other critical quality measures
- Improve and implement work processes and methods to assure customer satisfaction
- Establish and follow up project specific Quality plans and quality gates
- Perform audits and carry through improvement measures with suppliers and Project Core Teams
- Bachelor's Degree in Engineering preferably in Mechanical, Electrical, Process discipline or equivalent
- 8-10 years of relevant track record experience in railway systems and/or signaling are essential
- Interest of technique, products and good working experience preferably with experience in the areas of quality, construction, procurement or production
- Practice in quality and product revision is qualifying
- Experience from working with projects, products and suppliers
- Experience from working with operational development and change management
- Large initiative power, very good ability for cooperation and to rake own decisions
- Good knowledge of English. Further language knowledge is seen as qualifying
133
Quality Manager Resume Examples & Samples
- Prepares reports for Management about effectiveness of Quality Management System and recommendations for improving it
- Responsible for continued Quality Management System compliance and alignment
- Responsible for the mentoring, training, motivation and discipline of assigned employees
- Participates in the Quality and Lean/Six Sigma organization's strategic planning process, develops long-term plans and ensures appropriate skills are available when needed
- Develops, assists in the evaluation, and implements changes in work operations and processes to improve compliance with company policies and the quality management system
- Coaches and champions teams, leads multi-discipline and/or cross-functional teams
- Advises management on trends, returns, vendor performance, audit results and corrective actions
- Works with Engineering during development to advise on design-in quality issues and to provide input for quality planning
- Works with the Purchasing Department on vendor selection, development and control to achieve specified quality of received materials and products
- Ability and comfort with accurately speaking, reading and writing in English
- Demonstrated planning and leadership skills
- Self-motivated team leader with the ability to lead and sustain improvement activities
- Excellent organizational, communication (written and oral) and presentation skills
- Proficient in Microsoft Office software program. Ability to be trained in usage of manufacturing applications
- Familiar knowledge of basic lean manufacturing methodologies including: Kaizen, workplace organization, just in time principles, visual management and value stream mapping
- Must be able to communicate effectively at all levels of the organization
- Must be willing to travel on an ‘as needed’ basis when business demands or customers require so
- Must be able to maintain composure while under intense pressure and deadlines
- Must be able to work effectively with minimal supervision
- Ability to multi-task and manage multiple projects
- Excellent responsiveness and customer focus
- Strong motivational and team development skills
- Demonstrated success in employee relations and leadership
- Approachability -Easy to talk to, able to put others at ease
- Directing Others -Sets direction, distributes work, lays out clear plans, is organized
- Interpersonal Savvy -Relates well to others and can build rapport across the organization
- Motivating Others -Empowers others, creates a climate in which people want to do their best, shares ownership and visibility
- Sizing Up People -Good judge of talent; sees the importance of effectively using each person’s strengths
- Organizing -Able to orchestrate effective use of all available resources
- Planning -Ability to develop schedules and task/people assignments
- Priority Setting -Able to quickly zero in on the critical few leaving the trivial many
- Building Effective teams -Knows when and how to use teams and uses them effectively
- Managerial Courage -Takes appropriate action when necessary; faces up to problem people or situations
- Fairness to Direct Reports -Treats employees as adults and maintains equitable relationships
- Drive for Results -Reliable performer who can be counted on to achieve consistent results
- Bachelor’s degree in Engineering or related STEM course
- 5 -7 years of Quality Management experience in a manufacturing environment
- Previous experience building a strong and positive team environment
- Previous experience managing and achieving budgetary requirements within a department
- Previous experience recommending and initiating corrective actions
- Six Sigma Black Belt or Green Belt
- Bilingual in English and Spanish preferred
- ASQ certifications for one or more disciplines
134
Quality Manager Resume Examples & Samples
- Develops and maintains a quality plan for service center operations, including service quality standards, quality scorecards, monitoring, coaching, performance metric assessment, and improvement actions
- Manages a team of Quality Assurance Monitors and/or Specialists by establishing roles, work standards, performance objectives, and enforcement through regular oversight
- Ensures team standards for quality service center are achieved and initiates improvement actions when necessary
- Facilitates calibration activities and works collaboratively with training and contact center operations personnel to ensure consistency in quality service requirements
- Monitors and reports service center performance against service level agreements and performance standards, initiating improvement actions when opportunities are identified
- Analyzes performance trends and takes proactive steps to prevent service shortcomings
- Develops and conducts quality-related training
- Reports performance information through formal and informal reports that may be contractual deliverables
- 8-10 years of related experience in call center monitoring, quality assurance, and/or customer service
135
Quality Manager Resume Examples & Samples
- Provide subject matter expertise in quality control and compliance matters to Service desk, client SOW and/ or functional areas in the daily operations of the Service desk
- Work with senior managers and account teams to ensure that their quality control objectives are met
- Provide coaching, training and facilitation in quality, process and control across the Service Line
- Contribute significantly to quality policies, targets, plans and standards at the Business Unit Level
- Identify and implement improvements in the quality control and improvement mechanisms that have an impact across multiple service lines, Drive improvements in the quality governance and control framework
- Support readiness activities for Group Internal Audits
- Appropriate Quality management certificates
- 3-5 years of Quality Management experience in IT
- Experience working in an outsourcing and service delivery environment
- ISAE 3402 Fundamentals/Introduction certificate
- ITIL,ISO 9001, 20000, CMMi Intermediate certificates
- ISO27001,14001 Foundations certificates
136
Quality Manager Resume Examples & Samples
- Must have an active DoD Secret Security Clearance and must maintain eligibility throughout the terms of employment
- Requires at least 5 years of experience performing quality control in an industrial environment
- At least 3 years of experience in administrative, professional, analytical or other work related to International Organization for Standard (ISO) ((9001)(14001)) programs or operations is required
- Must possess knowledge to maintain a quality management system in accordance with the applicable ISO Standards
- Requires broad knowledge of Army logistical functions and the ability to analyze, develop, evaluate, advise or promote improvements in logistical programs
- The ability to establish program objectives or performance goals and assess progress and establish operational metrics/key indicators for process control and on-going quality process improvements is required
- Must conduct root cause/corrective action analysis
- Previous supervisory experience in an austere OCONUS environment with a multi-national workforce
- US Citizenship, a valid US or local driver's license and US passport
- Certified in specific trade, or maintenance journeyman/master technician
- Must be able to fluently read, write, speak, and understand English
- Ability to obtain/maintain Secret clearance
- Experience providing excellent customer services
- Ability to work in a fast-paced environment that requires handling multiple tasks at a given time and rapidly adapting to changing priorities and schedules
- Ability to become an active and functioning member of a team
137
Quality Manager Resume Examples & Samples
- Creates and maintains a Quality Management System (QMS) that delivers a consistent quality service for Digital Forensics that meets our contractual commitments
- Develops and maintains a log of ISO 17025 registration status for each FSP. Where this has not yet been achieved by an FSP then the Quality Manager monitors the FSP’s progress toward achieving registration
- Initiates development, reviews and approves procedures and work instructions consistent with the QMS
- As a registered assessor for ISO 17025 provides guidance and advice to FSPs seeking registration as a compliant organisation
- Attends the Service Management Board to report on quality matters. Prepares and receives actions to resolve quality issues identified
- Owns and maintains the quality plan
- Ensures that service deliverables match quality and legal compliance requirements and customer expectations
- Identifies opportunities for service improvement
- Reviews and approves all proposals for project, changes and R&D work
- Carries out quality assessments of FSP deliverables
- Monitors the quality of training delivered and the competency assessments of students
- Remains up-to-date with developments in ISO 17025 and other ISO standards which may be relevant for the contract
- Develops relations with the Forensic Regulator and customer QA team to develop best practice in the performance of the contract
138
Quality Manager Resume Examples & Samples
- Demonstrated deep SQA expertise as part of large and complex systems integration programs
- Previous experiences driving teams and processes from the ground up (ie. with no existing tools or processes in place)
- Outstanding communication and listening skills
- Proven ability to keep calm under high pressure situations involving time sensitive mission-critical software releases
- Demonstrated EDI transaction knowledge
- Successful track record of long-term, collaborative relationships with partners across the entire SDLC process
- Command of knowledge of compliance and audit responsibilities as they relate to system testing deliverables
139
Quality Manager Resume Examples & Samples
- Manage the preparation, implementation, and maintenance of a Quality Management System to comply with the published plant Quality Manual
- Develop and implement strategic projects to continually improve the overall Quality of products, information, and services
- Develop, coordinate, and implement training programs relative to the Quality Management System
- Develop, implement, and manage a product warranty system that provides feedback to responsible departments and assures permanent corrective action
- Accountable to performance of QA duties and has the authority to take the necessary actions to resolve any Quality issue
- Coordinate between Engineering Services, Sales & Marketing, and plant operations to ensure a systematic process is in place for warranty that maximizes customer resolution at a minimum cost
- Lead the deployment and support of the Eaton Quality System throughout the organization
- Provide Quality leadership and support in development of new products, processes, and services (PROLaunch)
- Minimum five (5) years’ experience in quality, manufacturing or engineering
- Minimum two (2) years’ of leadership experience
- Authorized to work in the United States without Company sponsorship
- Prefer ASQ CQE or CMQOE certification
- Prefer Six Sigma Blackbelt or Greenbelt certification
140
Quality Manager Resume Examples & Samples
- Maintains strong communication with customers, internal management team, and suppliers to ensure quality level is meeting expectations
- Develop, implement and execute product, process and program quality plans that assure conformance to customer, internal and regulatory requirements
- Develop, implement and execute quality improvement initiatives to align with and achieve macro plan & PDPR goals and objectives
- Initiate, monitor and execute quality improvement initiatives
141
Quality Manager Resume Examples & Samples
- Ability to work comfortably in a diverse environment that promotes teamwork to accomplish tasks
- Strong PC skills and proficiency in MS Office (Word, Excel, PowerPoint)
- Understanding and leadership of Quality Management Systems (QMS) and demonstrated application of measurement, analysis and ACE tools
- Communication skills, written and verbal, ability to communicate at all levels of the business, internally and externally with customers and suppliers
- Strategic planning and development skills, experience with policy deployment and macro planning
- Understanding of enterprise and regulatory agency requirements
- Customer, quality and continuous improvement focus
- Ability to support AS9100
- Demonstrated experience with customer focused activities and relationship development
- Legally authorized to work in the U.S
142
Quality Manager Resume Examples & Samples
- Team builder and problem solver
- Must be able to converse in Chinese and English
- Proven experience in a similar role
- At least 15 years of Automotive experience at OEM or Tier 1 level
143
Quality Manager Resume Examples & Samples
- Development and implementation of a site-specific Field Inspection and Testing Plan
- Providing sufficient resources to effectively conduct the project specific inspection and testing activities
- Assisting the inspectors in resolving issues relative to inspection and testing
- Verification that all inspection and test records are established and maintained in accordance with applicable procedures
- Supervising the activities of the Inspectors assigned to the project
- Verification of all personnel conducting inspection and testing activities are properly qualified and do so in accordance with the applicable procedures
- Assurance that all inspection and test records are completed and maintained in accordance with the applicable procedures
- Supervising inspection and testing activities as detailed in the Field Inspection and Testing Plan
- Preparing and issuing all reports as required by the Field Inspection and Testing Plan
- Verification, as required, that subcontractors have an effective QA/QC Plan, inspection and testing systems, equipment, and personnel in place to meet the stated requirements of their subcontract
- Performing random audits of contractor QA/QC Plans and related activities
- Communicating with site supervision, craft supervision, field engineering, clients, etc. regarding inspection and testing related activities
- Issuing Weekly reports to the Resident Construction Manager and Home Office QA/QC Manager
144
Quality Manager Resume Examples & Samples
- Establishes and expands intra-divisional interactions to develop/enhance a network of resources (laboratory, manufacturing, engineering, sales and marketing) to facilitate completion of programs
- Independently performs project planning. Establishes project objectives and priorities. May participate in quality strategic planning. Maintains an awareness of product/process quality improvement and scientific/product opportunities and is productive in evaluating ideas and making proposals
- Documents results, observations and conclusions in technical notebooks (or approved electronic files) and prepares reports to communicate results to appropriate personnel. Level of position classification is equivalent to that of a manager. May coach, counsel, and guide technicians, technologists, and engineers. Demonstrated ability to lead teams and projects. Functions as an effective team leader and promotes harmonious and efficient working relationships
- Employee has met the educational requirements of the T4 level and consistently performed at that level
- Professional quality certifications such as Certified Quality Engineer (CQE), Certified Quality Auditor (CQA), and/or Certified Quality Manager (CQMgr), through American Society for Quality (ASQ), are preferred
- Must have knowledge of TS/ISO 16949 certification and ISO 9001
- Individual must demonstrate the ability to establish, manage, and lead major projects of technical importance to the business. Knowledge and skills of scientific/engineering principles and the understanding of quality systems and the organization’s business are the basis of completing job expectations
- Implements a comprehensive education plan to develop, maintain, and expand state-of-the-art knowledge in areas of specialization. Systematically updates self and coworkers on emerging technologies and assists in development and motivation of other technical employees
145
Quality Manager Resume Examples & Samples
- Develop and implement tactics to achieve the divisional strategies
- Site quality metrics to support the site and divisional objectives
- Customer complaint coordination
- Supplier Management
- Maintain and improve the Quality Management System
- Develop the quality team
- Internal and Supplier auditing management
- Functional point of contact for Divisional Quality
- Calibration
- Demonstrable success in leading teams through successful improvement projects
- Good Understanding of ISO9001, PED and ATEX
- Highly computer literate
- Knowledge of Pressure Vessel manufacture
- Systematic approach to problem solving/experience of 8D
- Results orientated
- Independent, persistent and decisive
- Innovative
- ISO 9001(Quality Management System) auditing training
- Formal training on quality tools and techniques (Six-sigma training would be an advantage)
- A graduate in either a Quality or Engineering discipline
- Member of the Chartered Institute of Quality Assurance
- Quality Leader role in a low volume Mechanical Engineering organisation
146
Quality Manager Resume Examples & Samples
- Lead a team of Manufacturing/Quality Engineers
- Drive PPM to Best in class levels for analytical equipment through the development of new quality processes and continuous improvement on the existing program
- Work hand in hand with sourcing to improve vendor quality
- Oversee manufacturing hand off of New Product Introduction from commercial team
- Ensure product quality and performance conforms to company, customer and regulatory requirements
- Lead Site activities with department managers to improve first pass yield performance for key processes
- Support sustainment and continuous improvement of XOS quality databases/tools
- Develop, collect, analyze, and report quality data to identify process failures or opportunities for improvement
- Support the production team in resolving issues identified during production
- Interface with supply chain to disposition discrepant material and resolve quality
- Support quarterly business reviews, onsite audits, and other forms of communication
- Act as customer advocate when addressing quality issues by utilizing problem solving techniques to drive to root cause / corrective action for any escapes
- Lead Corrective and Preventive Action (CAPA) activities to drive quality/process improvements
- Support the Engineering Change Order (ECO) system from generation through implementation
- Respond to formal internal and customer issued corrective action requests
- Develop and maintain quality and control plans in support of an internal product development process
- Develop poka-yoke and fixturing strategies to be used in reducing process variation in assembly processes
- Perform training on workmanship specifications and quality system processes as necessary
- 3+ years in a quality-related discipline
- Prior experience working in a lean manufacturing environment
- Prior experience implementing root cause corrective actions and process improvements
- Experience working in an ISO:9001 and/or other regulated environment(s)
- Proficiency utilizing Microsoft Office
- Experience with regulatory requirements related to RoHS and REACH
- Developer of Access and/or SQL databases
- SQE Certifications
147
Quality Manager Resume Examples & Samples
- Bachelors or higher advanced degree in Biomedical, Mechanical, or Chemical Engineering, or related field
- 8+ years of related experience in Medical Device industry
- 8+ years of engineering experience
- 5+ years of experience with CAPA investigations
- Experience leading process improvement projects and conducting training with Quality to improve overall quality system compliance
- Auditing experience to the 21CFR820.200, 21CFR820.100, ISO13485, CMDR and the Medical Device Directive
- Working Knowledge of 21CFR820.30, ISO14971:2012 & IEC TR 80002-1, e.g. PRA, SHA, SFMA , DFMEA, PFMEA
- Comparative Statistical techniques & sampling plans
- Demonstrated ability to lead people and get results through others
- Demonstrated ability to organize and manage multiple priorities
- Ability to perform problem analysis and problem resolution at both a strategic and functional level
- Solid knowledge and track record in the application of Design Controls, Risk Management and Statistics towards supporting New Product Development and sustenance of Medical Devices
- Experience and excellent track record in effective communication, planning and cross-functional collaboration
- Experience in making critical decisions that prioritize patient care/safety and FDA regulations while supporting smart business decisions
- Effective team player with strong communication skills and track record of completing commitments with cross functional resources from R&D, Marketing, Regulatory Affairs, Manufacturing and/or other departments
- Strong data management skills
- Experience in Field Service
- Experience managing a team
- CQE certification preferred /ASQ certification in Quality Engineering desirable
- Training and/or certification in Six Sigma Black Belt, preferred
- Internal and External Audit experience, preferred
148
Quality Manager Resume Examples & Samples
- 8 plus years biopharmaceutical industry experience. Previous experience in the supervision of QA/QC activities is preferred
- Proactively addressing compliance issues and assuming responsibility for compliance deficiencies
- Actively leading “Lessons Learned” activities
- Ability to develop gap analysis and action plans
149
Quality Manager Resume Examples & Samples
- Manages both Quality Control and Quality Assurance personnel at the Ames, Iowa site
- Prioritizes schedules for testing and other activities in accordance with customers’ requirements
- Takes action to ensure appropriate quality systems are in place at all stages of manufacturing
- Reports quality results to Director and customers; reports any quality deviations immediately to all appropriate parties
- Oversees and assists with USDA submissions, especially Form 2008
- Coach QC and QA teams on best practices, quality principles and Merck leadership behaviors
- A minimum of 5 years industry experience in a biologics setting with supervisory experience
- Working knowledge of regulatory requirements in accordance with USDA manufacturing operations (9 CFR §113)
- Proven people development and coaching skills
- Excellent communication skills; able to communicate company and site strategies to direct reports and site employees
- Working knowledge of laboratory equipment in a biologic setting
- Proficiency in computer systems and applications including but not limited to: Microsoft Project, Microsoft Office (Word, Excel and Outlook)
- Must be able to lead in a team-based empowered culture
150
Quality Manager Resume Examples & Samples
- Participate in development of quality-related processes and tools
- Provide quality consultancy to Functional Leads, Line Manager and/or Project Leader/project leadership)
- Review and approve Production Batch Records and Test Records
- Perform and support P&E qualification/validation activities as appropriate
- Provide audit and inspection support as assigned. This may include: providing assistance/advice for audit/inspection preparation; representing Quality Management in audits and inspections as
- Attend (or where required, lead) internal quality-focused meetings
- Perform other assigned process, quality or training related tasks for particular workgroups (e.g. Line Managers, Leads) or project teams as assigned
- Relevant experience in the Clinical Research field (pharmaceutical industry or CRO), clinical or medical experience or other relevant experience
- Aseptic manufacturing experience required
151
Quality Manager Resume Examples & Samples
- Serves as owner for work processes supporting the Stability and Reference Standard programs
- Participates in Study Design and ensures scheduling of stability lots
- Manages existing stability studies through execution of the following
- Events management-coordination with CMO
- Provides QA Representation on Product Working Teams for
- Impact Assessment
- Issue communication and resolution
- Conducts Data analysis and authors trending reports
- Serves as SME for applicable studies during regulatory inspections
- Serves as Document Owner for procedures and work instructions in support of the Stability and Reference Standard programs
- Monitors regulations for changes that impact process, updates process as required
- Serves as Training Owner and SME for their process
- Serves as Reviewer/Approver or Owner of deviations to their processes
- Authors and/or Reviews/Approves SOPs to assess impact of change controls and at biennial review
- Identifies risks and communicates gaps to Quality System Owner
- Identifies and generates process related metrics- monitors for efficiency
- Provides both front and back room inspection support for their process
- Provides back room inspection support for stability and reference standard programs
- Serves as a SME on stability and reference standard programs and related processes-may train others on processes
- May generate metrics for stability and reference standard programs
- Reports risks related to stability and reference standard programs to Quality System Owner(s)
- Reports Events related to stability and reference standard programs
- Assesses stability requirements for new products and new dosage forms
- Provides stability data for regulatory filings
- Provides stability summaries for annual product review
- Authors Change controls
- Assesses stability impact on proposed changes
- CFR and EU regulations (ISO is nice to have)
- ICHQ1a-e
- Latin America/Brazil regulation preferred
- Pharma / small molecule experience preferred
- Experience with analytical methods
- Experience with stability programs
- Coursework and/or practical experience with statistical analysis tools/techniques
- Proven ability to lead improvement projects
- Proven ability to identify and analyze process metrics
- Proven ability to design, develop and deliver effective training
- Experience with electronic systems such as
152
Quality Manager Resume Examples & Samples
- Adhere to safety policies and procedures related to all facets of the job
- Generate reports off HFA system in order to identify areas where improvement opportunities exist
- Working with location staff to identify/correct problems with manufacturing quality
- Responsible for the compilation and reporting of the quality control check findings
- Responsible for daily quality checks/inspections anywhere on the floor
- Develops/revises standard operating procedures
- Evaluate department personnel using the Milgard Performance System
- Develop and manage the department's annual budget
- Develop and improve the department's investigative, data collection, and reporting capabilities
- Ensure required testing is performed for maintenance of AAMA certification
- Ensure incoming material is inspected and conforms to standards
- Ensure systems are in place for identifying, reporting, and processing of non-conformant materials and products
- Ensure that special testing requirements are met
- Provide investigative and research reports on Quality issues
- Communicate with outside vendors and customers on quality concerns
- Ensure that returned product is processed and logged for credit
- Provide training and investigations to internal and external customers
- Prepare and conduct training and informational presentations and documents
- Participates in the Leadership Development Program (LDP) for the location
- Responsible for developing people, improving processes, and reducing costs
- Incorporates Milgard’s vision and values into day-to-day activities and behaviors; guides and motivates others to remain committed to the Milgard Philosophy
- Minimum five (5) years related experience and/or training
- Manufacturing experience is a must
- Quality system development and implementation (Six Sigma or TQM) required
- Demonstrated track record of quality improvement
- Read, write and understand the English language
- Ability to read, analyze, and interpret financial reports and legal documents
- Sense of urgency and self-motivation; ability to work independently
- Ability to motivate employees to achieve results
- Computer literacy with ability to learn new computer software programs
- Excellent written and oral communication skills; ability to present to senior management
- Attention to detail with strong organizational skills
- Ability to respond to common inquiries or complaints from customers, regulatory agencies, and members of the business community
- Must possess ability to apply basic concepts of algebra and geometry and an ability to improve processes
- Must be results oriented with a people development affinity; proactive in attacking challenges and confident in setting and achieving stretch goals
- Must be able to teach and generate results while enhancing the Milgard work environment and supporting the Company philosophy
- Must have proven employee development and team building skills
153
Quality Manager Resume Examples & Samples
- Quality and Technical Auditing of Company activities
- Attending and reporting on Management Review Meetings
- Following up of all corrective and preventive action, to a satisfactory conclusion
- Liaising with managers on Quality matters
- Liaising with representatives of regulatory and certification bodies
- Writing of processes, procedures, work instructions etc
- Resolving complaints to a satisfactory conclusion
- Undertaking training and support activities
- To promote the Company’s Quality Procedures and to support the business managers in the Operational, Sales and Administration teams within the region
- Monitor regulatory and other changes and emerging issues, and communicate with branches to inform them of relevant changes and the required responses
- Maintain Quality networks internally and externally with industry and professional bodies for the benefit of information sharing and maximizing the use of resources where indicated
- Working with the branches to develop processes and to monitor their effectiveness and ensure on going compliance with relevant legislation and Company’s requirements
- Promote incorporation of Quality issues into business planning and performance measures by working with the local managers
- Ensuring that the regional Quality audit schedule is maintained and that auditing targets are met
- Monitoring and measuring conformity with Quality Standards, identifying trends and opportunities for improvement
- Implement the Quality audit program and monitor the quality of the audits and report results to the Head of Quality local managers and business Directors
- Following up of all corrective and preventive action to a satisfactory conclusion
- Assist business managers with the development of action plans, as necessary
- Assisting business managers with identifying Quality training and information needs
- Liaison with Directors/Managers within the region at all levels on Quality issues
- Ensure timely monthly reporting provide statistical reports to the Head of QEHS
- Taking ownership, assigning and reporting on projects for Quality issues, as required
154
Quality Manager Resume Examples & Samples
- 10 years of experiences required. Minimum of 5 years’ experience in Quality required. Prior leadership experience in Quality preferred. Aerospace industry experience is required
- Team Oriented individual with excellent interpersonal, written and oral communication skills required
- Demonstrated expert facilitation and negotiation skills required
- Demonstrated program management skills required
- Demonstrated team leadership in delivering results required
- Thorough working knowledge of UTC Quality Management System and flow down of requirements required
- Thorough working knowledge of Quality System Standards required (e.g. ISO 9000, AS9100, AS9120)
155
Quality Manager Resume Examples & Samples
- Quality Management consisting of the creation, execution and evolution of all aspects of the quality functions in the organization including development and implementation of effective plans, methods and procedures and the use of proper equipment to effectively respond to requirements for all aspects of company processes, products and services
- Manage a small group of direct reports and multiple other cross-functional teams/team-members engaged in a variety of improvement and corrective-action assignments involving various complex operations
- Provide counsel to senior managers and assist them with overall management of the organization. Promote, develop and implement measures to guide action plans to improve operations and customer relations and sales growth
- Report, provide direction and actions plans for key improvements in Operational Excellence and Quality metrics/initiatives including Net Promoter Score, Customer Complaint Resolution Process, ISO certification, Process quality metrics applied across functional teams as agreed to within our LBU
- Direct the development of functional strategy and roadmap, including long-term and short-term goals, objectives and plans for the organization
- Implement plans for proper prioritization and cost-effective accomplishment of same
- Schedule and manage activities, anticipate and direct timely and effective responses to problems
- Ensure that operations are conducted in accordance with the Company's policies and procedures and are in compliance with quality, health and safety, legal, and industry standard guidelines
- Manage the resolution of complex technical problems and human resource issues, while understanding the customer and political environment
- Promote and ensure fair and equitable treatment of staff and peers
- Monitor performance and initiate measures for improvement in such areas as quality of work and responsiveness to customer requirements
- Promote and facilitate introduction of alternative approaches, methods or equipment to more effectively accomplish objectives. Manage and ensure compliance with contractual agreements
- Provide guidance and arrange for training of staff
- Provide support for company and industry initiatives and programs to senior managers and advise supervisors regarding complex aspects of their assignments
- Manage and document employee performance and implement responsive measures
- Must have a teamwork orientation both within functional responsibilities and with other functions throughout the BU to ensure organizational alignment with objectives and plans
- Bachelor's Degree and 12 years of experience in Operations, Quality, Sales, Sales Operations, or Service
- 16 years of experience in Operations, Quality, Sales, Sales Operations, or Service
- Experience in a union workforce environment is a plus
- Broad knowledge of quality management in a complex operational environment, a variety of quality tools, approaches, equipment and processes
- Ability to independently resolve complex problems related to urgent customer or market events, as well as, longer-term problems evolving from within organization operations or strategic plans
- Ability to manage a skilled and diverse staff, including indirect reporting personnel, communicate effectively, represent the organization, act decisively and influence decisions of senior managers and customers
156
Quality Manager Resume Examples & Samples
- Drive quality levels and productivity growth by employing Kaizen approach and lean processes
- Manage quality technicians and their work in the quality lab
- Assist with data interpretation to provide direction for quality activities
- Direct staff in fostering, nurturing, and maintaining relationships with global suppliers
- Collaborate with Design Engineers and Manufacturing Engineers on new product introductions
- Create and implement process improvement projects across the manufacturing lines using various methodologies including lean Six Sigma and Kaizen
- 5+ years of Quality Engineering experience in agriculture, automotive, off highway, or aerospace
- 2+ years of previous hands-on work with Geometric Dimensioning and Tolerancing (GD&T)
- 3+ years of fabrication and welding experience
- 1+ years of project management experience
- Lean experience
- Prior management or supervisory experience
157
Quality Manager Resume Examples & Samples
- Engineering degree in Paint/Surface Coatings Technology/Post Graduate in Chemistry
- 6 years’ Manufacturing / Quality experience in Paint industry
- Should have managed a quality function of a chemical/ paint company
- Good Technical & Product Knowledge
- Appropriate knowledge in HSE&S Competence
- Operations Overview
- People Management skills and Good negotiation and interpersonal skills
- Good interpersonal relations and Patient trainer
- Knowledge of equipment (desirable)
- Understanding of KPI & its implications
- Good Analytical Skills
- Varied experience in trouble shooting at various locations
158
Quality Manager Resume Examples & Samples
- >5 years in a manufacturing quality role or in a comparable role to this one
- B.S. in Chemistry, Engineering in core discipline, or Technical equivalent
- Previous experience in change management, process/ continuous improvement
- ISO 9000 Certified
159
Quality Manager Resume Examples & Samples
- Develop and maintain the Quality Management system for the Projection division and ensure compliance to the ISO9001 standards
- Coordinate and provide pro-active collaboration, advice and decision making in the project/product development milestones
- Coordinate and steer monthly product quality meetings
- Coordinate and steer the Corrective Action and Preventive Action (CAPA) process
- Manage escalated customer complaints and severe supplier quality issues
- Install Software Quality Management systems
- Execute and follow-up internal audits
- Coordinate and organize certification audits, customer audits or other inspections
- Perform data analysis based on trend data
- Drive process adherence and uniformity across the projection division
- Drive continuous improvement thinking and action across the projection division
160
Quality Manager Resume Examples & Samples
- Direct and manage the safe, efficient, productive operations of the Polyurethane Systems multi-site U.S. QA/QC laboratories to achieve business objectives
- Develop, motivate and lead subordinates in meeting their personal and the organization's objectives through coaching, training and professional development
- Manage all ISO 9001, RCMS and other relevant management system requirements as they relate to manufacturing, maintenance, and business processes for Operations
- Manage customer visits and audits and serve as the primary interface with Quality Management for internal and external registrar audits
- Work with Sales/Marketing, Technology, Product Management, Supply Chain, and Product Stewardship to facilitate new product introductions as it relates to manufacturing capability and customer requirements, also ensuring customer concerns are resolved and relationships are enhanced through collaboration
- Drive continuous improvement through supplier compliance and development with Quality Management. Also support continuous improvement training of personnel
- Collaborate with Operations, Sales, and Product Management & Supply Chain Personnel to resolve customer concerns and enhance customer relationships
- Work together with the PM Quality Management Group, and the PUR Production Sites monitor KPI’s, implement continuous improvement corrective/preventive actions and initiatives, and share best practices related to manufacturing, quality, and continuous improvement
- Manage department cost center through personnel, budget and project development, execution and coordination of quality activities
- Tracks and reports the Cost of Poor Quality
161
Quality Manager Resume Examples & Samples
- Ensure product performance is known and improvements are identified and implemented
- Implement and maintain improvements in timeliness and accuracy of field product, service and software performance reporting
- Audit quality system policies and procedures in conjunction with other Liebert North America auditing activities. Ensures Quality Management System audits are completed and action plans are implemented and effective
- Develop and maintain an organizational structure, policies and procedures that ensures Liebert’s Quality Systems are effective and meet Customer’s requirements
- Develops and implements training and education that improves product quality and reliability through increased associate involvement
- Be the voice of the customer in the location
- Supervise associates involved in department activities, including assigning and reviewing work and evaluating performance. Supervise, delegate, and prioritize workload. Train staff on policies, procedures, and internal controls
- Monitors performance, provides regular feedback and conducts employee performance reviews. Encourages and facilitates implementation of improvements and development
- Foster employee engagement and ensure that business and operational goals are effectively communicated to employees. Acts as a role model and ensures compliance with company policies and procedures
- Promote a positive working environment that encourages employee involvement to achieve excellence in productivity, customer service, quality, and Environmental Health & Safety (EHS)
- Actively participates and initiates process improvements to organizational processes
- Demonstrates leadership behaviors that supports continued growth and development and company mission and values
- Identify and arrange for training on quality for department’s associates
- Identify and implement improvements in poor quality costs (warranty, rework, scrap, airfreight)
- Facilitate Associate Action Teams
- Aid, assist, and lead the various tasks of Ohio Operations in obtaining ISO 9001 Certification
- Successfully transition operation from Incoming Inspection to Supplier Quality Activities driving responsibility for component quality back to the supplier
162
Quality Manager Resume Examples & Samples
- Directs the Quality Management System at the plant
- Perform ISO Management Representative role for Norcross as an ISO certified plant
- Achieve Green Belt Six Sigma certification and lead green belt projects (Black Belt preferred)
- Achieves desired results in Quality by diagnosing, designing, implementing, then insuring division’s processes, practices and procedures are fully and consistently adhered within the plant by working directly with all plant personnel including sales, design, customer service, planning, manufacturing and shipping / delivery
- Fully accountable for continuous improvement in the plant’s quality programs through use of external and internal benchmarking, leveraging of industry/manufacturing best practices
- Facilitate formal problem solving team activities to drive to root cause and corrective action
- Coaches and trains plant leadership and plant personnel to achieve desired results
- Effectively consults with and presents quality programs and solutions to all levels of the plant’s internal and external customers
- Works with division’s suppliers and vendors in achieving quality expectations of internal and external customers
- Oversight for the areas specific to document management, calibration, CAPA, Internal Assessment, Management Review, Supplier Management and employee training as it relates to the Quality Management System
- Responsible for integrity of data collection systems (KIWI QMS)
- Candidate must support and drive Performance Excellence practices in all aspects of your role
163
Quality Manager Resume Examples & Samples
- Executing the company quality strategy and goals, in particular the achievement of certified QM systems in the plant
- Track and maintain data analysis of key metrics and performance data as it relates to the company quality strategy and results
- Support division to achieve plant targets and ensure Lessons Learned / Best Practice in respect of Quality
- Support division in cases of containments, customer - and warranty claims; executing documentation, root cause analysis and corrective actions and verification of effectiveness
- Interact with Management Team to meet or exceed internal and external customer quality performance targets
- Ensure QM systems corresponds to Magna Corporate and Group Requirements
- Bachelor’s / Master’s degree in engineering
- Knowledge of implementing and maintaining QM systems and its Auditing / Assessment internal and external, dealing Suppliers and Customers
- Advanced knowledge in FMEA Tools
- Comprehensive knowledge of Root cause analysis and Problem Solving Methods
- 5 plus years experience in Automotive Manufacturing
- Managerial experience
- Experience in field of quality, engineering or production
- Polish and English both spoken and written, German will be an advantage
- Excellent computer skills including Microsoft Office
- Able to provide results oriented environment and set high standard for self and department
- Able to effectively present information and respond to questions from management, team members and customers
- Able to work efficiently in a high demand environment
- Able to work well with others; build and maintain positive Team Member relations
- Able to provide excellent leadership example, able to coach, motivate and build self-confidence within work
164
Quality Manager Resume Examples & Samples
- Develop and implement quality control methodologies to ensure compliance with quality assurance standards, guidelines, and procedures for a DoD IT programs and/or systems
- Support the review, consolidation and/or creation of integrated program metrics, master schedules Reviewing modifications to drawings and target specifications
- Consolidation and reporting of budget information spend plan data and business process maps
- Following project plans and schedules as assigned by the Project Manager
- BS in Computer Science, Engineering, IT or equivalent
- Minimum 5 years’ experience
- Excellent writing skills to include writing technical documentation and proven track record of strong analytical and logistics skills
- Excellent customer facing skills that include understanding the customer's needs and requirements to ensure those requirements are fulfilled
- Strong interpersonal skills to interact with senior customers, management and team members
- Experienced with DOD requirements
- Must have an active Secret level clearance
165
Quality Manager Resume Examples & Samples
- 7-10 years of experience in medical device quality management
- Experience working in medical device product development (product design) and manufacturing (process design, process validation, and production)
- Expertise in FDA 21 CFR 820 regulations, ISO 13485, ISO 14971
- BS in Engineering or relevant degree
- MBA or Masters preferred
- An American Society for (ASQ) Certified Quality Engineers or Certified Quality Manager (CQM) certification is preferred
- ISO13485 Lead Auditor certification is preferred
166
Quality Manager Resume Examples & Samples
- Interfaces with customers on technical/quality issues and improvement initiatives
- Responsible for managing customer audits and regulatory/compliance agency audits
- Confers with engineers about quality assurance of new products designed and manufactured products on market to rectify problems
- Responsible for authorizing the released of final products to customer
- Identifies needs for evaluation/assessment with regard to regulatory issues and conducts or enlists internal/external experts to investigate, test and/or audit. Recommends corrective action to management and implements approved solutions. Follows up on implementation plans to ensure compliance
- Reviews discrepancy reports and implements corrective actions
- Ensures compliance with the Company’s Quality System and applicable regulatory requirements such as ISO 13485
- Develops, establishes and maintains quality assurance programs, policies, processes, procedures and controls ensuring that performance and quality of products conform to established standards, agency guidelines and customer requirements
- Provides factory support to identify and resolve issues associated with purchased parts, materials and manufacturing
- Interfaces with manufacturing, engineering, quality and customer representatives to develop quality systems and ensure compliance, determine responsibilities and solutions when required
- Leads a team of Product Quality Engineers, Staff Engineers and Quality function leaders
- Contributes to continuous improvement activities
167
Quality Manager Resume Examples & Samples
- Drive Product Reliability Performance improvement
- Oversees ORT team to achieve company level product reliability target
- Continue to improve reliability test capability and capacity
- Continue to improve ESD system
- MRO forecast review
- Conduct Failure Analysis on the ORT failures
- Lead the definition of the actions for the related ORT issues
- Work with RD team for reliability test plan definition
- Work with CFT teams to evaluate quality risk on the shipments
- Monitor the execution of the defined ORT tests
- Publish reliability report
- Issue tracking report
- Preparation of Acoustic report, EMC report, Control run report
168
Quality Manager Resume Examples & Samples
- Lead the creation and execution of manual and automated test cases for functional, regression and end-to-end testing, including both back-end and front-end testing of entire system, subsystems and interfaces to other systems
- Design and implement functional and end-to-end test automation
- Execute automated tests on multiple environments, utilizing multiple browsers
169
Quality Manager Resume Examples & Samples
- Creation and control of processes and documentation in the area of Quality
- Identification, evaluation and optimization of process and quality measures
- Development/optimization of the quality KPI system
- Plan and perform internal audits
- Analyse the root cause of product shortcomings
- Plan, optimize, develop and execute Quality Assurance actions
- Ensure projects' compliance with quality assurance standards
- Management consulting regarding all topics related to Quality Management
- Employee training and consulting regarding all topics related to Quality Management
- Degree in business administration in the area of banking, commercial training in banking or other relevant background, preferably with an IT focus
- Professional experience in quality management
- Experience in implementation of established standards (e.g. ISO, Sig Sigma, ITIL, CMMI)
- Knowledge of IT processes (software development, operations)
- Team player with excellent communication skills within the organization as well as with customers
- High level of organizational and analytical skills as well as entrepreneurial thinking
- Good German
170
Quality Manager Resume Examples & Samples
- Must be comfortable with the implementation of lean manufacturing and quality tools, in accordance with ISO 9000
- Six Sigma Black or Green Belt Certification is a plus
- Must have strong problem solving and critical thinking skills
- Basic SAP knowledge mandatory
- Proficient in Microsoft Office (Excel, Word, and PowerPoint)
- Excellent interpersonal & organizational skills are required
- Must be able to effectively lead employees promoting a team-orientated environment
- Must be able to lead, instruct, and maintain safety rules and regulations
- Bachelor Degree in Engineering or Technical equivalent experience is mandatory
- Minimum of 3-5 years of experience of quality management experience in a lean manufacturing environment
- Must have some kind of experience with electrical or power electronics components
- Must have railway, aerospace or similar industry experience
171
Quality Manager Resume Examples & Samples
- 10+ years of total software testing experience with focus on strategy development, delivery and execution, maturity assessment and process optimization, project management and onsite/offshore coordination (preferred 3-5 years in Agile Implementation)
- Experience in defining regression test strategy for large-scale implementation
- Experience with DevOps, Release Mgmt. & Test Environment coordination within a large, multi-project setup
- Knowledge of Test Management tools like HP QC/ALM
- Knowledge of Test Automation tools and standards highly desirable
- Experience with Agile delivery models, especially Scrum and/or Kanban and Ensure processes are optimized (Better Quality, Lower cost and Quicker Time to market)
- Provide thought leadership , Garner necessary support from COE’s and bringing best practices in process, technology and domain
- Institutionalize Automation and Performance Best Practices
- Drive Innovation and find avenues for adoption of proven best practices from Industry standards
- Develop and execute enterprise-wide regression test strategy that particularly constituting of best practices, test design tools and techniques such as Pairwise testing, and regression testing process in Agile development model
- Responsible for coordinating the use of test environments and resolving conflicts
- Collaborate with DevOps and Infrastructure teams to ensure environment provisioning, maintenance, scalability and capacity planning
- Drive skill enablement cross pollination of knowledge and help to build assets and strive continuously to build strong collaborative agile teams
- Motivate and keep the team intact in maintaining good quality and timely delivery
- Share status reports and delivery dashboards on project status
- Participate in governance meetings and provide update to Senior Leadership / Executive team
- Responsible for designing common and industry-standard benchmarks for quality improvement
- Help in the evaluation of quality assurance process framework, tools and technology
- Present ideas and progress on various strategic initiatives to clients’ senior leadership team
- Strong knowledge on Metrics and analysis. Analyze various metrics, design trends and work with Leadership to improve processes
- Strong communication Skills
172
Quality Manager Resume Examples & Samples
- Working closely with ACT’s Operations Management team to meet short term customer requirements while implementing business strategies in support of long term demands
- Provide leadership to solve value stream quality challenges to ensure site success and customer satisfaction
- Overseeing management of bench inspection and MCL resources to ensure cross training, overtime and productivity goals are achieved
- Drive product and process improvements that ensure ACT’s quality metric goals are met (Escapes, Scrap, Rework and Process Cert)
173
Quality Manager Resume Examples & Samples
- Keeps weekly quality meeting where customer issues are discussed and action plans developed and followed up. Ensures for timely feedback to the customer
- Monitors the quality performance of our suppliers in conjunction with our supplier quality engineer. Regular sessions are held to analyse performance gaps, and monitor timely and complete realisation
- Responsible to withdraw non confirming products and stop/release production/shipments (engineering/operations)
- Plans and/or contributes to quality improvement programs, projects, audits
- Develops, manages and/or maintains Quality Management Systems meeting the needs of the Business and complies with required standards and regulations together with the Quality Assurance Manager
- Drives uniformity in process/procedures/working practices
- Drives continuous improvement thinking and actions within Barco
- Collaborates pro-actively, advices and decides in granting project/product milestones (R&D)
- Responsible for the validation and safety compliance and environmental testing of newly developed products and releasing the products for mass production and creates a vision and execution plan for “validation of the future” by automated testing and statistical analysis
- Responsible for long term testing and follow up of performance over lifetime of the products
- Motivates the organisation to think Quality. Highlight excellent examples/behaviour
- Organises twice a year the quality management session to discuss status of the quality management system and actions to close performance gaps
174
Quality Manager Resume Examples & Samples
- Manage and drive bottom line improvements in Quality performance in line with business objectives. - Cost of Poor Quality (% COGS), Warranty (ICQ and Standard Warranties for new completes and parts), Internal Failures (scrap, reworks), Supplier Failures, (rework, return to Vendor and backcharge). This is accomplished through development of AOP for the site in coordination with other Plant Staff Managers deploying quality culture utilizing strategic and innovative approaches
- Actively support Procurement and SDE functions in Suppliers’ approval and monitoring deploying a formal supplier partnership, supplier scorecards, PPAP and Corrective Action processes in line with Std Works requirements
- Drive the lean Quality organization of qualified and experienced people with the enthusiasm and continuous improvement approach, promoting cultural change within the organization to meet the overall business objectives in Safety, Quality, Cost, Delivery
- Ensure Internal and Customer quality performance and perception, by controlling processes, outgoing products quality and reliability. Support Company projects through IR PDP process, ensuring process conforming deliverables. Manage quality escapes and customer feedback through external and regular reviews with service, technical support, engineering and operations in ICQ and warranty issues resolutions identifying opportunities for improvement
- Manage multi level RCCA and CAPA processes to drive continuous improvement in all functions of the business including monitoring of CAPA effectiveness and continual improvement initiation
- Be a benchmark site for the development of quality processes and prompt their adaption at other sites. E.g. Supplier Partnership, RCCA, CAPA, Customer Feedback, Training, Auditors Coordination, Inspections to products, Special Process Controls, Quality Control Codes and Rules, updated documentation, audits, inspections to Customer requirements, initiatives to involve and engage employees
- Documented business processes are in line with business objectives and regularly verified. Support continuous improvement. Maintain the Quality Management System certifications and identify potential certifications that could be an opportunity for business growth
175
Quality Manager Resume Examples & Samples
- Demonstrates superior command of and the ability to convey to business owners Quality concepts including, but not limited to Quality Control, Quality Assurance, development of test questions, statistical sampling and sampling strategies, metric development, process monitoring, trend analysis, root cause analysis, and corrective action
- Demonstrates superior execution and management skills on implementation projects, balancing the responsibility of multiple engagements simultaneously
- Directly manages associates and project teams operating in a matrixed environment
- Communicates with executive sponsors and resolves conflict through broad decision making
- Manages organizational barriers to ensure that project teams are effective in reaching project resolution
- Coaches and / or directs other – provides deep subject matter and technical expertise in support of the Firmwide Quality initiative
- Incorporates and leads organizational change management projects by leveraging ADKAR’s structured change management methodology and toolkit
- Responsible for delivering Quality implementation projects using formal project management methodologies including Lean, Six Sigma and ADKAR
- Drives performance improvement through the development of Quality programs which clearly connect Quality performance with process inefficiencies
- Creates and delivers presentations and facilitates productive meetings (both in-person and virtually) at various management levels up to Executive Level report outs
- Provides clear and concise documentation that supports the milestones of implementation projects, represents key business decisions made, and obtains sign off from stakeholders
- Assesses current processes including risks and controls to identify defects and areas of improvement to help develop future state design
- Uses creativity, strategic thinking and planning abilities as well as financial thinking to determine benefits and results for the business with a focus on being able to identify key Quality metrics and drivers and identify ROI of engagement work
- Applies analytical / quantitative approach to problem solving; knows how to obtain and use data, and comfortable with statistical analysis and concepts and is able to coach and mentor others in these areas
- Assists with developing documentation and information to gain agreement from business managers on new processes and service level agreements
- Promotes effective use of existing tools and processes, makes improvement recommendations as needed, contributes to the development of new tools and processes
- Serves as a catalyst for organizational change
- Command of Quality systems across various types of business or industries
- Ability to lead detailed current state assessments of LOB Quality programs and determine improvement methodologies
- ADKAR Organizational Change Management and Strategic Change Communications, including organizational readiness and resistance management strategy formulation
- Exceptional executive level presentation skills and ability to create Power Point decks of the highest caliber
- High-performing team-player with excellent written and verbal communication skills
- Proven ability to thrive and create structure in ambiguous work environments with an aptitude for remaining composed and confident under pressure
- Proven ability to prioritize and efficiently complete multiple assignments while maintaining the highest quality
- Ability to lead teams, manage employee performance and mentors others
- Ability to think globally and understand implications beyond project specifics
- Superior facilitation skills with ability to bring teams to consensus
- Exceptional customer service mentality
- Excellent judgment and logic to handle sensitive information
- Exceptional problem solving skills as well as the ability to create logical and realistic solutions under tight deadlines
- Ability to perceive risks and make decisions quickly, often with incomplete information
- Passion for improving systems and processes
- Ability to meet travel expectations of 50-75%
- 5+ years of experience implementing and / or managing Quality Management Systems (ISO 9001 or QS 9000)
- Bachelors degree from an accredited school, with a demonstration of strong academic performance (Master's Degree Preferred)
- 7+ years of experience utilizing process improvement skills in a transaction, service or manufacturing business environment (Process Improvement/ Managerial Consulting experience Preferred)
- Formal Lean/Six Sigma training and experience is required (Certification Preferred)
- Certified in Prosci’s ADKAR change management methodology
- 5+ years of Project and Program Management Experience (PMP Certification Preferred)
- 5+ years of experience and a proven understanding of the Financial Services industry
- 5+ years experience in Training and Development mentoring others on process improvement methodologies
- Strong computer skills; proficiency in Microsoft applications (MS Visio, iGrafx, Advanced MS Excel - including macros, logic functions, solver, etc., MS PowerPoint) and comfort with learning and using new software tools
176
Quality Manager Resume Examples & Samples
- Ensures that processes needed for maintenance of the Quality Management System and the site Quality Policy are established, implemented, and maintained. Enlists the site leadership staff and subordinates in the cost-effective manufacture of high-quality IEC assemblies, UPS units and standard products, and in the continual improvement of the Quality Management System through Management Review
- Establishes objectives, policies, and procedures for plant quality assurance activities. Reports the plant’s performance to Eaton upper management against Quality targets for leading performance indicators, customer quality concerns, internal Cost of Quality / Cost of Non-Conformance (CONC), and any needs for QMS improvement
- Manages a staff of Test Technician and Quality Technician to achieve quality assurance objectives. Recruits and develops a talent pipeline for Quality professionals
- Ensures the promotion, awareness, and compliance to customer and regulatory requirements throughout the Quality department
- Monitors overall plant quality progress and performance and makes corrections as needed
- Acts as a primary organizational contact for customer concerns and ensures appropriate corrective actions are deployed as necessary
- Ensures manufacturing readiness for customer and other third party assessments (i.e. FAT)
- Manage QA department resources to maximize QMS compliance and to ensure continual improvement against established objectives
- Deploy Eaton Business System tools, where appropriate or required, to improve Quality Management System effectiveness
- To Drive quality tools utilization such as tracking, Scrap Review, Quickly Responding, Error-proofing, Risk reduction, for process monitor and catch opportunity for improvement
- Leads and track problem solving and root cause analysis activities in order to eliminate recurrence of non-conformances
- Perform continuous training on the quality inspectors. And daily tier quality meeting
- Guides and works closely with Engineering & Manufacturing on development opportunities such as Quality Systems, Process Controls, Control Plan, etc
- Minimum five (5) years’ experience in Quality Engineering is required
- Minimum two (2) years’ experience in a managerial or supervisory role is required
- Prefer 3 years’ experience managing direct reports
- Prefer minimum ten (10) years in Quality or Manufacturing environment
- Quality Management experience is preferred
- Understanding of ISO9001 requirements is preferred
- Administrative- Knowledge in the usage of Microsoft Word, Excel, Outlook and other basic computer skills; English spoken and writing
- Managerial- Ability to plan, schedule, organize and conduct meetings. Ability to delegate responsibility and to track progress
177
Quality Manager Resume Examples & Samples
- Coordinate multiple test projects to insure completion according to scope and schedule
- Provide direction and mentoring for staff
- Empower staff to solve problems, take initiative, and make independent decisions within a defined, flexible, and logical QA process
- Balance deployment of resources between projects as necessary
- Train staff to manage expectations and communicate effectively with project stakeholders
- 7+ years of industry experience in Project Management, Software Development, or Quality Assurance
- Proven ability to source and grow talented, cross-functional engineers
- Programming skills in Java, PHP or Python
178
Quality Manager Resume Examples & Samples
- Quality Culture
- COPQ
- Supplier Quality Controls
- Change Control Governance
- Manufacturing Process Quality
- A minimum of 5 to 10 years relevant work experience with a multinational organization including responsibility for product and process quality, regulatory compliance as well as quality training and development
- A primary degree in an Engineering discipline and preferably a post graduate qualification in quality assurance
- Exceptional communication, inter-personal and team leadership skills are essential
- Six Sigma Black Belt qualification would be a distinct advantage
- Fluency in a second European language would also be an advantage
179
Quality Manager Resume Examples & Samples
- Direct supervision/management of the quality engineering and inspection staff for Mechanical Manufacturing and for providing objective-oriented direction to subordinates utilizing management guidelines and general principles
- Staffing, training, budget management and employee development
- Overseeing projects and tasks assigned to the organizational group performed by both non-exempt and exempt employees
- Collaborating with Program IPTs and SPMs is required to ensure quality standards are in place and schedules are supported
- Involvement in policy/procedure execution, ensuring QMS compliance, and interfacing with DCMA and other customers
- Creating and implementing methods and procedures for inspecting, evaluating and improving (reducing) variation from processes affecting precision and accuracy of products and production equipment
- Facilitating and ensuring that corrective and preventive measures meet acceptable standards and that documentation is compliant with requirements
- Bachelor’s Degree in a STEM field
- A minimum of 7 years experience with background in quality, manufacturing, and/or engineering
- This position requires strong leadership, interpersonal and communication skills; the ability to effectively interface with internal and external customers
- Working knowledge of wiring schematics, blueprints, GD&T, and use of basic inspection equipment
- 3 years of prior management experience
- MS or MBA
- SPM/CAM/IPT experience
- Active SSBI
180
Quality Manager Resume Examples & Samples
- Plans, coordinates and directs the Quality program to ensure continuous production of products consistent with established standards
- Manage the day to day operation of the Quality Team to ensure efficient use of resources with an objective to ensure incoming and outgoing activities of the Quality Department meet the requirements of the business
- Report to Senior Management Team on quality results and identifies breaches of the Company's quality policies along with recommending any need for improvement
- Promotes Quality within the organization as well as facilitates training for quality systems, methods and tools
- Quality planning for new product introduction
- Review and Monitor Customer and product issues in Corrective Action Reporting/Non-Conformance Reporting; Responsible for product quality issues and timely response to customers
- Support all departments in the development of procedures and policies to ensure consistency in methods to deliver quality products
- Develops, upgrades, maintains and improves the quality system as needed in line with the requirements of ISO 9001:2015 Quality Management Standards; including documentation control
- Audits system to ensure compliance and prevention of quality issues and ensure that there are sufficient internal auditor resources to support continuous improvement
- Respond to requests from external and internal customers as well as suppliers regarding our quality systems
- University degree in Manufacturing or Mechanical Engineering
- 2 or more years of experience leading a multi-disciplinary team
- A minimum of three (3) years in developing and implementing successful programs focused on both quality initiatives/processes and productivity improvements
- Six Sigma Champion or Black Belt training or equivalent education/experience is an asset
- Must be able to direct, manage, and support initiatives to attain operational wide goals for quality product manufacturing and inter-department processes and procedures
- A minimum of two (2) years of experience in an ISO 9000 environment is essential
- Good understanding of manufacturing processes (mechanical/electrical assembly, welding and machining)
- Previous experience with large scope project management and change management initiatives related to quality improvement
- Good time management, prioritization and organization skills
- Experienced with Quality Management Systems, Microsoft Office software
181
Quality Manager Resume Examples & Samples
- Recruit, develop and lead the QA team in areas of expertise and high performance team behaviours
- Provide technical expertise and leadership to the QA group with regard Compliance and Quality Systems
- Oversee the Batch Release process
- Support Technology Transfers through Process Validation to Regulatory Approval
- Drive implementation of a science and risk based Quality Culture throughout the facility
- Lead the preparation and facilitation of Regulatory Inspections
- Oversee activities related to core quality systems including Deviations, Change Controls and CAPA systems
- Oversee relevant metrics for each quality system
- 8+ years experience in a cGMP regulated manufacturing environment, with exhibited knowledge or proficiency in Quality Assurance and Compliance
- Ability to speak, present data, and defend approaches in front of audiences and inspectors
- Ability to comprehend technical information related to equipment, processes, and regulatory expectations
- Experience with participation in regulatory inspections presenting or defending departmental functions in audits or regulatory inspections
- Understanding and familiarity with FDA & European regulatory requirements, guidelines, and expectations
182
Quality Manager Resume Examples & Samples
- Knowledge of physician office practice operations
- Knowledge of organizational policies, procedures, systems and objectives
- Knowledge of applicable regulatory, compliance, and accreditation standards and requirements
- Mentor, influence, and manage through matrix reporting relationships
- Ability to gather, analyzes, and interprets complex data
- Ability to prepare comprehensive management reports
- Project Management: Skilled in project planning, task prioritization, effectively manages resources, outcomes measurement, and tracking. Takes initiative and exercises good judgment
- Effective problem solving skills to include data analysis and judgment to make effective decisions
- High Impact Communication - Effective oral and written communication skills
- Effective change leadership knowledge and skills
- PC Skills – Proficient in Microsoft Office applications and others as required
- Maintains high level of confidentiality at all times
- Ability to build trust and gain respect through effective team leadership and participation skills
- Minimum 3 years of related clinical and management experience involving quality improvement, leadership, and healthcare quality practices, as well associated governing laws and regulations. At least one year must have been in capacity as direct supervisor of other professional level employees
- Minimum 3 years direct experience in ambulatory care quality improvement preferred
183
Quality Manager Resume Examples & Samples
- Current Florida RN license
- BSN required; Master’s Degree strongly preferred
- CPHQ certification preferred
- 5+ years of progressive healthcare experience in an acute care setting
- 2 or more years of experience focusing on Quality Management and performance improvement
- Thorough knowledge of quality management practices, core measures, hospital policies and procedures and regulatory requirements
184
Quality Manager Resume Examples & Samples
- Staying responsible for all performance improvement activities including leadership coordination of PI projects with other departments
- Staying knowledgeable in TJC and CMS requirements and making sure that those requirements are implemented and sustained throughout the organization
- Leadership of improvement projects related to quality improvement and patient safety with clinical, administrative, and support services
- Analyzing quality improvement data and reporting outcomes to clinical, administrative, and medical staff on an ongoing basis
- Coordinating the quarterly Clinical Excellence Committee meetings with data aggregation and analysis
- Managing hospital wide policies and ensuring that compliance to regulatory requirements is supported in policies
- Direct supervision of quality analysts and the ongoing Core Measures compliance to include ensuring completion of records abstraction, making certain that clinical, administrative, and medical staff have ongoing knowledge of current and new core measure requirements, and communicate compliance requirements with clinical staff and physicians to ensure compliance
- Participation in the peer review process and maintaining physician practice data
185
Quality Manager Resume Examples & Samples
- As the Quality Manager you will be daily manager for up to 10-15 Quality Engineers whose main responsibility is to assure that our projects are executed efficiently and all customer and health authorities' requirements are fulfilled. They have extensive knowledge within the following fields
- National and international GMP
- ISO 9001:2000
- Writing specifications
- Document control
- Document standards and templates
- You will demonstrate leadership by ensuring that the department constantly strive for an optimal development of both the processes, critical competences and customer relations. Be a role model and support necessary changes and a global mind set, by cooperating across organisational as well as geographical boundaries
- You know how to stimulate employee enthusiasm through an open, proactive and inspiring management style, and you support the continuous personal development of your employees
- You will be responsible for the overall development of the department and that all services are optimally adjusted to business opportunities and the company visions
- You will also take part in sales activities and focus on establishing relations in order to obtain preferred partnerships with our clients
186
Quality Manager Resume Examples & Samples
- At least 5-10 years of experience in construction inspection for transportation projects is required
- Required to have and maintain a satisfactory driving record
- Ability to read and interpret roadway, structure, and bridge plans and specifications
- Perform calculations
- Promotes and maintains a safe working environment
187
Quality Manager Resume Examples & Samples
- Company quality strategy and its development
- Responsibility for quality processes within whole organization and its understanding demonstrated in daily work
- Maintenance and updating of all quality processes and systems and controls within whole organization according to regulations through cross-funcional cooperation and understanding
- Well performed all types of quality controls, audits and inspections
- Compliance with all quality regulations and recommendations
- Implementation of best practices quality principles
- Awareness of affiliate quality risk and minimization of risk activities
- Ensure that management reviews are conducted and documented and that LT is pro-actively alerted of systemic compliance and quality issues/risks and opportunities for training or process improvement
- Delivering reports for global and Affiliate Management Review, including collection, compilation, reporting, and analyzing relevant data
- Ensure that all Affiliate process documents that describe the QMS are properly maintained
- The appropriate metrics in collaboration with the business and PDQ
188
Quality Manager Resume Examples & Samples
- Training and certifications: On-going In-depth training with current and emerging products and technologies
- Flexible benefits: Medical program, Sports benefits, Lunch vouchers, Mobile phone, Laptop
- Compensation: Competitive salary package and relocation bonus for candidates outside West Area
- Extra vacation days
189
Quality Manager Resume Examples & Samples
- Define and implement local QMS (incl. MSO), aligned with Group/Global QMS,
- Ensure the defined local QMS meets requirements of relevant norms, most notably ISO9001,
- Keep the local QMS aligned with new versions of the norm (currently: the migration to ISO9001:2015),
- Prepare, chair and report on the local Management Review, at least once a year,
- Personally responsible for ISO9001 and ISO14001,
- Oversight role for ISO20000-1 and ISO27001,
- Local ownership of the Document Control process,
- Local ownership of the Customer Excellence and Loyalty process,
- Input into Service Excellence and Rainbow Delivery Reviews through KPI data
190
Quality Manager Resume Examples & Samples
- People management skills
- Knowledge and experience of operational process(es) and their continuous improvement through
- Good knowledge of ISO9001 /ISO 14001
- M.Sc. or Bachelor degree in a relevant field or equivalent experience
- 5 years of professional experience
- Written and spoken German, English and French
- Basic Quality knowledge in Quality tools, methods, systems
191
Quality Manager Resume Examples & Samples
- Education Level: A basic university degree in either science or engineering
- Other Technical/Professional Qualification
- CQE, CQM and Lead Assessor qualifications are added assets
- Very good communication skills in oral and written English
- Working knowledge of computer and statistical software is a must
- Ability to communicate in both English and Mandarin is essential
- T least 8 years of industrial experience in Quality Assurance in related field
- Must be able to communicate with all management levels and possess good facilitating skills
192
Quality Manager Resume Examples & Samples
- Lead and host audits carried out by customers, third parties and authorities
- Responsible for documenting customer findings from audits and issuing and managing the non conformances for satisfactory response and closure
- Devise the internal quality plan based on risk and carry out internal audits in accordance with Company programme
- Identify gaps relating to audits and implement procedural changes to reflect current practices which comply with regulatory requirements
- Ensure customer dissatisfaction is documented and the appropriate action taken to ensure non re-occurrence of issues found
- Devising and implementing appropriate methods of analysis for data related to KPI’s appropriate to the business such as internal audits, supplier performance, customer returns and non conformances for continuous improvement
- Reporting KPI’s at appropriate intervals and holding continuous improvement meetings and associated issued actions
- Direct the quality team on a daily basis related to prioritisation of tasks
- Responsible for release of Product in accordance with EASA Form 1 Requirements (CAA Part 21 and 145), FAR 145 and Certificate of Conformity of all products from the business site, including delegating responsibility during absences
- Achieve and maintain delegated quality responsibility from Customers and where necessary delegate to other competent individuals
- Produce and submit First Article Reports to customer and check supplier reports
- Monitor and escalate, where necessary, internal product quality issues
- Lead problem solving teams in line with the Ametek Airtechnology standard processes to ensure effective corrective action is implemented
- Deputising for the Quality Manager
- Significant Microsoft office skills, including creation
- HNC level education in related discipline
193
Quality Manager Resume Examples & Samples
- At least 8 years of experience in Quality, Manufacturing and/or Engineering with a minimum of 3 years in the quality discipline
- An understanding of P&W Quality Procedures, Quality Management Systems, AS9100 and Regulatory Agency Requirements
- Demonstrated ability to interface with all levels of management and external customers
- Strong knowledge and experience with Six Sigma, root cause and process control tools
- Ability to lead projects, develop and mentor other leaders
- Strong interpersonal and communication skills and ability to facilitate and motivate teams
194
Quality Manager Resume Examples & Samples
- ASN
- Active New York State Registered Nurse license
- Strong hospice skills and knowledge
- Patient-oriented
- Proven data analysis and quality management skills
195
Quality Manager Resume Examples & Samples
- Collect, analyze, and report GMP performance metrics associated with the pharmaceutical development supply chain. Make recommendations to management based on analysis of performance metrics
- Support development of IMP Supply Chain compliance and control strategy and execute effectively. Ensure that IMP supply chains maps are documented and kept current
- Perform risk assessments of the IMP supply chain and make recommendations to management based on the results
- Independently and proactively provide communication to management on new and outstanding supplier quality and internal compliance issues
- Have strong knowledge and understanding of the global IMP supply chain. Identify and analyze risks and quality issues, and develop mitigation strategies
- Collaborate effectively with Global Quality Auditing, IMP Quality, and other applicable groups to ensure creation, accuracy, and maintenance of an annual supply chain audit schedule. Execute an effective strategy to ensure audits are conducted as required
- Ensure appropriate Quality Agreements are in place and maintained with all 3rd parties across the IMP supply chains. Ensure vendor agreements reflect supply chain compliance requirements
- Manage internal quality metrics pertaining to IMP Quality and Pharmaceutical Sciences; assess the results in collaboration with internal stakeholders
- Identify and initiate process improvement opportunities pertaining to the GMP quality management system
- Bachelor’s Degree in Chemistry, Biology, Engineering or related field
- Minimum of 6 years pharmaceutical manufacturing, packaging, or laboratory experience including at least 4 years in GMP QA or Compliance
- Experience working with a global outsourced-based supply chain
- Knowledge and understanding of pharmaceutical GMP regulations ability to apply & interpret in support of Takeda activities
- Demonstrated teamwork, initiative, and problem solving skills
- Strong oral/written communication skills
- Strong relationship management and interpersonal skills. Essential skills include collaboration, maintenance of focus, consensus-building, negotiation and conflict resolution, de-escalation, relevant concept identification and focus on facts, and listening
196
Quality Manager Resume Examples & Samples
- Develop and implement a successful project quality program based upon contract requirements and company quality standards
- Directly supervise and manage inspection and testing personnel
- Develop positive and trustworthy relationships with the client
- Provide technical expertise, troubleshooting and solutions for quality issues
- Ensure proper documentation and recordkeeping is performed, validated and easily retrievable through audits
- Promote and enforce quality processes with the goal of performing work right the first time
- Ensure that all non-conformance work is properly reported, tracked and documented
- Research, read and interpret construction plans, standards and specifications
- Assist with the development of root cause analysis
- Personally meet deadlines and contribute in a positive, safe, professional and high-quality project
- At least seven years’ experience developing and implementing construction quality management programs in the oil, gas, and chemical or Power industry
- Bachelors or master’s degree in mechanical, electrical, welding, civil engineering, industrial or related discipline (preferred)
- Effective organizational, analytical, problem solving and time management skills
- Ability to travel and/or relocate as required
197
Quality Manager Resume Examples & Samples
- Leading the 3M Brownwood Quality Organization
- Developing and implementing the vision and strategy for the plant’s Quality and Lean initiatives
- Driving Improvements in Quality results and advancement of Lean Manufacturing Methodologies
- Maintaining the plant’s current quality certifications
- Works collaboratively with employees at all levels on site and within the global 3M organization
- Willingness to accessible to support the plant operations teams as needed
- Minimum of three (3) years of experience within a technical environment
- Minimum of three (3) years of experience as a supervisor and/or manager
- Bachelor’s degree or higher in a technical discipline from an accredited institution
- Experience in Quality systems and processes, International Organization for Standardization (ISO) certifications, Lean Management Methodologies, Six Sigma and leading functional groups or organizations
- Skills include strong technical aptitude, application of statistics, and excellent written/speaking/presentation skills
- Certified Black Belt
- Microsoft Office proficient
198
Quality Manager Resume Examples & Samples
- Implementation of ISO9000 quality system with additional considerations to ISO/TS-16949 and AIAG guidelines (Automotive Industry Action Group)
- Drive and lead collaborative cross functional teams to determine critical parameters and manufacturing controls to meet customer requirements
- Collaborate with Product Engineering to develop product control plans and FMEAs throughout the lifecycle of the product and equipment
- Determine improvement opportunities using Quality Methodology including statistical methods, and problem solving techniques
- Improve product quality control measurement methodology to ensure that products and processes comply with the relevant requirements of the quality management system and customer expectations
- Work closely with Purchasing and Product Engineering to establish supplier quality performance criteria and monitor supplier performance
- Assess suppliers' product specifications and quality plans
- Perform supplier and internal audits
- Bachelor’s degree engineering, mathematics or statistics
- Implemented ISO9000, 2015 (2008 considered) in another company, preferably a company manufacturing, LEDs, Lasers and other III-V related products
- Language Skills: Ability to read, analyze, and interpret general business periodicals, professional journals, technical procedures, or governmental regulations. Ability to write reports, develop procedure manuals/procedures and conduct business correspondence. Ability to effectively present information and respond to questions from groups of managers, clients, customers, and the general public
- Mathematical Skills: Ability to apply statistical tools for analyses of production processes, and inventory control
- Master’s degree in engineering or equivalent
199
Quality Manager Resume Examples & Samples
- Minimum Bachelor degree in Food Science and Technology/ Agricultural Science with knowledge on FSSC 22000, ISO 9001 and Halal Management Systems QRP; GMP; HACCP, RCA (6W2H; 5 Why Analysis; Fishbone diagram), Loss analysis
- At least 7 – 10 years experience in a manufacturing environment and 4 years in a QA managerial capacity
- Having ISO certification will be an advantage
- Good knowledge of the National Food and Food S
- Good knowledge in SSEafety regulations
- Advanced process knowledge/ manufacturing conversion, logistics operations, procurement, commercialization, and regulatory/health authorities management
200
Quality Manager Resume Examples & Samples
- Ensures ongoing compliance with ISO and Quality System requirements as well as the definition and execution of continuous improvement activities. Recommends improvements related to lab management and reporting systems; assures that procedural and technical consistency meet standards of excellence in a cost-effective manner
- Works with commercial and technical service personnel to identify customer expectations and ensure that these take priority in daily plant activities
- Acts as coach and resource for lab personnel to ensure compliance with all legal and statutory requirements. Provide technical skills support and assessment for laboratory testing and oversees shipment releases
- Participates as member of the local management team and promotes a customer service culture at the plant
- Implements plans to support Global and Regional Quality initiatives, including ISO, Laboratory Information Systems (LIMS), etc. Develops plans for implementation and maintenance of software for Quality documentation management
- Monitors and reports efforts to resolve customer complaints. Develops and maintains operation of the Corrective Action Request System. Develops plan to teach and monitor the use of root cause analysis tools for problem solving and decision-making in the plant
- Plans, prepares and monitors departmental budgets and expenditures. Effectively practice Performance Based Management by coaching and developing employees, direct as well as matrix reports, and assuring effective alignment with the matrix functions. Manages activities of Quality Lab Supervisor, Quality engineers and specialists
- Bachelor/University Degree in Science or Engineering, and minimum 5 years of technical experience in quality in a manufacturing environment
201
Quality Manager Resume Examples & Samples
- In cooperation with the members of that team, the incumbent is responsible for implementing the Quality plan in his/her country ensuring alignment with commercial partners
- He/she will ensure that a Quality Management system is deployed properly in the Cluster in accordance with applicable standards, policies, and procedures as well as current and emerging regulations
- He / She ensures E2E quality oversight for all quality related items in his/her cluster and should be consulted by the Quality associates, when applicable
- He / She ensures that the quality systems supporting the cluster are in a constant state of readiness for planned and ad hoc regulatory audits or inspections conducted by regulatory bodies, competent authorities, or other agencies and JJRC assessments
- He / she will be accountable for the MR execution at cluster level. He/She is responsible to share the MR outputs at regional level
- He/ She is responsible for product release/quality hold / returns decision in the cluster
- He/ She is responsible to conduct he recall at cluster level, according to QRB decision
- He/ She is responsible to assure an adequate internal audit program is in place, as well as the action plan proposal and FUP
- The incumbent makes risk based Quality decisions in his/her country and will consult the regional BQ lead on decisions taken for product disposition in case of deviations
- He/She will be responsible for escalations at country/cluster level
- Lead escalation level 2 meetings, prepare slide deck with all adequate information and oversee processes and follow up actions to address significant Quality issues in the respective LOC
- Ensure PRC decks are robust and addresses all relevant inputs to the regional BQ lead in order to perform PRC meetings (slide decks, HHE, medical impact assessments)
- Support the hiring, training, coaching and development of quality members in the cluster , including the goals and objectives definition and the performance appraisals of the quality associates
- He / She is responsible to communicate the HA of Quality & Compliance issue when needed
- At least 5 years of management experience in a regulated medical industry (Pharmaceuticals, Medical Devices, and / or Diagnostics)
- Working knowledge of the business environment inside a quality organization,
- Demonstrated knowledge of applicable regulations within the country
- Ability to coach employees on quality and compliance topics
- Knowledge of the business environment outside of the quality organization (e.g., manufacturing, product / process development, customer service, etc.)
- Strategic (develop valued added solutions)
- Passionate (for the perfection of the product, brand, innovation and execution)
- Creative (to challenge barriers, and status quo)
- Focused on Results (Customer, Business and Processes)
202
Quality Manager Resume Examples & Samples
- Assure that the Quality Management System (QMS) is performing properly and effectively, is (continuously) improving, and is compliant with plant certifications (such as ISO 9000)
- Assure that plant data security systems are performing properly and effectively, protecting intellectual property (IP) as required by PolyOne and by customers
- Assure that process conditions are monitored, controlled for product consistency, and according to plant and customer specifications
- Assure that process changes are made only according to MSA/CSA process. (Management of change process)
- Assure maintenance of correct customer product specifications in SAP and the plant LRM system
- For quality issues and product specification matters, serve as the the plant’s representative to customers. Also for same, serve as the the plant’s representative to the PolyOne technical community and to the commercial group
- Assure resolution of and communication for customer complaints as required by PolyOne’s (ETQ) customer complaint system, or as dictated by particular situations (considering time-sensitivity, seriousness, etc.)
- Assure effective investigation and corrective action on all plant-related customer complaints
- Assess for QMS knowledge gaps and assure training needs are met for plant personnel
- Keep site personnel informed of current quality issues. Provide prompt communication to plant employees to include immediate notification that can help prevent re-occurrence of an issue. When training is needed as a corrective or preventive action (CAPA), assure that the training is effective and delivered in a timely manner
- Serve as plant representative for all quality and IP related audits
- Own, update, and operate (includes assignments of CAPA’s, etc.) the PolyOne customer complaint system (ETQ). Serve as the site representative and as trainer to users of ETQ at the site
- Ability to explain Quality concepts to plant Operators
- Knowledge of plant's manufacturing systems and processes
- Knowledge of statistical analysis
- LSS experience preferred
- Computer skills: Proficiency with word-processing and spreadsheet applications required (MS Word & Excel preferred)
- Strong organizational & problem-solving skills required
- Excellent oral and written communication skills required
- CQA: Certified Quality Auditor
- CQM: Certified Quality Manager
- CQE: Certified Quality Engineer
- Certification of Lead Auditor training by a recognized entity (ABS, UL, etc.). for ISO 9001:2015 or TS 16949 is preferred (not required)
- Five years of progressively more responsible quality experience in a manufacturing environment to include prior supervisory responsibility
- Experience managing an ISO 9001 Certified Quality System. Experience with TS16949 is preferred
203
Quality Manager Resume Examples & Samples
- 5-10 years’ experience
- At least 3 years Management experience
- Experience in a Manufacturing environment
- Customer management
- Pharmaceutical Regulatory
- Emotional intelligence
204
Quality Manager Resume Examples & Samples
- Analyzes, evaluates and presents information concerning factors such as business situations, production capabilities, manufacturing problems, economic trends and design and development of new products for consideration by other members of management team
- Suggests and debates alternative methods and procedures in solving problems and meeting changing market opportunities
- Cooperates with other top management personnel in formulating and establishing company policies, operating procedures and goals
- Develops initial and subsequent modifications of product assurance program to delineate areas of responsibility, personnel requirements and operational procedures within program
- Evaluates contents of reports from product assurance program department heads and confers with top management personnel preparatory to formulating fiscal budget for product assurance program
- Conducts management meetings with product assurance program department heads to establish, delineate and review program organizational policies, to coordinate functions and operations between departments, and to establish responsibilities and procedures for attaining objectives
- Interface with customers on technical/quality issues and improvement initiatives
- Visits and confers with representatives of material and component vendors to obtain information related to supply quality, capacity of vendor to meet orders and vendor quality standards
- Comply and ensure their staff complies with applicable standards, regulations, and rules regarding to the project they are assigned
205
Quality Manager Resume Examples & Samples
- People development and management of the Quality Team Leaders and their teams
- Conduct weekly 121’s and Team Meetings with the Quality Team Leaders
- Managing the delivery of consistent global quality calibrations across all teams in Customer Care
- Managing the Quality teams delivery of agreed KPI’s for scoring quality
- Ensuring all advisors across all teams are quality scored each week
- Managing the feedback cycle so that all feedback is delivered in a consistent and fair way to all Team leaders on a weekly basis
- Experience within a multi-channel Customer Care environment working at a Management Level is desirable
- Excellent attention to detail and organisational skills
- Logical approach to contextualising and presenting large volumes of qualitative data
- Excellent commercial awareness and understanding of impact that decisions can have on commercial performance
- Excellent communicator at all levels, including senior level stakeholder engagement, communication management between senior departmental stakeholders and their direct reports
- Ability to lead projects within the business through collaboration and working with other departments
- Ability to manage and develop a team in a high performance culture
- Conscientious and responsible
- Proficient in MS Office and databases
- In depth understanding of quality control management procedures and “Best in Class” frameworks along with quality assurance and standards
- Leadership flair with the skill to motivate teams to perform and exceed expectations
- Customer, Company and team centric
- A keen eye for detail and a results driven approach in a fast paced environment
206
Quality Manager Resume Examples & Samples
- Assisting / Leading the QC team members on decisions relating to day-to-day QC to support Delivery reliability
- Lead the site Quality Assurance management system - plant audit to ensure GMP and SOP compliance align to Global Quality / Key customer requirements
- Facilitating Third Party certification and regulatory audits. Site coordinator for SEDEX, Management Representative for Ethical, Quality Management and Food Safety audits.This is measured as compliance to audit requirements during Annual Surveillance Audits
- Facilitating customer audits or visits and revert with corrective / preventive action plans in case of findings as per timelines given
- Facilitating Root Cause Analysis and arriving corrective / preventive actions, including SAP reporting for internal rejections and customer complaints. Focus on continual improvement of both Indonesia and Singapore site quality & operation activities
- Response to Queries and tasks from Regional Quality Director and Corporate Quality
- Weekly and Monthly reporting on QC / Operational Quality KPI's, data & trend analysis
- Focusing on people development and all training aspects
- Organise monthly meetings and lead Quality presentations
207
Quality Manager Resume Examples & Samples
- Provide supervision to Quality Analysts to insure all safety procedures and work practices are being followed
- Mentor, coach, and develop Quality Analysts
- Maintain Quality Analyst staffing/schedule and manage overtime
- Drives changes to manufacturing plant QA lab on method support and testing support
- Maintain and drive improvements in quality specifications for products and raw materials
- Responsible for daily QA metrics
- Help troubleshoot batches for chemistry and/or raw material related issues
- Research customer complaints, when required
- Develops and maintains quality systems for ISO compliance
- BS Degree in Chemistry required
- 5+ years working in a quality or analytical chemistry role in the lab or plant
- Experience supporting oxyalkylation or ethoxylation reaction processes
- 7+ years working in a quality or analytical chemistry role in the lab or plant
- MS in Organic Chemistry
- Good understanding of ISO requirements
- Knowledge of product chemistry and how spec variation affects field performance
- NMR Data Interpretation skills
- Proven record of meeting personal or department goals; motivating peers or direct reports; ushering change; and championing safety
- Ability to work in a team atmosphere
208
Quality Manager Resume Examples & Samples
- Knowledge including: education, qualifications and training
- High Graduate degree in micro, chemical, technological or quality management
- Experience in Statistical Process Control
- Good knowledge of IL6S principles and practical experience in implementation
- In-depth understanding of ISO 9001, FSSC22000, PAS96 requirements
- Expert knowledge of legal and corporate requirements to products’ quality and food safety
- Advanced PC user (Microsoft Word, Excel, Power Point, Internet Explorer, Microsoft Outlook)
- Experienced user of QCMS (SharePoint), iQS and SAP
- Qualified internal auditor of Quality and Food safety management system
- Qualified supplier auditor/developer
- Skills & Competencies
- Strong Leadership skills and role model Servant Leadership
- High levels of learning agility and willingness to take up diverse, challenging assignments
- High level of problem solving and decision making skills
- Ability to coach and mentor multiple stakeholders at different levels of the organization
- Strong English communication and negotiation skills
- Min 10-12 years of experience in the quality function within the food industry, preferably biscuits
- Experience gained in an Operations/Production role will be an added advantage
209
Quality Manager Resume Examples & Samples
- Adopt and implement the Global Quality Management Plan within the scope of the assignment; this will include: o planning and executing the Quality Management activities
- Knowledge of CRO or Pharmaceutical industry operations
- Strong influencing and negotiation skills
- Ability to travel within the region/country
- Bachelor's degree in life sciences or equivalent nursing qualification with a minimum of 7 years’ experience in Clinical Monitoring including at least 2 years’ experience in a role equivalent to a Clinical Project Manager/Clinical Team Lead preferably within Quintiles; or equivalent combination of education, training and experience
210
Quality Manager Resume Examples & Samples
- Minimum 4 years quality management/engineering
- Knowledge of AS9100 Standards
- Candidate must be able to work well in a team environment and work well across various departmental functions
- Familiarity with the ACE operating system
- Highly skilled communicator with an ability to maintain productive relationships in difficult situations
- Candidate must have excellent analytical, problem solving and project management skills
- Familiar with typical operations in an aerospace engine overhaul and repair environment
- Proficiency in MS Office applications to include MS Word, Access, Power point and Excel
211
Quality Manager Resume Examples & Samples
- Bachelor of Science degree in technical field
- 5 to 10 years experience in manufacturing environment in quality position preferred
- Knowledge of Quality Standards especially ISO9001 and AS9100 Preferred
- Certified auditor preferred
- Strong Leadership
- Good training and presentation skills
- Experience in statistical methods, including SPC, capability studies, etc
- Experience in high mix/low volume should be appreciated
- Be responsible for safety awareness in all jobs to help eliminate injuries to yourself and your team members
- Learn and follow all safety requirements. Failure to do so will result in disciplinary action
- Constantly check for safety hazards and ensure problems are rectified promptly
- Maintain a clean and orderly work area
- Report to work fit for duty and not affected by alcohol, drugs, medications or other harmful influences
- Actively participate in safety improvement activities
- Report any unsafe practices by coworkers or contractors
- Immediately report all injuries and other safety incidents
- If you are injured return to work as soon as possible to appropriate duties
212
Quality Manager Resume Examples & Samples
- Provide leadership and guidance to ensure member company compliance to all Quality plan contractual requirements
- Ensure appropriate use of Member Company operating and quality systems (P&W – ACE, GE – six sigma)
- Develop and maintain effective relationships with member company representatives, program partners, Middletown operations and Engine Alliance aftermarket organizations
- Administer EA / Airbus Integrated Quality Plan (IQP)
- Achieve Airbus quality KPI metric
- Lead quality communications with Airbus and Airline Customers (Sales Force)
- Audit engine build records for accuracy and ensure all records are available for customer use at time of engine delivery. Reconcile overhaul and delivery records as requested
- Develop and maintain EA quality standard work
- Provide quality leadership to the EA aftermarket network
- 7 - 10 years’ experience in a technical discipline
- 5 years’ experience in a program quality role or equivalent quality experience, Aftermarket quality experience a plus
- Working knowledge of P&W quality procedures and quality management systems
- Demonstrated ability to interface and communicate with all levels of management within the EA network of Airline Customers, Airframes and Overhaul Operations
- Ability to lead diverse multi-national, multi-functional teams
- Working knowledge and experience with ACE and/or six sigma quality processes
- EASA and FAA Regulatory certification procedures and delivery documentation
- Ability to work independently in an unstructured environment
213
Quality Manager Resume Examples & Samples
- Bachelor’s Degree in engineering, technical or other related discipline
- 10 years of experiences in manufacturing, manufacturing engineering, product engineering or quality assurance. Two years of experience in quality engineering. At least 5 years experiences on supervisory position
- A demonstrated knowledge of quality assurance and continuous improvement methods, approaches & tools, including strategic planning and project management
- Has the knowledge on Six Sigma, Lean Manufacturing, Project Management, Quality Management System standards (i.e. ISO 9000, QS9000, VDA 6.1, etc)
- Have the certifications in: CQM, CQE, CQA is a plus
- Interpersonal Communications and Leadership Skills Development
- Advanced skills in team leading, goal setting, financial forecasting and budgeting, training, cost reduction, policy administration, and achieving results
- Excellent communication skills and interpersonal skills
- Assertive leadership, good team player
- Proactive, possessing initiative, driven with a ‘can-do’ attitude
214
Quality Manager Resume Examples & Samples
- Experience in either a Digital Forensics supplier or a service provider managing a complex 3rd party delivery
- Knowledge of Digital Forensics techniques
- Excellent supplier management skills
- Ability to communicate to both technical and non-technical audience
- Good customer facing skills
- Strong written communication and presentation skills
- High level of drive & motivation
- In depth knowledge of ISO 17025 and related accreditations
- Holds or has ability to achieve UK security clearance to NPPV/SC level
215
Quality Manager Resume Examples & Samples
- Understands and assures conformance to regulations in the microbiology laboratory. Interfaces with regulators during regulatory inspections
- Responsible for ensuring that all systems and processes of the Microbiology Lab are carried out and conform to requirements (GMPs, SOPs, Specs)
- May participate in or manage quality assessments of internal operations and suppliers to analyze compliance and assess risk
- Interacts frequently with subordinate supervisors and functional peer group managers
- Identifies and manages continuous improvement projects with the objective of achieving quality, reliability and cost improvements
- Manages the coaching, training and development of subordinates
- Thorough knowledge of applicable procedures, specifications, regulations and standards
- Good interpersonal/communication/influencing/negotiation skills
- BS in microbiology or biological sciences. 5+ years of experience, which should include 1-2 years of supervisory experience
216
Quality Manager Resume Examples & Samples
- Enable and maintain a culture of quality awareness and compliance in the Site by leading and engaging others in the quality vision and journey
- Ensure Food Safety & Quality programs are developed and executed with excellence
- Manage regulatory relationships and ensure Site compliance to all relevant regulatory legislation, company compliance requirements and Quality and Food Safety certifications
- Facilitate achievement of customer/consumer expectations
- Lead continuous improvement across all areas of Integrated Management Systems, Quality & Food Safety
- Align with plant productivity goals and manage quality department budget
- Effectively manage, lead & develop quality team members
- Develop functional and technical quality skills across site employees
217
Quality Manager Resume Examples & Samples
- Act as the main point of contact for customer complaints by managing issues and ensure they are resolved in line with TE processes and procedures and ensure that customer complaints and issues are resolved with a sense of urgency
- Standardize and coordinate QMS for the Grass Valley site
- Handle customer complaints and Analyze customer complaints and recommend and implement action plans and improved processes to prevent reoccurrence of customer complaints for assigned GPLs
- Analyze customer information and manufacturing processes and data to identify possible risks, understand consequences of costs and determine viability of customer partnerships
- Mobilize teams of direct and non-direct reports to address customer issues
- Support development and maintenance of manufacturing process based on Voice of the Customer (VOC) and product engineering information
- Compile and/or create PPAP where required for manufactured products
- Process Quality System requests as required
- Achieve KPI targets based on FY goals
- B.S. degree in Quality Engineering, Mechanical engineering, Process engineering, Manufacturing engineer preferred or equivalent combination of experience & education
- ASQC Certified (Quality Manager, Organizational Excellence or Quality Engineer)
- Quality, or Lean/Six Sigma belt or additional experience leading the quality function in a manufacturing environment
- Technical skills and demonstrated experience in engineering assignments: ability to read drawings and specification documents
- Minimum 5 years of Quality Management Experience in underwater or mil-aero connectors and cable assemblies required
- Experience managing an ISO9100, AS9100 or QS9000 Quality System
- Experience interfacing with Aerospace and Defense Customers highly desired
- Experience and comfort working in a Global Matrixed Organization
- Proficient with Microsoft Office Suite including Word, Excel, PowerPoint
218
Quality Manager Resume Examples & Samples
- This Lead Quality Manager will proactively identify systemic issues, implement improvement initiatives, and track progress, leading to decreased quality issues on projects
- Review operational performance against the requirements of the Quality Management System (QMS) and facilitate changes and/or corrective actions, as necessary
- Identify performance deficiencies and trends, and recommends/initiates solutions for improvement
- Audits and evaluates performance measurement data, to include surveys and audits
- Leads, coordinates and reports on quality advancement activities
- Provide leadership in the implementation of the quality management system
- Champions the Value Plus and Sustainability Plus programs, leading to increased participation by all operating units
- Frequent contacts with internal and external individuals at all management levels
- Conducts briefings, training, and participates in technical meetings and pursuit interviews related to specific operations
- BA/BS degree in a related field and 15+ years of related experience, or an equivalent combination of education and experience, is required
- The ideal candidate will have experience in both buildings and infrastructure projects
- Experience working in a dynamic integrated multi-team environment is essential
- Strong PC skills to include Microsoft software required
- Strong interpersonal and communication skills is a must
219
Quality Manager Resume Examples & Samples
- Demonstrated experience as an action oriented leader with the ability to make decisions that always protect product safety for products and services provided by the business
- Strong ability to properly balance good compliance practices with other business initiatives to avoid conflict and allow all objectives of the business to be satisfied
- Demonstrated experience with balancing multiple and sometimes conflicting business objectives
- Experience with managing and working in a matrix organization (dual reporting relationship to Quality function and Local Management
- Must be a driver of continuous improvement
220
Quality Manager Resume Examples & Samples
- As a Qualified Person, you will have responsibility for product release. As such you will ensure that each batch released has been produced and tested in accordance with current EU GMP directives and the relevant marketing authorisation
- Reporting to the Managing Director the Quality Manager is responsible for the management, direction and co-ordination of all quality activities across the site
- As a key member of the site leadership team you will contribute to all areas of company strategy, policy development and general management
- As Quality Manager you have responsibility for the following areas
- QP Function
- In your role you must remain independent of other departments within the company
- You must ensure that adequate resources, equipment and facilities are available for Personnel within the Quality department to fulfil their responsibilities
- To ensure compliance with the requirements of Good Manufacturing Practice (GMP) and Good Laboratory Practice (GLP)
- To oversee and direct the management of the QA, QC, and the QP function
- To ensure that adequate resources and appropriately trained and experienced personnel are available to manage the Quality System. This includes but is not limited to the following systems
- Process Deviation Reporting
- Supplier and Subcontractor Approval, Complaints and Performance
- Batch File Review
- Material and Product Disposition Systems
- To manage the plant recall procedure
- To oversee plant validation
- To ensure adequate records are in place to provide full traceability
- To ensure all GMP critical SOPs and batch records are approved by the Quality Department and to ensure that all Quality documentation is maintained up-to- date and compliant with cGMP
- To lead all Regulatory and Customer GMP Inspections and to manage related follow-up activities
- To manage the site internal auditing procedure
- To approve and monitor contract manufacturers and contract testing laboratories
- To be the contact person for interactions with the HPRA and other Regulatory Authorities as required
- To act as Management Representative and to manage the maintenance of the Quality System as required by the Medical Device Regulations
- Review customer complaints and modify processes as necessary to eliminate defects
- To manage and guide the activities of the Quality Management personnel and to monitor and review performance
- To perform the role of Responsible Person overseeing the wholesale activities in compliance with WDA licence
- A minimum of 8 years post-graduation experience in Quality environment with at least 3 years in a management role
- A third level qualification in a scientific discipline and relevant experience in the pharmaceutical industry
- In addition you must have fulfilled the education requirements for the role of the Qualified Person
- Good organisational ability and initiative to be able to work to and meet deadlines in a result orientated environment
- Strong leadership skills and the ability to work in cross-functional team environments, as well as independently
- Strong attention to detail and good decision making skills
- Good IT skills
- Will be proactive and flexible
- Knowledge of lean systems and tools
- Experience of continuous improvement within
221
Quality Manager Resume Examples & Samples
- Implement the quality management system processes and procedures, and maintain supporting documentation to ensure the integrity of the quality management system
- Assure that all activities comply with quality procedures, all applicable government regulations and contract requirements
- Maintain quality records required by the QMS and regulators
- Address customer complaints, perform DIFA , drive CCR process and analysis and set objectives for CCR closure
- Prepare and submit Quality reports required by the customers and Quality System
- Develop Quality related procedures and work instructions fas needed by the bussines
- Work closely with the Surface Quality Leader, Site Manager and the Geo Market Director to drive the quality programs and culture within the business
- Establish means of collecting relevant data for the goals and analyze the data to monitor for trends and establish project decks to drive improvements with the support of the leadership team and their staff
- Establish goals, objectives, and work plans, such that lowest cost and highest quality results are achieved
- Assure audit of areas of responsibility for conformance to quality plans, systems, and requirements
- Establish and maintain training matrix for field service engineers and other functions at the site
- Provide training for key personnel charged with the implementation of the process improvement efforts throughout the organization
222
Quality Manager Resume Examples & Samples
- Manage the activities of a section or department in the Quality organization with responsibility for results in terms of product quality, performance and safety. In some instances this manager may be responsible for a functional area
- Implements the quality systems procedures and manages compliance in a section or department
- Write, approve and manage CAPAs within the area of responsibility
- Understands and assures conformance to regulations in a section or department. Interfaces with regulators during regulatory inspections
223
Quality Manager Resume Examples & Samples
- Manages program compliance to numerous systems, and standards
- Interfaces with the Customer and program management on quality related matters
- Manages the execution of the program quality plan, including sub-contractor Quality teams
- Works with product development, and operational management, in coordination with Director of QA to define, iterate, document, and enforce QA processes and procedures
- Lead, direct and motivate a culture of quality improvement across program and business teams to eliminate inefficiencies/ defects, and drive root cause analysis and lesson learning
- Communicates QA expectations to teams; plans, monitors, appraises, and reviews contributions, and enforces policies and procedures
- Analyze data, concluding results to program management and Director of QA
- Represents QA organization during audits, reviews, action boards, and customer meetings
- Prepares QA documentation in pursuit of bids and proposals
- Supports vendor assessment and management of the quality deliverables
- Acts as leader/facilitator between QA and other functions
- Provides QA Director with input regarding decisions and actions for the QA function
- Fulfills the QA Director responsibilities in director’s absence
224
Quality Manager Resume Examples & Samples
- Lead and coach the organisation in relation to quality to drive standards
- Establish and maintain the Quality Management System across the sites covering ISO 9001:2008, AS9100 and ISO TS 16949:2002
- Work with the Swindon Sites to achieve new industry/ customer approvals as required
- Ensure compliance with trade licensing rules
- Manage the internal audit programme, including supplier audits where required and the corrective actions process
- To ensure that the company procedures and systems are continually reviewed and maintained in line with Industry Quality Standards
- Local quality representative, to be able to hold people accountable for their actions and deliverables for quality
- To introduce, coach, and engage cross functions teams to conduct root cause analysis on both internal and external quality issues and formulate resolutions in a timely manner. Also, to ensure the implementation and effectiveness of actions and prevent problem from reoccurring
- Report and respond to customer quality ratings/ scorecards
- Manage Contract Review on Customer Quality Assurance Requirements
- Identify gaps and opportunities and drive continuous improvement throughout the organization
- Communicate and coordinate with sister companies when quality issues arise
225
Quality Manager Resume Examples & Samples
- BS Engineering or Technical field
- 21 CFR 210 & 211. Working knowledge of FDA regulations and experience with interacting with external agency audits necessary
- Good organizational skills a must. Effective communication skills needed to provide clear and concise information to team members
- Technology Skills: Windows, MS Word, MS Excel, Database Management. Will require training for CATSWeb
- Certified ASQ CQE and/or Lean Six Sigma Green belt preferred
- Training in problem solving tools is required (Process Mapping, Histograms, FMEA, Risk Assessment, Cause & Effect Diagrams, PCDA, Pareto Analysis)
- 8+ years’ experience in pharmaceuticals, with a minimum of 5 years in complaint management. Supervisory experience required
226
Quality Manager Resume Examples & Samples
- Provide leadership assuring that necessary quality systems are in place for compliance to customer requirements: coordinate/facilitate CAB and management reviews, support leadership team meetings, and facilitate all audits
- Manage all aspects of associates’ activity as to provide growth and foster development and motivation
- Prepare and manage manpower and budget plans to achieve optimum results
- Generate, maintain and provide quality metrics to the UTAS ISR-SS Management Team and oversee quality system improvement projects
- Work with management to ensure that a quality culture is prevalent while promoting problem resolution activities that support the customer as well as the producer
- Participate on teams that continually strive to improve the quality of our products and culture as needed
- Provide Quality support and maintain a strong working relationship with other functional disciplines and the entire Quality organization in general
- Must display excellent teamwork and problem solving skills, and have the ability to drive projects to completion
- Strong Quality System knowledge and familiarity with SAP system transactions
- Minimum 5 years relevant experience
- Understanding of Internal and External Customer requirements with a high attention to detail is a plus
- Excellent verbal/written communication and presentation skills appropriate for direct interaction with Management & Supplier/Partners
- Good computer skills in MSOffice applications
- Ability to work in a highly structured environment, with frequent customer interactions
- Must be adaptable to changing priorities
227
Quality Manager Resume Examples & Samples
- Leads ISO 9001 compliance at the plant: owns the Internal and External Audit Program, CAPA and Calibration Services for the plant; creates and maintain work instructions, visual instruction booklets and process picture maps in accordance to ISO 9001 standards; sets up and administers audit system for internal and external providers of products. Collects and reports on Customer Quality indicators; and drives complaints and other quality indicators results. Improves product quality using advanced quality tools e.g. SPC, FEMA, & Process Control to monitor and improve quality at the assembly station, rather than downstream
- Maintains all engineering specifications, bills of materials, and job routings for the plant in accordance with ISO 9000 procedures and UL, ETL and NSF certifications. Develops dish machine refurbishment parts and labor standards and is responsible for product cost estimating, the processing of engineering changes (both from the plant and corporate requests). Supports qualification and rating of raw material, packaging material, and finished goods vendors. Ensures raw materials, packaging materials, finished goods, and distribution activities have and meet specifications. Develops validation requirement for new equipment/tools installation
- Collaborates cross functionally in the development of new product offerings, contributing to the design and engineering of dish machines, Booster Heaters, field service parts, and other products to ensure manufacturability of products when transferred to production or refurbishment. Ensures continued adherence to safety, quality, cost, and productivity standards. Coordinates the transition of new products from design to production with Corporate Engineering, Planning, Production, Purchasing, and Marketing
- Promotes the generation of and implements ideas for projects that improve quality indicators, processes and systems in line with customer, cost, investment and service goals or to identify the root causes of quality/engineering issues and to implement processes to resolve and prevent issues. Leads and participates in projects to improve new and existing workflow processes, to identify and implement cost savings opportunities and to dispose of obsolete products
- Bachelor’s degree in Engineering, Science, Math or Technology
- 7+ years Quality Systems experience
- 4+ years of experience in manufacturing, supply chain and/or RD&E function with increasing levels of responsibility
- 5+ years of experience managing quality improvement projects
- 5+ years of experience in an ISO 9001 registered or GMP/regulated facility
- 3+ years of experience in an assembly / component manufacturing industry e.g. automobile, appliance, or HVAC
- Demonstrated experience in Progressive Quality and Total Production Management (TPM)
- Six Sigma Certification (Green Belt or Black Belt)
- 1+ year experience applying the Toyota Production Systems principals in a Lean environment
- 1+ year of experience using statistical process control to monitor and improve quality
- Experience with creating and maintaining bills of materials
228
Quality Manager Resume Examples & Samples
- Give feedback to vendors/linguists/translators regarding the quality of the translation by actively involving in our vendor coaching initiatives
- Investigate client complaints regarding translations – holding both freelancers and full-time employees accountable
- Perform other special projects or duties when required, such as to participate in client-facing conference calls when needed
- At least 2-4 years of office environment working experience (preferably as part of a team)
- Native or near-native English as well as native or near-native Chinese speaker with excellent written and verbal communication skills in both English and Chinese
- Excellent problem solving and time management skills, under deadlines in various time zones worldwide
- Ability to maintain effective and prompt communication with peers
- Ability to work with multiple software tools (including Microsoft Office and web-based tools) on each project
- Familiarity with computer text input tools for both Simplified and Traditional Chinese
- Self-motivated and can work independently on each of assigned projects as well as being a good team player in a language group when a group effort is required
- Experience with basic Microsoft Office programs (Word, Excel, PowerPoint), as well as Adobe Acrobat PDF marking tools
- Prior translation industry and/or life sciences industry experience
- Master’s degree in translation-related linguistics studies
- Prior exposure with using CAT Tools such as Trados or SDLX
- Experience working with encrypted or password-protected files
229
Quality Manager Resume Examples & Samples
- Address customer complaints and drive CCR process and CCR analysis and set objectives for CCR closure
- Develop Quality related procedures and work instructions as needed by the business
- Work closely with the Surface Quality Leader and the Geo Market Director to drive the quality programs and culture within the business
- Assure that all activities in service/repairs comply with quality procedures, all applicable government regulations and contract requirements
- Address customer complaints and drive CCR process and drive CCR analysis and set objectives for CCR closure
- Establish and execute project quality plan, witness-points, quality records for compliance with contract
- Establish and maintain training matrix for field service engineers. Provide training for key personnel charged with the implementation of the process improvement efforts throughout the organization
230
Quality Manager Resume Examples & Samples
- Perform contract reviews for new customers/products by reviewing customer purchase orders, product/quality specifications and any other documentation to ensure delivered products meets or exceeds customer expectations
- Develop, prepare and implement Quality Program Plans for new and existing customers and products
- Function as primary liaison for various customers in order to resolve quality issues, ensure appropriate flow down of quality requirements, enable positive channels of communication, and ensure customer satisfaction
- Provide FAA Designated Manufacturing Inspection Representative (DMIR)
- Coordinate and perform internal audits, update and prepare schedule, review and prepare final reports, and provide overall report on progress of audit program to management
- Must have experience managing a team of direct reports; multi-site management experience and/or international management experience a plus
- The right person will be ambitious and flexible who wants to learns and grow professionally
- Strong computer skills are a must, to include: Word, Excel, PowerPoint; experience with Lotus Notes Databases is a plus
231
Quality Manager Resume Examples & Samples
- Responsible for development and sustainment of a culture of safety, quality and professionalism within the assigned areas
- Responsible for the development and maintenance of URS’ Quality Control Plan, Quality Management Plan and Quality System Plan, assuring appropriate corrective actions are directed
- Monitors and audits for compliance with contract Quality requirements to include URS Quality Policy Manual, URS instructions and procedures, PWS, Army regulations (including DA PAM 738-751 and TC 3-04.7, Chapter 9), applicable technical requirements, Government instructions, OEM guidance/commercial and manuals or portions thereof, applicable technical messages for surveillance techniques, and performance thresholds contained in the PWS
- Manages or oversees the implementation and maintenance of International Organization of Standard (ISO) 9001 or SAE-AS9100 procedures, registration, compliance and Lean Six Sigma (LSS) events
- Familiar with Government QASP; Coordinates, supports and cooperates with Government Quality audits and other surveillance methods
- Directs quality self-assessments and investigations and develops and leads quality improvement initiatives
- Responsible for the administration of Company policies
- Directs the implementation of performance management tools by subordinate managers and supervisors
- Current working knowledge of US Army regulations and requirements for rotary wing maintenance
- Experience developing and maintaining an ISO9001 and/or AS9100 compliant quality systems for a military aircraft operation
- Lean Six Sigma Black Belt
232
Quality Manager Resume Examples & Samples
- Manage ISO/TS16949 quality system (audit & improve)
- Manage customer complaints – quality answer in SMART, sample analysis, build action plan & follow-up, joined customer
- Visit with sales or customer technical service (CTS)
- Manage customer satisfaction survey
- Manages QC lab team to ensure the internal quality check (Gage R&R incl.) and that control plans for both raw materials
- And finished goods are fully and well implemented
- Manage HSE on his/her perimeter
- Troubleshooting for potential quality issues
- Organize jointly with the production team the plant quality inspections, the operators training, and control of the
- Application of procedures in both plant and warehouse
- Audit and evaluate with the purchasing team suppliers & subcontractors performance to help ensure a stable quality supply
- Lead and monitor the Industrial Performance and quality Improvement plans on the site through quality
- Tools (six sigma, WCM) and implement best practices
- Coordinate the Operational Change Management process (OCM)
- Participate to the global network of QC/QA managers within EP to share and implement best practices and new processes
- Bachelor or above degree in Material science relative quality control and QA
- Good command of spoken and written English and Chinese
- At least 5 years plant operation management experience (production / QC /QA)
- ISO/ TS audit certificate
- Impact and influence (incl. good communication skills)
- Fact based & Pragmatic
233
Quality Manager Resume Examples & Samples
- Provide leadership and direction for the development of policies and plans for quality control for the project
- Develop a monitoring program to ensure design development and completion of work is in compliance with contract specifications as these relate to quality requirements
- Provide technical support to the bid process and proposal evaluation as it relates to quality compliance and implementation
- Provide assistance in audits and verification of consultant and contractor compliance with Quality Management Plans
234
Quality Manager Resume Examples & Samples
- Engineer degree with a minimum of 5 years leadership experience in a manufacturing environment 3 years of experience in Quality position
- Fluent verbal and written communication skills in both English and French is required
- Experience building a Quality management system
- Six Sigma GB, BB and LE are preferred
235
Quality Manager Resume Examples & Samples
- Directs the management, integration, and coordination of quality efforts as it relates to a logistics management/maintenance program
- Maintains established Quality Management System ISO-9000:2015. Oversees the review of written procedures and implementation of any actions needed to ensure designated certification(s) remains active
- Understands, assures compliance with, and improves established company policies and procedures. Is responsible for development of standard work, policies and procedures, business tools, and business process communications
- Determines MPF Program objectives and implements quality management policies, processes, and procedures to ensure on-going compliance with program objectives
- Develops, evaluates, and implements changes in work operations and processes to improve operating efficiencies
- Monitor, audit and evaluates all logistics and maintenance operations to prevent defects/errors and to verify adherence to quality plans and requirements
- Formulates, interprets, and ensures on-going compliance with internal quality policies, practices and procedures
- Leads quality initiatives and/or related projects. Directs projects through different phases, manages project resources, monitors project status, generates progress reports and keeps management informed of issues
- Develops and maintains a strong, effective relationship with customer, acting as primary interface between customer and daily program operations/administration
- Uses problem solving skills in situations where general standardization should exist but may not be operating effectively. Uses process mapping techniques leaning heavily on Six Sigma and Lean to reduce waste and inefficiency
- Maintains MPF Quality policies and procedures and ensures on-going compliance with such
- BA/BS degree in a scientific field (i.e., quality assurance, statistics, mathematics, production management) or engineering discipline or other related field
- Ten years of progressively complex experience with a working knowledge of quality assurance programs, methods, and techniques pertaining to logistics management, including 8 years in a management capacity involving various aspects of cost/schedule controls, performance monitoring, report writing, program planning and customer interface
- Must have Black Belt Certification
- Must have Lean /Six Sigma experience
- Ability to obtain a Favorable Government Public Trust Investigation
- Ability to obtain and maintain Military Base Access
- Ability to obtain and maintain a Common Access Card
- Complete the Logistics Officer Course or equivalent
- Working knowledge of Marine Corps shipboard equipment/materiel and associated logistics processes
- Working knowledge and application of quality assurance concepts, principles and techniques
- In-depth understanding of the services MPF provides to the customer and the processes and techniques used to deliver these services
- Working knowledge of personnel management, concepts, principles, and techniques
236
Quality Manager Resume Examples & Samples
- Associates Degree in Nursing
- CPHQ Preferred
- 3 yrs Experience as RN in Acute care or hospital preferred
237
Quality Manager Resume Examples & Samples
- Micro Project Manager, who
- Drives Corrective- and Preventive Actions and Improvement Projects and Activities
- University degree in natural or pharmaceutical science (health science, biology, biochemistry area) with relevant professional experience
- Several years experience with Varelisa and EliA products
- High level of people management, negotiating, decision making and problem solving skills
- Independent and well-structured approach of tasks
- Excellent team working and communication skills
- Excellent spoken and written language skills in English
238
Quality Manager Resume Examples & Samples
- Builds people capability through effective employee relations, hiring, training, and communication for both management and front-line hourly personnel
- Ensures compliance with all Health & Safety regulations and Good Manufacturing Procedures
- Leads the Total Productive Manufacturing (TPM) Quality Pillar
- Leads Lean Six Sigma projects, as needed
- Prepares plant for annual quality audits
- Bachelor's Degree and/or a minimum of 5 years of previous Quality Control work experience
239
Quality Manager Resume Examples & Samples
- Responsible for monitoring and maintaining the plants Quality systems to ensure compliance to regulatory, federal, and local laws
- To direct the activities of the Quality Department to ensure that raw materials, packaging materials, in process products and finished products conform to all specifications
- Assist in the development of new quality/regulatory systems and personnel and also serve as a resource for plant quality and manufacturing functions
- Provide leadership and technical assistance by aggressively managing food safety and compliance systems, instilling regulatory awareness and commitment
- Establish ongoing continuous improvement activities which will deliver reductions in consumer complaints and ongoing process control improvements
- Own the IL6S Quality Management (QM) pillar – working with pillar and core team members on work processes to identify, track and eradicate all quality losses
- Support the development of Quality Improvement Plans and direct employee involvement for production/quality issues through to resolution
- Assists in the identification and achievement of facility Quality KPIs through appropriate corrective/preventative actions and continuous improvement initiatives
- Leads all internal and external auditing activities and follow-up. Assures the plant maintains compliance to external / 3rd party standards such as ISO 9001 and FSSC 22000
- Ensure all required quality/regulatory training is maintained throughout the facility
- Support the commercialization process and provide technical expertise for the Quality and sanitation perspective
- Ensure that products are produced to specification to meet safety, quality, and regulatory requirements via system implementation, training, and auditing
- Primary plant Quality Resource
- Member of plant leadership team setting the strategic direction for the facility
- Lead the Quality Functional department including compliance, sanitation and quality
- Responsible for salaried direct reports and functional leadership for the site, indirectly responsible for sanitation and quality personnel
- Bachelor’s degree in Quality, Food Safety or related field
- Minimum of 5 years’ direct manufacturing experience in food producing facility (operations, quality, sanitation, safety)
- Minimum of 5 years’ experience as a leader in a HPWS team Environment
- Minimum of 5 years’ experience leading and managing a diverse work force
- Minimum of 5 years’ experience directly managing food quality, sanitation, receiving and delivery processes
- Sound understanding of quality, sanitation, and warehouse environments
- Strong leadership and people/team development skills
- Proven organizational skills
- Proven communication and leadership skills that support a workforce in a HPWS environment
- TPM / World Class Manufacturing / IL6S (Integrated Lean Six-Sigma) experience at a manufacturing facility
240
Quality Manager Resume Examples & Samples
- Manage and oversee project quality to ensure compliance to codes, standards, regulations, equipment specific specifications, and QMS requirements
- Advancing quality achievement and performance improvement throughout the organization
- Managing the development and implementation of the QMS for planning, fabrication, inspection, documentation, and operations activities including
- Minimum of 12 years of quality inspection experience on pressure equipment
- Petrochemical or oil refining plant owner / user organization work experience
- Certifications in API 510, 570, and/or AWS-CWI or ability to obtain
- Advance knowledge of qualifying ASME WPS and welder/welding operator qualifications, including local regulation requirements
241
Quality Manager Resume Examples & Samples
- Represent customer requirements internally
- Define, staff, and develop the Plant Quality organization
- Collaborate with the Purchasing organization in all activities and initiatives concerning Supplier Quality Assurance
- Interrupt the manufacturing or the delivery of products when Quality is not assured
- Manufacturing experience, preferably in the automotive industry
- Solid knowledge of Quality in Production
- Process orientation
242
Quality Manager Resume Examples & Samples
- Ensures ongoing compliance with ISO and Quality System requirements as well as the definition and execution of continuous improvement activities
- Manages the continuous improvement process within the plant including daily control and statistical methods
- Recommends improvements related to lab management and reporting systems in concert with regional and global team; assures that procedural and technical consistency meet global standards of excellence in a cost-effective manner
- Works with sales and technical service personnel to identify customer expectations and ensure that these take priority in daily plant activities
- Monitors and reports efforts to resolve customer complaints. Develops and maintains operation of the Corrective Action Request System
- Develops plan to teach and monitor the use of manufacturing statistical tools for problem solving and decision-making in the plant
- Supports local site for improvements regarding QA, QC and laboratory activities in the plant, target with manufacturing and regional quality group specific quality goals/gaps and identify/prioritize statistical methods to resolve problems
- A champion of Continuous Improvement process
- Experience with Lab Info Mgt Systems (LIMS); lab procedures & equipment; ISO Management; Mfg. Process Control; QA/QC Problem solving techniques; product uniformity, variation and specifications; Statistical Process Control; Safety
243
Quality Manager Resume Examples & Samples
- Lead the development and deployment of the Quality strategy for Hydraulics EMEA Region ensuring alignment with Global Hydraulics Group
- Ensure the Hydraulics EMEA Plants comply with applicable Eaton, customer and industry-specific Quality requirements by conducting the necessary audits and assessments and determine system effectiveness
- Ensure that quality-related KPIs are reported correctly in EPM and on time
- Recover cost from internal/external suppliers due to quality-related issues
- Continually improve the capability of the Quality organization through ongoing development activities and identification of talent to promote functional bench strength. Ensure deployment of Eaton’s quality functional excellence tool set and provides input to development plans for functional reports
- Champion the Eaton Quality System (EQS) within the Region. Identify and lead initiatives across the organization to address common barriers for the plants and enable improvement in effectiveness and efficiency of EQS. Responsible for overseeing utilization of EQS to control and improve key regional quality processes and plants
- Support the Operations Assessment (OpA) process as a Lead Assessor for Quality and represent the Quality Function in the OpA Leadership Review (OpA-LR) process for the EMEA Region and identifying common themes and actions
- Lead bi-annual Quality functional reviews with specific focus on EQS self-assessment effectiveness and maturity, corrective and preventive actions, timely closure of actions, and other items as required
- Overall ownership of the Quality Alert and Escape Management process for the Region. Ensures timely escalation / communication of customer spill incidents, and coordinates with Group, Plant Quality/OpEx, and Supplier Development colleges to ensure appropriate containment, root cause, and corrective actions are undertaken with the utmost urgency
- Effective communication with Customers in case the customer requires direct visit and clarification on quality related issues. Coach plants in case of HSCQE (high severe customer quality escapes)
- Support the management of performance and provide career development opportunities to all the employees within the quality and warranty function of the organization. This includes the development and implementation of training programs to build “bench strength” in the organization
- Communicate and report of the development of Quality and Warranty performance to senior leaders in the company
- Support the implementation of 6-sigma in accordance to Corporate and Group guidelines
- Certified Quality Engineer (CQE) and Six Sigma Greenbelt – required
- Certified Manager of Quality / Organizational Excellence (CQM / OE), ISO-9001 Auditor and Six Sigma Blackbelt – preferred.EQS Assessor, ISO 9001 Lead Auditor certified, Six Sigma, Lean Manufacturing, Project Management, Interpersonal Communications and Leadership Skills Development
- Ten years of experience minimum in manufacturing, engineering or quality assurance with demonstrated ability to drive results in the area of Quality, continuous improvement
- Three 3 years of experience in a role with multiple site responsibilities is preferred
- Demonstrated knowledge of quality assurance and continuous improvement methods, approaches and tools, including strategic management and project management
- In-depth experience with the practical application of Quality tools, Six Sigma, and Lean Manufacturing methodologies
- Demonstrated knowledge of Quality Management Systems such as ISO-9001, TS-16949, AS-9100
244
Quality Manager Resume Examples & Samples
- Conduct internal and external quality audits, including customers’ audit, according to Quality System requirement
- Review and update existing quality control system with the support and guidance from the global quality team. Ensure that the quality management system and strategies are implemented and complied throughout the Site
- Review and optimize testing methods, equipment calibration and maintenance as required by Quality system and specifications, to ensure RMs and packaging material, semi-finish goods and FGs quality meets customers’ requirement
- Conduct RMs supplier audits according to quality management system
- Manage and track customer complaints, both quality and logistic related. Investigate root causes and develop short term and long term solutions. Respond to customers the investigation outcome and preventive action to the customers
- Implement ALPS/TRACC in continuous improvement
- Any other responsibility that may be assigned as required by the business and operation, within the AkzoNobel business principle and legislative requirement
- Bachelor degree in chemistry or chemical engineering
- Good skill in PC including Word, Excel, PowerPoint, etc
- Good communication and presentation skill
- Good leadership and collaboration skill
- Customer and Team Focus
- Experience in ISO9001/ISO14001/OHSAS18001/ TS16949
- Good English listening, speaking, reading and writing skill
245
Quality Manager Resume Examples & Samples
- Bachelor’s Degree in Business, Finance, Operations or related fields
- Progressive operational experience in a formal or informal leadership role, preferably with some tenure at a Fortune 100 company
- Leadership experience of individuals with a span of control at least 10 associates
- Critical and analytical thinking skills to ensure your operation is data-driven and on the path to meet and exceed KPIs and goals
- Leadership experience with leading multiple teams
- Experience with quality control or auditing for process and/or regulatory compliance
- Experience or working knowledge of grievance and appeals, and/or Medicare Advantage
- Prior experience in a health care or insurance setting highly desired
246
Quality Manager Resume Examples & Samples
- Develop and implement plans for receiving inspections
- Certify and decertify vendors and products
- Audit vendors
- Apply sampling plans
- Control mechanical measuring equipment
- Maintain national standards of certification, calibration and traceability
- Develop and implement plans to control and improve quality in the Fabrication and Subassembly areas
- Maintain ISO 9000 registration
- Control and document scrap materials from manufacturing and control stores
- Perform process capability studies
- Manage the quality audit group
247
Quality Manager Resume Examples & Samples
- Data Management and Reporting –Compile data, generate reports, make recommendations, and help implement solutions for quality and production teams to improve product. Must be active participant in all quality and manufacturing programs
- Material and Finished Product Inspection –Oversee and/or perform finished product inspections to make certain boots meet expected quality standards and aesthetics
- 5+ years quality/engineering experience in a production environment required
248
Quality Manager Resume Examples & Samples
- Accountable for the coordination and integration of quality assurance processes and procedures in the following areas: Government and Regulatory compliance (ISO, AS, TS, FAA, DCMA), Customer Quality Compliance, and internal quality procedural compliance
- Establishes and executes site level strategic quality plan to meet business objectives and customer expectations. Supports group level strategic quality plan
- Develops and holds staff accountable for quality metrics that enable evaluation of progress to the site strategic plan and goals
- Develops staff and supports the site regarding implementation of PLC, APQP, Lean, process capability/First Pass Yield and continuous improvement initiatives while implementing and maintaining an effective Six Sigma System
- Represents Woodward from the site level to customers, potential customers, regulatory bodies through presentation and communication of the Quality Management System and quality strategies to meet or exceed customer expectations while providing advocacy
- Accountable for effective Root Cause and Corrective Action within the site or business area/value streams for escapes (internal or customer) and ensures an effective internal and external corrective action process (timely and effective closures of Corrective Action Requests - CAR's)
- Report customer and internal quality metrics to management and other business segments as needed. Drives with site leadership, corrective action and problem solving to accelerate improvements
- Stay abreast of current quality and regulatory trends and methodologies in the applicable industry and utilize this information for developing proactive strategies and readiness
- Provides direction, development and performance management of direct reports
- Develop and maintain an appropriate site quality organization to support the successful adherence to the QMS and the transformation process enterprise wide. Accountable to manage quality resources to meet the financial plan
- Leads and develops in others the behavioral application and adherence to the Woodward Constitution, Codes of Business Conduct and Ethics (Policy 1-14) and participates and leads BCOC investigations as needed
- Supports Quality Director/Group Director in site transition toward an ever improving One Woodward quality system
- Collaborates with functions inside and outside the organization (Enterprise Wide)
- Leads or influences systematic support of Six Sigma and problem solving for the site. Leads Black Belt projects for challenging business issues
- Sets high quality standards and demonstrates a firm commitment to quality and continuous improvement
- Must be able to travel to customer and other Woodward sites, domestic and international independently
- Strong understanding of: QMS; Processes approach; ISO, AS and TS; APQP; LEAN principles; Six Sigma tools and methodologies; other continuous improvement methods to support lean order fulfillment processes
- Strong knowledge of statistical concepts and methods to ensure appropriate application and analysis of data, with strong ability to analyze issues, solve problems and develop others to do the same
- Ability to collaborate, develop and integrate site strategies for quality performance and continuous improvement. Supports site strategy development with Directors and managers and can follow through with implementation at site level
- Strong oral and written communication with all levels of the organization, but in particular at the site leadership level, and at customer leadership level
- Able to lead and develop a vision and strategy for the site level QMS, including gaining alignment and support of key site stakeholders
- Strong collaboration and influencing skills with peers and leaders across the site and, as needed across the CoE. Supports the improvement of processes across the site and on a per project basis at the group level
- Ability to work across the site's value streams (enterprise wide - supply to customer) to achieve site and value stream performance objectives
- Excellent time management and project management skills to organize and plan effectively in developing effective systems and processes at the value stream, area and site level
- Strong people and leadership skills in coaching, motivating and leading others
- Ability to understand and work effectively with various cultures
- 8 years quality and/or operations leadership in a manufacturing environment required
- 3 years experience working with quality management systems with solid understanding of quality management systems, process approach, and continuous improvement methods and tools required
- 3 years quality and/or engineering leadership experience supporting a manufacturing environment preferred
- Proven leadership capability for collaborating with internal and external customers toward continuous improvement required
- Program management and new product launch leadership experience desired
- Experience with APQP and process capability improvement required
249
Quality Manager Resume Examples & Samples
- Customer Satisfaction & Quality Project Manager / Country
- Manages the Process/Continuous improvement within their unit to supportCustomer Satisfaction and Quality
- Manages cross functional teams, implements operational technique and performs activities aimed both at monitoring a process and at eliminating causes of dissatisfaction
- Management of KPIs improvement action plans and follow-up techniques
250
Quality Manager Resume Examples & Samples
- Responsible for maintaining safe working conditions and practices to ensure the safety of all employees by performing as applicable, regular workplace inspections, monthly safety talks, staff meetings, review of accident investigations, correcting unsafe acts or conditions as observed and commending employees on positive health and safety performance
- Complies with all Company Safety policies, procedures and rules
- Ensure all Quality departmental objectives and activities are aligned to the CSS Bill of Rights
- Adheres to Technical System Procedures, Quality instructions and compliance to all CSS policies and procedures
- Responsible for coordinating and managing the supply base to ensure consistent flow of defect free materials for production requirements within the CSS facility
- Responsible to ensure that the performance measurable related to the materials department are on track with the departmental Key Operating Indicators (KOI’s)
- Deliver on commitments made, treat people at all levels fairly and with respect. Responds to employees concerns in a timely manner (general issues, safety concerns, etc.)
- Responsible for providing clear and specific performance feedback. Develop others and improve employees’ performance through coaching, training, development activities and completing annual performance appraisals for all direct reports
- Responsible for design, development and implementation of quality systems and works directly with CSS engineering department in design, build and approval of new/revised tools and processes affecting the manufacturing operations
- Plan, coordinate, organize, manage and review internal quality audits of the TS 16949 Quality System to ensure conformance; follow up all quality related non conformances found during audits to ensure corrective action has been taken
- Ensure all testing and measuring equipment is maintained, verified and accurate as per the procedures outline in the TS 16949 Quality System
- Prepare annual budget and monitor performance of Quality department, providing explanations for variances to budget
- Develops procedures and systems to ensure total Quality performance and complete conformance with all Customer Requirements, supporting efforts aimed at Continuous Improvement of all operations,
- Work with Engineering to establish effective variability study procedures, part specific data to support process controls and customer needs
- Develops formal tracking and response system follow up on internal and external Quality issues. Places priority on customer service and response. Establishes measures, tracks part history to evaluate performance and avoid repeat problems
- Responsible for informing employees of all news (customer related, safety, quality, etc.) by developing proper communication method
- Develops plans for efficient use of materials, equipment, supplies and employees. Reviews manufacturing costs and product quality and modifies quality departmental activities to maintain and enhance profitable operation of division
- Perform special projects in support of the organizations business objectives
- Responsible for maintaining Quality Procedures and Instructions within the department
- Ensure that processes needed for the quality Procedures and Instructions within the department
- Report to management on the performance of the quality management system and any need for improvement and ensures the promotion of awareness of customer requirements throughout the facility
- Ensure that customer requirements are addressed including special characteristics, setting quality objectives and related training, corrective and preventive actions, product design and development
- Represents CSS with customers, suppliers, corporate and other Magna facilities to evaluate and promote improved processes
- Other all duties as assigned
- Minimum Completion of a Post Secondary Degree/Diploma in a related field or Business Management related study
- P. Eng or A.S.Q.C. designation, preferred
- In depth knowledge and understanding of TS 16949 standards
- 7 – 10 years quality management in an automotive (JIT) Tier 1 manufacturing environment
- Must be able to work in a fully computerized work environment
- Extensive computer skills (Microsoft Office)
- Commitment to continuous improvement and lean manufacturing principles with experience related to complex assemblies
- Demonstrated leadership skills and the ability to lead people with excellent interpersonal skills