Lean Manager Resume Samples
4.8
(96 votes) for
Lean Manager Resume Samples
The Guide To Resume Tailoring
Guide the recruiter to the conclusion that you are the best candidate for the lean manager job. It’s actually very simple. Tailor your resume by picking relevant responsibilities from the examples below and then add your accomplishments. This way, you can position yourself in the best way to get hired.
Craft your perfect resume by picking job responsibilities written by professional recruiters
Pick from the thousands of curated job responsibilities used by the leading companies
Tailor your resume & cover letter with wording that best fits for each job you apply
Resume Builder
Create a Resume in Minutes with Professional Resume Templates
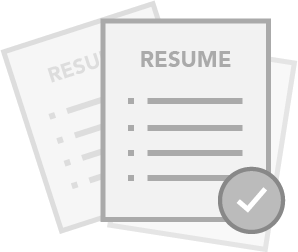
CHOOSE THE BEST TEMPLATE
- Choose from 15 Leading Templates. No need to think about design details.
USE PRE-WRITTEN BULLET POINTS
- Select from thousands of pre-written bullet points.
SAVE YOUR DOCUMENTS IN PDF FILES
- Instantly download in PDF format or share a custom link.
AG
A Green
Amelie
Green
3012 Nolan Roads
San Francisco
CA
+1 (555) 398 7890
3012 Nolan Roads
San Francisco
CA
Phone
p
+1 (555) 398 7890
Experience
Experience
Houston, TX
Lean Manager
Houston, TX
Ruecker, Olson and Crona
Houston, TX
Lean Manager
- Support efforts to establish and improve standard work, management systems, and key business processes
- Work with Lean sponsors/leads to develop process improvement strategies for site
- Work with the Lean Leadership, other Corporate Lean managers and Corporate Training Department to develop and direct the training of Lean Leaders
- Implement and track Lean Six Sigma metrics that provide data for process management and indicators for future improvement opportunities
- Leads and / or facilitates process improvement work teams, problem solving events and workshops
- Work with the Lean Leadership, other Corporate Lean Managers and site Lean Coordinators to create a format for sharing Lean Best Practices company wide
- Provide accurate and timely reporting to Lean Leadership, Corporate Department Managers and site management on pending and completed projects
New York, NY
ACE / Lean Manager
New York, NY
Hoeger LLC
New York, NY
ACE / Lean Manager
- Present CI training materials/modules and teaching (OJT)
- Roll up and monitoring of ACE/Lean metrics and reporting to SBU and segment ACE leadership
- Coaching site employees on ACE/Lean tools and their application
- Implement ACE/Lean programs to ensure vertical and horizontal integration across organization
- Assist with the necessary follow-up actions to close out "to-do" actions after Kaizen Events
- Management and oversight of the ACE Assessment Process throughout Electric, Environmental & Engine Systems (ES) to ensure adherence to standard work and development of Certified Assessors
- Monitor progress of ACE/Lean within the facility
present
San Francisco, CA
Site Quality & Lean Manager
San Francisco, CA
Adams, Hamill and Kreiger
present
San Francisco, CA
Site Quality & Lean Manager
present
- Lead and develop HOS and Quality talent including hiring, career path development and performance management
- Closely monitor HOS performance and maturity scorecards; develop actions to address performance gaps and accelerate improvements
- Lead the implementation of HOS at the site to achieve all relevant elements within the Standard Implementation Framework (SIF)
- Coach and mentor leaders through the facility on HOS Behaviors, principles and practices
- In conjunction with ISC STRAP and AOP processes, partner with site leadership to develop and deploy the site ISC strategy
- Drive a robust Root Cause Corrective Action (RCCA) process across the organization and champion internal and external escape reduction initiatives; ensure the completion of corrective actions through eCats and CAR’s in order to prevent recurrence
- Lead continuous improvement initiatives focused on achieving business objectives in an accelerated fashion
Education
Education
Bachelor’s Degree in Technical Aptitude With
Bachelor’s Degree in Technical Aptitude With
East Carolina University
Bachelor’s Degree in Technical Aptitude With
Skills
Skills
- Ability to work with mathematical concepts such as probability and statistical inference, accounting and financial calculations and projections. Ability to produce and interpret financial reports in graph and diagram form
- Ability to define problems, collect data, establish facts and draw valid conclusions. Ability to deal with several abstract and concrete variables. Ability to compile and present data in a format that facilitates information sharing and decision making
- Ability to read, analyze and interpret general business periodicals, professional journals, technical materials and governmental regulations. Ability to write reports, business correspondence, work instructions and procedure manuals. Ability to effectively present information and respond to questions from groups of managers, customers, employees and vendors
- Strong project management and project leadership experience
- Ability to build relationships and influence all levels in the organization
- Knowledge with demonstrated skills in using and teaching Six Sigma, Lean tools, and Quality system controls
- Ability to utilize strong written and verbal communication skills, work in a team and facilitate team development
- Demonstrated leadership ability to drive results and influence others to meet strategic objectives
- Ability to teach and facilitate groups using data for decision making
- Ability to work cross-functionally in the organization
15 Lean Manager resume templates
Read our complete resume writing guides
1
Continuous Improvement / Lean Manager Resume Examples & Samples
- Works with management to strengthen and drive effective "benchmark-level execution" of world class manufacturing in a complex and fast paced manufacturing environment
- Develops and manages cross-functional teams to meet project objectives. Monitors productivity of groups and individuals, recommends changes where desirable. Provides leadership and support to team
- Leads long-term projects aimed at waste elimination/production efficiencies and establishment of Lean Manufacturing areas in conjunction with manufacturing sites. Subject matter may include plant floor layout, material-handling routes, service parts, and key future launches
- Facilitates continuous improvement project teams to continuously improve processes and give support to areas within the organization. Based upon management requests, leads employees through workshops designed to improve work processes to reduce cycle time, inventory, labor hours, scrap, etc
- Identify problems in a process, establish and manage projects within the process, evaluate the process and develop potential solutions to improve the process. Applies principles of statistical process control when appropriate. Identifies opportunities for common mistake proofing
2
Lean Manager Resume Examples & Samples
- You design and communicate the LEAN strategy and coordinate the LEAN roll out plan for the Market
- You lead initial key LEAN projects and ensure sustainability by transferring skills to the appointed LEAN champions in the divisions
- You support the implementation of newly designed end-to-end flows
- You train, coach and assess the LEAN activities in the market (across functions, businesses and E2Es)
- You build and leverage your network with other market LEAN managers in Europe to accelerate local implementation
3
Lean Manager Resume Examples & Samples
- Provide leadership, coaching and training in leading large scale improvement and shift culture change that is inherent in Lean transformations. Provide objective assessments of our capability to lead significant change and work with plant managers to reconcile any issues or obstacles
- Develop the appropriate driving metrics for Lean, assess baseline performance, work with operation managers to develop appropriate targets and measure progress to targets
- Hands-on leadership and teaching of Lean principles and tools. Mentor Lean Sensei within facilities. Certify Lean Sensei and RIW facilitators. Develop learning opportunities for executive leadership. Facilitation and implementation of the Lean through Rapid Improvement Workshops by value stream and facilitate the use of various structured problem solving techniques, team effectiveness techniques and drive the workshop participants to implement lean tools using team ideas and solutions that will achieve real and sustainable improvements in PPG Kunshan’s manufacturing capacity, quality and cost
- Play an active role within a network of Lean/Performance improvement sharing within in plant and China region. Document and share the best practices and spread them in place other cell
- Expertise in Performance improvement processes
- Minimum of 2 (4)years experience on manufacturing operations,3 years on Lean relative experience
- Ability to plan and set target at operational cell level, and drive execution of improvement plans
- Chemistry tertiary level degree
- Ability to effectively facilitate cross functional teams in a process improvement workshop
- Working knowledge of how to facilitate/lead organizational change initiatives
- Ability to work under muti-culture environment
- English Level CET 4
- Should meet all related requirements regarding Quality Management Systems and EHS Management Systems
- Any training experience and ability is plus
4
Lean Manager Resume Examples & Samples
- Facilitate, train and lead Strategy Deployment Activity
- Lead change management activities (create transition plans from current to future state and execute)
- Bachelor degree in Operations Management or related field. Master’s degree preferred
- 10+ years business process or manufacturing continuous improvement experience
- Six-Sigma knowledge or certification preferred
- Lean Champion certification or willingness to obtain certification a plus
- Strong project management and project leadership experience
- Ability to build relationships and influence all levels in the organization
- Knowledge with demonstrated skills in using and teaching Six Sigma, Lean tools, and Quality system controls
- Ability to utilize strong written and verbal communication skills, work in a team and facilitate team development
- Demonstrated leadership ability to drive results and influence others to meet strategic objectives
- Ability to teach and facilitate groups using data for decision making
- Ability to work cross-functionally in the organization
- Analytical skills and business financial knowledge a plus
- Application of lean principles to non-manufacturing and non-traditional situations
- Skilled in full cycle process/project management, planning and change management
- Ability to effectively plan, direct and coordinate to changing demands and circumstances activates across cross functional teams and departments
- Provide leadership and influence to others
- Developing relationships and networks
- Strong interpersonal, communicate on (oral and written), and presentation skills
5
ACE / Lean Manager Resume Examples & Samples
- Implement ACE/Lean programs to ensure vertical and horizontal integration across organization
- Help leadership team progress in support of Policy Deployment, Macro Plan, and ACE/Lean (Production System) Criteria by coordinating actions to ensure improvement
- Partner with the sites to drive ACE site Progression to Bronze, Silver and Gold
- Help identify and remove barriers to implementation of Continuous Improvement (CI)
- Monitor progress of ACE/Lean within the facility
- Present CI training materials/modules and teaching (OJT)
- Plan for & facilitate, lead or co-lead, either internal or external Kaizen events including creating scope sheets, staffing event teams, and coordinating event logistics
- Assist with the necessary follow-up actions to close out "to-do" actions after Kaizen Events
- Management and oversight of the ACE Assessment Process throughout Electric, Environmental & Engine Systems (ES) to ensure adherence to standard work and development of Certified Assessors
- Roll up and monitoring of ACE/Lean metrics and reporting to SBU and segment ACE leadership
- Coaching site employees on ACE/Lean tools and their application
- Advance in the ACE/Lean certification program to practitioner
- Prepare, participate, and co-lead in ACE/Lean site certification assessments and coordinate homework action closure for site
6
Senior Lean Manager Resume Examples & Samples
- Drive the site effort to link customers with manufacturing and ultimately suppliers with supermarkets, kanban and other lean tools through the Alere Lean Enterprise (Safety, Quality, Efficiency & Delivery)
- Spearhead a cultural shift towards value-added creation and waste elimination
- Create a permanent competitive advantage for the site as a center of Quality, Efficiency and Delivery
- Identify key individuals to support the lean enterprise in year two
- 5S Program
- Policy Deployment Steering Committee
- Kaizen, TPM and 5S activity Schedule
- Planning and Review Session (2 per year)
7
Lean Manager Resume Examples & Samples
- Lead complex projects that cut across various organizational, functional, and internal boundaries
- Maintain local team by training team members to become Lean experts fora career development path
- Conducts regular plant Lean assessments (VSM), develop action plans and work implementations
- Conduct Kaizen events using Lean methodologies to generate priority initiatives with measurable results
- Establish, implement and monitor critical business operating systems, policies and procedures that support the achievement of business objectives
- Represent the business in customer, community and industry events or associations
- Provide standard work guidance and support to all the levels of the organization, especially the shop-floor
8
Lean Manager Resume Examples & Samples
- Develops and maintains lean transformation plan including value stream maps to identify key opportunities to eliminate waste and improve performance based on strategy deployment and business results
- Collaborate with leader to execute Gemba walk process (Managing for Daily Improvement), utilizing and constantly improving the visual management on the shop floor and in the office areas. Drive all levels of leaders to implement continuous improvement and eliminate flow inhibitors (anything that prevents us from satisfying our customers)
- Coordinates all Lean Manufacturing Activities within the location including kaizen events, projects and any other activity to improve and further lean efforts to ensure execution of transformation plan
- Drive flow, pull and material management through the operations. Including supermarket and tugger concepts; cell design with product, material and information flow considerations; Plan For Every Part implementation; pull systems and flow concepts in all applicable areas based on appropriate takt-time or takt image
- Support operations and office group to drive the establishment and maintenance of standard work and continuous flow in all areas. This includes 5S and visual management in all areas
- Drive lean thinking into the office to create enterprise level value stream management including customer interfacing and new product development areas. This includes implementation of 5S and standard work in the office and visual management and daily improvements as appropriate
- Provides lean training and coaching for site employees based on needs and requirements
- Provides lean status reports for both internal/external communications including metric based accomplishments of the transformation plan. Estimate and report on true savings of lean efforts in areas of: Safety, Quality, Delivery, Cost and Cash (inventory)
- Interfaces and coordinates lean activities with GBU and Corporate lean groups
- Lead Lean Assessment preparation and develop improvement plan based on assessment results. Participate as a lean assessor for other Pentair facilities
- Partners with new product development to ensure design for manufacturability
- Knowledge of Lean tools
- 8 Wastes, 5S, Gemba walk (Managing for Daily Improvement)
- Value stream mapping and analysis
- Takt time and standard work (shop floor and leader standard work)
- Pull systems (Kanban signals)
- Single piece flow and cell and factory floor design
- Material Flow – based on Rick Harris Methods from Making Material Flow (green book) published by Lean Enterprise Institute. Including Plan For Every Part (PFEP), supermarkets and tugger routes
- Level scheduling
- Strategy Deployment (Hoshin Kanri)
- Poke yoke (mistake proofing)
- SMED (rapid change-over)
- TPM (Total Productive Maintenance
- Has lead, coached and participated in numerous lean events in manufacturing, engineering and support areas
- Has demonstrated the ability to articulate the desired state, purpose and value of lean and constantly able to identify opportunities for waste elimination
9
Lean Manager Resume Examples & Samples
- Possess expert knowledge and practical application of problem solving 8D, PDCA and DMAIC tools and methodologies
- Experience providing problem solving training and coaching to all levels of the organization
- Black belt Six Sigma preferred
- Knowledge of planning and supply chain management is a plus
10
ACE / Lean Manager Resume Examples & Samples
- Has a strong understanding of ACE/Lean principles
- Experience applying fundamental lean tools to achieve tangible results. Preferred experience with ACE Operating system
- Lean leadership/management/coaching experience is a must, Six Sigma experience and training preferred
- Capable of influencing and getting cooperation and action from others
- Ability to effectively communicate (verbal and written), work and relate with people at all levels of the organization and be self-sufficient
- Ability to handle nebulous situations, with minimal guidance, effectively
- Effective team player, good coaching skills and can develop other co-workers
- Ability to encourage and motivate others to be successful
- Excellent knowledge of MS office computer software including MS Word, Excel, PowerPoint, and Outlook. Able to use Minitab or other statistical software
- Ability to multi-task, organize and prioritize
- Good analytical and problem-solving skills
11
Lean Manager Resume Examples & Samples
- Develops and maintains the sites lean transformation plan, including value stream maps
- Lead kaizen events driving to clear measurable outcomes or deliverables
- Lead process improvement analysis/standardization
- Collaborates with leaders to execute the Gemba walk process (Managing for Daily Improvement)
- Utilize and improves visual management in all areas
- Coaches and mentors leadership toward a continuous improvement culture
- Assures open communications and involvement of employees who work in the Lean process
- Leads Lean Assessment preparation and develops improvement plan based on assessment results
- Provides lean status reports for both internal and external communications including metric based accomplishments of the transformation plan
- Stays current with technologies and lean concepts through continuing education and benchmarking
- Bachelor's degree (B.A., B.S.) or equivalent
- 5-7 years of experience in Manufacturing/Continuous Improvement Operations experience preferred with proven knowledge of TPS (Toyota Production System)
- Comprehensive business knowledge (organization structure, business functions, processes, procedures, objectives, goals, measures, metrics, internal self-assessment processes, etc.)
- Word, Excel, PowerPoint, Access, Outlook, Outlook, JDE, Visio, Minitab
- Specialized Knowledge, Licenses, etc.: Six Sigma black/green belt preferred
12
Lean Manager Resume Examples & Samples
- At least 5 years' experience delivering on Performance Excellence and continuous improvement methods in a manufacturing or supply chain environment (Lean, 6sigma, Shingo, TPM, TQM), demonstrating tangible and significant business impact
- Pharmaceutical industry experience preferred. Experience of working with and improving external manufacturing partners preferred
- Experience in project management is essential
- Demonstrating leadership skills to drive change, and influence teams
- Flexibility to travel to accommodate the global challenges of this role (up to 30% of the time)
- Computer fluency
13
Lean Manager Resume Examples & Samples
- Train site leadership and other key personnel on Ryder Lean Guiding Principles concepts and Lean Transformational Processes in concert with the Supply Chain Solutions deployment strategy, and develop shop floor experts capable of driving Lean in their areas. Coach and mentor others on Lean so it becomes engrained in Ryder's culture. Mentor Lean on-site managers through Lean certifications
- Facilitate VSM's, Lead Kaizen events, Lean projects and other activities that execute the site Lean transformational improvement plan
- Coach and mentor the implementation of MDI and RCCM processes and Provide regular reports of data and actions to measure progress against site objectives and remove barriers to deployment of continuous improvement plan
14
Lean Manager Resume Examples & Samples
- Champion operational excellence initiatives by driving process improvements, eliminating waste, reducing cost and optimizing flow
- Responsible for analyzing, planning, implementation, training, and facilitating Lean/ZAOS initiatives company-wide across all functions
- This function will assist in determination of the scope, objectives, metrics, cost and schedule for Lean/ZAOS projects
- Lead Lean initiatives including Value Stream Mapping, workplace organization (5S), set-up reduction, standardized work process/work flow improvements, visual management, Poka-Yoke methods, and Pull Systems
- Working with organizational managers and the Lean Team to lead the implementation of specific Lean/ZAOS initiatives throughout the facility
- Support the planning & execution of lean/ZAOS initiatives by working side-by-side with departmental personnel and associated work groups to fully implement and assure sustaining mechanisms are in place
- Proactively involves employees at all levels of the organization to gain their input and support
- Educates and trains all company personnel in the various Lean manufacturing concepts, tools and methods
- Organizes and guides project teams to ensure that results are achieved to meet project objectives
- Participates in the identification and selection of Kaizen activities
- Serves as team leader and facilitator for continuous improvement implementation activities
- Follows-up on tasks generated in project meetings and monitors sustaining activities to ensure successful and timely completion of action items
- Coordinates the implementation of sustaining activities as needed throughout the organization
- Solid knowledge and background with Lean Concepts (Kanban, 5S, visual management, Poka-Yoke methods, VSM, pull systems, etc.)
- Experience in Supply chain and manufacturing process improvements
- Must be able to work effectively with employees at all levels of the company, as well as with suppliers and customers
- Excellent interpersonal skills as well as verbal and written communication skills
- Strong facilitating & coaching skills, acts as an effective advisor to management and employees
- Ability to adapt easily to changing priorities in a fast-paced environment
- Ability to effectively train others
- BS Degree, Certification or License in a technical discipline, or equivalent experience in a related technical field
- Five (5) or more years of related experience and demonstrated ability to perform the essential functions of the position
- Technical knowledge of lean principles, tools, and techniques
- Experience in Lean and/or Six Sigma processes
- Management experience in Supply Chain or Operations or Programs/product development will be a plus
15
Lean Manager Resume Examples & Samples
- Work with leadership teams to define the current and future state Value Streams to plan and prioritize continuous improvement activities
- Provide leadership / mentoring / training to all levels of the organization on the use and practice of Lean methodology and tools (VSM, 5S, Kaizen, SMED, “Design for Lean”, MDI, etc…)
- Facilitate the 5S process in all areas of the facility
- Ensure that all financial, operational and customer improvements are realized and sustained through regular audits
- Act as a key driver of change within the business, supporting management/cross functional decisions by communicating the enterprise-wide changes to employees and helping them to learn, understand, adjust and grow with the business’s Lean transformation
- Leverage Lean principles to assist in the design and execution of new manufacturing processes, methodologies and equipment layouts to improve overall equipment effectiveness
- Develop a culture that strongly values excellence in customer service and quality, and rewards and recognizes achievements in these areas
- Provide leadership and direction to teams performing the following functions: material planning, inventory management, purchasing, production, shipping/receiving and logistics
- Assure that effective work processes, tools and systems are developed, documented, and maintained, and that all operational requirements of Thornton' s ISO 9001 quality system are fulfilled
- Establish and maintain data collection and performance measurements to track performance in key areas such as the reduction of waste in both the office and floor
- Working knowledge of proven continuous improvement methodologies and use these tools to drive improvement in key performance measures. Examples include SPC, TQM, JIT, Lean, etc
- An ideal education will include a technical undergraduate degree and 5+ years of relevant lean experience utilizing Value Stream maps, COPQ, Toyota Product System and/or Six Sigma techniques or an equivalent combination of education and experience
- Excellent communication skills throughout all levels of the organization
- Strong people and change management skills
- Five years or more experience successfully leading similar Lean Continuous Improvements efforts
- Ability to initiate and lead significant change
- Ability to work effectively in teams with peer managers and others to achieve overall organizational goals
- Commitment to and passion for achieving Continuous Improvement in a made to order technical product focused environment
- Strong analytical skills and process focus
- High energy level and drive required to lead critical functional areas within a dynamic business unit
- Strong persuasive skills and the ability to exercise influence beyond direct authority
- Hands-on style and a willingness to perform a range of detail-level work, i.e. a doer rather than an administrator
- Working knowledge of Microsoft Office suite, especially Excel, Word and PowerPoint
- Working Knowledge of Six Sigma Techniques
16
Lean Manager Resume Examples & Samples
- Support CBS (ContiTech Business System) Industrial Fluid System Business Unit in developing and implementing CBS Culture through roadmap implementation for BU management aligned to BU strategies and objectives
- Define the KPI for measurement of CBS roadmap implementation. Cascade the BU True North metrics and Corporate initiatives to each site. ( i.e.: Energy, PLNS, etc)
- Develop BU Leaders, BU Coaches on CBS management system through coaching and DDT training
- Develop training and apply CBS coaching routine (principles, methods, tools, processes etc.) within Industrial Fluid Systems BU Leadership, at sites, value streams and across functions based on business situation
- Act as Coach and Mentor to Managers at all levels, CBS coaches & Specialists to support them in executing the routine to deploy our holistic LEAN Management System in their areas of responsibility
- Insure that projects, RIE’s and Just Do Its are aligned to LEAN principles for each Site, Value Stream or Function based upon targeted future state Value Stream Designs
- Develop, train, and coach future and current BU CBS coaches within the BU as well as all levels of managers
- Develop ways to share best practices (Yokoten) across the BU and network with other BU
- Moderate/facilitate workshops and events to teach and realize results
- Support regional and local training facilities. Motivate BU management, local management, and CBS coaches to further CBS implementation in their area of responsibility
- Support and promote the cultural change, by working with leaders to create and communicate the vision, and urgency for change that incorporates a Continuous Improvement Culture and Holistic Management system
- Coach leaders to empower and involve employees and demonstrate how short term wins can anchor the new culture
- Oversee and insure organization utilizes CBS Data Base in support of Yokoten/Sharing of best practices
- Report status of CBS to top management and corporate functions
- Communicate BU activities and coordinate with ContiTech Central CBS group
- 10+ years’ experience leading and managing people, departments and organizations
17
Lean Manager Resume Examples & Samples
- Provide leadership to create a data-driven culture that focuses on measurement and metrics
- Lead internal and external productivity work-out sessions. Implement Lean Six Sigma metrics that provide data for process management and indicators for future improvement opportunities
- Train, mentor and lead team members to propose, justify and execute projects to reduce product/operational cost using Lean Six Sigma methodologies
- Lead, drive, and facilitate implementation of Lean Six Sigma projects including, but not limited to, SMED, Value Stream Mapping, Kaizen Events, etc
- Lead implementation of 5S as appropriate; develop and implement 5S system throughout manufacturing campus
- Train and mentor key organizational stakeholders on the use and practice of Lean Six Sigma methodology and tools
- Implement and track Lean Six Sigma metrics that provide data for process management and indicators for future improvement opportunities
- Solve new and recurring Lean Sigma issues through the use of root-cause analysis and corrective actions
- Other duties as requested
- Manufacturing experience in a fast paced environment
- Bachelor’s degree in Engineering or related technical field or equivalent work experience
- 3+ years of experience leading projects, teams, and/or initiatives in a technically and operationally complex business
- 3+ years of successful leadership in executing continuous improvement/Lean Six Sigma efforts and enabling efficiency, effectiveness and tangible financial benefit
- Minimum Green Belt or Comparable Project Experience
- Strong ability to communicate and relate to employees at all levels of the organization and craft communication accordingly
- Strong written and oral communication, interpersonal, and organizational skills
- Experience with Microsoft Office (Word, Excel, PowerPoint) and Minitab applications
- Capacity to work in a fast-paced environment with exceptional attention to detail
- Solid analytical and mathematical/statistical skills
18
Lean Manager Resume Examples & Samples
- Minimum of five (5) years of manufacturing or supply chain experience
- Bachelor’s degree or higher in Mechanical, Chemical and/or Industrial Engineering from an accredited university
- Experience with lean projects and methodologies including projects with significant impact on the business
- Proven understanding of leadership principles and behaviors
- Previous experience across multiple divisions, manufacturing locations, and job functions
- Self starter and self directed that leads with high energy and passion
- Ability to deal with significant value stream complexity
- Experience leading change and ability to influence at all levels
- Strong project management, organizational, analytical and presentation skills
- 3M Global Terms of Use and Privacy Statement
19
Lean Manager Resume Examples & Samples
- Maintains and develops appropriate process improvement / Lean training material that is compliant with Zodiac Aerospace (ZA) and Zodiac Services (ZS) policy, objectives and standards and provides training to all levels of employees
- Provides specialized training and guidance commensurate with requirements of other Lean staff and specific process improvement initiatives eg. QRQC
- Leads and / or facilitates process improvement work teams, problem solving events and workshops
- Documents and assists in the development of business metrics related to process improvement / Lean performance for US sites (e.g. 5S) and in collaboration with offshore Lean Managers and colleagues
- Determines opportunities for improvements in processes and communicates associated value propositions to management
- Coordinates and establishes process improvement plans with minimal direction from others
- Prepares status reports, documentation and presentations for management and coordinates resulting actions with affected business units
- Where performance is lagging plan / targets, serves as a resource for root cause analysis, corrective actions and implementation or monitoring of associated recovery plans
- Provides input to annual Masterplan and provides regular updates to confirm objective status and progress to schedule
- Adheres to safe work practices and contributes to the evolution of health, safety, and environmental program and culture
- Bachelor's degree in Engineering from a four-year college or university, or six to ten years related experience and/or training, or equivalent combination of education and experience
- Formally trained in Lean’s tools and principles
- Strong interpersonal, verbal and written communication skills essential for interaction with both internal and external customers
- Ability to read, analyze, and interpret common scientific and technical journals, aerospace regulations, financial reports and legal documents
- Ability to comfortably perform public presentations, reporting and synthesis
- Ability to coordinate Quality, Environment and Health actions plans within Zodiac Services Americas Repair Stations and Distribution Centers
- Ability to respond to common inquiries or complaints from customers, regulatory agencies or members of the business community
- Ability to write speeches and articles for publications that conform to prescribed style and format
20
Lean Manager Resume Examples & Samples
- Support LMI corporate and Aerostructures site Lean initiatives and the mentoring of site Lean Coordinators. Conduct lean training and facilitate Lean events and improvement teams as needed
- Ensure all Lean events/activities have documented project scopes, performance goals (deliverables) and metrics developed as well as an implementation and reinforcement plan
- Partner with Aerostructures sites and/or Lean Coordinators on continuous improvement and reduction of waste in their Value Streams and/or manufacturing processes. This may include research and development to include tool design, evaluation of equipment, developing manufacturing processes for potential new work and other projects as needed
- Collaborate with General Managers and Lean Coordinators to implement improvements to obtain and sustain customer specific certification programs
- Facilitate the Lean Transformation of administrative processes at LMI sites and Corporate Office
- Work with the Lean Leadership, other Corporate Lean managers and Corporate Training Department to develop and direct the training of Lean Leaders
- Facilitate the development of highly effective self-managed work teams motivating them towards a higher level of involvement and understanding
- Provide strong leadership to the project, departmental and site teams. Set communication and behavioral standards for teams by demonstrating desired behaviors through personal interactions and mentoring
- Ensure follow-up to improvement projects through site visits and working with GM’s, Lean Steering team and Lean Coordinators on project results, Transformation Maps, Gap Assessments and their alignment with corporate goals and strategies
- Work with the Lean Leadership, other Corporate Lean Managers and site Lean Coordinators to create a format for sharing Lean Best Practices company wide
- Monitor metric performance at all levels of LMI and foster a problem solving culture
- Provide accurate and timely reporting to Lean Leadership, Corporate Department Managers and site management on pending and completed projects
- Maintain involvement in outside Lean Organizations, read Lean publications, training materials and attend workshops to learn and share knowledge within the industry
- Assist with special projects and participate on other teams as requested
- Excellent PC skills, proficiency in Microsoft Office, Visio, CAD and other manufacturing related software
- Ability to work in a dynamic environment with multiple priorities and shifting time requirements. Must be able to promote a participative, team oriented environment, working with customers (both internal and external), all employees, vendors and others in a professional and respectful manner
- Excellent communication skills and be able to communicate clearly and professionally, both orally and in writing
- Ability to read, analyze and interpret general business periodicals, professional journals, technical materials and governmental regulations. Ability to write reports, business correspondence, work instructions and procedure manuals. Ability to effectively present information and respond to questions from groups of managers, customers, employees and vendors
- Ability to define problems, collect data, establish facts and draw valid conclusions. Ability to deal with several abstract and concrete variables. Ability to compile and present data in a format that facilitates information sharing and decision making
- Ability to work with mathematical concepts such as probability and statistical inference, accounting and financial calculations and projections. Ability to produce and interpret financial reports in graph and diagram form
21
Lean Manager Resume Examples & Samples
- Required to have and maintain current and up to date Passport
- Management of AOE principle initiatives
- Internal audit of plant AOE Certification status
- Training on AOE initiatives for implementation in the plant
- Audit regional sites as needed for AOE Plant Certification
- Successful completion of needed CI Leader training modules, or structured development plan for said training; prior exposure to and use of Lean Methodologies (Value Stream Management) and Production tools (such as Toyota Production System, or equivalent) and/or Six Sigma tools helpful
- Ability to read/write/speak English
- Operating knowledge and skilled in MS-Office (Excel, Word and PowerPoint)Experience
- Minimum 2 years of related experience. Additional education can be substituted for experience
22
IE & Lean Manager Resume Examples & Samples
- Maintains consistent and accurate hourly production job descriptions and staffing levels by position by plant. Facilitates evaluations for maintaining and developing new job descriptions. Keeps documentation current
- Represents the division in industrial engineering and lean manufacturing related grievances, where needed
- Provides support to other plants, as needed, during the implementation of approved process changes
- Maintains input for the standard cost files. Updates file where needed and assists cost accounting in providing product cost estimates for marketing
- Contributes to the development of corporate and plant industrial engineers and lean engineers
- Prepares training material of Industrial Engineering and Lean Manufacturing
- Design of experiments, statistical process control, six sigma methodology knowledge, accounting, Microsoft office, and highly desired a Certified Black Belt under JCI guidelines
- Excellent communication, presentation, leadership, analysis, and skills of shop floor and office work, presence and interaction with several ranks
23
Lean Manager Resume Examples & Samples
- -----------------------------------------------------------------------------------------------------------------
- Within area of responsibility analyze current work practices to identify areas for improvement and educate as to how to improve the business and manufacturing processes
- Devise, test and roll out new work processes / procedures with minimal disruption to the group
- Able to complete process mapping, value stream mapping, identifying inefficiencies in productivity, with a particular focus on layouts and sequencing
- Demonstrate performance excellence behaviors within the business and champion performance excellence initiatives
- Able to perform root cause analysis and resolve problems
- Able to carry out time and motion studies to support productivity improvements
- Monitor the completion of tasks and ensure good performance and record results
- Conduct risk assessments of processes and tasks in the department
24
BA Liquid Lean Manager Resume Examples & Samples
- 4+ years working on projects in the Digital space
- 2+ years of experience as a technical architect or consulting in multiple areas of Digital
- 2+ years of software design or development or creative design
- Agile delivery experience
25
Lean Manager Resume Examples & Samples
- Develop and own lean improvement plan across the entire site. Develop metrics to measure progress towards lean objectives, specifically: Safety, Quality, Delivery, Cost, and Engagement
- Work with Plant Director and functional leaders to develop a pipeline of viable projects. Review and rank against the sites strategic objectives. Recommend the best projects to execute based on alignment with the Plant's Strategic Roadmap. Report out progress to objectives
- Execute Lean initiatives to improve processes, drive out waste, and optimize flow across all value stream
- Understand intersections of core Engineering processes and identify improvement opportunities for better overall process effectiveness
- Educate and align employees to the principle, practices, and philosophy of continuous improvement through tools such as value stream mapping, basic problem-solving, Kaizen, standardized work, work-content analysis, waste elimination, quality at the source, 5S, etc
- Lead development and implementation of Engineering Standard work
- Provide guidance and leadership for process improvements teams to ensure process changes are optimizing value to both external and internal customers
- Assist with Annual Plant Roadmap vision and creation, lean organizational development, cross-functional project planning, and training in continuous improvement principles and methods for all employees
- Support efforts to establish and improve standard work, management systems, and key business processes
- Champion and provide leadership, training, and support to achieve “World Class” performance and strategic objectives
26
Lean Manager Resume Examples & Samples
- Work with Lean sponsors/leads to develop process improvement strategies for site
- Facilitate, train and lead Lean deployment activities
- Lead and execute change management activities (from current to future state)
27
Lean Manager Resume Examples & Samples
- Organizational Development –Provide leadership, coaching and training. Provide objective assessments of our capability to lead significant change and work with leadership team to reconcile any issues or obstacles
- Measurement / Metrics –Develop the appropriate driving metrics for Lean, assess baseline performance, develop appropriate targets and measure the progress
- Teaching / Mentoring –Hands-on leadership and teaching of Lean principles and tools
- Drive Continuous Improvement- Facilitation and implementation of the Lean through Rapid Improvement Workshops by value stream and facilitate the use of various structured problem solving techniques, team effectiveness techniques and drive the workshop participants to implement lean tools using team ideas and solutions that will achieve real and sustainable improvements in PPG Zhangjiagang’s manufacturing capacity, quality and cost
- Internalization & Best Practices –Play an active role within a network of Lean/Performance improvement sharing within plant and China region. Document and share the best practices
- #DW1
- Minimum 4 years’ experience of chemical operations, 3 years on Lean relative experience
- Ability to plan and set target, and drive execution of improvement plans
- Ability to work under Multi-culture environment
- Good English skill
28
Site Quality & Lean Manager Resume Examples & Samples
- Lead the implementation of HOS at the site to achieve all relevant elements within the Standard Implementation Framework (SIF)
- Lead continuous improvement initiatives focused on achieving business objectives in an accelerated fashion
- Identify initiatives that lead to standardization, simplification and overall improvement of quality and HOS systems, ensure process controls are in place for standardized work instructions, tooling and test equipment
- Closely monitor HOS performance and maturity scorecards; develop actions to address performance gaps and accelerate improvements
29
Lean Manager Resume Examples & Samples
- Performance improvement efforts, oversees the status and monitoring of operations improvement efforts, coordinates the improvement dashboard(s), and facilitates the training of individuals and teams throughout the organization utilizing the Alere Operating System (AOS) tools and techniques at our Pomona site
- Drive the site effort to link our customers to our manufacturing and ultimately our suppliers with supermarkets, Kanban and other lean tools through the Alere Operating System (AOS) platform (Safety, Quality, Efficiency & Delivery)
- Gain mastery of the Alere Operating System (AOS) materials and implementation methods through on-site training at our Alere San Diego site
- Conduct Kaizen activities company site wide
- Create local presence and structure for the KPO (Kaizen Promotion Office) on site
- Develop a rolling six-month plan for kaizen activities with site management
- Complete three or more kaizen activities and create a foundation of kaizen methodology, deployment of the 5S program, standardized work, and Gemba
- Work with senior management in order to deploy policy deployment (Hoshin Kanri)
- Deploy training and organize high-performance work teams in the facility
- Identify key individuals to support the Lean Enterprise
- Functional KPO with the following venues
- Develop and manage the 5S Program
- Manage Kaizen, TPM and 5S activity schedule
- Coordinate planning and review session for site (2 per year)
- Create a permanent competitive advantage for the site as a center of Safety, Quality, Efficiency and Delivery
- Manages performance of staff towards department and Company goals, including feedback on performance, appraisals, recommendations for merit increases or necessary disciplinary actions, communication to employees on performance, etc
- Responsible for exhibiting professional behavior with both internal/external business associates that reflects positively on the company and is consistent with the company’s policies and practices
- Perform other duties & projects as assigned
30
Lean Manager Resume Examples & Samples
- Lead the plant lean transformation process using the Perfect Execution System driving out waste and ensuring the success of the business objectives
- Conduct lean events in the areas of Value Stream Mapping, 5S, TPM, Visual Factory, Creating Continuous Flow, Making Material Flow, SMED and other lean tools/systems, while establishing the RCCM process to create a foundation for continuous improvement
- Provide formal training in Lean process improvement methodologies across the departments to enhance lean behavior, structured problem solving skill, standardization of practice and calibration of mindset
- Partner with the Site Leader to develop staff ownership of Lean metrics and charter, lead and direct teams in project completion and work closely with production, maintenance and other support functions in managing equipment moves and improving facility layout
- Implement Key Modules into operationally effective processes and work closely with the Engineering Department in Lean Principles when designing for new products